Environmental system designers are frequently asked where to position sample points for particle monitoring, whether it is conducted in a clean device (Isolator, RABS, etc.) or a pharmaceutical cleanroom.
There is not always a simple solution. There are multiple guidance documents that provide explanations on which processes need to be assessed, along with guidance on appropriate distances from the process being evaluated.
The aim of this article is to determine the most appropriate location for process monitoring, developing a scientific argument for the decision and to establish the considerations.
In pharmaceutical applications, particle counting can be easily divided into one of three types: monitoring, certification and qualification. A unique approach is required for each of these categories.
Certification
This is where a cleanroom is evaluated according to a standard.
ISO14644-1, “Classification of air cleanliness by particle concentration”, is the only internationally recognized standard that establishes how a cleanroom works and its capability to demonstrate uniformity throughout the whole space. This is completed regardless of the activities conducted in it.
Qualification
The system of evaluating the risk assessment for the room activities. Grid methodology testing techniques are used in qualification. Particle counts are quantified in both at-rest and operational modes, but the operational data is the most accurate.
Monitoring
The continual sampling of the cleanroom at a frequency that corresponds to the degree of control necessary to ensure risk to the end product is managed. The location and quantity of the sample points are established via the certification and qualification processes and risk assessment.
Certification
As outlined earlier, the certification of cleanrooms is founded on ISO14644-1, “Classification of air cleanliness by particle concentration” standards. The details of the evaluation can differ slightly between EU GMP and FDA regulations, but the methodology that underlies them both is consistent.
Certification shows that the whole area meets a particular ISO classification by particle concentration. Only the implementation and design of the filtration system are evaluated, where the final use of the room is disregarded.
The universal standard means that a cleanroom proven to comply with ISO 5 standards will comply with that standard irrespective of regulatory (such as EU GMP or FDA) or geographical factors.
This offers an international standard to demonstrate that a cleanroom level has been set. Products from Particle Measuring Systems are in line with the latest ISO standards established in 2015, such as the Airnet® II and IsoAir® Pro-E Aerosol Particle Sensors.
The Lasair® Pro Aerosol Particle Counter’s interactive software can even guide the user through the process of certification.
There are multiple resources to verify ISO compliance and this article will not outline these in detail.
In this article, the basic rules of testing have been shown utilizing the example of a classic filling machine (Grade A/ISO 5) within a Grade B (ISO 7) background area.
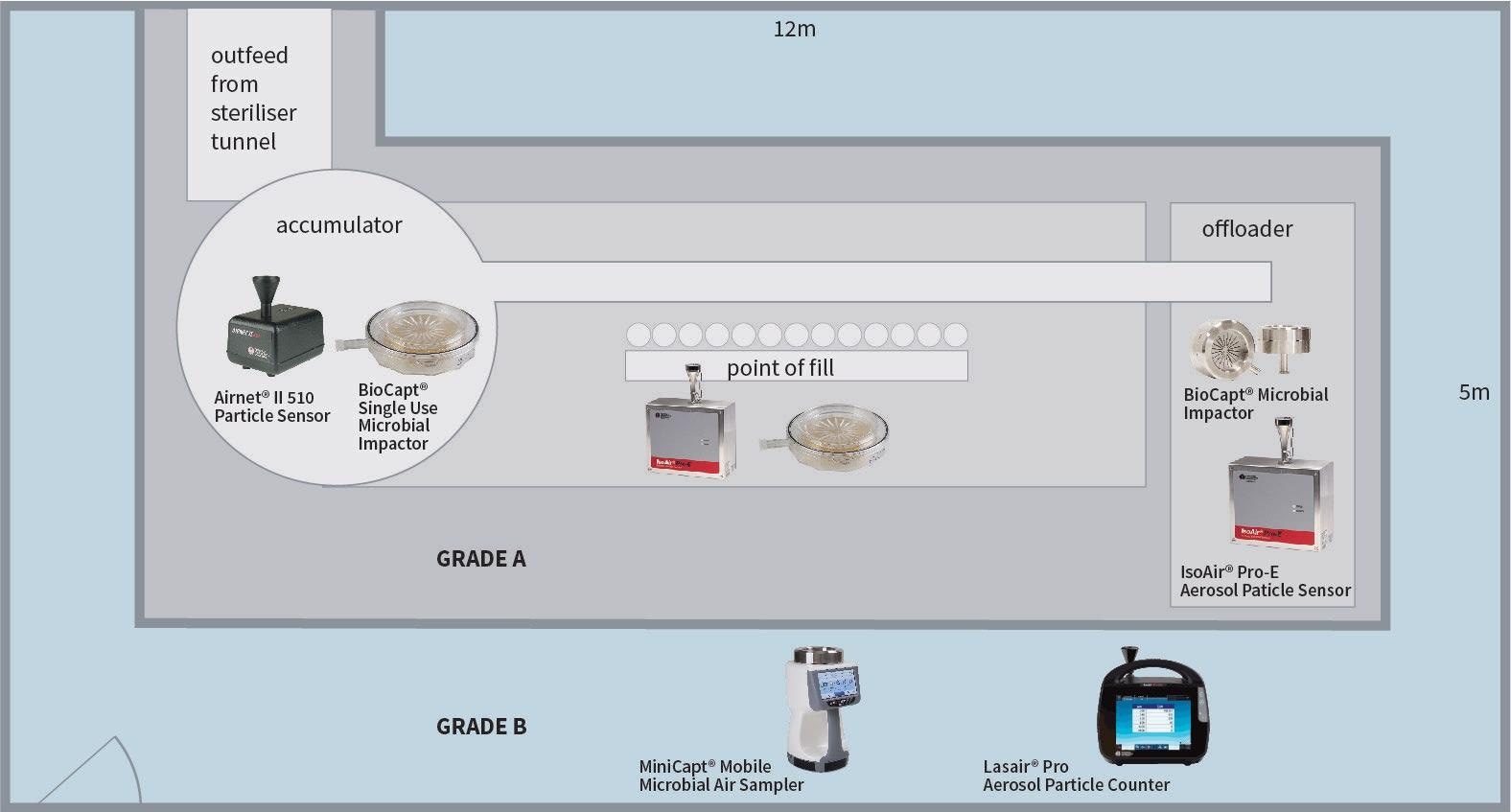
Figure 1. BIOCAPT® single-use and stainless-steel microbial impactors, and the MINICAPT® mobile microbial air sampler comply with ISO14698-1, certification standards set for biocontamination control. Image Credit: Particle Measuring Systems
1. The quantity of sample points is established on a statistical function of the region. The area of Grade A/ISO5 should be determined. The quantity of necessary sample locations in the table should then be identified.
- Determine the area of Grade A/ISO5. Identify the quantity of necessary sample locations in the table.
- Determine the area of Grade B/ISO7. Identify the quantity of necessary sample locations in the table.
2. The placement of sample points for the Grade A (ISO5) area:
- Regardless of the activity at the location of their placement, the sample points must be at work height and at an equal distance.
- Samples are obtained in a grid pattern at the locations found. The minimum amount of sampling locations, NL, can be derived from Table A.1 in ISO 14644-1. This table outlines the amount of sampling locations in relation to the area of each clean zone or cleanroom to be classified and offers at least 95% confidence that a minimum of 90% of the clean zone or cleanroom area is not greater than the class limits.
- For ISO and EU GMP Annex 1, PASS/FAIL standards are determined. It is advised to have both data sets because the EU requires Annex 1 data points and the FDA requires ISO14644-1 (although the EU data would be sufficient for the FDA).
3. Placement of ample points for the Grade B (ISO7) area:
- The steps employed for the Grade A (ISO5) area can be repeated.
- If the room is unusually shaped, it may be more challenging to establish the sample point locations. Use ISO 14644-1 Table A.1 to establish the minimum quantity of sampling locations. This table outlines the quantity of sampling locations in relation to the area of each clean zone or cleanroom to be classified and offers at least 95% confidence that a minimum of 90% of the clean zone or cleanroom area is not greater than the class limits.
4. The completion of the certification phase is marked by the creation of a final report.
Qualification
Risks to the quality of the end product are evaluated in the qualification stage. All activities should be quantified and considered. Following on with the example of the filling line, the accumulator table at the sterilizer tunnel’s exit will now be evaluated.
The risk is that glassware (bottles or vials) are vulnerable to the operator and open environment. Prior to filling, contamination may fall into clean bottles or vials.
The moving of glassware and operator intervention produces turbulent movement of air on the table, influencing the risk of contamination to the open bottles or vials. This means it is an area of contamination risk, and the following steps should be followed:
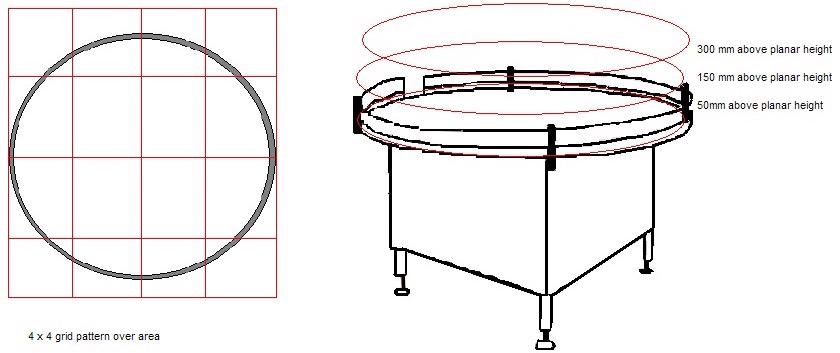
Figure 2. Image Credit: Particle Measuring Systems
1. The risk area should be divided into a 4 x 4 or a 3 x 3 grid. Each level (+300 mm from work height, +150 mm from work height, and working height) must be evaluated if the activity can arise at multiple levels.
2. A sample of the particle should be taken at the center of each of the grid squares at each level.
- Samples are acquired in both operational and at-rest states. To gain appropriate information, it may be necessary to work around an operator or an activity.
- It is acceptable to slightly move the sample points inside the grid square. If it is identified as interrupting standard activities, a location will be deemed invalid.
3. A particle map of the pharmaceutical activity is created once all the samples have been obtained.
All of the main operations inside the cleanroom (such as stoppering, general background activities, filling point) must be evaluated accordingly.
Monitoring
The monitoring points location must be established on a formal risk assessment utilizing methods such as but not restricted to Failure Mode, Effects, & Criticality Analysis (FMECA) or Failure Mode and Effects Analysis (FMEA), with information from the qualification and certification measurements.
Further elements, such as mounting points, equipment interference, operator intervention and operator impedance, all play a role in the selection of the sample probe’s final location.
A risk assessment is completely essential in the modern regulatory environment. If a risk assessment is not performed, inaccurate or poor sampling techniques can produce unreliable data related to the process.
This could also result in harm to the quality of the end product. Without the choice of events correlation, the lack of relationship between sample frequency and location can result in lengthy investigations of out-of-tolerance events.
There are multiple stages to establishing a plan for risk-based environmental monitoring:

Figure 3. Image Credit: Particle Measuring Systems
1. Process Understanding
Material flows and personnel inside the evaluated area must be investigated, along with the operations of production. This will provide knowledge of how the system is utilized and what evidence there is to back up its state of control, for example:
- Smoke studies
- Current monitoring practices
- Historical information
This Gemba walk of the rooms and process is required for the required scope of monitoring to be defined and to assist in deploying a system that adheres to the internal practices of a business. The figure presented above gives an example.
2. Determining Critical Areas
Hazard Analysis Critical Control Point (HACCP) can be used for identification which helps to identify which critical areas need environmental assessment and locates areas that have the requirements of a critical sample location.
3. Assessment of Sampling Techniques
A choice must be made between traditional techniques like volumetric air samplers, the latest technologies like Rapid Microbiological Methods, or manual collection methods, for example, contact plates and swabbing.
Establish if the technique selected must be remote, portable, continual, etc.
4. Identifying Potential Sample Locations
As presented in the adjacent figure, a single sample area inside each critical location must be determined, following the below guidelines:
- Evaluate the space that is available around the critical area.
- Quantify the size of the plate holders and probes.
- Establish the accessibility of the area for when maintenance must be performed by operators.
- Evaluate the relationship between the mechanisms of the process with material flows and personnel.
- Determine the likelihood of possible contamination events.
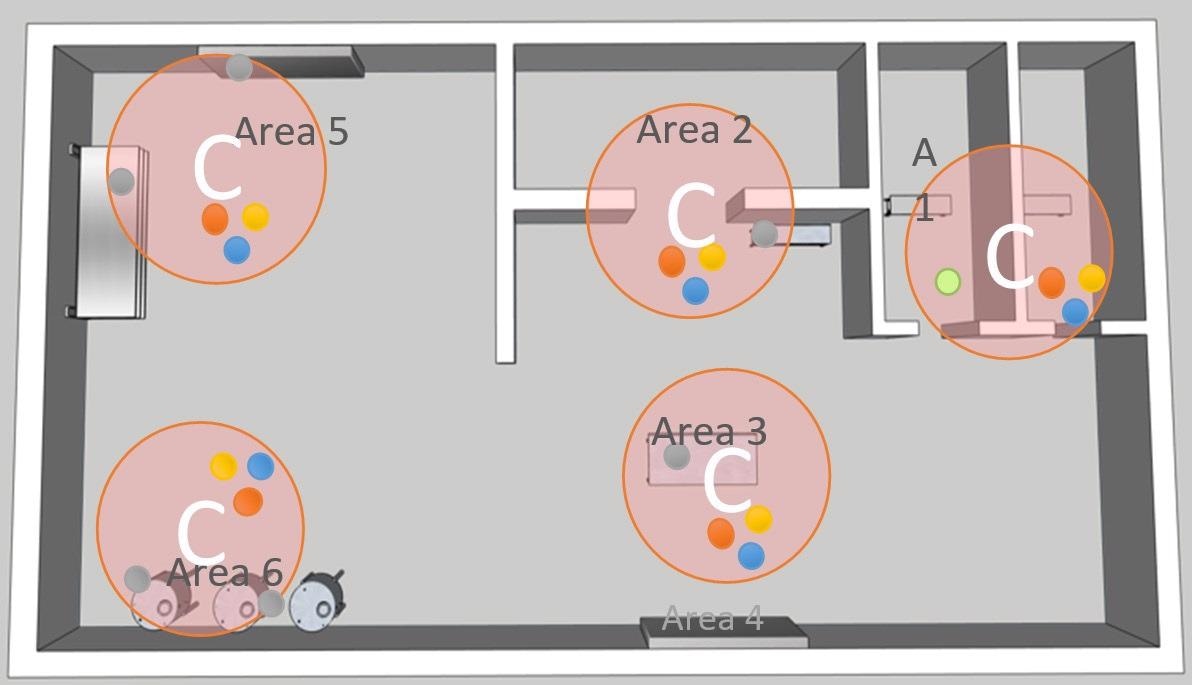
Figure 4. Image Credit: Particle Measuring Systems
5. Determination of Critical Control Points (CCP)
The FEMA method can be used to categorize and determine critical sample locations for each individually evaluated location.
6. Sampling Parameters are Defined
The sample frequency is established according to the importance of operations along with any extra principles, for example, mitigation parameters and incubation measures that may be established before a monitoring scheme is created.
Sampling practicalities cover factors such as:
- The isokinetic sample probe must face into the stream of air.
- The minimum tubing length should be utilized. While various manufacturers state that particular lengths of tubing can be employed with their particle counter, this is normally due to vacuum pump dynamics and not of the transportation of particles.
Particles of 0.5 µm can easily travel in long tubing lengths. Particles of 5.0 µm are not equally mobile. The tubing should be kept at the minimum lengths recommended because 5.0 µm particles are a bigger concern.1
Maximum tubing lengths are quoted by Particle Measuring Systems based on equivalent airflow conditions and have an advised maximum length of 3 m. For pharmaceutical particle systems, a smaller recommended length of 2 m is recommended to ensure the larger particles can move freely.
The following is taken from the Aseptic Processing cGMP Guideline by the FDA:
“Air in the immediate proximity of exposed sterilized containers/closures and filling/closing operations would be of appropriate particle quality when it has a per-cubic-meter particle count of no more than 3520 in a size range of 0.5 µm and larger when counted at representative locations normally not more than 1 foot away from the work site, within the airflow, and during filling/closing operations. This level of air cleanliness is also known as Class 100 (ISO 5).”
The sampling frequency should acknowledge the risks and follow the EU GMP Annex 1 and the FDA standards on sterile manufacturing. Particle monitoring should be maintained in a continual state and be automated when products and glassware are exposed.
Acknowledgments
Produced from materials originally authored by Mark Hallworth from Particle Measuring Systems.
References and Further Reading
For more information on tubing, read, “Particle Loss in Transport Tubing” by Particle Measuring Systems.

This information has been sourced, reviewed and adapted from materials provided by Particle Measuring Systems.
For more information on this source, please visit Particle Measuring Systems.