For manufacturers dealing with high precision, granite-based, multi-axis motion systems, two primary choices exist.
One option involves designing a motion system where the granite base becomes an integral part, with bearings directly mounted on the granite slab, eliminating the need for a base plate. Manufacturers can also use off-the-shelf, discrete motion/positioning stages, which are mounted on a split-bridge granite structure or a granite base.
The selection between these two multi-axis motion platform designs hinges on various factors—both have specific advantages and disadvantages.
This article explores the difference between stage-on-granite base and integrated granite motion systems.
Multi-Axis “Rails-on-Granite” Stages With Mechanical Bearings
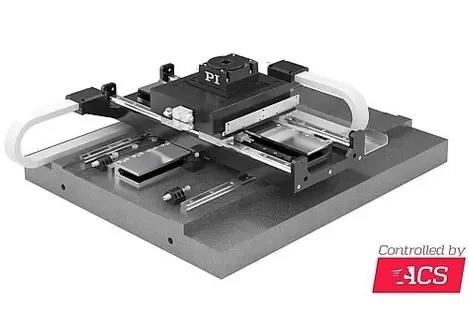
A 4-axis XYZ-Theta stage rails on granite system for wafer inspection and metrology. Here, a Z-stage with 360-degree access was used. Image Credit: PI (Physik Instrumente) LP
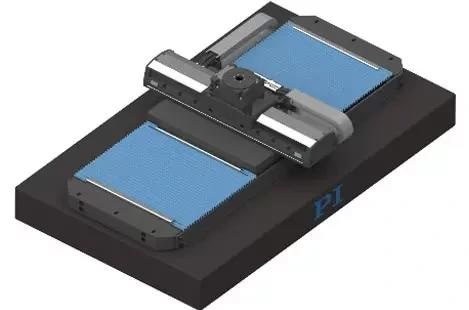
A 3-axis wide base rails on granite XY-theta stage with bellows for protection on the lower linear axis and seal strips on the upper linear axis. Image Credit: PI (Physik Instrumente) LP
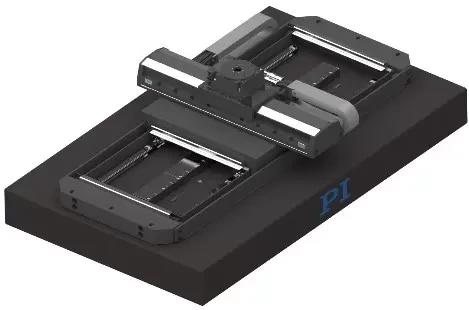
The same XY-Theta multi-axis rails on granite stage without bellows. Image Credit: PI (Physik Instrumente) LP
The precision motion systems depicted above consist of multiple stages for versatile motion. The 4-axis system on the left is tailored for substrate and wafer inspection and integrates mechanical rails directly onto the granite base.
Integrating rails on the granite base enables the creation of a more thermally stable and compact system.
In scenarios where protection against debris is necessary for bearings, motors, and encoders, the lower axis can feature integrated bellows with an internally isolated double-walled structure with a positive pressure air purge.
Meanwhile, the upper axes can feature linear stages with sealed construction utilizing sealed sidebands, hard covers, and positive pressure air purge—as demonstrated in the central and right images.
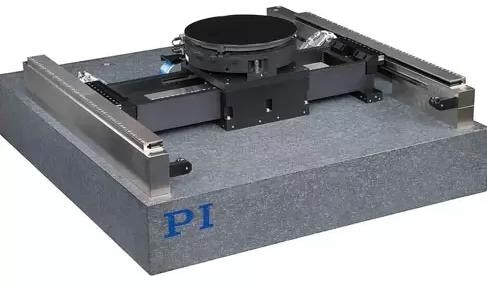
A 3-axis XY-Theta stage based on a gantry-type planar air-bearing XY-table carrying an air-bearing rotary table. The linear motor magnet tracks are mounted on the granite base, but due to the air-bearing principle, there is no contact at all. Frictionless planar XY motion is possible with magnetic bearings, air bearings, and flexures and provides better geometric performance than stacked XY stages. Image Credit: PI (Physik Instrumente) LP
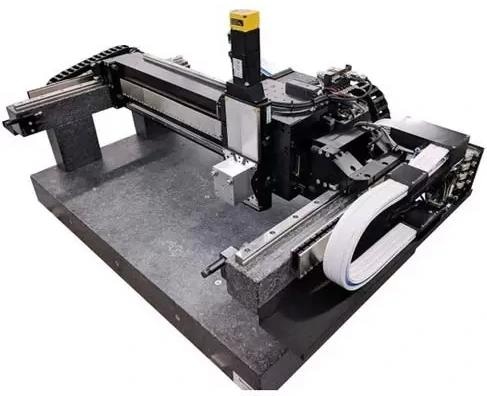
A 3-axis hybrid gantry stage with mechanical linear bearing rails and linear motor tracks mounted on granite and an air bearing on the cross axis. The Z-axis uses a ball-screw-driven stage with a 3-phase rotary motor, an absolute encoder, and a brake. Image Credit: PI (Physik Instrumente) LP
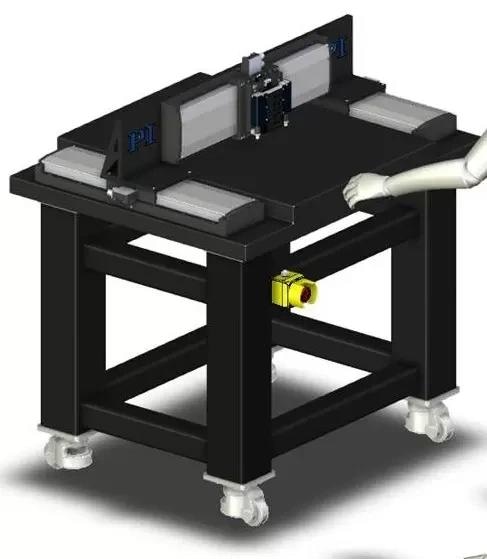
A 3-axis stage-on-granite gantry based on V-817 long-travel linear motor stages and a counterbalanced Z-axis with linear motors and air springs. Image Credit: PI (Physik Instrumente) LP
Options for the Z-axis: When the Z-axis is mounted on the XY-table, and comparatively short travel is necessitated, a wedge-type vertical translation stage serves as an excellent choice. This design allows for 360-degree access and removes momentum loads on the horizontal axes, as is the case with a linear axis vertically mounted on a bracket.
In split-bridge or gantry multi-axis positioning systems, the Z-axis is commonly mounted either directly on the bridge, the bridge-mounted X-axis, or the gantry cross-axis.
The ball-screw-driven L-511 linear stage is frequently employed in a vertical orientation, amplified with a brake and an absolute encoder, because of its high resolution and payload capacity.
For applications demanding higher-speed vertical motion, linear motor stages can be utilized with mechanical counterbalance, magnetic weight force compensation, or air springs to maintain the current to the linear motors at close to zero—except for when acceleration or response to external forces is needed.
Size and Form Factor: Rails-on-Granite vs Stage-on-Granite Multi-Axis Positioning Systems
Small improvements can arise through the granite motion system's unified design. In this scenario, the base plate of the bottom stage is removed, reducing both the center of gravity and height marginally. However, the majority of the other elements—from motors to sensors and cable tracks—are the same.
The Effect of Reduced Center of Gravity on Abbe Errors, Stiffness, and Lifetime
Removing the base plate from the individual stages lowers the working height and reduces Abbe errors. This positively affects the performance of work point positioning across multiple degrees of freedom.
Simultaneously, stiffness can be enhanced by removing an element between the moving platform and the granite base. This leads to a higher resonant frequency, which improves motion performance with reduced noise, particularly in the nanometer range.
Mounting rails on granite also facilitates a substantial increase in the stage base width, which significantly affects XY flatness and straightness accuracy, load distribution, and lifespan by minimizing bearing loads on the lower axis.
The Effect of Bearing Size/Spacing on Dynamics and Throughput, and Load Capacity
Both designs allow for similar mechanical and air bearings. However, when true planar XY motion is needed, air bearings stand as the only viable solution, apart from levitation or flexure guides.
When using mechanical bearings, the rail-on-granite design accommodates larger bearings without increasing the vertical height or center of gravity of the moving platform (unlike the stage-on-granite design), thanks to the removal of the machined metal base.
Utilizing larger bearings at a wider spacing in the lower axis offers numerous advantages in terms of roll stiffness, yaw stiffness, and pitch stiffness compared to an equivalent stage-on-granite multi-axis design.
Increasing the angular stiffness of a multi-axis precision automation system enables higher dynamics and overall throughput. Additionally, larger bearings provide increased load capacity or extended service life at the same load capacity.
Linear Motors, Screw Drives, Linear Encoders, Cable Management
No notable distinctions exist between a stage-on-granite multi-axis positioning system and an integrated granite motion system. Motor output, position resolution, and acceleration remain unaffected by the varying designs. The same holds for cable management, mechanical hard stops, or limit switches.
Environmental Considerations, Protection From Debris – Laser Processing
Various high-performance linear stages, such as the V-417 linear motor stage, already feature side seals, hardcovers, and air purging for debris ingress protection (IP 50). This is crucial, particularly in safeguarding bearings and encoders during laser processing or within industrial settings with debris-generating processes.
In this regard, a standard linear stage might hold an edge over a rails-on-granite solution.
Nonetheless, it is feasible to incorporate ingress protection measures (like wrapped bellows, air purges, and double-walled construction), into the rails-on-granite motion platform to shield the otherwise exposed bearings and encoders, as depicted in the concept below.
While this is not a concern in cleaner environments, exposed bearings and encoders can pose issues in the presence of contamination.
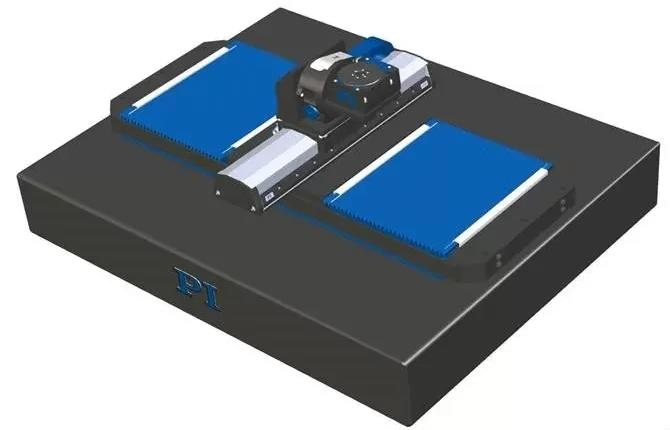
Multi-axis positioner with bellows-protected wide-base rails-on-granite bottom stage, V-417 linear motor stage with side seals, and Theta-X and Theta-Z precision rotary tables. Image Credit: PI (Physik Instrumente) LP
Serviceability/Maintenance
For multi-axis motion systems based on discrete stages, exchanging individual axes during maintenance is relatively straightforward. Direct drive, linear-motor stages tend to boast an exceptionally long service life—if bearings and motors are sized according to application requirements.
External events, such as a severe crash involving other application-related components (robots, improper workpiece mounting by the operator, and so on), may necessitate servicing or replacing a stage.
Keeping a spare on hand at the customer or the manufacturer via a service contract minimizes downtime and restores the machine online—more swiftly than it would take to replace and align distinct components in a rails-on-granite motion system.
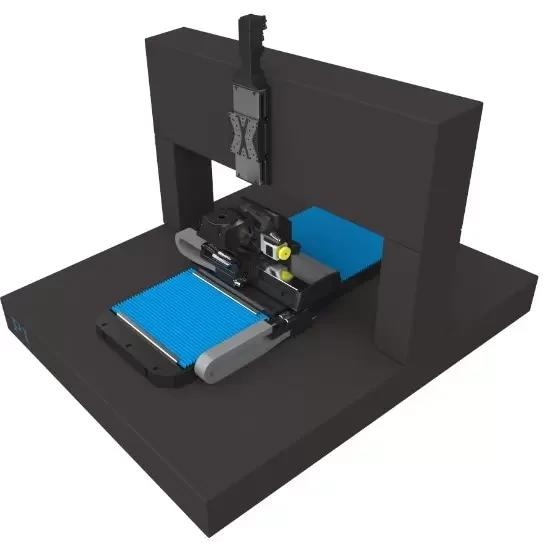
A 5-axis split-bridge rails-on-granite motion system with bellows to protect the wide-base lower linear axis from debris. Image Credit: PI (Physik Instrumente) LP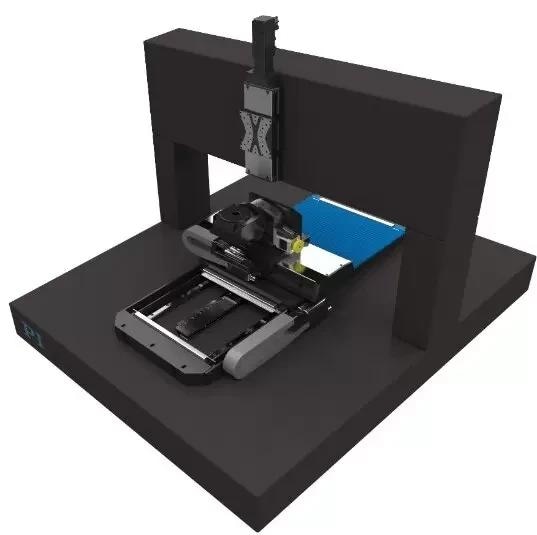
The same 5-axis integrated granite motion system without the protective bellows. Image Credit: PI (Physik Instrumente) LP
Cost Comparison of Integrated Granite Motion Systems vs Stage-on-Granite Motion Systems
Here, differences in cost primarily hinge on the level of customization and the number of identical systems needed by a customer.
Some cost and time savings can be anticipated when designing and constructing a single granite motion system utilizing existing off-the-shelf discrete stages, compared to a rail-on-granite motion system. However, when dealing with orders for multiple systems, the scenario can easily shift.
Naturally, this discussion assumes an apples-to-apples comparison with identical performance specifications, load capacity, accuracy, speed, and dynamics ratings.
Integrated Granite Motion Systems and Multi-Axis Positioning Systems From PI
PI, a prominent global firm, possesses design and in-house manufacturing capacities for numerous crucial technologies, components, and mechatronics systems that are essential to fulfill intricate nano-precision motion needs across industries like semiconductors, electronics, optics, photonics, and aerospace.
- Air Bearings: PI crafts its air bearings, and its teams boast extensive experience in crafting high-end air bearing motion systems.
- Piezo Ceramics: A dedicated division focuses on piezo ceramics optimized for ensuring highly reliable motion, canceling vibrations, and handling nanopositioning applications.
- Direct Drive Motors: Custom electromagnetic and non-magnetic ceramic motors are designed for PI's motion systems.
- High-end Motion Controllers: ACS advanced industrial motion controllers from PI are globally renowned for their exceptional performance and adaptability.
- Parallel-kinematic Hexapod Motion Systems: PI embarked on hexapod design and production in the early 1990s, specifically for precise optical information purposes.
- Positioning Sensors with Sub-Nanometer Resolution: PI devises various digital and analog nanopositioning sensors for its standard and tailored motion systems.
Leveraging extensive experience and a stream of innovation (with over 500 patents/patent applications), PI can deliver cutting-edge precision motion control solutions for automation, spanning from actuators with force and position control to customized motion platforms integrating mixed technologies.
Beyond motion hardware and control electronics, PI also provides software—including solutions for laser and galvo scanner control or dispensers for additive manufacturing.
For over 50 years, PI has stood as a dependable ally to the world's most pioneering companies, enabling it to surpass existing boundaries.
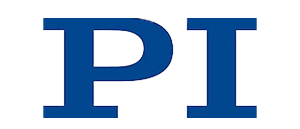
This information has been sourced, reviewed, and adapted from materials provided by PI (Physik Instrumente) LP.
For more information on this source, please visit PI (Physik Instrumente) LP.