Before humans discovered ultrasound for a variety of medical, technical and military applications, nature had perfected it over millions of years for navigation under and above water. Dolphins and bats are but two species who mastered its transmission, reception and real-time processing.
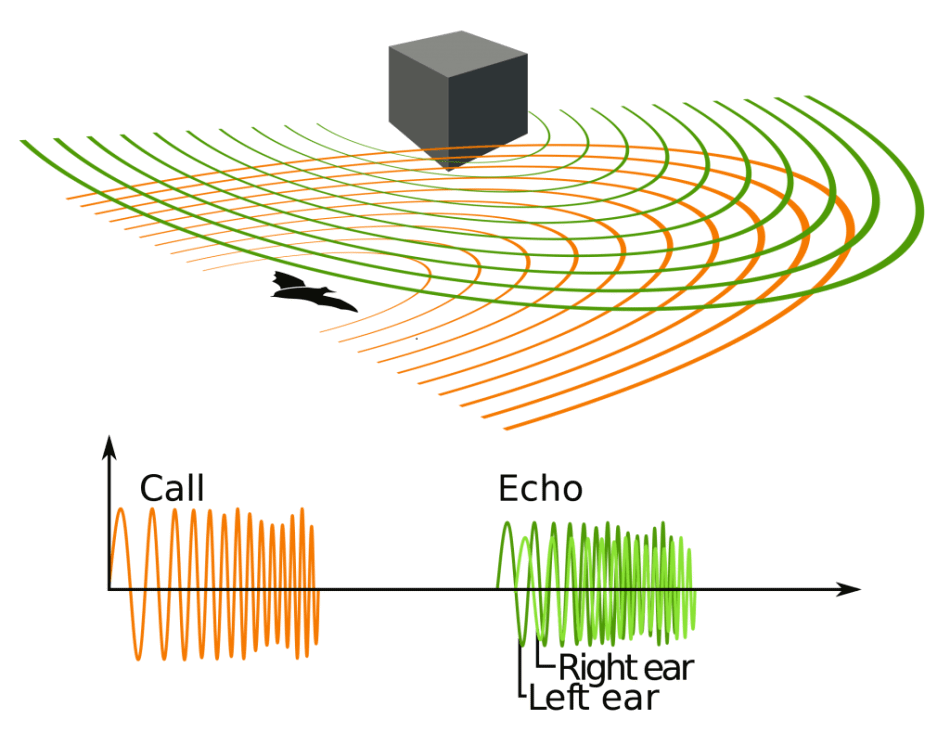
Echolocation of a bat based on transmission, reflection and reception of ultrasound. (Image: Petteri Aimonen, Wikipedia)
Frequencies above 20 kHz – more than the hearing range of the human ear – are called ultrasound. What works extremely well in nature has also found many applications in scientific research and industrial and medical engineering. Examples include filling level or flow rate measurements, distance measurement and object recognition, bonding or welding, medical diagnosis and therapy, and high-resolution material testing. Electro-ceramics materials that produce electricity when a force is applied, and change their shape when an electric field is applied, work extremely well for these applications. Usually the class of piezoelectric ceramics is used since it is possible to manufacture them in a cost-effective manner in many shapes perfectly matched to the application requirements.
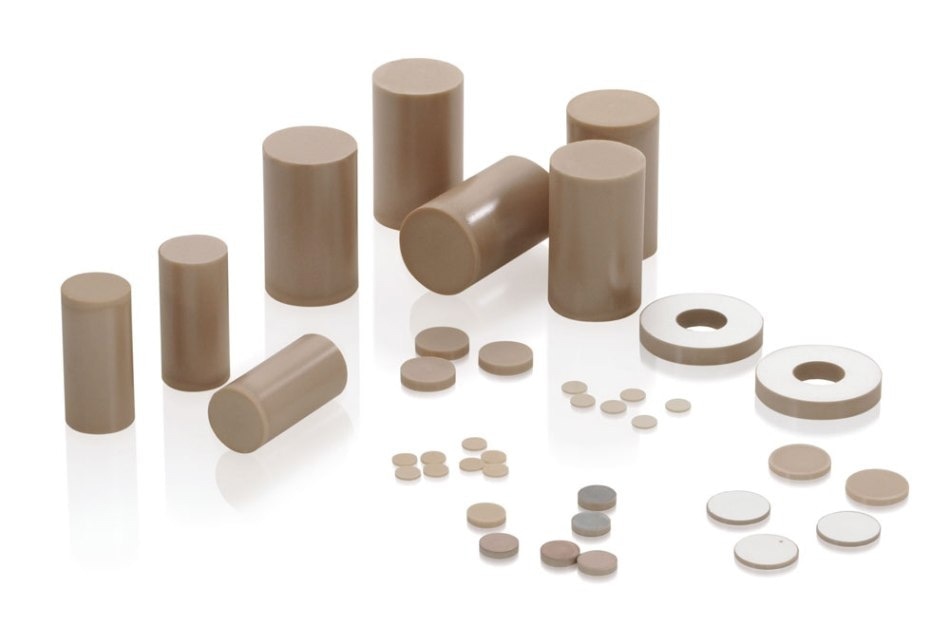
Lead-Free Piezoelectric Materials for sonar and hydrophone applications. PIC700 material from PI Ceramic is the first lead-free piezo ceramic material on the market. PIC700 is based on bismuth sodium titanate (BNT). It has very similar characteristics to barium titanate materials and is suitable for ultrasonic transducers in the MHz range and for sonar and hydrophone applications. (Image: PI Ceramic)
Piezoelectric materials modify their dimensions when an electrical field is applied (inverse piezo effect) and generate an electrical charge when a force is applied (direct piezo effect). In other words, they transform mechanical power into electrical power and vice versa, and this the reason why they are frequently referred to as transducers. Piezo transducers are based on solid state effects, and are fundamentally free of wear and tear. The inverse piezo effect lends itself particularly for precise and fast motion generation, while the direct piezo effect can be used for sensor applications.
Frequencies and Amplitudes
Piezo elements begin to oscillate when an AC voltage is applied. The very fast response in the microsecond range and below allow for ultrasound generation with frequencies of up to 20 MHz.
It is possible to classify ultrasonic applications in sensor applications and power ultrasound where the energy densities are higher and frequencies range from 20 to 800 kHz.
Power ultrasound can be used in medical applications, for example, industrial processes, such as cleaning and bonding or welding, for removing dental plaque and to crush kidney stones.
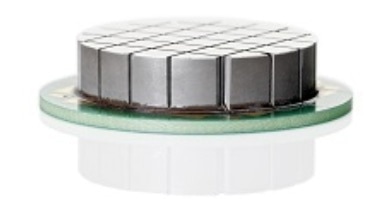
Piezo ceramic in an array structure for generating directed ultrasound. (Image: ELAC)
Design Flexibility
In addition to the material selection, different resonant frequencies and geometric variants can be realized in order to optimize the transducer for the respective application. While most common piezo transducers are based on PZT formulations, lead-free PIC700 material is currently available, ideal for ultrasonic transducers in the MHz range and for hydrophone and sonar applications; components such as disk or plate shaped transducers in thickness vibration mode, piezo tubes, piezoceramic rings, and shear elements are available on very short notice on the basis of semi-finished products in stock. OEMs mostly need custom geometries with integration in the final product. This includes the contacting of the elements based on customer specifications as well as mounting in provided components, potting or gluing of the ultrasonic transducers.
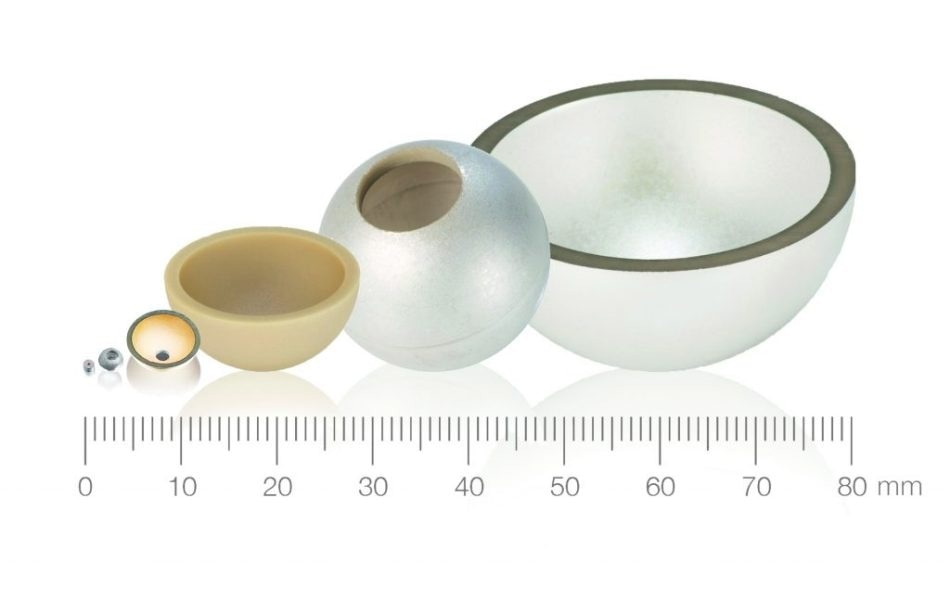
Spherical and hemispherical piezo ultra-sound transducers.
Ultrasound Transducers, Piezoelectric Transducers, Pumps, Medical Piezoelectric Transducers
Watch Piezo Technology & Applications of Ultrasonic Transducers, Pumps, Medical Equipment.
Flow Measurement, Filling Level Measurement
Piezoceramic components have a diverse range of applications. The inverse and direct piezo effect is used in ultrasonic measurement of propagation times. The measurement of filling levels is considered to be a typical application for propagation time measurement. Unlike the biological solutions where receiver and sender are separate – superfast muscles in the bat’s larynx produce the sound while highly sensitive ears detect the reflection – a piezo transducer can work as both a receiver and a transmitter, almost simultaneously. The filling medium reflects the ultrasonic pulse that is transmitted. The propagation time needed is a measure of the distance traveled in the empty part of the container.
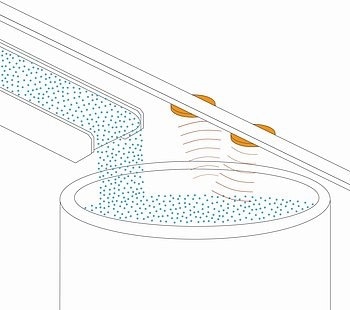
Level Measurement by Ultrasound: Similar to park distance sensors, piezo transducers can be used for level measurement. The principle is based on ultrasound pulses reflected by the filling medium with the piezo transducers (transmitter and receiver) placed outside the medium. The measured distance is proportional to propagation time, while the precision is influenced by the shape and texture of reflecting surface. (Image: PI)
Flow measurement is based on the propagation time difference during alternate transmission and receiving of ultrasonic pulses both in and against the flow direction. Here, two piezo transducers functioning as both receiver and transmitter are arranged diagonally to the direction of flow in an acoustic path. With the Doppler Effect, the phase and frequency shift of the ultrasonic waves, which are scattered and reflected by liquid particles, are examined. The shift in frequency between the reflected wavefront emitted and received by the same piezo transducer is proportional to the flow speed. A number of other tasks can be efficiently solved in a similar manner, such as high-resolution tests or object recognition.
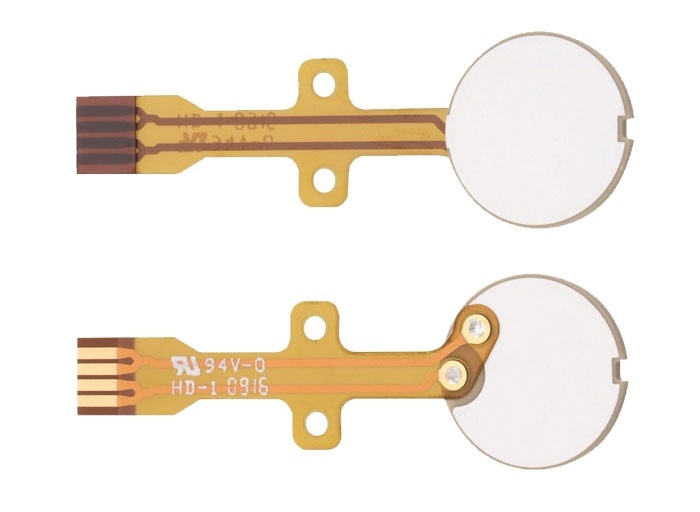
Piezo transducer discs with flexible PCB facilitate integration. (Image: PI)
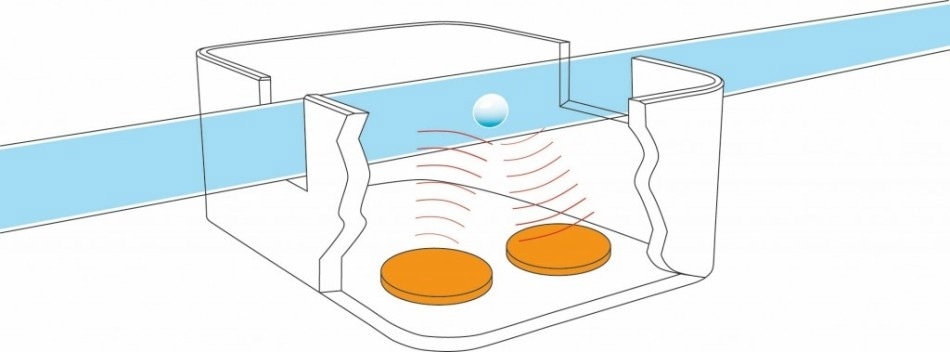
Flow measurement with piezo ultrasonic transducers. The propagation time measurement is based on the alternate transmission and receiving of ultrasonic pulses in and against the direction of flow. (Image: PI)
Piezo Transducers for Oil Field Services / Downhole Applications
Piezo transducers have successfully been employed in oilfield services industry. Examples of these versatile elements have been recently illustrated in “marine seismic survey, sonic logging-while-drilling, precision pressure measurement, and ultrasonic bore-hole imaging” which is a paper by Goujon N, Hori H, Liang KK, Sinha BK.
Out-of-this-World Applications for Piezo Transducers
An even more extreme application of piezo transducers can be discovered on the science lab onboard the Mars Rover Curiosity. Here, piezo transducers help produce drill samples for the X-ray diffraction and fluorescence spectrometry system that will enable Scientists to figure the possible existence of life on the red planet.
Flexible Piezo Transducers / Patch Transducers
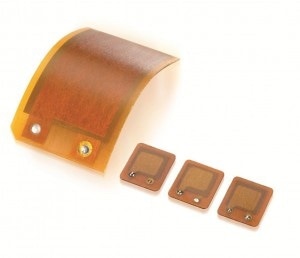
Different sizes of DuraAct flexible patch transducers. (Image: PI Ceramic)
Piezo patch transducers can be designed in order to provide multiple functions in an extremely compact and flexible package. The whole transducer itself becomes bendable by embedding the ceramic patch into a laminated flexible polymer material.
Applications include active vibration damping by integrating a piezo sensor with a closed-loop controller and an actuator for active vibration cancelation, fast switching and structural health monitoring.
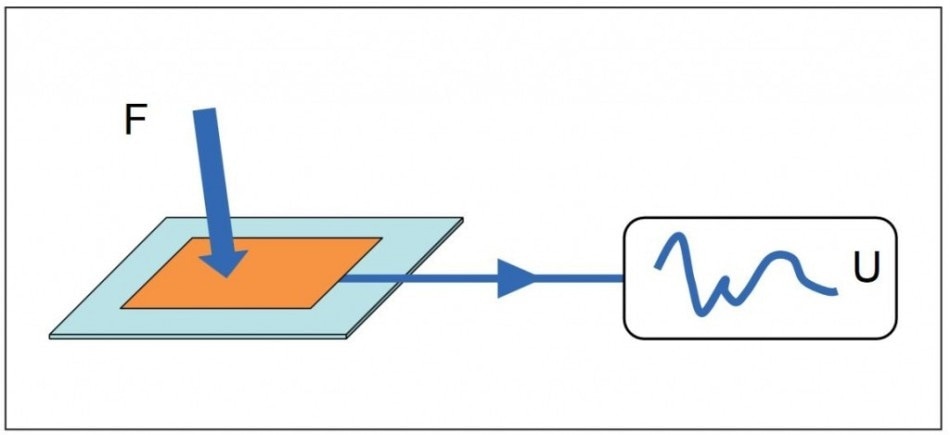
Direct Piezoelectric Effect.
The direct piezoelectric effect (shown above) takes place when a force on the piezo ceramic substrate or a deformation or deflection produces an electric field, and thus a voltage/current that can be amplified and is proportional to pressure or strain. This effect works from DC to high frequencies if contact between the piezo transducer and the structure is good.
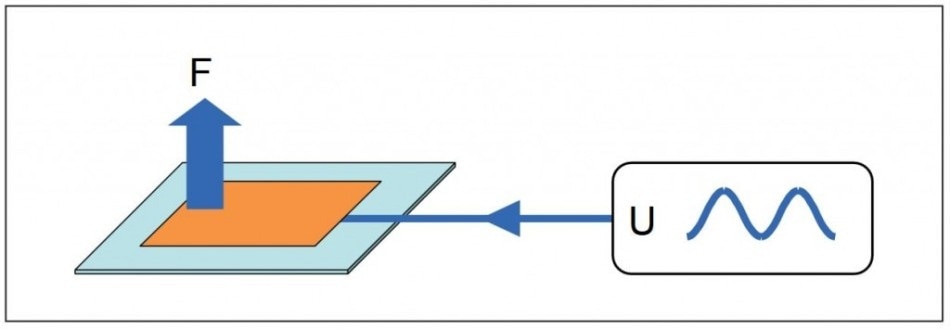
Inverse Piezoelectric Effect.
The inverse piezoelectric effect (shown above) takes place when an electric field is applied to a poled piezo material, resulting in a deformation that can be used to produce a force or a displacement. If the transducer is glued to a structure, it is considered to be suitable for actively controlling the structure, damp vibrations, etc.
Using inverse and direct piezo effect (shown below) in a structural health monitoring system, one piezo transducer is electrically excited to induce vibration which can be detected by a multitude of piezo transducers operated in sensor mode. Conclusions on the state of the structural health can be drawn by evaluating the excitation signal and the various senor output signals.
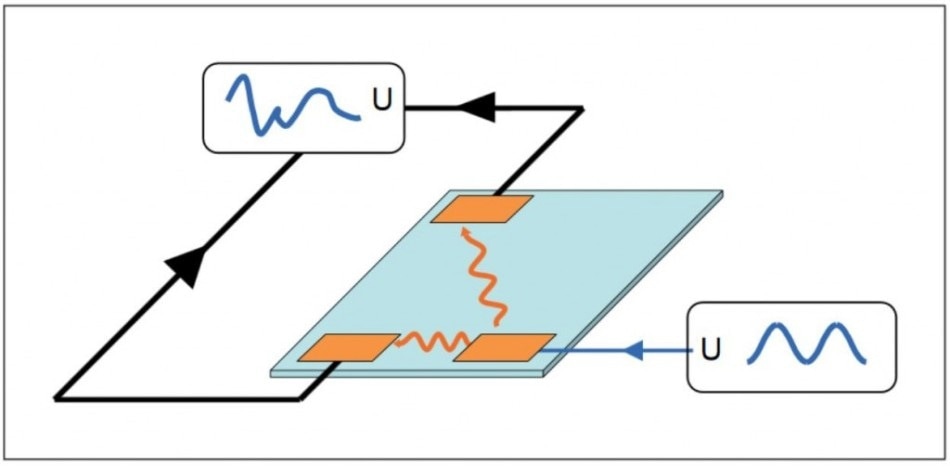
Structural health monitoring system, using the direct and inverse piezo effect.
Medical Transducers and Nano-liter Dosing
Piezo elements and transducers have also become crucial in medical engineering. In addition to propagation time measurements such as in air bubble detection (Air In-Line sensing), typical applications are in dosing and pumping. The dosing amounts range from the microliter and nanoliter range to the picoliter range. Here, piezo-based precision systems excel because of their minute dimensions, low costs and low energy consumption. The same also applies to devices for aerosol generation, in which a piezo element excites a diaphragm to ultrasonic vibrations. The frequency is approximately 35 kHz. Due to the resulting pressure changes at the diaphragm, the fluid is pressed through the holes in the diaphragm and is thereby aerosolized.
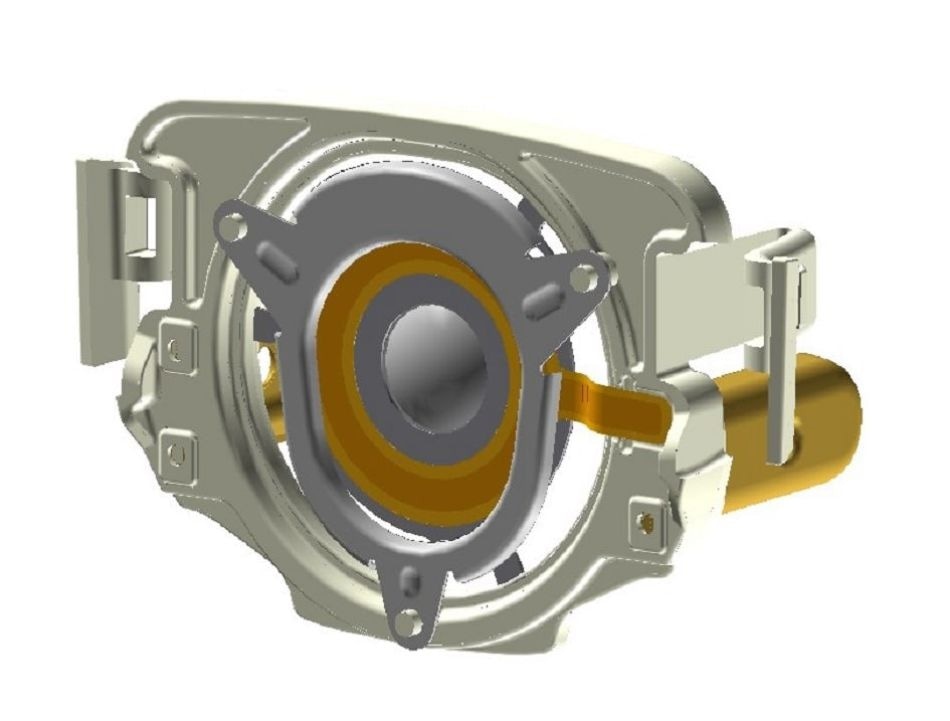
Aerosol generation with ultrasonic piezo transducer. The piezo ring is directly glued to the metal ring of the diaphragm. When an AC voltage is applied, the piezo element oscillates with a frequency of approx. 35 kHz (Image: Pari Pharma/PI)
Ultrasonic transducers are also becoming main stream on surgical instruments for minimally invasive surgery as they are capable of replacing traditional scalpels, thus providing the Surgeon more control while reducing injuries to vessels and nerves. It is possible for some ultrasonic tips to simultaneously cut and cauterize tissue, resulting in a quicker recovery. Dental Hygienists use ultrasonic scalers in order to remove dental tartar and plaque – and Urologists depend on high-power piezo sound transducers for shock wave lithotripsy, which involves crushing kidney stones into small particles.
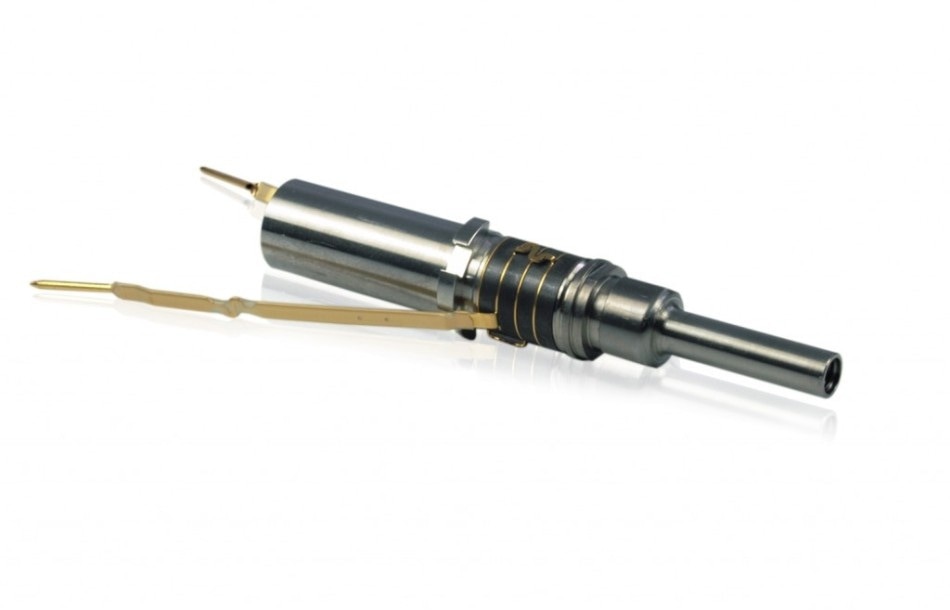
Instrument for ultrasonic plaque removal (OEM product). The dark rings are piezo disks with copper electrodes in between. (Image: Sirona)
Welding and Cleaning with Power Ultrasonic Piezo Transducers
Power ultrasound is used for bonding of minute wires in semiconductor chip manufacturing and industrial welding of plastics. Ultrasonic cleaning is another industrial application that is also used in semiconductor manufacturing and microsystems technology.
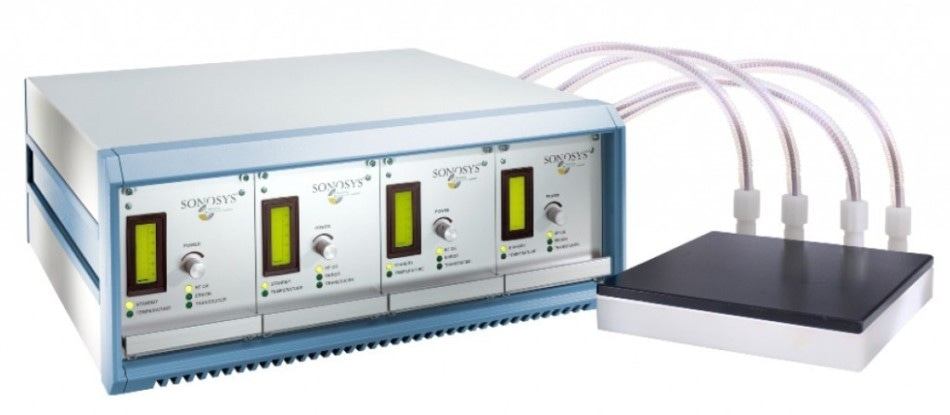
High-frequency ultrasonic cleaning systems offer effective support for cleaning, etching, and development processes in the semiconductor industry (Image: Sonosys)
The challenge with micro-systems cleaning is to prevent damage to smallest structures on the surface to be cleaned. High frequencies in the range of 700 kHz to 3 MHz offer the best results without damage. With these systems, contamination particles in the nanometer range can be removed in an reliable manner without causing any damage to the sensitive surfaces by excessive temperatures and pressures. The functional principle is shown below.
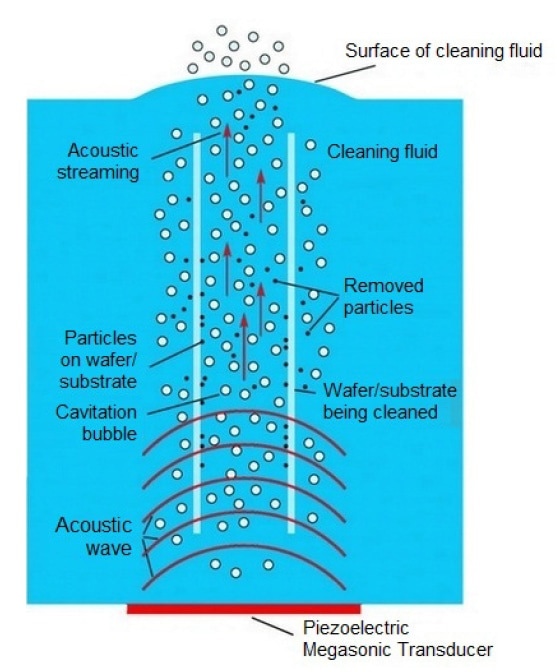
Principle of Megasonic cleaning (Image: Sonosys)
The ultrasonic system is made up of three components: the ultrasonic transducer/oscillator, the electronic ultrasonic generator, a piezo element and also a special cleaning fluid, selected based on the cleaning task.
The ultrasonic generator transforms the supplied AC current of 50/60 Hz to a frequency equivalent to the operating frequency of the transducer. The transducer in turn transforms the discharged electric energy into mechanical acoustic oscillations causing the surrounding fluid to oscillate. Every single oscillation leads to an over-pressure and low-pressure phase in the fluid, based on whether the transducer contracts or expands. During the low-pressure phase, small cavities (cavitation bubbles) develop in the fluid because of the fluid’s limited tensile strength. The bubbles implode during the over-pressure phase. Dirt particles are removed when bubbles implode at the surface of the item to be cleaned.
Summary
Ultrasonic piezo transducers have widespread usage in applications ranging from medical to semiconductors. Since there is no one-size-fits-all solution, a Manufacturer will have to provide flexibility in materials, mechanical design and the enthusiasm to work with customers from markets as diverse as semiconductor technology, chemical engineering, medical engineering and nano/bio-technology. The potential to control all critical manufacturing steps reduces the design cycles and time to market – a fact that is greatly valued by OEM customers.
The Piezoelectric Effect, Manufacturing Processes: How do Piezoelectric Transducers work?
Insights into piezo transducer manufacturing processes at the PI Ceramic factory.
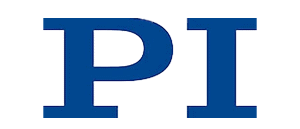
This information has been sourced, reviewed and adapted from materials provided by Physik Instrumente (PI) GmbH & Co KG - Worldwide.
For more information on this source, please visit Physik Instrumente (PI) GmbH & Co KG - Worldwide.