Progress in materials testing methods has enabled Researchers and Engineers to measure mechanical properties, and study and characterize mechanical phenomena that control deformation and failure down to almost the atomic level. One field that is gaining from such advances in testing methods is energy storage. The option of developing higher energy capacity batteries has direct implications on performance with smartphones, laptops and electric vehicles.
A number of the rechargeable batteries used in these vehicles and portable devices are lithium-ion (Li-ion), made up of two electrodes, a negative electrode made of graphite, a positive electrode made of lithium and a chemical electrolyte. The incredible capacity of lithium and the metals ability to transport lithium ions and electrons in and out of an electrode as it cycles through charge and discharge, make it a perfect anode material.
The electrolyte chemically contains the electric charge and also serves as the medium through which the current travels between electrodes when the battery is linked in a circuit. As the electrolyte in a Li-ion battery also contains a solution of lithium, the lithium electrode is inclined to react with this medium, causing dendrite fibers to develop over the course of battery charge and discharge cycles, mainly when the battery is cycled at a rapid rate.
These fibers leave the electrode and move into the electrolyte, where they break down the controlled path that the electrons usually take by creating conductive paths randomly throughout the structure. This can result in a fast discharge that allows surplus current to flow, resulting in premature battery failure. It can also dangerously heat up the battery to a point where it can cause fire.
To realize important improvements in energy density, cost requirements, vehicle range and safety, the use of metallic lithium anodes will probably be required for robust next-generation rechargeable battery chemistries like lithium-sulfur and lithium-air. However, the use of metallic lithium with liquid and polymer electrolytes is restricted because of dendrite formation, and efforts to solve this issue have met with minimal success.
Researching Pure Lithium and Superionic Solid-State Electrolytes
An alternative method is being pursued at Michigan Technical University’s Department of Materials Science and Engineering, Small-Scale Mechanical Testing Laboratory, in partnership with Oak Ridge National Laboratory and the University of Michigan. The research concentrates on a pure lithium anode accessed through, and protected by a superionic solid-state electrolyte that would prevent side reactions and promote safe, long-term and high-rate cycling performance.
Our lab is focused on the mechanical characterization of small volumes of materials. We are trying to understand how materials like metals, ceramics, polymers, composites, and biomaterials respond when their boundaries are mechanically loaded. We perform experiments relating to characteristics such as elasticity and hardness, to probe the properties of these materials.
Dr. Erik G. Herbert PhD, Assistant Professor, Department of Materials Science and Engineering, Michigan Technical University
“The key risk and current limitation of Li-ion technology is the gradual loss of lithium over the cycle life of the battery,” said Dr. Herbert. “In particular, losses caused by physical isolation from roughening, dendrites or delamination processes, or to chemical isolation from side reactions. To abate these problems we endeavor towards a much deeper analysis of the degradation processes and a predictive understanding of the lithium-metal solid electrolyte interface as a function of cycling.”
“Specifically, we need to understand how the lithium is gradually consumed, why the interfaces are surprisingly resistive, how the electrolyte eventually fails, how defects in the lithium migrate, agglomerate or anneal with further cycling or time,” continued Dr. Herbert. “And additionally, whether softer electrolytes can be used without incursion of lithium dendrites, and what effects processing and fabrication have on the interface performance.”
Among the efforts being attempted to answer these queries, advanced small-scale mechanical characterization methods are being conducted at Michigan Technical University to provide the crucial information that will directly enable transformative understanding of the complex coupling between the microstructure, its defects, and the mechanical behavior of both the solid-state electrolytes and lithium.
Nanoindentation Studies
Besides a broad collection of optical and electron microscopes, X-ray diffraction instruments and atomic force microscopes accessible through the University’s Applied Chemical and Morphological Analysis Laboratory, the Small-Scale Mechanical Testing Laboratory operates a versatile group of six small-scale mechanical testing systems in which the user has direct control over the way the test is performed and how the raw data is recorded, reduced and tested.
Nanoindentation is one of the main methods utilized to conduct the Li-ion tests. Studies of lithium films, numerous solid electrolytes and fully operational solid-state batteries are being performed in an inert atmosphere as a function of several variables, such as strain rate, strain, temperature, composition, chemistry, microstructural length scale, defect structure and in-operando cycling of the battery.
In a traditional indentation test, micro or macro indentation, a hard tip composed of a material such as diamond, whose mechanical properties are known, is pressed into a sample whose properties are unknown. The load placed on the indenter tip is increased as the tip penetrates more into the specimen and soon touches a defined value.
At this point, the load may be maintained at a constant for a period of time, or removed. The area of the residual indentation in the sample is measured and the hardness is defined as the highest load divided by the residual indentation area.
With nanoindentation, small loads and tip sizes are employed, so the indentation area may just be a few square micrometers or even nanometers. This causes problems in establishing the hardness, as the contact area cannot be easily found.
Atomic force microscopy or scanning electron microscopy methods may be applied to image the nanoscale indentation, but can be difficult. Instead, an indenter with a geometry proven to have a high precision is used, such as a Berkovich tip, which is a three-sided pyramid geometry. During the indentation process, a record of the depth of penetration is prepared, and then the area of the indent under load is established using analytical models and the known geometry of the indentation tip. A record of the measured parameters can be plotted on a graph to form a load-displacement curve, which is used to extract the material’s mechanical properties.
The crucial nanoindentation system used by the lab is the iNano, manufactured by Nanomechanics, Inc. It is the newest generation of the maximum performance ambient and non-ambient nanoindentation systems that are commercially available.
Among the enabling technology of the iNano is its ability to achieve less than 1 nm of noise in the displacement signal while using a measurement time constant of 20 microseconds. There is no averaging of fast time constant data to lower the noise floor. Coupled with a data acquisition rate of 100 kHz, the critical outcome is that the iNano offers unparalleled ability to perform high-speed testing, and unmatched ability to capture sudden events such as strain bursts, fracture, film delamination, and dynamic ringing.
Dr. Erik G. Herbert PhD, Assistant Professor, Department of Materials Science and Engineering, Michigan Technical University
“The nanoindentation is mission critical,” continued Dr. Herbert. “Without nanoindentation, there is no way to investigate how the mechanical properties are changing the function of these variables in the solid electrolytes and lithium anodes. We measure such characteristics as the phase angle, which provides a direct measure of the materials damping capability, and gives us an understanding how it dissipates mechanical energy.”
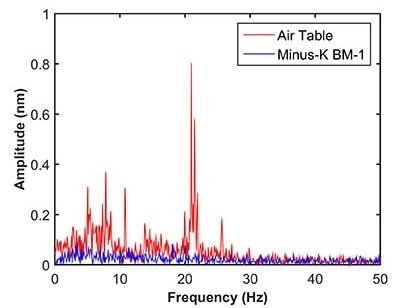
Figure 1. The labs vibration isolation comparative results of Negative Stiffness vs Air-Tables.
Vibration Isolation for Nanoidentation Measurements
The nanoindentation measurements being carried out within the Small-Scale Mechanical Testing Laboratory can range from just a few nanometers in depth, but are usually in the vicinity of 50 to 300 nm (0.05 to 0.15 µm) in depth. Measurements at this nano-level of precision require isolation from ambient environmental vibrations, especially very low-hertz vibrations, which air tables are incapable of satisfactorily preventing. Isolating a laboratory’s sensitive nano-instrumentation against low-frequency vibrations has become progressively more important to maintaining data integrity and imaging quality.
Low-hertz vibrations can be caused by a multitude of factors. Every structure is transmitting noise. Within the building itself, the heating and ventilation system, pumps, fans and elevators are just a few of the mechanical devices that cause vibration. Movement of people inside the building is another cause for vibrations.
Based on how far away the lab equipment is located from these vibration sources, and where in the structure the equipment is placed, whether in the basement or on the third floor, for instance, will determine how intensely the instrumentation will be impacted. External to the building, the labs research can be impacted by vibrations from vehicle movement, noise from aircraft, neighboring construction and even wind and other weather conditions can result in movement of the structure.
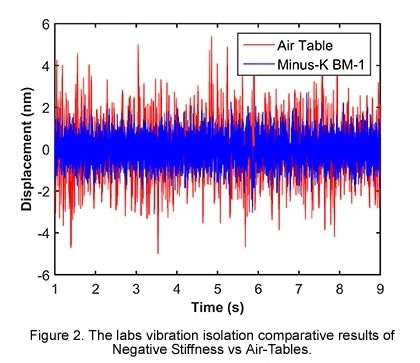
Figure 2. The labs vibration isolation comparative results of Negative Stiffness vs Air-Tables.
Any high-resolution instrument such as an electron microscope, transmission electron microscope, atomic force microscope or nanoindentation system, should best be situated in a basement on a bedrock or thick concrete slab to reduce the effect of low-hertz vibrations. With extremely sensitive instrumentation, these vibrations will impact and corrupt data sets and imaging. However, placing its precision nanoindentation instruments in the basement was not an option for the Small-Scale Mechanical Testing Laboratory.
“We set up the lab on the sixth floor of our building, because this location had the best temperature stability, which is required for our research,” said Dr. Herbert. “But we had to contend with low-hertz vibrations from the air handling system which sits above the seventh floor on the roof. The vibrations can actually be felt coming through the building structure. We positioned the iNano indentation system on one of the labs existing air tables, and measured the displacement as a function of time. The noise was just entirely too large to extract meaningful results. If we were going to make use of this location that had the best temperature stability, we needed to find a better vibration isolation solution.”
Since the lab had earlier used Negative-Stiffness vibration isolation for laboratory microscopy applications, it reached out to Minus K Technology, the developer of Negative-Stiffness isolators, to suggest a solution for the nanoindentation system.
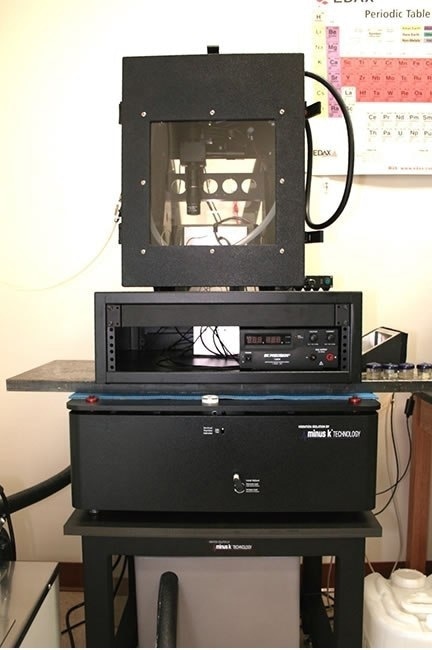
Figure 3. Indentation system on a Negative Stiffness vibration isolator.
“We positioned the iNano on a model BM-1 Negative-Stiffness isolator, just as we had done on the air table, and ran the exact same test regimen for several days,” said Dr. Herbert. “The Negative-Stiffness isolator outperformed the air table by a long shot. Looking at the data sets, it is very clear that there is a huge gain from the Negative-Stiffness isolator over the air table.”
What is very beneficial about Negative-Stiffness isolators is that they accomplish a high level of isolation in various directions. Negative-Stiffness isolators possess the flexibility of custom tailoring resonant frequencies to 0.5 Hz* horizontally and vertically (with certain versions at 1.5 Hz horizontally).
Vertical-motion isolation is provided by a stiff spring that supports a weight load, combined with a Negative-Stiffness mechanism. The net vertical stiffness is made very low without affecting the static load-supporting capability of the spring. Beam-columns connected in series with the vertical-motion isolator provide horizontal-motion isolation. A beam-column behaves as a spring combined with a negative-stiffness mechanism.
Dr. David Platus, Inventor of Negative-Stiffness isolators and President and Founder of Minus K Technology
Vibration transmissibility is a measure of the vibrations that are conveyed via the isolator relative to the input vibrations. Negative-Stiffness isolators, when attuned to 0.5 Hz, attain approximately 93% isolation efficiency at 2 Hz; 99% at 5 Hz; and 99.7% at 10 Hz. Negative-Stiffness isolators deliver excellent performance, as measured by a transmissibility curve.
Negative-Stiffness isolators resonate at 0.5 Hz. At this frequency, nearly no energy is present. It would be very rare to find a major vibration at 0.5 Hz. Vibrations with frequencies over 0.7 Hz (where negative-stiffness isolators start isolating) are quickly attenuated with increases in frequency.
Expectations
The expected outcome of our research is a clear interpretation and understanding of how the mechanical properties of a lithium anode and solid electrolyte control ion transport and limit the overall cycling performance of solid-state battery technology. This would reveal the design rules essential for successful fabrication of the solid electrolyte and packaging, in order to maintain full access and efficient cycling of the lithium over many cycles. It would enable the development of advanced Li-ion batteries, capable of considerable expanded performance, and significantly safer than any other Li-ion battery options currently available.
Dr. Erik G. Herbert PhD, Assistant Professor, Department of Materials Science and Engineering, Michigan Technical University
Dr. Herbert added, “Without question, both Nanoindentation and Negative-Stiffness vibration isolation have proved absolutely critical to advancing this important Li-ion research.”
(*Note that for an isolation system with a 0.5 Hz natural frequency, isolation begins at 0.7 Hz and improves with increase in the vibration frequency. The natural frequency is more commonly used to describe the system performance.)
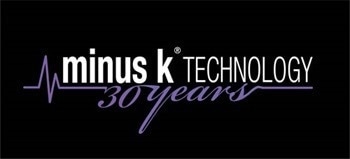
This information has been sourced, reviewed and adapted from materials provided by Minus K Technology.
For more information on this source, please visit Minus K Technology.