Gathering 3-dimensional image data is a staple of automated microscopy. Imaging cells in a single plane in biological science is not possible because of inherent unevenness across the sample or the thickness of the cell is more than the depth of field of the microscope objective or imaging method.
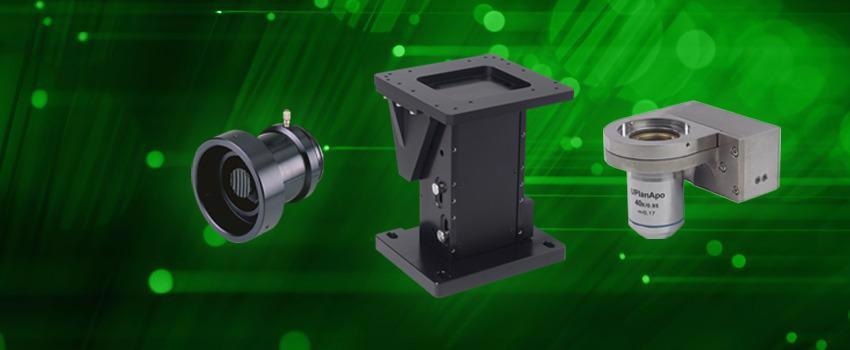
Image Credit: Prior Scientific Instruments Ltd.
As it supplies a more true-to-life representation than traditional 2D cultures, imaging cells grown on 3D substrates is becoming more popular.
To image and render multiple cell layers or tissues, organs or even whole animals need even greater penetration of the sample. Live events occurring in these samples must also be tracked in three-dimensional space.
Image acquisition in 3D space is also required by materials microscopy. Large samples, for example, 12-inch semiconductor wafers, usually cannot be positioned so flat that the areas of interest are always in focus when mapping the sample.
Extended focus, where small Z-stacks (series of images taken at the same XY coordinates) are gathered at each frame, enables an in-focus tile scan image to be stitched together when the scanning routine is complete by utilizing the best image from each stack.
To image all of the relevant materials therein, multilayer samples, for instance, LCD screens, also need Z-stacking. Automated microscopy is needed for this type of analysis, and taking 3D images by hand takes a considerable amount of time and places strain on the microscope user.
On the other hand, motorized acquisition takes a matter of seconds and is repeatable. To enable the acquisition of 3D image data as efficiently as possible, Prior Scientific provides three technologies to upgrade an existing microscope or create a standalone focusing system.
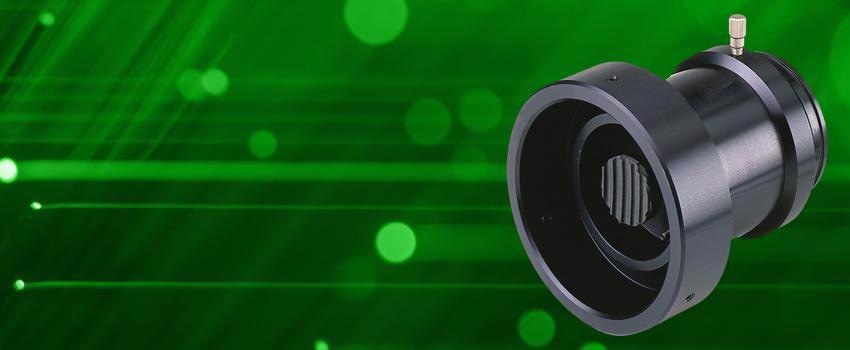
Image Credit: Prior Scientific Instruments Ltd.
Simple, Easy to Fit Motorized Focus Control – Prior PS3H122R Microscope Add-on
Entry-level 3D imaging often starts by motorizing a manual microscope frame. Prior's PS3H122R focus drive clamps directly onto the coarse focus knob and drives the fine focus mechanism.
The PS3H122R has a much better mechanical resolution than the manual focusing system of the microscope so that the same axial imaging resolution can be achieved but in a quicker and more reliable way.
A direct coupling between the microscope fine focus mechanism and the focus drive can be utilized to further enhance focusing repeatability, which is useful for autofocusing or time-lapse applications.
No microscope disassembly is needed when fitting the PS3H122R to any of the wide range of compatible microscopes from Leica, Nikon, Zeiss, Olympus and others. It takes just a matter of minutes.
A common cause of repetitive strain injuries in long-term microscope users is the manual rotation of focus drives. The addition of Prior's PS3H122R can eliminate this via the utilization of a lightweight joystick or digipot.
Prior recently equipped a UK university hospital department with a motorized focus upgrade for exactly this purpose. Through the use of programmable buttons on its joystick, longer-range fast movements were enabled without the need to use rotational hand movements when focusing altogether.
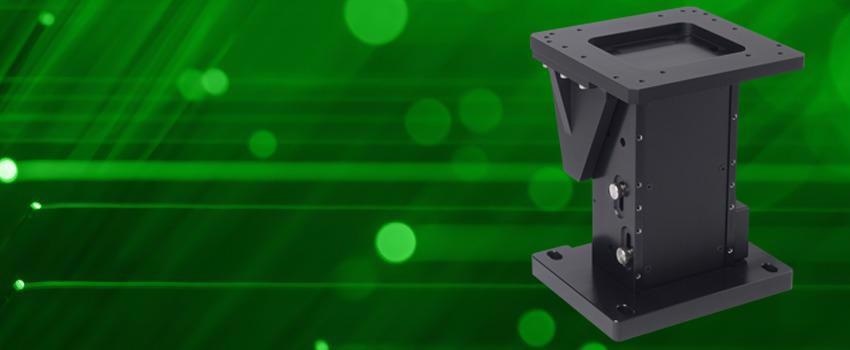
Image Credit: Prior Scientific Instruments Ltd.
Standalone Z Axis Motorized Focusing Mounts – Prior FB-Series Focus Blocks
Sometimes the utilization of a conventional microscope can put constraints on the research or analysis being performed in universities, production lines or industrial design companies. Breadboard-based optical arrangements and bespoke microscopes are commonly used to address this, which opens the door to higher performance motorized focusing.
Prior's FB-series of focus blocks feature ball screws instead of a rack-and-pinion design, allowing improved accuracy, linearity, and step resolution. This also enables them to provide up to five times the travel range and double the load capacity of traditional microscope focusing mechanisms.
Finally, in contrast to a conventional microscope, where the focus mechanism is coupled to the PS3H122R via a focus knob, the ball screws are also coupled directly to a motor to create a compact linear axis that can easily be fitted with linear encoders to enhance repeatability and resolution.
To create standalone XYZ devices for research and industry Prior has routinely used the FB-series in combination with its XY stages. The Mesolens microscope features a microscope lens that provides the unique combination of a large field of view with high resolution.
The unique nature of the optics needed a high-performance focusing and XY translation system, which could be decoupled from the overall microscope frame.
In combination with numerous Prior stages over the past ten years of research, Prior's FB204 has always been up to the task and is currently employed in multiple Mesolens research microscopes.
Openstand - Prior's imaging system development platform - also features a focus block-style Z-axis. This means that all of the advantages of the FB-series can be combined with a complete optical system and an XY stage as part of a completely motorized, customized microscope.
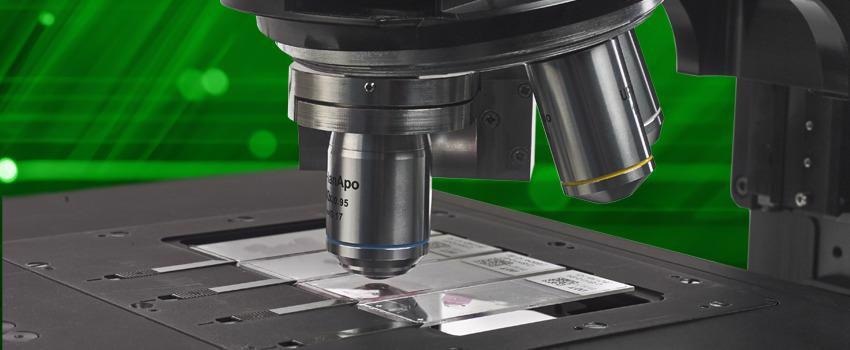
Image Credit: Prior Scientific Instruments Ltd.
Piezo-Based Nanopositioning Stages for Rapid Acquisition of High-Resolution Z-Stacks
Ultimately, however, depending on the resolution of the encoder, focus blocks are limited to microscopy with an axial resolution of approximately 100 nm and to longer-range Z-axis movements at slower speeds. The stop-start nature of acquiring Z-stacks means that focusing mechanisms with fast acceleration and deceleration are needed to capture dynamic events or optimize image collection speeds.
Prior's Queensgate brand of nanopositioning stages provides world-leading performance for microscopy requiring axial resolution at the level of confocal microscopy through to high-end super-resolution methods or applications that need fast acquisition of Z-stacks, like 3D time-lapse imaging.
These stages can be used as part of a customized imaging solution, or they can be added to existing microscopes.
Piezo motors respond to an increased voltage by expanding by an extremely precise amount at the nanometre scale, enabling a vast increase in performance compared to stepper motor devices.
Queensgate's SP-series nanopositioning stages, and OP400 objective positioner, provide sub-nanometre resolution and 7-millisecond step settle times over up to 600-micron travel ranges. Regarding the potential this supplies for 3D image acquisition, 400 images can be collected in under 30 seconds when Z-stacking.
This can be reduced to four seconds by utilizing a position-based hardware trigger, where camera acquisition occurs following a positional trigger directly from the Queensgate device to acquire each image, enabling the Queensgate device to stop at each Z-position independently from software-based camera acquisition.
The extended range of Queensgate nanopositioning devices means that the user's Z-axis hardware is able to match the user's imaging method's resolution and penetration depth (e.g., multiphoton imaging).
The stability and speed of the Queensgate SP400 enabled the UK-based imaging instrumentation company, Visitech International, to achieve a unique time saving for a system designed around their high speed structured illumination (VT-iSIM) super-resolution imaging system.
By using the SP400, movements between adjacent positions in each Z-stack can be fully completed with no oscillation in five milliseconds, which enables every axial movement in a Z-stack to be completed within the readout time of the camera. This meant no time loss between images caused by the hardware, enabling the system to run as quickly as possible.
In addition, the SP400 provided the perfect match in terms of precision and accuracy, as the VT-iSIM supplies an axial image resolution of 300 nm, two times better than regular widefield microscopy.
Choosing the Right Focusing Device for Your Application
It can be challenging to find the right component for automating a Z-axis movement. Prior Scientific has the expertise to guide the user to a product to meet their technical requirements or can recommend one which could future-proof a system or take it to the next level.
The three options presented here can add low, moderate or high precision automated focus to numerous systems, from customized systems underpinning research or new product design to microscopes from world-class manufacturers.
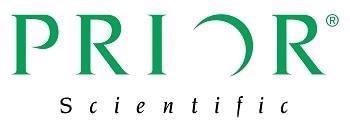
This information has been sourced, reviewed and adapted from materials provided by Prior Scientific Instruments Ltd.
For more information on this source, please visit Prior Scientific Instruments Ltd.