High force and compact design are combined with a piezoelectric stick-slip inertia drive in PI’s newest stage.
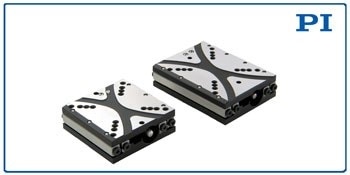
PI (Physik Instrumente), a top provider of precision motion control and positioning solutions for more than 4 decades, announces the release of a new compact linear stage, just 45mm wide, which combines high positioning accuracy with higher force and velocity than conventional inertia drives. The space-saving Q-545 provides advantages for use in research and OEM instrumentation that require positioning precision and alignment, such as photonics, bio-technology, nanotechnology, precision-optics, life-sciences, or medical design.
How It Works
Stick-slip drive motors, lacking gears, are powered by the natural difference in the static and dynamic friction coefficients found between two surfaces. This direct linear motion drive principle reduces the number of components that can wear, making the stages more compact, reliable, and cost efficient. In addition to a number of standard product variations with 0.5” and 1” travel, PI stages and drives can be customized for OEM production quantities.
Watch Video of Different Types of Piezo Motor Designs >
What is a Piezo Motor? How does it work? Piezo Motor Designs for Automation & Motion Control | PI
Self-Clamping at Rest, High Force and Stability
With holding force of 8N and maximum velocity of 10mm/sec, the self-clamping motor design provides long-term power-off position-hold capabilities without the need for a brake -- a space and energy saving advantage.
Nanometer Precision Encoder Option
The stages can be run in open and closed-loop. A high resolution option with integral linear position encoder providing 1 nanometer resolution is also available. Nonmagnetic versions and an ultra-high-vacuum version for pressures of 10-9 hPa are optional.
Specifications, Datasheets, More Information
http://www.pi-usa.us/products/Compact_Positioning_Stages/index.php#Q545
Features & Advantages
Self-Clamping High Precision Ceramic Motor
XY Configurations
Linear Encoder Available
8N Feed Force
13 and 26mm Travel Range
10mm/sec Max. Velocity
Standard and Custom
PI has in-house engineered solutions with over 4 decades of experience working with customers to provide products that meet application demands, and can quickly modify existing product designs or provide a fully customized OEM part to fit the exact requirements of the application. <