Sponsored by ELMARCOReviewed by Louis CastelDec 11 2023
Ever-increasing worldwide concerns surrounding levels of plastic waste alongside water and air pollution have driven the search for viable, sustainable solutions. Emerging as a potential resolution, electrospun nanofibers show great promise, especially in the field of water treatment. 1
Major progressions in the methodology of electrospinning have propelled the manufacturing of nanofiber materials into widespread utilization. This has marked a turning point in their use, from niche applications to industrial-scale production.2
The characteristics of electrospun polymers are unmatched, highlighting them as the ultimate material for filters. This usage as an efficient filtration material is derived from brilliant pore connectivity, outstanding surface-area-to-volume ratios, and a high degree of tunability regarding porosity exhibited by these polymers.3
Outstanding biodegradability and recyclability are also key features of many electrospun polymers, alongside the ability for fibers to be functionalized. Functionalization could occur with additional species, such as nanoparticles, and can impart additional material properties, such as antibacterial functionality.
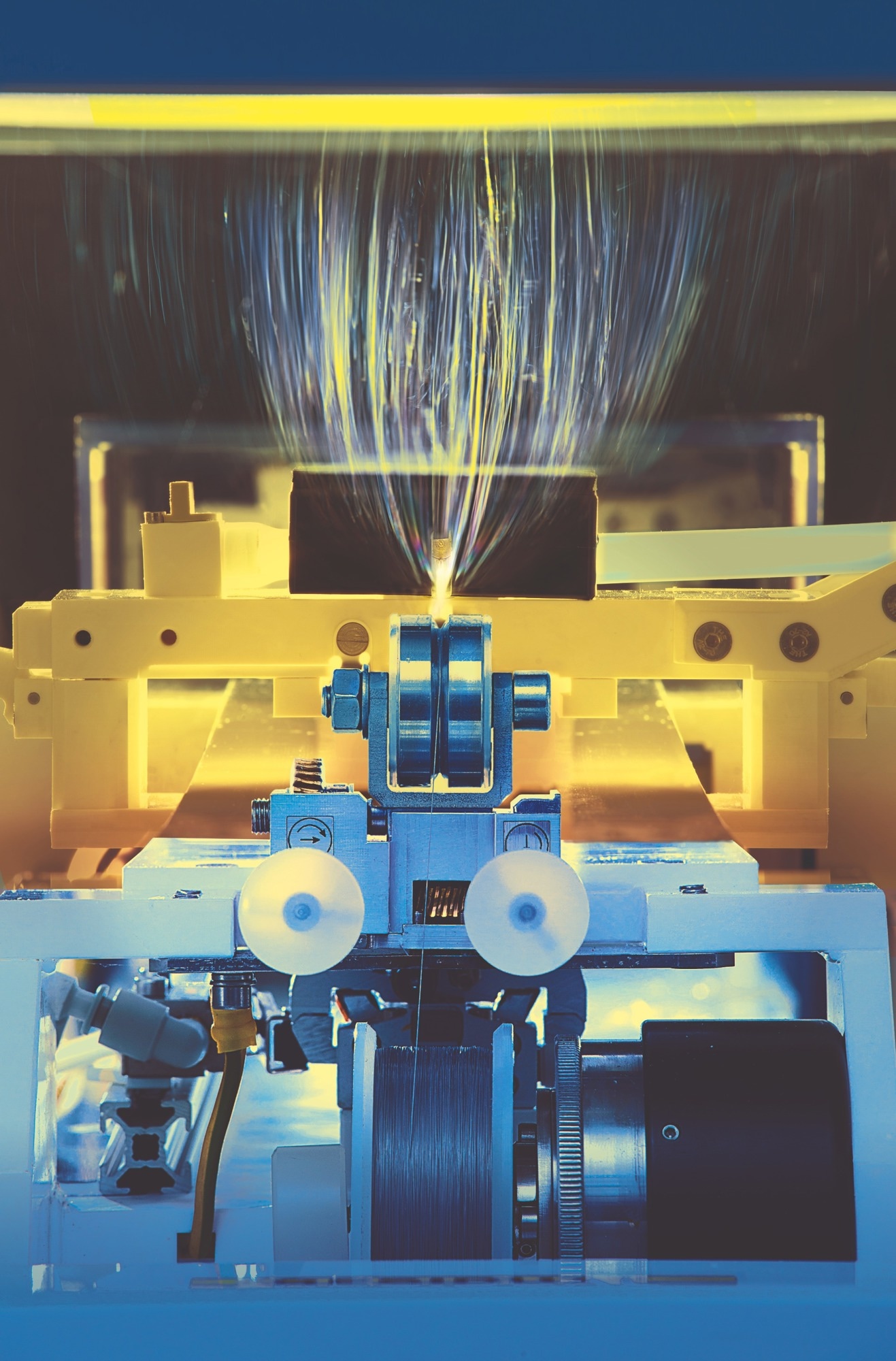
Image Credit: Elmarco
Electrospinning is inherently well-suited to nanofiber creation and has the potential to aid in both the production of large-area fiber material and tackle one of the biggest challenges facing all industrial manufacturing sectors – sustainability and waste reduction.
While polymer nanofibers have many desirable properties, many sustainability issues surrounding plastic waste also apply to nanofibers.
Traditional polymers are typically sourced from feedstocks derived from oil and fossil fuels, and their poor biodegradability, with decomposition times of 20–500 on average, are all adding to growing landfill problems.2
As a result of these concerns, there has been a shift in manufacturing towards more environmentally friendly polymer sources, alongside endorsing recycling and implementation of circular economy principles.4
Such polymers are derived from renewable feedstocks, such as plant materials, and are typically more suitable for recycling.
Solvents used during the electrospinning process in the creation of polymer materials also raise concerns due to the environmental and pollution problems associated with their use. Therefore, it is crucial to explore the future of eco-friendly solvents within the field of electrospinning.
This article will delve into the sustainability of electrospun polymers, analyzing environmentally friendly alternatives and addressing the challenges that remain to create a greener future.
Electrospinning – Solvents, Polymers and Substrates
A shift towards sustainable practices in the field of electrospinning centers around two crucial aspects: the incorporation of eco-friendly solvents and the use of biodegradable polymer bases. These green solvents have vast potential for numerous electrospinning methods, including both needle and needleless techniques.
Green solvents yield comparable results without relying on toxic substances or those derived from petroleum chemistry. 7 However, despite their proven potential, there are still certain barriers to the widespread adoption of green solvents.
The adoption of green solvents, while promising, presents challenges due to their sensitivity to environmental conditions, leading to complexities in their utilization.
A significant obstacle to their widespread adoption lies in the need for further process optimization and the scarcity of general procedures. Nevertheless, advancements in synthetic routes utilizing green solvents have yielded nanofibers with desirable traits such as air permeability, repellency, and enhanced filtration capabilities.7
Moreover, many green solvents can be seamlessly integrated with advanced electrospinning techniques, facilitating the creation of functionalized nanofibers.
The pursuit of more environmentally friendly starting materials for electrospun polymers leads to two key options. These include biopolymers (materials resulting from wholly biological resources) or bio-sourced/biobased materials (a blend that includes a specific ratio of biopolymer).
However, the effectiveness of spinning a particular polymer/solvent combination is determined by the nature of the interactions between the solvent and polymer.
In this context, solubility is critical in identifying compatible pairs, as the solvent must effectively dissolve the polymer starting materials. Various fluid properties, including viscosity, surface tension, elasticity, and conductivity, significantly influence the ultimate properties of the fibers.
For instance, when the Taylor cone is formed during the electrospinning process, it is the Rayleigh instability that determines when capillary breakup occurs.
Finding solvent combinations with appropriate surface tension is crucial to prevent unwanted breakup, ensuring they align with the viscoelastic properties of the polymer fibers, which are also influenced by the polymer concentration that is being used.
Additionally, there is an increasing trend in the market towards creating innovative substrate materials derived from bio-based or eco-friendly starting materials. These efforts aim to enhance the biodegradability and recyclability of nanofiber-coated materials, aligning with the growing demand for eco-friendly solutions.
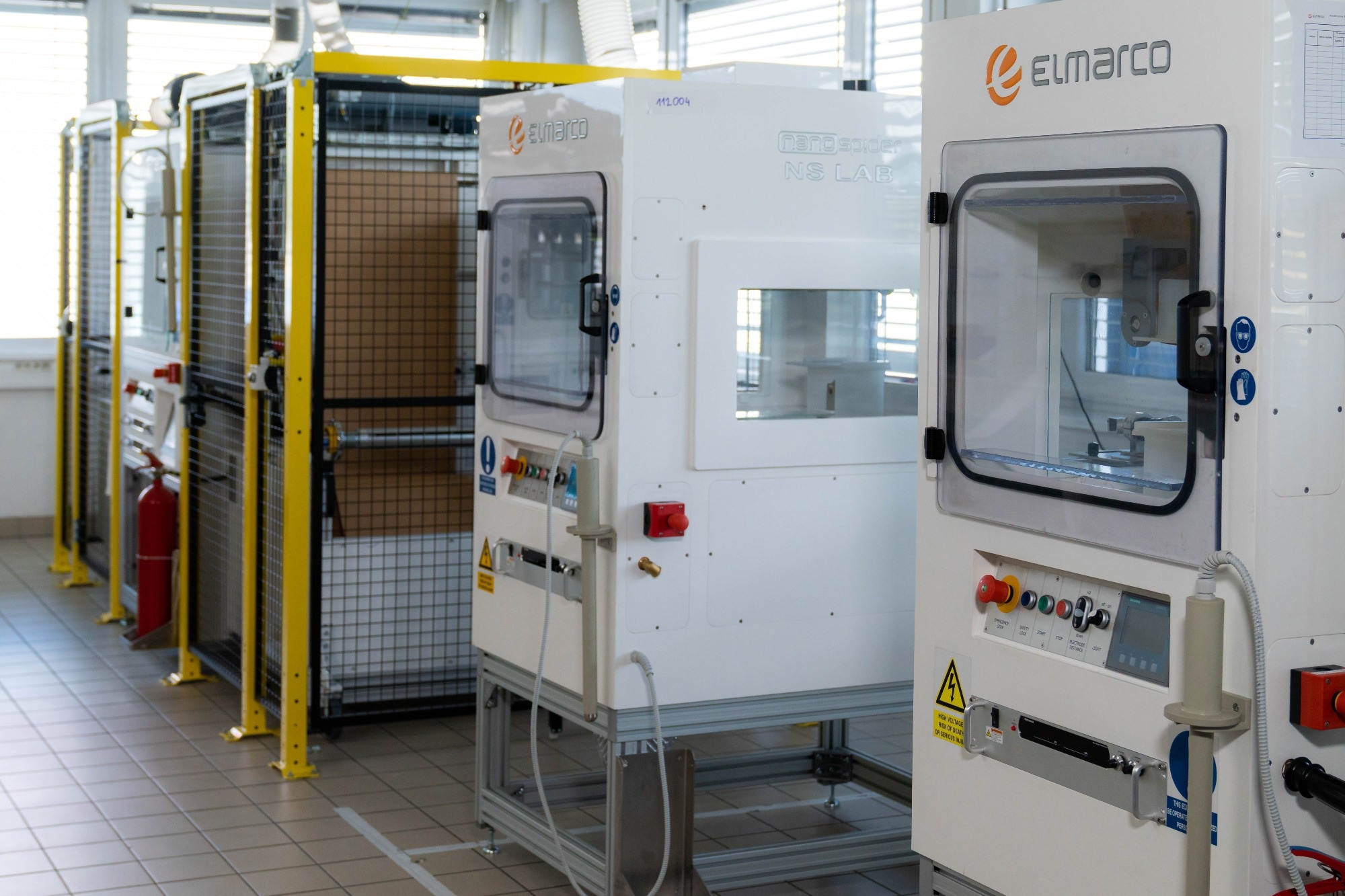
Image Credit: Elmarco
Sustainable Biobased Polymers
A variety of green polymers are presently employed in the field of nanofiber electrospinning. Each polymer has distinctive applications, with further benefits derived from the electrospinning process.
Polyester Derivative (PETG): This polymer is an eco-friendly, cost-effective replacement for PET, removing the requirement for processing with fluorinated solvents.
Due to its adaptability, PETG can be modified for a range of uses. Furthermore, it can be spun into finer structures compared to conventional PET, making it particularly suitable for 3D printing with improved thermal characteristics and for use in packaging applications.
Polylactic Acid (PLA) and Polycaprolactone (PCL): Polylactic acid and polycaprolactone are exemplary biobased polymers. Microbial polymerization can also aid in driving the process, further enhancing its sustainability. Both PLA and PCL are highly compostable, with PLA being especially biocompatible, making it suitable for a variety of biomedical applications.
TPU/Polyamides: These polymers are known for their remarkable strength and chemical resistance, rendering them ideal for bioapplications, especially in the area of wound compatibility. Electrospinning facilitates the production of extremely fine fiber dimensions, and these polymers demonstrate high solubility.
Cellulose: Cellulose is regarded as one of the most advanced biomass materials globally, known for its outstanding environmental compatibility and excellent biodegradability.
It is particularly effective as a filter material in packaging applications. Additionally, cellulose can be electrospun into ultrafine fibers as small as 300 nm, featuring low thermal expansion and maintaining a balance of being lightweight yet strong.2,3
Chitosan: Chitosan, a bio-based polymer, is known for its impressive water absorption properties and is utilized to form hydrogels. It can also be infused with bioactive compounds, making it an ideal choice for medical formulations and wound treatment applications.4
Incorporating these sustainable biobased polymers into the nanofiber electrospinning process not only broadens their application spectrum but also plays a significant role in advancing environmentally friendly solutions across diverse industries.
Low Energy Solution For Waste Air Treatment
The environmental and economic consequences associated with waste air from chemical processing are regarded as a major issue in today’s industrial landscape. This waste air often contains high levels of particulate matter, leading to serious concerns about its environmental and health impacts.
Irrespective of the type of solvent used, the methods employed for waste air treatment remain fairly consistent, encompassing catalytic systems, thermal systems, and scrubbers.
Scrubbers are the most commonly used method for treating contaminated wastewater. Yet, emerging technologies such as low-temperature plasmas present a promising alternative, offering more efficient waste air treatment while reducing energy requirements.8
The use of green solvents eliminates the need for expensive particle recycling or trapping systems, as their adoption in manufacturing processes negates the requirement for waste air treatment that is necessary when using harmful solvents.8,10
However, in scenarios where green solvents cannot be used, different solutions to recycling waste air must be found.
Every stage of the electrospinning process generates waste air, from creating solutions and polymers to preparing substrates. Thus, focusing recycling efforts on this waste air presents a valuable opportunity to bolster the industry’s sustainability efforts.
Catalytic and thermal scrubbers function by absorbing unwanted pollutants onto the material’s surface. Subsequently, the Volatile Organic Compounds (VOCs) are either trapped and later removed through a rinsing process, or they undergo a degradation reaction or thermal decomposition, transforming into other harmless chemical products.
However, one problem with this is that the reaction conditions often require extremely high temperatures, resulting in significant energy consumption during the desorption and cleaning stages.
Scrubber systems often employ a chemical trap, such as activated carbon, which adsorbs VOCs onto its surface to capture them.
Wet scrubbers utilize a spraying mechanism to treat incoming waste air with a liquid, typically water, aiding in the removal of dust and particulate matter. Occasionally, additional chemical species are introduced that either react with and decompose any present VOCs or assist in trapping various species.
On the other hand, low-temperature plasmas provide a more energy-efficient way to clean up waste.
In plasma cleanup, reactive radical species are formed, which subsequently react with unwanted pollutants, leading to their degradation. The high efficiency of low-temperature plasmas makes them an ideal, energy-efficient alternative to traditional scrubbers. This contributes to the enhanced sustainability of nanofiber production processes.
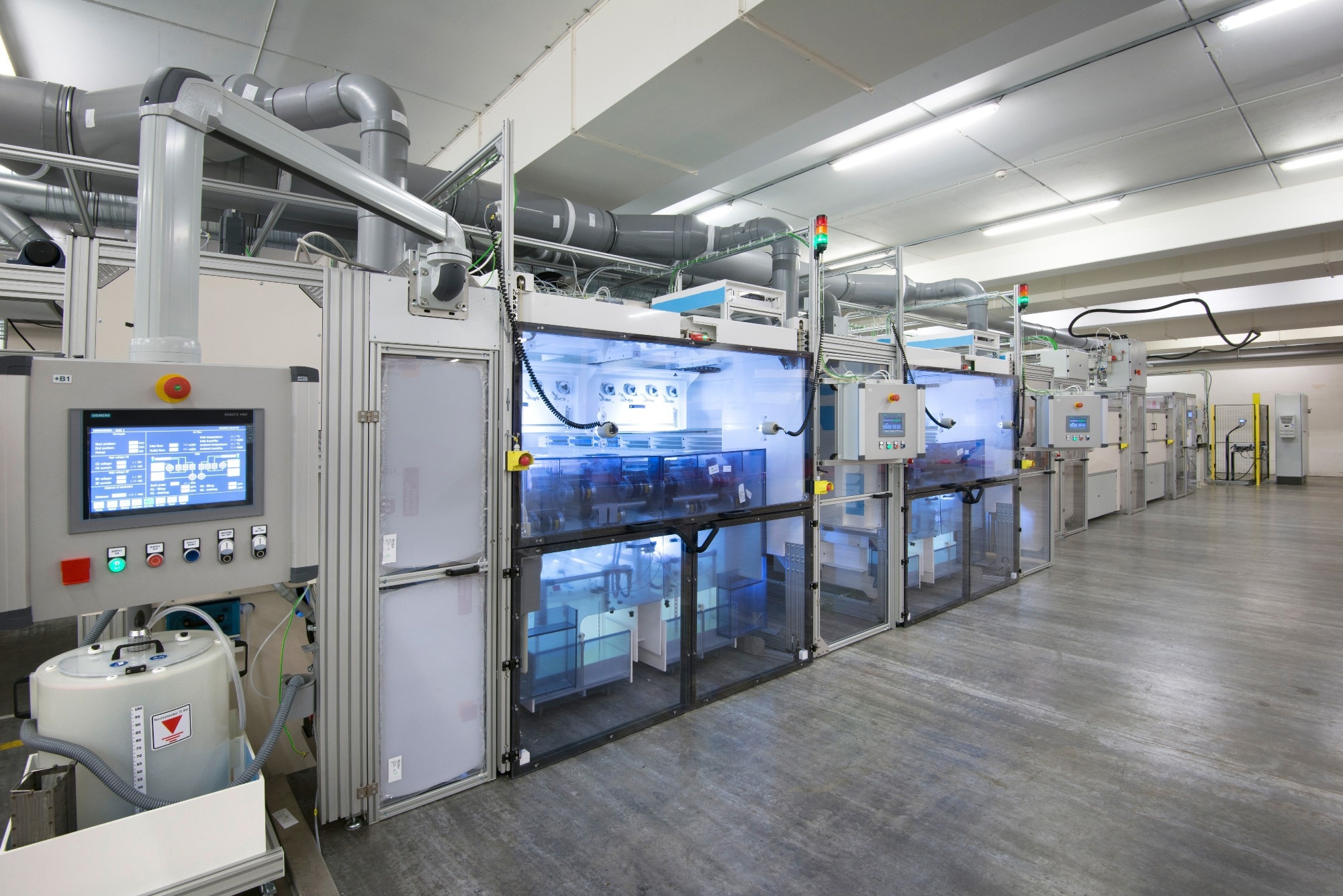
Image Credit: Elmarco
Scaling Up
Nanofiber production using green polymers and solvents has achieved remarkable scalability recently, with nanofiber production anticipated to reach or exceed 100,000 m2 per year.2
Specific products can be manufactured in even larger quantities. However, there are certain challenges associated with scaling up, generally related to the volumes of solvents required for processing, which, in turn, further emphasizes the need for process optimization.
The limitations surrounding scaleability tend to arise partly due to a lack of understanding regarding the electrospinning process at the nanoscale level for fibers. This knowledge gap thus makes it hard to predict the interactions that are likely to occur between a solute/solvent pair.
Collaborating with specialists in electrospinning, such as Elmarco, can be extremely advantageous in addressing these challenges.
Elmarco can help reduce the costly burden of research and development for creating or adapting a new electrospinning process for new solvents or starting materials.
Leveraging Elmarco’s extensive expertise in electrospinning processing can offer invaluable support and guidance, effectively streamlining the path toward developing innovative and efficient solutions in this field.
To learn more and explore further possibilities, get in touch with a member of the Elmarco team today.
References and Further Reading
- Feng, C., Khulbe, K. C., Matsuura, T., Tabe, S., & Ismail, A. F. (2013). Preparation and characterization of electro-spun nanofiber membranes and their possible application in water treatment. Separation and Purification Technology, 102, 118–135. https://doi.org/10.1016/j.seppur.2012.09.037
- Elmarco (2023) Sustainability in Electrospinning, https://youtu.be/B2LlG8kI9p8, accessed July 2023
- Zhang Y, Zhang C, Wang Y. Recent progress in cellulose-based electrospun nanofibers as multifunctional materials. Nanoscale Adv. 2021;3(21):6040-6047. doi:10.1039/d1na00508a
- Celebioglu A, Saporito AF, Uyar T. Green Electrospinning of Chitosan/Pectin Nanofibrous Films by the Incorporation of Cyclodextrin/Curcumin Inclusion Complexes: pH-Responsive Release and Hydrogel Features. ACS Sustain Chem Eng. 2022;10(14):4758-4769. doi:10.1021/acssuschemeng.2c00650
- Zhou, Y., Liu, Y., Zhang, M., Feng, Z., Yu, D. G., & Wang, K. (2022). Electrospun Nanofiber Membranes for Air Filtration: A Review. Nanomaterials, 12(7). https://doi.org/10.3390/nano12071077
- Syberg, K., Nielsen, M. B., Westergaard Clausen, L. P., van Calster, G., van Wezel, A., Rochman, C., Koelmans, A. A., Cronin, R., Pahl, S., & Hansen, S. F. (2021). Regulation of plastic from a circular economy perspective. Current Opinion in Green and Sustainable Chemistry, 29, 100462. https://doi.org/10.1016/j.cogsc.2021.100462
- Mosher, C. Z., Brudnicki, P. A. P., Gong, Z., Childs, H. R., Lee, W., Antrobus, R. M., Fang, E. C., Schiros, T. N., & Lu, H. H. (2022). Green electrospinning for biomaterials and biofabrication. Biofabrication, 13(3), 035049. https://pubmed.ncbi.nlm.nih.gov/34102612/
- Avossa, J., Herwig, G., Rossi, R. M., & Toncelli, C. (2022). Electrospinning based on benign solvents: current definitions, implications and strategies. Green Chemistry, 24, 2347–2375. https://doi.org/10.1039/d1gc04252a
- M. Kurecic, Mohan, T., Virant, N., Maver, U., Stergar, K., Gadinsknik, K., Kleinschek, K. S., & Hribernik, S. (2019). A green approach to obtain stable and hydrophilic cellulose-based electrospun nanofibrous substrates for sustained release of therapeutic molecules. RSC Advances, 0, 21288–21301. https://doi.org/10.1039/c9ra03399h
- Zhang, X., Ru, Z., Sun, Y., Zhang, M., Wang, J., Ge, M., Liu, H., Wu, S., Cao, C., & Ren, X. (2022). Recent advances in applications for air pollutants purification and perspectives of electrospun nanofibers. Journal of Cleaner Production, 378, 134567. https://doi.org/10.1016/j.jclepro.2022.134567

This information has been sourced, reviewed and adapted from materials provided by ELMARCO.
For more information on this source, please visit ELMARCO.