Interview conducted by Olivia FrostMay 18 2021
In this interview, Wes Wigglesworth, the Product Manager at TMC, talks to AZoNano about Cryogenic Electron Microscopy (Cryo EM).
What are some of the current trends in materials analysis, life sciences research, nanotechnology, and nanofabrication?
Smaller features, higher resolution, longer exposure times, more data, more sensitivity to the environment than ever before. Cryogenic Electron Microscopy (Cryo EM), and specifically the Cryo TEM commercialized several years ago, is one of the most significant technologies in advanced microscopy and an excellent example of this trend.
Can you give us a brief overview of vibration isolation and the different approaches?
Vibration Isolation solutions are available in a very large range of sizes, performance levels, for many applications: passive, active, whole building, concrete plinths, and isolated slabs, and within these categories, there are different approaches such as damping, inertial sensors, feedback and feedforward, parallel and serial type designs.
What are some of the advantages and limitations of the more traditional approach of concrete plinths and isolated concrete pads?
A large concrete plinth or slab within a building takes advantage of Newton’s law. This was a good approach before the development and commercialization of serial hard-mount type active vibration cancellation. For example, a Quiet Island with STACIS can be designed to fit the footprint of the instrument, cancels low-frequency building vibration, is modular, and can be reconfigured for a relocation or a different tool, all of which the plinth and slab approach is either ineffective or limited.
When it comes to electron beam users, such as those who use scanning electron microscopes or transmission electron microscopes, why do they need to be concerned about floor vibration, magnetic fields, and acoustic noise?
Any imaging or lithography device with an electron beam, and most with ion or photon beams, is sensitive to these noise problems. Most, if not all, such instruments have environmental specifications which the installation site must meet.
Can you tell us about the lab environment and its effects on sensitive instruments, and the effect this will have on the e-beam tool performance?
Low-frequency building vibration, particularly due to footfall, nearby automobile traffic, and rail activity, at some level, as well as acoustics, will limit resolution even at low magnifications. A high AC magnetic field from nearby power will often manifest as a sawtooth wave on a particle and result in faulty data, whereas shifting DC fields may render an otherwise clean and long image capture useless. One passing streetcar could erase 30 minutes spent prepping a TEM sample on a Focused Ion Beam (FIB) tool if the vibration is not properly controlled.
Can you tell us a bit about floor vibration criteria, in particular, the ‘VC Curves’?
Many instrument manufacturers utilize the industry standard “Vibration Criterion” developed by Colin Gordon, known as the VC curves. It is very helpful of course to have a standard that can be referred to for increasingly higher resolutions and smaller feature sizes. 10-15 years ago, we often helped folks achieve VC-C or VC-D (12.5 um/s RMS or 6.3um/s RMS). Now it seems VC-E, F, G are common in our discussions for commercial instruments and lower for a more sensitive custom application. As an example, an electron-beam lithography (EBL) instrument writing line widths of 10-40nm may require floor vibration no higher than VC-E, or 3.12um/s RMS from 1-100Hz. Today, we are commonly seeing less than 10nm line widths with EBL. Advanced microscopy capable of sub-nanometer resolution typically requires even lower vibration levels.
In terms of active vibration isolation, what is the difference between parallel and serial and why is this important for e-beam lithography and electron microscopes?
All inertial active vibration isolation systems consist of a mechanical spring, an inertial sensor measuring vibration, and feedback and/or feedforward control loop. Serial simply means that the active control loop is in series with the spring. Parallel type active systems are very effective at canceling payload motion because the sensor is looking up at the payload – great for moving stage applications for example. The serial-type system, such as STACIS, employs a downward-looking sensor to aggressively measure and cancel floor vibration.
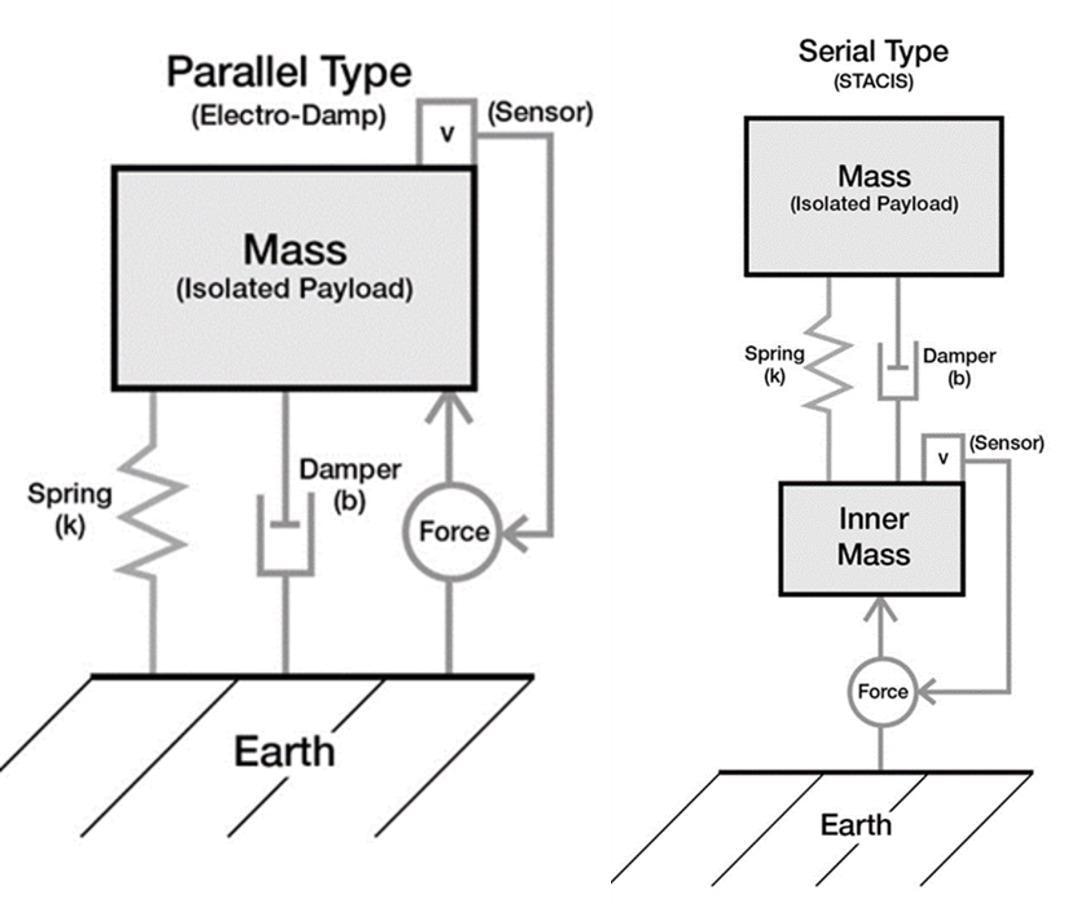
Image Credit: TMC Vibration Control
When combined with a stiff spring to greatly reduce the impact on the control loop from payload resonance or movement, such a serial type system is inherently more effective at protecting ebeam tools from floor vibration while allowing the tool’s internal isolators (often a soft pneumatic spring) to be optimized for high-frequency vibration coming from the frame, electronics, and other flanking paths. This combination is ideal for canceling both high and low-frequency vibrations.
How effective are mitigation attempts, such as room and HVAC system modifications, as well as point-of-use solutions in helping with impactful noise issues?
When the source in the building can be identified and is accessible, modifications can be very effective, particularly to mitigate the effects of acoustic noise. Modifying the room to add, or better yet including in the construction, passive shielding for magnetic fields, mainly AC fields, can also be very effective. If it’s not possible to implement whole room solutions, point-of-use solutions, such as active field cancellation and active vibration isolation in comparison can be very easy to install, cost-effective, and extremely effective exactly where it is needed – at the instrument itself.
Where can readers find more information?
Supporting Scanning Electron Microscopes with the SEM-Base VI, Active Piezoelectric Vibration Isolation Enables Advanced Electron and Ion Beam Instruments in Harsh City Environment, TMC Quiet Island Enables High-Resolution Cryo TEM, Evolving criteria for research facilities: vibration
Please provide links to any materials that may be relevant to our audience.
About Wes Wigglesworth
Wes Wigglesworth has been with T
MC since 1997 and is currently the Product Manager for TMC’s flagship line of Active Vibration and Noise cancellation systems, including Stacis, Stacis iX, Mag-NetX, and the new Everstill.
Wes has previously held positions in Application Engineering, Sales Engineering, and OEM Account Management in the scientific and technology industry over a period of over 24 years.
He holds a bachelor's degree in Electrical Engineering from Tufts University in Medford, MA.
Disclaimer: The views expressed here are those of the interviewee and do not necessarily represent the views of AZoM.com Limited (T/A) AZoNetwork, the owner and operator of this website. This disclaimer forms part of the Terms and Conditions of use of this website.