During the production of a metal, the manufacturing process is marked by careful regulation of the mechanical properties of the wrought metal. However, these may undergo change later on when the wrought metal is shaped into the end product. For instance, welding or joining are processes which can change the mechanical behavior of a metal on a localized basis, as can deep drawing.
In the current article, metal sheet folding to seam a can is described, with a focus on the local work hardening of the metal bends within the areas of folding. One ideal technique to map mechanical properties and their alterations, and to understand work hardening effects to within micrometers of the affected area, is nanoindentation.
When a spherical indenter is used in combination with CMX load function, it enables stress-strain behavior to be investigated in any region of interest. Localized stress-strain curves can then be compared with those generated by bulk tensile testing.
Hardness Mapping
In the current setup the can was mounted and a cross-section taken using traditional metallography methods. testing was done on one location which showed a high degree of bending on the cross-section of the sample. The inside aspect is deformed when compression is applied to the metal fold, but the outside is deformed by tension, with the central part being neutral.
Load-controlled indentation tests were used to generate a hardness map using a Berkovich indenter, with a maximum load of 5 mN. This produced a penetration depth of about 200 nm. The inter-indentation distance was 6 μm, which effectively prevented overlap between the plastic zones of the indentation.
As Figure 1 shows, the hardness map indicates significantly higher hardness on both the outside and the inside of the folded metal but not in the center. This correlates with the predicted work hardening caused by the metal forming process.
.jpg)
Figure 1. Micrograph of the cross-section of the folded metal in the seamed part of a can. The hardness mapping reveals a low hardness in the intermediate region while the metal sheet is work hardened on the inside and the outside of the fold.
Stress-Strain Relationship
It is possible to test local stress-strain relationships by the indentation testing of a material. The use of a spherical indenter makes it convenient to probe the material under stress at a variety of strains during the same indentation experiment. If the area function of the spherical indenter of 2 μm radius is calibrated on fused quartz, constant monitoring of the stiffness is yielded by the CMX load function, and this in turn yields the contact area.
For a spherical indenter, the angle, ß, between the indenter surface and the sample surface defines the representative strain, ε. The constant monitoring of hardness by CMX from 2 nm of penetration depth onwards yields the stress. The hardness may be interpreted also as the mean pressure under the indenter, and can also be correlated to uniaxial stress σ of equivalent value by the Tabor relationship:
H[kg/mm2]≃C∙σε[MPa]
Where C is the plastic constraint factor that links the tensile stress to the hardness measurement; C=3.
Figure 3 depicts the stress-strain curve generated by this indentation, showing the elastic loading of the metal surface. Slope analysis yielded a Young´s modulus of 220 GPa, and a yield stress of 95 MPa was also calculated, which is comparable to the available values for mild steel in published literature. When the stress-strain plots in two locations were compared, an increased yield stress is associated with local work hardening, which agrees with the hardness map.
Berkovich indenters at a representative strain of 8% were used for the hardness experiments which also show a similar pattern. Experiments have confirmed that the Tabor relationship used to denote stress and strain during the course of indentation experiments is ideal for many types of metal samples.
Hardness mapping is well correlated with stress-strain relationships based on the measurements obtained with CMX, which means that these methods act in complementary fashion to uncover the occurrence of local work hardening during the shaping of metal.
.jpg)
Figure 2. Geometry of the contact between the tip (dotted circle) and sample (horizontal line) showing the contact radius (a), tip radius (R), and contact depth (hc). The angle (ß), between the sample and the indenter defines the representative strain (ε).
.jpg)
Figure 3. Stress-strain curve derived from a spherical indentation into steel with a CMX load function.
Conclusions
The use of the Hysitron® nanoDMA® III option with CMX testing enables the continuous monitoring of stress and strain in a representative fashion over the course of an indentation experiment. By using spherical small indenters, the material volume needed for testing becomes very little, which results in obtaining high-spatial resolution as well as the capability of ultra-thin-film testing.
Bruker produces extremely symmetrical spherical tips to match its very sensitive transducers to enable experiments to be initiated within the elastic loading conditions, and thus allowing observation of the onset of yield.
References
- Tabor, T., Hardness of Metals, Clarendon Press, Oxford (1948).
- Hn, J.-H. and Kwon, D., J. Mater. Res. 16 (2001) p. 3170.
- Jeon, E.-C., Park, J.-S., and Kwon, D.,J. Eng. Mater. Technol. 125 (2003) p. 406.
- Choi, Y., Jang, J.-I. Kim, K.-H., Kwon, D., and Park, S.-K.,Eng. Mater. 270-273 (2004) p. 1694.
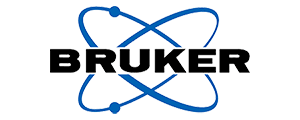
This information has been sourced, reviewed and adapted from materials provided by Bruker Nano Surfaces.
For more information on this source, please visit Bruker Nano Surfaces.