In this interview, discover how ATLANT 3D's DALP technology is revolutionizing thin-film deposition, enabling rapid prototyping and advanced material applications in nanofabrication.
Can you please tell us about your background and your current role?
My name is Dr. Mira Baraket. I am the Vice President of Technology at ATLANT 3D. I have a background in advanced materials and nanotechnology, with experience spanning fundamental research and practical applications in energy and bio-devices fields.
I have worked at institutions such as the Naval Research Laboratory and the French Atomic Energy Commission, and I have also been involved in startups. ATLANT 3D is the second startup I have worked with.
Can you provide an overview of ATLANT 3D and its operations?
ATLANT 3D was founded in 2018 and is headquartered in Copenhagen, Denmark, where most of our activities occur. We also have entities in the United States and the United Kingdom, along with support from multiple distributors worldwide. In Asia, several distributors assist our customers with implementing our technology.
We are a team of 40 people with core expertise in material science, particularly in atomic layer deposition (ALD). We also focus on a range of application areas, including optics, photonics, microelectronics, and sensors. Our team includes software engineers, system engineers, a sales team, a business development team, and a strategic growth team, all working together to develop and deliver our products.
What is Atomic Layer Deposition (ALD), and what are its working principles and challenges?
Atomic Layer Deposition (ALD) is a technology that originated in the 1960s and 1970s. It is a deposition technique based on the reaction of two different gases to create layers of material. What makes ALD unique is that these gases do not react in the gas phase; instead, the reaction occurs directly on the surface of the substrate. This results in a very conformal technique that produces high-quality films.
The reason for this high quality lies in the sequential nature of the gas exposure. First, a gas is introduced to the substrate, and then a purging process is carried out before introducing the second gas. This purging step cleans the process chamber to ensure that the gases do not mix in the gas phase but only react on the surface.
The process goes like this: you send gas one, perform a purge, send gas two, and then perform another purge. As you can tell, this makes the process somewhat long and slow. Although ALD has been known for producing excellent film quality, this lengthy cycle has historically been one of its major drawbacks. As a result, while technology holds great promise, its slow deposition process has limited its widespread adoption in industrial applications.
What is spatial ALD, and how does it differ from traditional ALD?
Spatial ALD is a technique that improves upon traditional ALD by replacing the sequential and temporal approach with a continuous one. In spatial ALD, all the gases flow simultaneously over the substrate, and instead of opening and closing valves, the substrate moves between two different regions.
These regions, where the two gases are located, are separated by a shielding gas to prevent them from mixing. The substrate moves from one section to the other to be exposed to each gas. The quality of the material remains the same as in traditional ALD, but the process is much faster. This innovation has made ALD more widely applicable in microelectronics.
What innovation has ATLANT 3D introduced in relation to spatial ALD, and how does it benefit micro and nanofabrication?
What we have done at ATLANT 3D is take the concept of spatial ALD and shrink it down. The precursors are delivered to the surface in the same way as in spatial ALD, but now all the gases are delivered over a very small surface area, while the substrate moves underneath.
Our approach is different because the process is now partially localized on the surface, enabling direct patterning or direct processing. We achieve this using our patented micronozzle, which is customizable and scalable. The size and geometry of the nozzle can be adjusted depending on the application and the size of the pattern we want to deposit.
Our micronozzle technology has already been granted several patents across the world, and we are actively working on protecting our innovations, both on the hardware side and in terms of specific applications. The reason we developed this solution is because traditional lithography-based micro and nanotechnology processes involve many lengthy steps that have slowed down the innovation cycle.
For example, photolithography requires starting with a wafer, creating a photomask, performing exposure and development steps, and repeating the process multiple times. Our approach simplifies and speeds up this entire workflow.
What limitations exist in traditional cleanroom microfabrication processes, and how does ATLANT 3D’s technology address them?
In traditional cleanroom microfabrication, the processes are usually done using different machines, which means constantly switching between equipment and processing techniques. This leads to very high capital expenditure (CapEx) and operational expenditure (OpEx), along with the need for highly skilled personnel to manage complexity.
As a result, the innovation cycle becomes very slow. A limited number of materials and processes can also be used, because each tool is typically dedicated to a specific process or compatible with only certain materials. Traditional lithography steps like resist removal and liftoffs are ecologically harmful and generate significant waste.
What we are bringing with our technology goes beyond just deposition. We enable localized, multiple modes of processing. While I spoke earlier about ALD, our approach—DALP—includes various processing techniques. This means we can perform direct deposition, etching, doping, and cleaning, all with a single tool and a single micronozzle. Our technology enables both additive and subtractive processes, direct doping, direct 3D structure growth, and more—all localized and efficiently integrated in one system.
What is the Nanofabricator Lite, and how does it support digital manufacturing and accelerate innovation?
ATLANT 3D’s Nanofabricator Lite includes our DALP module. With advanced automation and precise gas system control, we are now enabling a very accessible approach to digital manufacturing. With just one tool, most of your time and focus can go into designing your experiment. You start by bringing in the design you want to print or process. Then, you prepare the nanofabricator by filling in the required materials and loading your samples. After that, you define and fine-tune your processing parameters.
Our nanofabricator comes with software that allows you to import your CAD design. You can visualize and simulate how the output will look, and during that process, you can still make edits and refine parameters for deposition or other processes. Once everything is ready, you launch your job. When it is finished, you end up with either a material, a process, or even a fully fabricated device, all created using our tool.
This technology is for device fabrication or prototyping. It enables a full lab-to-fab transition across the entire value chain. You can accelerate material and process innovation, develop micro-devices, or even move into manufacturing. Our roadmap includes mobile platforms tailored for specific application manufacturing.
Compared to traditional technologies, our system has significantly reduced the number of process steps. This leads to much faster innovation cycles, lower overall costs, and a more sustainable approach. There are fewer post-processing steps, reduced usage of precursors and chemicals, and you can directly create complex, multi-material patterns right on your wafers within the system.
In terms of sustainability, we are also reducing waste. It is not only because we are eliminating lithography and the post-processing steps through our direct patterning approach, but also because of the way our gas system is designed. Our nanofabricator system includes a unique gas delivery system that allows us to supply only a very small number of precursors, just what is needed for the process.
This is one of our core know-hows and stands in contrast to traditional ALD systems, which require significantly larger volumes of precursors.
How does ATLANT 3D’s DALP technology compare to ALD, inkjet printing, and lithography?
In terms of precision, both ALD and DALP deliver atomic-level precision. This is possible because of how the gases interact and react on the surface, allowing for highly controlled deposition thickness. Inkjet printing, by contrast, operates in the nanometer range at best, but more typically in the micrometer range.
When it comes to lithography, it is not a single technique, so precision depends on the combination of processes used. If we compare with methods like PVD or CVD, the precision is significantly lower. As for resolution, we can achieve patterning resolution below 100 microns, and in some cases as low as 2 microns, which is comparable to inkjet printing.
Where our technology truly stands out is in material versatility. ALD already supports over 400 materials, and with DALP, the potential expands even further. There are many ways to develop new materials through DALP. Inkjet, on the other hand, is limited in material variety due to the physical constraints of the technology. Lithography requires switching between various fabrication methods to expand material compatibility.
In terms of scalability, we have a clear product roadmap that supports scaling from prototyping to high-volume manufacturing. This is less developed in the inkjet space. As I have shown earlier, we are integrated across the entire value chain. And when it comes to innovation speed, developing new materials or bringing new processes to life, the time required with DALP is significantly lower compared to ALD, inkjet, or lithography-based techniques.
What materials can be deposited with ATLANT 3D’s DALP technology?
So far, we have tested and validated a wide range of materials. Primarily, we are working with oxides and metals. To cite some specific examples, we have successfully deposited platinum, titanium oxide, tin oxide, zinc oxide, and indium oxide.
We are constantly working on expanding this list, and we have already validated sulfides and fluorides as well. We are also actively developing a process that will soon allow us to include nitrides among other emerging materials.
What is the resolution size that can be achieved with DALP technology?
Back in 2019, when our technology achieved its first proof of concept, we reached a lateral resolution of 400 micrometers. As I mentioned earlier, our nozzles are customizable, and since then, we have made steady progress. In 2020, we improved it to 250 micrometers, and by 2022, with better process understanding and optimization, we reached 5 microns in deposition resolution.
Most recently, we had a significant breakthrough: we introduced a new type of nozzle that allows for variable line widths using the same nozzle. This means you can pattern different line widths directly on the same wafer without changing tools. It gives a whole new level of flexibility in patterning. We are confident that our upcoming technologies and processes will allow us to go beyond 1 micron in resolution.
This means that with our direct patterning capabilities, you are not only able to fabricate multi-material devices but also unlock entirely new ways of surface structuring at micron and even submicron levels.
How does ATLANT 3D’s DALP technology ensure alignment, precision, uniformity, and advanced material capabilities?
We work continuously to improve alignment, precision, and the uniformity of our deposits. Since we are creating actual devices, there are many cases where the deposition needs to be aligned with pre-existing patterns on the substrate. This makes accurate alignment extremely important, and we can achieve an alignment accuracy of one micrometer.
In terms of deposition precision and repeatability, we apply rigorous process controls and continuous quality assurance. Under controlled conditions, same material, same nozzle, and same process parameters, we have achieved a deviation in the deposition process as low as 1%. This level of precision can vary depending on the specific material, substrate, and nozzle configuration being used.
Regarding material uniformity, our technology allows for a high degree of consistency across the surface. Typically, we are better than 1% in terms of uniformity, which is essential for high-performance applications.
I would also like to bring the focus back to the fact that DALP process is not only limited to just deposition. It also enables etching, ternary material synthesis, and multi-layering. As I mentioned earlier, we have already qualified a range of materials including metals, oxides, sulfides, and fluorides, and we are actively working on adding nitrides to that list.
On the etching side, we have already confirmed and demonstrated etching processes for zinc oxide and aluminum oxide, and additional materials are currently in development. For ternary materials, we are in the proof-of-concept stage for compounds such as aluminum zinc oxide, lithium niobium oxide, and hafnium zinc oxide.
Multi-layering is an inherent capability of our DALP technology. We have successfully validated multi-layer structures using materials like titanium oxide and magnesium fluoride, and we have also achieved this with other materials including those based on aluminum and platinum.
Where is ATLANT 3D’s technology currently being used, and what are some concrete application examples?
I will share a few use cases to give you a better understanding. In terms of application areas, we see a wide span of interest across various industries. For instance, there is significant interest in optics and photonics in using our technology for fabricating optical filters and waveguides. In microelectronics and power electronics, there is strong demand for MEMS, sensors, and for localized passivation and etching, particularly in semiconductor and advanced packaging applications.
When it comes to emerging technologies, I would especially highlight neuromorphic computing, where we see a very strong alignment between the technology needs and the solutions we can provide. In addition, we are making a major impact on both fundamental and industrial R&D, whether that is through new material innovations, new processing techniques, or the development of novel device architectures.
With our technology, we are enabling complex patterning of multiple materials, and I will show you examples of some of the structures and materials we have directly deposited and patterned on wafers. But let me walk you through a few specific use cases to give you a better idea.
If we think about the materials development and the value chain, one of the key things that DALP enables is a rapid design of experiments for material and process development. Take an application like optics or photonics, where the goal is often to identify optimum material properties or conditions. With our technology, you can design your experiments very efficiently. For example, you can take a wafer and deposit multiple materials or vary the process conditions across many lines and regions.
In one case, we worked with titanium oxide, and we deposited numerous lines with varying thicknesses in different rows, while also varying the process temperatures. What we ended up with was a highly efficient development process that allowed us to generate 50 different data points for titanium oxide—all within six hours. To put this in perspective, achieving the same result using conventional technologies would have taken one to two weeks.
Another example is rapid process development and prototyping, specifically in high-performance thin-film transistors. In this case, we had pre-deposited contacts on the surface. Using our technology, we deposited zinc oxide under 24 different deposition conditions, all within a single day, on the same wafer. Each region on the wafer became a separate prototype. Compared to conventional methods, this would typically take two to three weeks to achieve.
Can you share more specific examples of how ATLANT 3D’s technology is being used in advanced applications?
One of the impactful use cases I want to highlight is what we call chip surgery. This is especially relevant in microfabrication, where even minor deposition errors can introduce significant downstream costs and delays. With our technology, we can scan the surface, inspect it, and if we detect any abnormalities or defects, we can instantly patch the area by drawing directly onto the surface. Then, after doing the patch or deposition, we re-inspect the surface and can continue with a seamless and continuous deposition.
In this specific case, we did it with platinum, and it is a great example of how we reduce not only costs and turnaround time, but also material waste, supporting a more sustainable fabrication workflow.
Another strong example is from device fabrication. We created multiple metal-insulator-metal (MIM) capacitors as part of a rapid design of experiment approach. What we did was vary the deposition process parameters to find the optimal performance conditions. After the DALP depositions, we were able to quickly characterize each variation and zero in on the most promising conditions.
We ran a similar experiment, where not only did we change the dielectric thickness, but we also used different deposition conditions for the top electrodes. This multi-variable approach speeds up innovation significantly because we are not limited to single-variable iterations.
This kind of direct processing of multi-material devices is a fundamental strength of our technology. Because we directly pattern onto the substrate, we can deposit multiple materials on the same device with high precision. In another case-study, we fabricated several components: MIM capacitors, electrochemical sensors, and even surface sensors made of platinum and titanium oxide. All of these were printed on the same substrate, and the entire process took just 34 hours, which is incredibly fast for this level of complexity.
Another powerful example involves microfluidics, where surface geometry challenges usually limit what can be fabricated. Traditional methods struggle with uneven surfaces like 90-degree walls and trenches, which are common in microfluidic channels. But with our DALP process, we can conformally deposit inside these structures.
And lastly, I want to share a case where we made a big difference in MEMS and optical device fabrication. We worked on a suspended chip, which is typically very difficult to handle using standard processing techniques due to its fragile and exposed geometry. But with our technology, we were able to deposit a protective layer directly onto the suspended structure, and we did this without altering the device’s properties. The entire deposition took just a few hours, showing how fast and gentle our process can be, even with delicate structures.
What does the ATLANT 3D product roadmap look like, and how does it support different stages of innovation?
Our technology is truly a lab-to-fab solution, supporting the entire innovation value chain—from early material discovery, through rapid prototyping, and into scalable manufacturing.
We have several products in our roadmap, each designed to address different stages of development and different substrate formats. For instance, with the Nanofabricator Lite, we are enabling fast material innovation and process development on coupons and small wafers. It is ideal for early-stage research and proof-of-concept work.
Then we have the Nanofabricator Pro, which is built for industrial R&D and low-volume production. It supports 4-, 6-, and 8-inch wafers, giving our customers flexibility in transitioning from research to pilot-scale manufacturing.
Looking further ahead, we are also thinking about long-term scalability. Our nanofabricator systems are cluster-tool compatible, which allows them to be integrated into fully automated production lines. That is already the case with the Nanofabricator Lite, which can be connected as part of a cluster setup.
In addition, we offer a more application-specific tool called the Nanofabricator Flow. This is a platform designed for dedicated applications, where we can combine multiple digital manufacturing tools into a single integrated system—customized to specific customer needs.
From a business model standpoint, we of course sell equipment, but we also work closely with customers through innovation-as-a-service. This includes pilot programs, R&D services, and joint development projects. A lot of our progress comes from these collaborations.
Long-term, our vision is to significantly accelerate the innovation cycle. One way we are planning to do this is by building what we call the A-Hub. This would be a centralized innovation ecosystem, equipped with our manufacturing platforms and characterization tools, enabling users—from academia to industry—to go from R&D to prototyping to production all in one place.
Ultimately, our mission is to drive atomic-scale manufacturing forward. By expanding into new application markets with modular, versatile platforms, we are enabling broader adoption—and with the A-Hub concept, we are building the foundation for a global innovation network focused on advanced manufacturing.
About Mira Baraket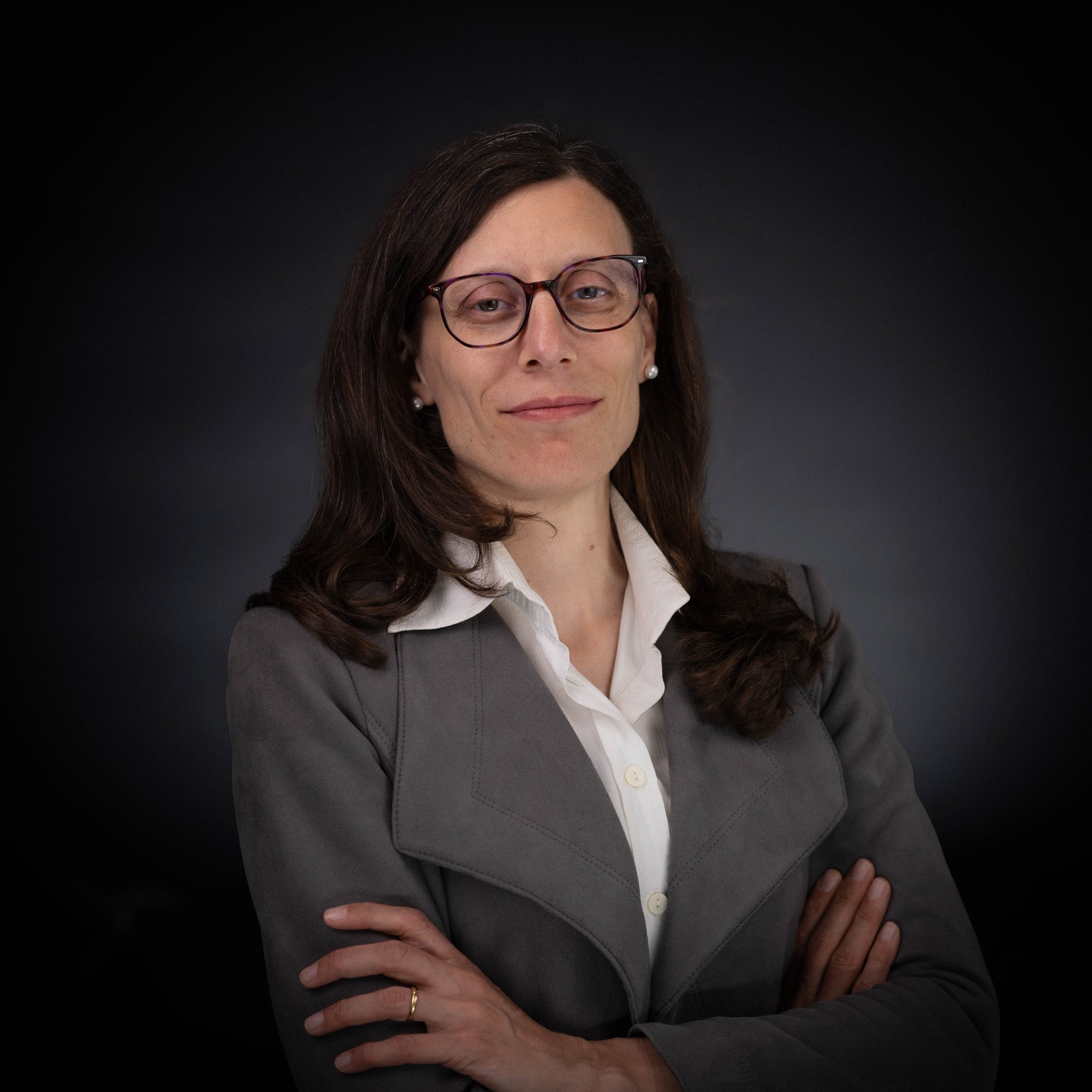
With over 18 years of experience in advanced materials and nanotechnology, Mira Baraket has worked at the intersection of research, industry, and innovation. She has been involved in both fundamental research and practical applications, starting from top institutions such as the Naval Research Laboratory in Washington, DC, the French Atomic Energy Commission, and the Néel Institute to innovative startups specializing in advanced materials and technologies, including General Graphene Corp and, most recently, ATLANT 3D.
Mira has worked within the industry to translate scientific discoveries into real-world solutions in fields such as energy, healthcare, and electronics. Her experience spans from developing new materials to exploring how emerging technologies can be scaled and applied across different industries.
In her current role at ATLANT 3D as VP of Technology, she leads the development and advancement of Direct Atomic Layer Processing (DALP) technology and products. She works closely with scientists, engineers, and industry partners to push the boundaries of innovation, ensuring that cutting-edge research translates into scalable, real-world applications.
Passionate about bridging science and industry, Mira focuses on how innovation can meet market needs and create meaningful impact. Whether working in research, product development, commercialization, or business development, she enjoys integrating technology and strategy to drive progress.
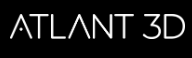
This information has been sourced, reviewed and adapted from materials provided by ATLANT 3D Nanosystems.
For more information on this source, please visit ATLANT 3D Nanosystems.
Disclaimer: The views expressed here are those of the interviewee and do not necessarily represent the views of AZoM.com Limited (T/A) AZoNetwork, the owner and operator of this website. This disclaimer forms part of the Terms and Conditions of use of this website.