A stretchy, transparent material that powers itself could help wearable devices respond in real time to thermal stimuli.
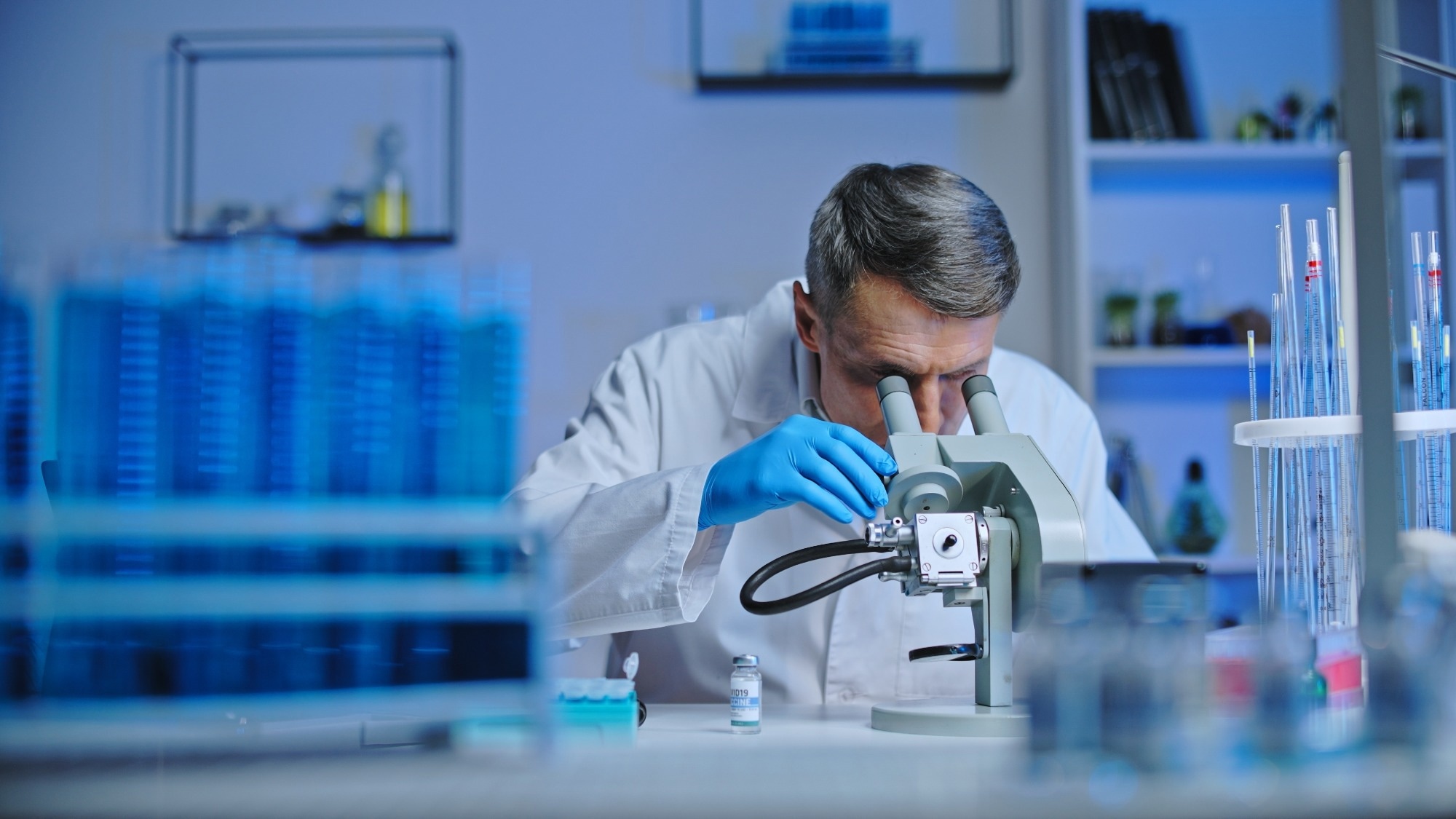
Image Credit: SynthEx/Shutterstock.com
By combining a flexible polymer with ionic liquids, researchers have created a triboelectric sensor that turns heat into electrical signals without a battery.
The new sensor, described in Advanced Functional Materials, is based on ionic elastomers. Ionic elastomers are materials that respond sensitively to changes in temperature and are made by blending polymers with ionic liquids (ILs). In this study, researchers investigated thermoplastic polyurethane (TPU), a visco-poroelastic polymer known for its stretchability and thermal responsiveness.
TPU naturally forms microphase-separated regions, with areas of harder crystallinity and softer, more amorphous characteristics. These regions respond differently to heat, giving the material useful shape memory and mechanical properties.
Combining TPU with ILs improves the elastomer's ion mobility and alters its interfacial properties, making the material especially promising for temperature-sensitive applications.
The Sensing Device
Researchers created the sensing device by embedding ionic liquid 1-ethyl-3-methylimidazolium bis(trifluoromethyl sulfonyl)imide ([EMIM]TFSI) into the TPU matrix. This resulted in a flexible, optically transparent material with distinct microstructural behaviour under varying temperatures.
This elastomer was then integrated into a triboelectric nanogenerator (TENG), which serves as the positively charged layer, with perfluoroalkoxy alkanes (PFA) as the negative counterpart.
The study found that the layers generated triboelectric charges as they came into contact and then separated. These charges were affected by the temperature-driven changes in the elastomer's microstructure, particularly its ion mobility and deformation of its crystalline regions.
The device's voltage output was captured in real time using an oscilloscope connected to a MATLAB-based data acquisition system.
To test the sensor's performance, researchers applied heat using an electric hotplate and conducted thermal cycling between room temperature and 70 °C. Thermocouples attached to the elastomer ensured accurate temperature readings, while the output voltage was calibrated against standard temperature measurements.
Real-Time Results
One of the study's key findings was that the sensor's output voltage increased with temperature. As the material neared the glass transition point of its hard segments (around 60 °C), the crystalline regions softened and deformed, significantly enhancing ion movement. This, in turn, boosted the formation of interfacial charge and electrochemical double layers, resulting in a stronger voltage signal.
The ionic liquid [EMIM]TFSI played a central role in this process. It facilitated faster ion transport and helped conduct heat, improving the elastomer's sensitivity to temperature changes. The researchers found that the sensor's electrical response was rapid, reversible, and consistent across repeated thermal cycles. The sensor's performance was optimized at a 10 % IL concentration by weight.
Download your PDF copy now!
What Comes Next?
The researchers suggest that self-powered, highly sensitive sensors like theirs could be valuable in wearable electronics, where real-time thermal monitoring is increasingly important. As devices get smaller and more complex, managing heat effectively, without adding bulk or external power sources, is a growing challenge.
Looking ahead, the team will investigate tailoring IL concentrations for specific uses, test the material under more extreme conditions, and explore integration with AI systems for interpreting irregular or complex signals.
Journal Reference
Hwang H. J. et al., (2025). Self-powered real-time temperature sensing based on flexible ionic elastomer on triboelectric nanogenerators. Advanced Functional Materials. DOI: 10.1002/adfm.202504081, https://advanced.onlinelibrary.wiley.com/doi/10.1002/adfm.202504081