Erik Runge, Director of Engineering at Minus K Technology, talks to AZoNano about their low-frequency vibration isolation systems.
Could you provide our readers with a summary of the history of Minus K and explain how the company has evolved since it was founded in 1993?
Minus K Technology, Inc. was founded by David Platus, our president, in 1993. The early products were semi-custom in nature and were designed more on a case-by-case basis. There were a couple of standard products offered.
When I came on board, in 2000, we started developing more standard products, while continuing the custom work we had previously done. We now have a mature, comprehensive line of isolators that are suitable for many applications. We look to the future and continue to innovate our products as well as maintain the highest levels of service and support our customers have come to expect.
How do vibration isolation systems work and what are the main types of systems which are available on the market?
Vibration isolators can be broken down into passive and active types. Passive vibration isolation systems are essentially spring-mass-damper systems that provide a fundamental natural or resonant frequency.
The isolators provide the spring-damping behavior and the payload or item being isolated typically provides the mass. Vibrations somewhat higher than the fundamental frequency are attenuated. Damping is provided by various techniques. Active types use electricity, sensors and a feedback loops to emulate a low resonant frequency system.
Passive systems don’t use any source of power fundamentally to give isolation, (hence the name). Examples are mechanical springs, elastomeric spring-dampers, pneumatics or air springs, and the unique Minus K negative-stiffness systems that use mechanical springs and flexures.
Some passive systems do use a constant supply of compressed air, but that is just to keep the systems floating in their adjusted positon after something has changed with the payload. Electricity is also sometimes used to enable some damping elements, or auto-adjust features. These, however are not fundamental to the isolator. The isolators remain passive. There are also some hybrid systems that use elements of both active and passive elements.
What are the main application areas in which isolation systems are used?
Isolation is used in many industries: Microscopy of all types (including AFM, STM, SEM, STEM, white light and laser), profilometry, micro harness testers, aerospace, materials fabrication, interferometry, optics and even Hi Fi audio.
People place turntables (vinyl is coming back!) on isolators to get rid of noise due to footfall in residential homes, resonant shelving and things like that. We are often surprised by some of the applications we encounter.
Floor Vibration Isolation | Minus K FP-1 Floor Platforms
Minus K Vibration Isolation Floor Platforms
How specifically can the use of vibration isolation systems benefit users of Atomic Force Microscopes (AFMs)?
AFMs are among the most sensitive instruments in existence. Being able to image things on the order of atoms certainly requires a high degree of stability and hence, isolation. They are sensitive down to very low frequencies as well.
AFMs can have problems as low as 2 Hz or so if located on an upper floor of a building. Noise in this frequency range is very problematic for AFMs. Our isolators are very effective in this range. Air tables have a resonance near 2 Hz typically and can actually make things worse in some cases.
Some people use long bungee cords suspending a cement block as an inexpensive isolator. The AFM is placed on the cement block. These do work well, however, anyone that has used one with an expensive AFM knows that it can be quite scary to have your AFM swinging and swaying around when you touch them. Our isolators provide very similar levels of vibration isolation, without the danger, in a much more compact, convenient package.
Minus K supplies a wide range of vibration isolation products. Could you summarise the main features of some of these systems and explain the advantages of using Minus K vibration isolation systems?
The main feature that sets Minus K apart is our use of negative stiffness elements to provide very low natural frequencies, E.g., ½ Hz or less. This enables isolation of lower frequency vibrations than most systems and improved isolation over the entire frequency range of interest. For many, if not most applications, Minus K systems provide the highest isolation performance available.
We directly control the stiffness of the system by using some clever flexural elements in our designs. Most other isolators tend to be quite heavy because they try to make their system behave more softly by adding mass.
Vibration Isolation | An introduction to Minus K Technology's negative-stiffness isolators
An introduction to Minus K Technology's negative-stiffness isolators
We don’t have to do this. This makes our isolators very easy to deal with. Our 800CM-1 is the most “capacity dense” isolator we have. It is roughly an 8 inch cube, weighs only 26 lbs, yet can support up to 800 lbs. They can be combined to make a larger multi isolator system very easily.
We have standard models that can support any payload from a few ounces (10BM-10), up to 4000 lbs. per isolator (4000SM-1), and everything in between. We offer many different form factors as well. We have benchtop models and systems that look like traditional air tables, but use no air and deliver our 0.5 Hz performance.
Another thing that also sets our isolators apart is our ability to make them vacuum compatible. This is relatively easy for us as there is no compressed air to deal with. We also don’t have to worry about cooling any electrical components.
We have done systems for customers where the isolators went into high vacuum and greatly simplified the design due the elimination of complex bellows and other consideration that would be required with other isolation technologies. We can also design custom isolators for your exact application and specification. Give us your challenge.
I recently read that Minus K’s vibration isolation systems had been selected for use by the NASA Jet Propulsion Laboratory. Could you summarise this story to our readers?
We have done a few isolation projects for JPL. One was for the SIM (Space Interferometry Mission). They needed to simulate zero gravity and reduce vibrations on their testbed such that they could demonstrate stability in their measurements of a few nanometers. We provided a set of 0.4 Hz isolators for this system and they were able to successfully reach their goal.
Readers can find more about this project here: https://www.minusk.com/
Do you have any more interesting case studies which you could tell us about?
Minus K Technology was selected to provide the ground-based test isolation system for the James Webb Space Telescope. Six of our custom isolators are on top of Chamber A at Johnson Space Center.
The satellite and test fixtures are suspended inside the chamber by rods. They wanted to be able to simulate the zero external vibration environment of space to test the resolution of the optics. Our 0.5 Hz isolators proved to be ideal for the job. The payload is quite large, 60,000 lbs.
There are not many vibration isolation companies out there that have that sort of capacity, let alone the performance. We worked extensively with them to deliver a highly customized system that delivered the performance they needed.
How do you see the vibration isolation systems industry progressing over the next decade and how do you see Minus K being part of this change?
Everything is getting smaller. People are looking at smaller line widths in the semiconductor industry, for example. They are already well beyond what regular light microscopes can see, so more advanced technology and instrumentation becomes necessary. As line widths continue to shrink, the requirements for vibration isolation will also grow.
In fact, we are working with LBNL (Lawrence Berkeley National Lab) on their cutting edge MET 5 system. It is going to be key in developing the future generations in EUV (Extreme Ultra Violet) lithography techniques. We recently delivered a system of isolators for them and initial test of the system have proven very promising. The system will not be completed for maybe a year and a half, but they are very pleased with the performance we have delivered.
We are uniquely positioned to offer the best possible performance for those sensitive instruments for the future. Keep an eye on us to see what we do next. We are excited for the future of vibration isolation.
Where can our readers find out more information about vibration isolation systems and Minus K more generally?
Our website www.minusk.com is the best source. There, the readers will find information on all of our products such as weight, dimensions, and capacities. There is information on performance and prices as well.
We also have a section “In the news” where the readers can find all sorts of press releases, white papers, editorials.
We can always be reached by email [email protected] or phone (310)348-9656.
.jpg)
About Erik Runge
Erik Runge was raised in the Silicon Valley. He earned a degree in Physics from UC Santa Barbara in 1996. He worked at Digital Instruments, (which was later acquired by Veeco, and then Bruker) where he performed R&D and system and component level engineering for DI’s AFM products.
During this time, he also developed a specialty in vibration isolation and integrated Minus K Technology isolators into a specialized acoustic and vibration isolation enclosure (IS3K) for the Dimension 3100 AFM.
Erik came aboard Minus K Technology in 2000. During his time at Minus K, he has developed many new and custom products as well as in-house test systems. He also exhibits at many trade shows, demonstrating Minus K Technology’s signature 0.5 Hz, negative stiffness technology.
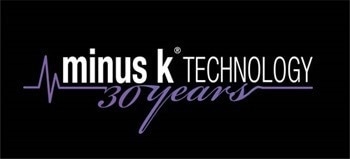
This information has been sourced, reviewed and adapted from materials provided by Minus K Technology.
For more information on this source, please visit Minus K Technology.
Disclaimer: The views expressed here are those of the interviewee and do not necessarily represent the views of AZoM.com Limited (T/A) AZoNetwork, the owner and operator of this website. This disclaimer forms part of the Terms and Conditions of use of this website.