Hexapod multi-axis motion and positioning platforms have been around for several decades. Initially used for exotic applications, these six-legged parallel-kinematic machines are now becoming popular in a wide range of industrial automation applications after “learning” how to directly communicate with PLC controllers or CNCs through EtherCat® interfaces.
Starting out in high-end photonics and semiconductor test and manufacturing applications, even the automotive industry has adapted them for numerous high precision production processes that would be hard to realize without them. Today, these six-axis positioning systems are available with a load capacity from 0.5kg to more than 2000kg and motion ranges from a millimeters to 10's centimeters, while preserving sub-micron precision. Hexapods are now employed for aligning the tiniest optical components in the newest Silicon Photonics production processes, as controlling automated labeling machines and positioning full body parts for automotive production.
The complex Hexapod features contribute to a wealth of new possibilities in robotics.

Video: Hexapod 6DOF Platforms - 6-Axis Motion / Positioning Systems, for Multi-Axis Automation | PI
Comparison of serial and parallel kinematics 6-axis motion mechanics (Image: PI)
There are two techniques for constructing multi-axis positioning systems — serial kinematics and parallel kinematics. Stacked serial kinematic systems are easy to design and control. However, there are several drawbacks compared to the more powerful and sophisticated group of parallel kinematic machines.
Parallel Kinematics and Their Advantages
Each actuator in a serial-kinematic multi-axis system is allocated to precisely one degree of freedom. When position sensors are incorporated, they are also each assigned to one drive and only measure the motion on the equivalent positioning axis. Any unwanted motion in the other five degrees of freedom, which for instance, occur due to guiding errors of the individual axes, cannot be compensated or detected. In contrast, in a Hexapod, all actuators directly drive the same platform. The accumulation of drive train and guiding errors – usual with stacked systems – does not happen with well-designed parallel kinematics.
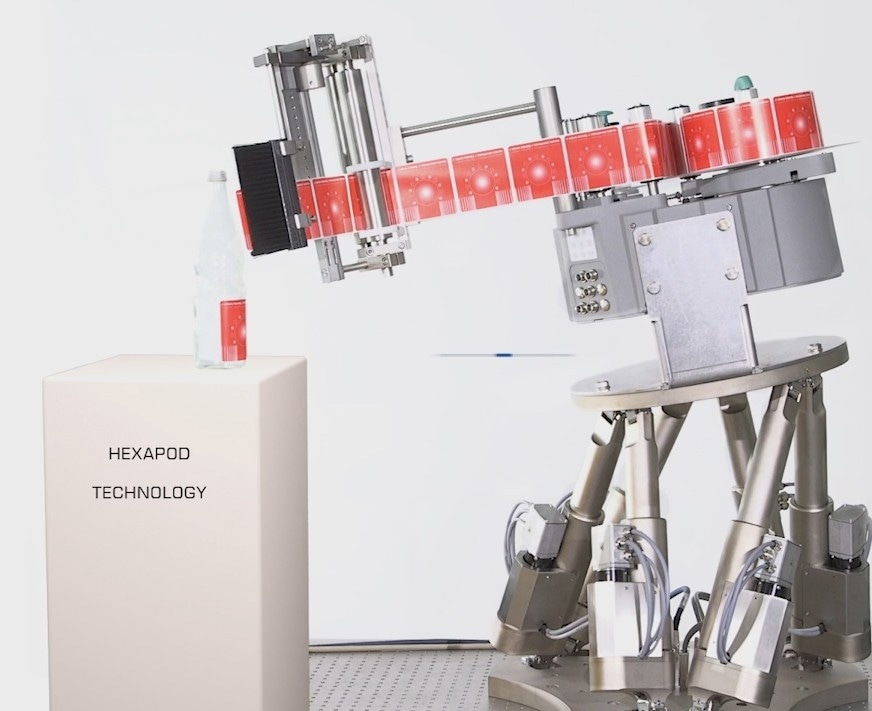
PI Hexapod in Industrial Automation | Bottle Labeling facilitated | Programmable Flexible Adaptation
Hexapod in a labeling robot prototype (Image: Tirelli / PI)
Hexapods do not have any dragged cables, minimizing torque or friction on the motion platform while boosting lifetime. Furthermore, Hexapods are more compact, stiffer and along with a considerably reduced inertia (moving mass), can provide quicker response and settling resulting in repeatability, higher dynamics and accuracy.
Mechanics, Controls, and Software
While the mechanical design is important for accuracy, repeatability, stiffness, and lifetime, and a number of details such as spherical rolling joints which look like a good idea at first glance turn out to be a dead end, the versatility and flexibility rely on the software and controller.
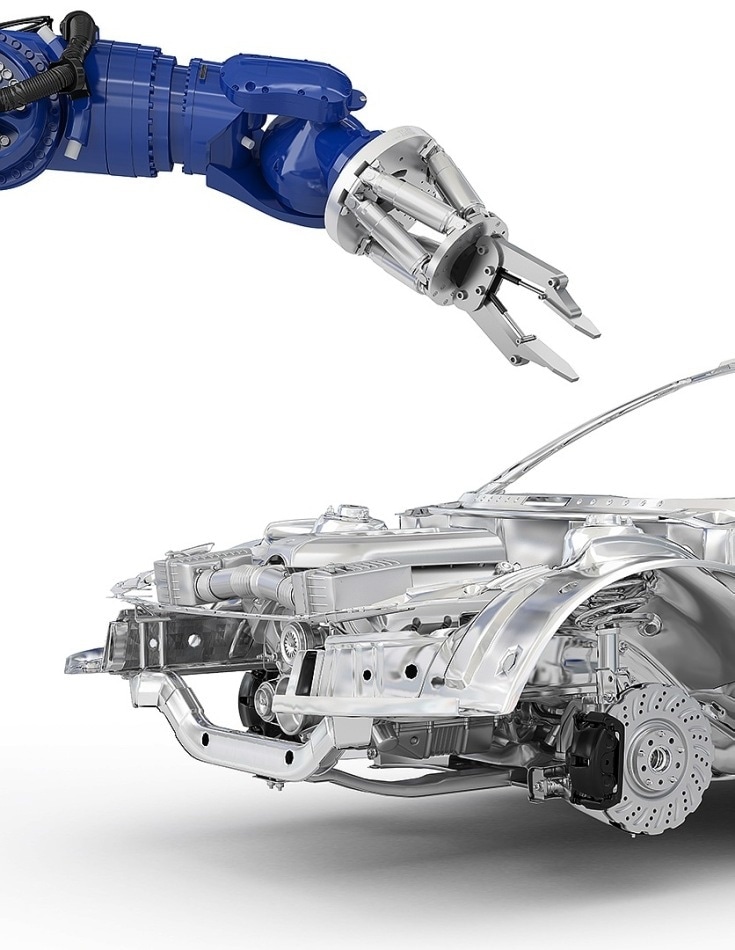
Hexapod six-axis positioning systems are available with load ratings from 2 kg to 2000 kg and travel ranges from just a few to several hundred millimeters, providing precision in the sub-micrometer realm. Applications include alignment of Silicon Photonics components, semiconductor manufacturing, as well as the positioning of entire body parts in automobile production. (Image: PI)
For instance, unlike with serial kinematics, if users want to move a platform in only one axis, the controller has to alter the lengths of each strut – some will contract and some will extend. The necessary coordinate transformations and path calculations need a robust controller capable of operating hundreds of thousands of operations per second, because there is no linear reliance on the current coordinates. The stiffest mechanical designs are based on cardanic joints with an offset between the axes, making the math even more complex.
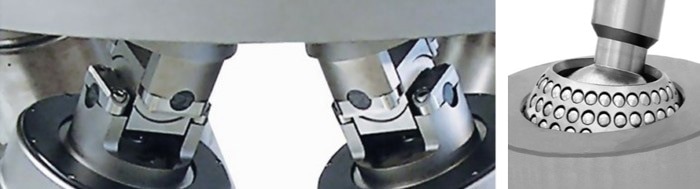
Robust Hexapod joints:
(left) Cardanic joints with Z-offset provide the highest stiffness, and best orientation-independent performance but require more advanced algorithms.
(right) Spherical bearings are not recommended due to their lower stiffness and directional dependency. (Image: PI)
Usually, there is no analytical solution, and CPU-intensive, iterative algorithms are needed to recalculate the intricate Hexapod kinematics for all the steps. All of this is transparent to the user who does not have to worry about applying the Hexapod kinematics on the PLC.
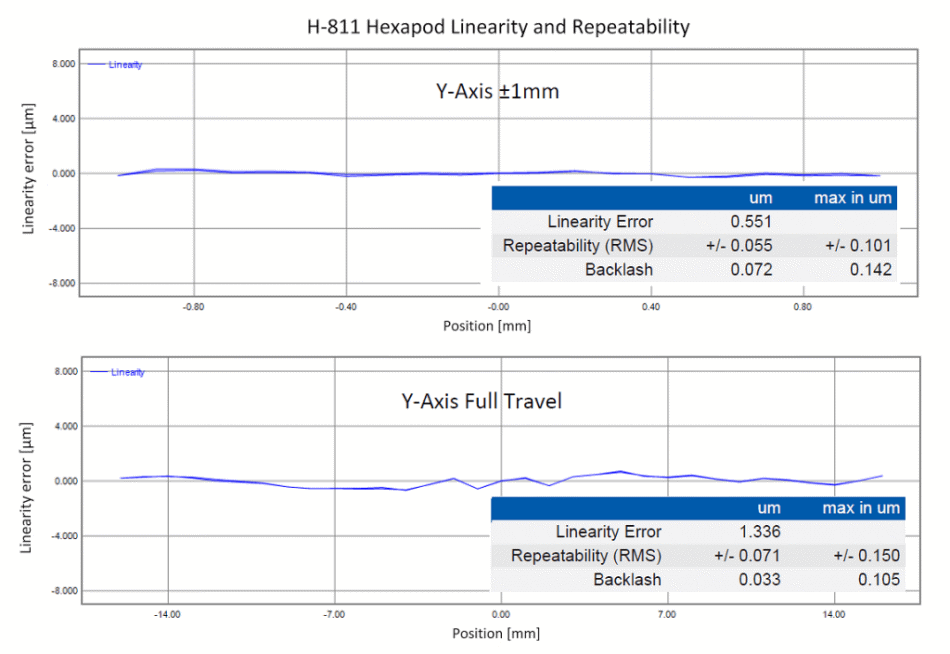
Hexapods with cardanic Z-offset joints combine high stiffness with high precision as shown in the graphs above. Here, Y-axis motion of an H-811 hexapod is measured with a laser interferometer, to determine linearity and repeatability. For full travel moves, the RMS repeatability is ±71nm and ±55nm for 2mm travel. The X and Z performance is on the same level. (Image: PI)
A dedicated digital Hexapod controller, incessantly improved over three decades, serves motion with sub-micron precision by firmly controlling each actuator in real time. Rotary and linear motion of the system is simply commanded in Cartesian coordinates.
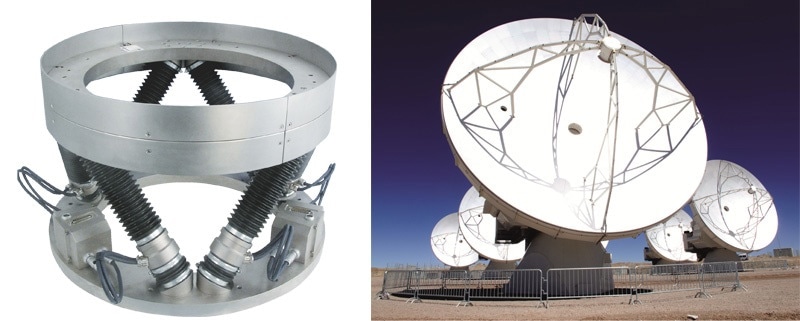
Weatherproof Hexapods, such as the H-850k model shown above, align the secondary reflectors in the world’s largest astronomical telescope: The ALMA observatory in Chile (Image: PI)
A vital feature of the Hexapod system allows the adaptation of both the position and the alignment of the reference coordinate system and the pivot point using basic software commands.
To match the trajectory perfectly to the necessities of the application, work and tool coordinate systems can be defined referring to the position of the tool or work piece. This task saves valuable time in photonics alignment and industrial automation tasks.
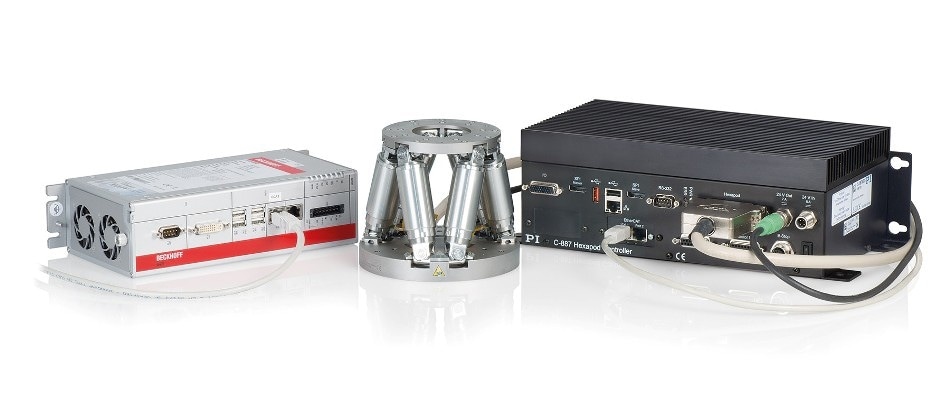
All functions of the PLC standard languages can be used for controlling the Hexapod systems – a proprietary language is not required. (Image: PI)
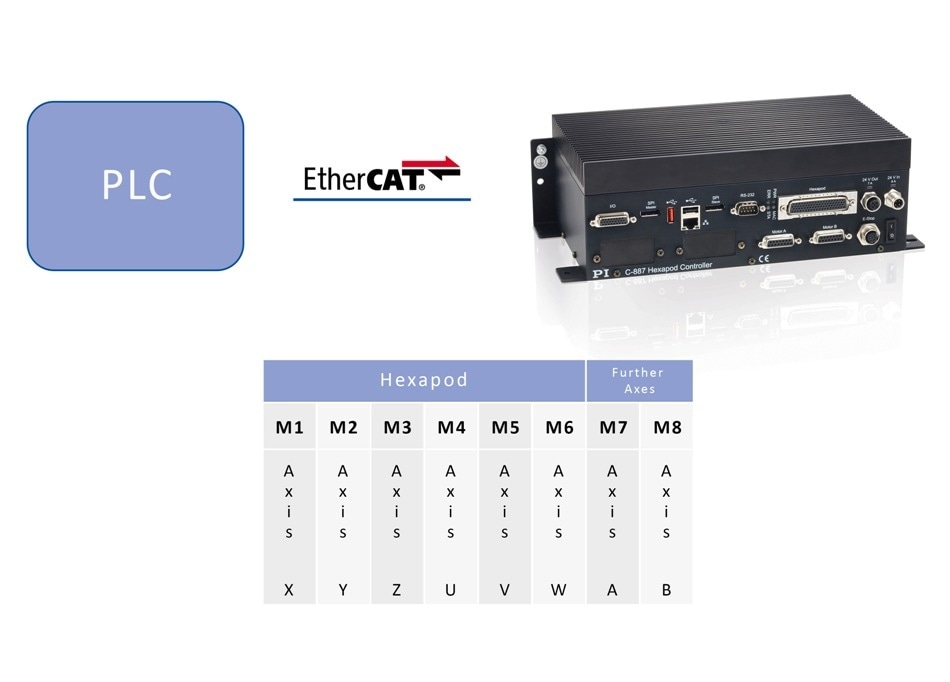
The controller communicates with the Hexapod via a standard protocol, such as EtherCAT. (Image: PI)
All PLC standard language operations are available for managing the Hexapod systems; the controller communicates with the Hexapod through a standard protocol. Well-known fieldbus protocols, such as ProfiNET or EtherCAT, are available for this purpose; extra RS232 and TCP/IP interfaces are combined as well. With the assistance of these interfaces, time-synchronized data, such as status information or target and actual positions, can be exchanged in real time with the Hexapod system as well as any other components in the network.
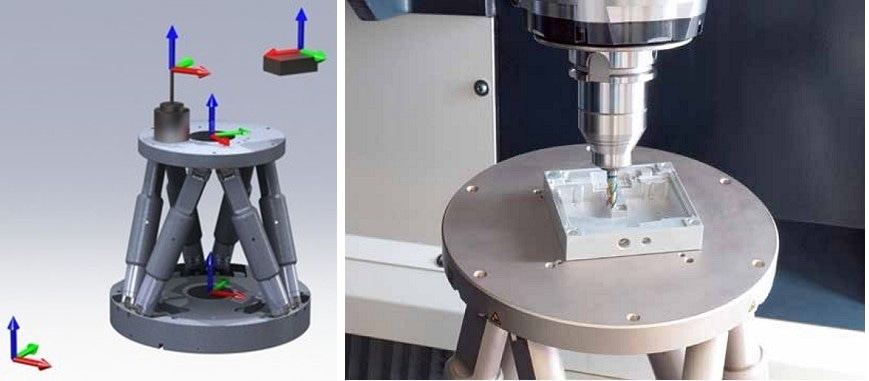
PI Hexapods can work with multiple coordinate systems and allow the user to change the center of rotation or cast / rotate a coordinate system with a simple software command – an important feature when using the Hexapod in precision machining applications. (Image: PI)
In a normal automation application, the corresponding Cartesian target positions, or trajectories, are produced by a master controller (e.g., a standard software PLC with TwinCAT) and conveyed to the Hexapod system, through the EtherCAT protocol or similar, and in return, the actual positions and status information can be surveyed. System parameters, such as the coordinate systems and the center of rotation, can also be easily configured. The Hexapod system acts as an intelligent multi-axis drive on the bus.
Examples of Use in Manufacturing and Quality Assurance
There are wide-ranging areas of application for the flexible Hexapods, as there is no difference between precision positioning of mechatronic components, semiconductor components or heavy loads.
For instance, automated 6D alignment systems deal with crucial tasks during testing and manufacturing of accessories for Microelectromechanical Systems (MEMS) camera sensors and photonics components, including the alignment of fiber arrays and optical fibers, the production of optical lenses.
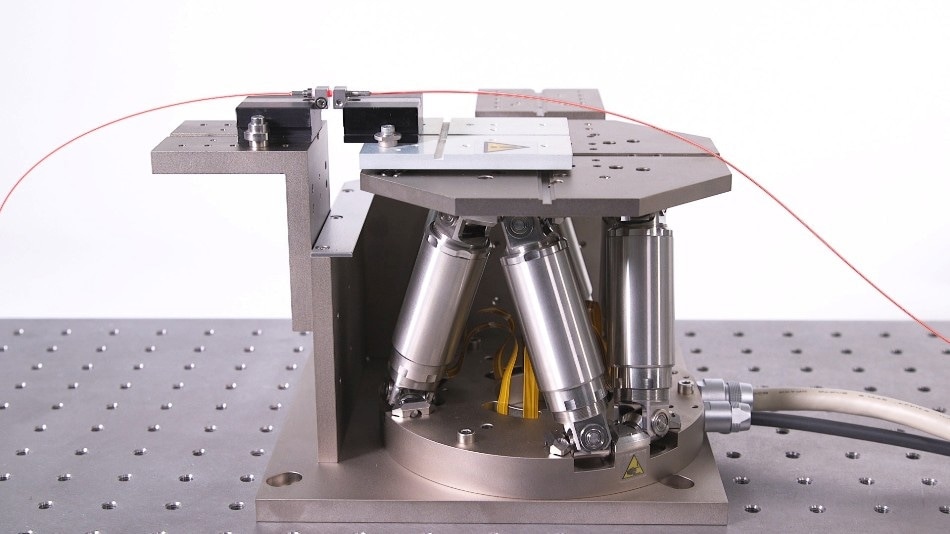
Active Fiber Optic Alignment Stages, Micro Manufacturing: Mini Hexapod 6DOF Robotic Motion Platform
Fiber alignment in micro-assembly (Image: PI)
Additional applications can be established in the “classical” industrial environment, such as material processing, when multiple axes are mandatory, or inspection systems in the automobile sector. Precision alignment on a number of axes can also be significant for heavy objects, such as reflectors and mirrors in large telescopes, inspection systems for large-format flat panels, or precisely positioning and aligning patients to a radiation source for tumor diagnosis and therapy.
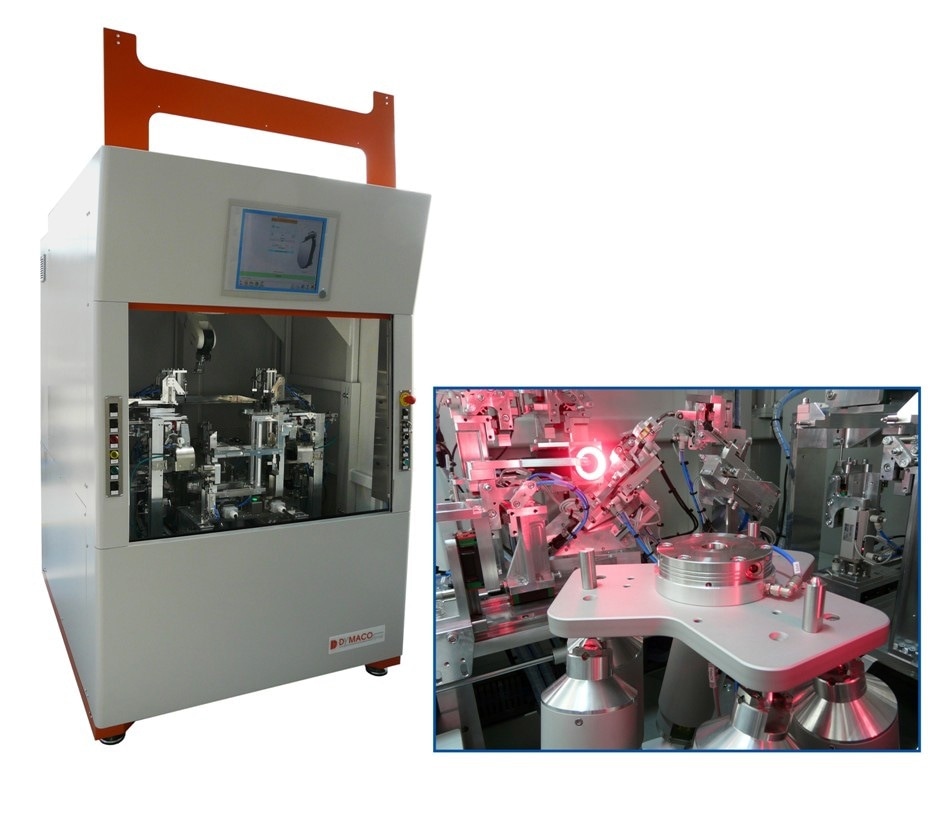
Precision alignment of headlamps in a coordinate measuring machine (Image: Dymaco)
Hexapods can handle loads up to two tons at any orientation, and if necessary, be mounted upside down. As the highest permissible load of a Hexapod system is based on a variety of parameters, such as the center of gravity of the load, the mounting position, and the current position, suitable simulation programs are supplied that enable convenient arrangement. Hexapods also enable easy determination of workspace and motion limits according to the selected center of rotation or the current position.
Fast Motion and Scanning
Motion simulators rely a lot on motion dynamics. They repeatedly perform defined motion cycles, for instance, for quality assurance and operation monitoring of products in mobile application. Typical examples for this include inspection systems for acceleration or gyroscopic sensors, like those used in cell phones, smartphones and cameras for detecting deviations in position. They are verified by means of a specified motion pattern.
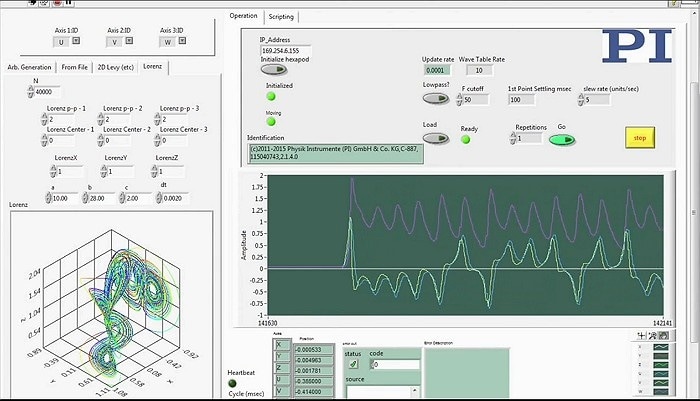
Complex patterned motion generation is becoming increasingly important for applications such as vehicular simulation and airborne platform simulation and test and Hexapods with advanced controllers and software can perform complex profiles in 6 degrees of freedom. (Image: PI)
Likewise, this applies during testing of image stabilization systems in cameras when the mechanics and algorithms are analyzed for effectiveness. For this, precise, natural, repeatable and artificial motion must be replicated with the same dynamics and accuracy on all rotary and linear axes. Hexapods are appointed for these operations and PI offers Hexapod systems that are certified according to Camera and Imaging Product Association (CIPA), which are used for examining image stabilization systems.
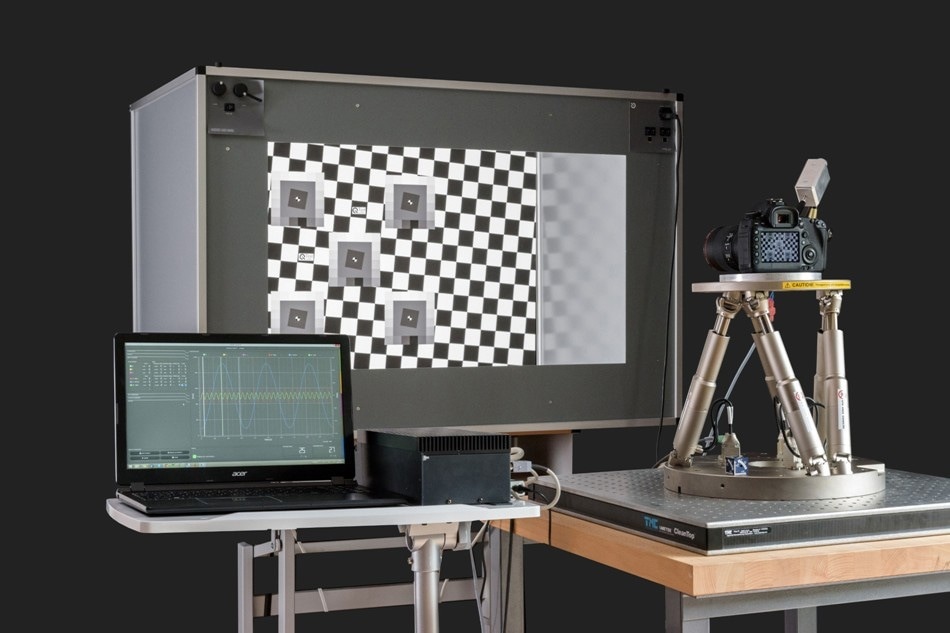
H-840 Hexapod in a camera image stabilization testbed with STEVE 6D (Stabilization Evaluation Equipment) system. (Image: Image Engineering)
Software for Hexapods
The digital motion controllers from PI are delivered with a full software package that spans all application aspects, beginning with easy start-up to the convenient control of the systems using graphical interfaces to fast and controllable integration into external programs.
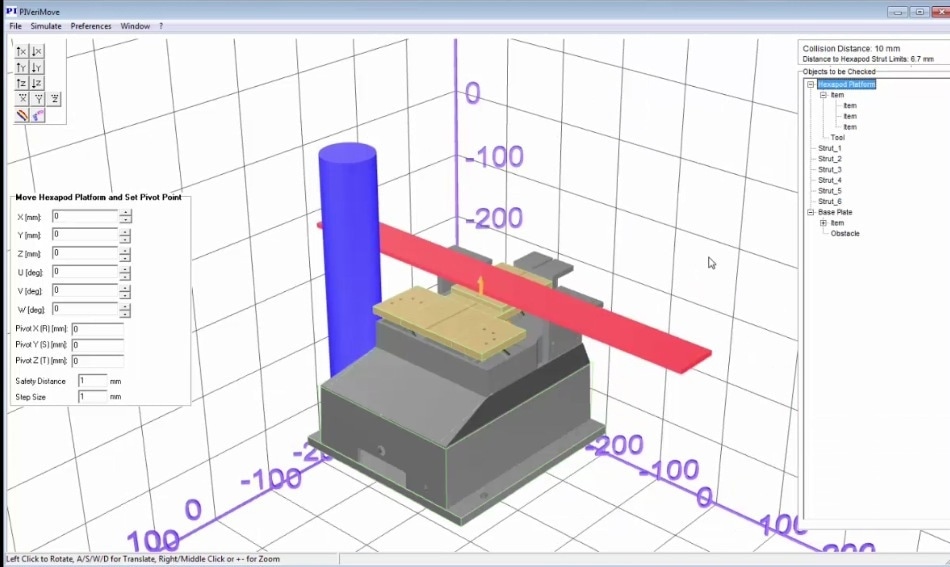
PIVerimove software tool allows simulation of interference between fixtures mounted on any PI hexapod and external obstacles. Example shows H-206 photonics alignment hexapod. (Image: PI)
A virtual controller permits creation of application programs without any of the components at hand. Simulation tools help to measure the workspace and ensure that collisions with external objects are avoided. A mobile app allows wireless monitoring and control. Development libraries and example applications make implementation simple and easy, and the following standard programming languages and software environments are also supported (C, C++, Visual C++, Visual Basic, Python, and Delphi, or LabVIEW, TANGO, µManager, EPICS, MATLAB, MetaMorph as well as all programming environments that aid loading of DLLs).
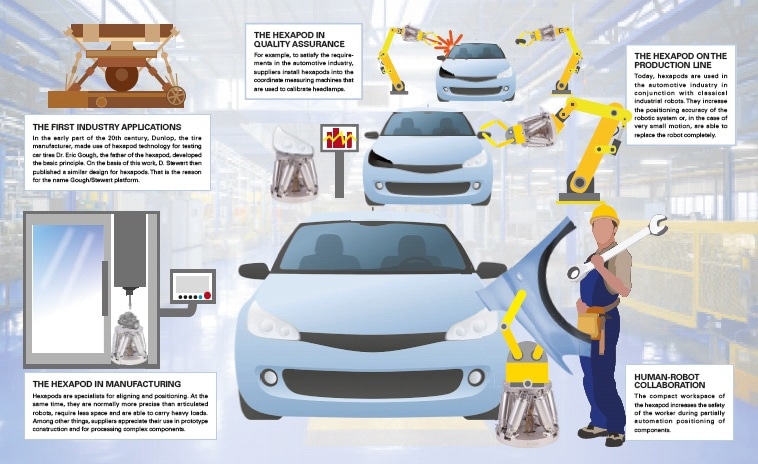
Hexapods: Solutions for Automotive Industry
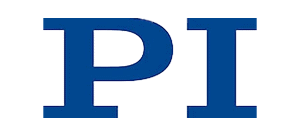
This information has been sourced, reviewed and adapted from materials provided by Physik Instrumente (PI) GmbH & Co KG - Worldwide.
For more information on this source, please visit Physik Instrumente (PI) GmbH & Co KG - Worldwide.