DriveAFM by Nanosurf AG is a new flagship AFM platform. The device incorporates a tip-scanning atomic force microscope (AFM) that integrates, for the first time, various capabilities in a single instrument to allow new measurements in life sciences and materials.
The DriveAFM overcomes flaws of other tip-scanning instruments and offers atomic resolution collectively with fast force spectroscopy, fast scanning and large scan sizes ranging up to 100 µm.
As a result of Nanosurf’s innovations in optical beam path engineering and scanner design, the Drive scan features photothermal actuation and complete motorization for excellent research performance and is user-friendly for scientists during all stages of practice.
- Ultra-low noise
- CleanDrive: stable excitation in liquid and air
- Fully motorized system: full control through software
- Direct drive: high-resolution imaging and large scan area available
DriveAFM introductory webinar trailer
This video shows the summary of the introductory webinar about the DriveAFM. Users will see the main topics that are discussed in the full webinar. Video Credit: Nanosurf AG
CleanDrive: Stability in Air and Liquid with Photothermal Excitation
Photothermal excitation of the cantilever offers unsurpassed stability, a linear frequency response and a high excitation bandwidth in liquid and air surroundings. These advantages enable measurements at various frequencies and high-speed applications and set the stage for innovative new measurement modes (for example, PicoBalance).
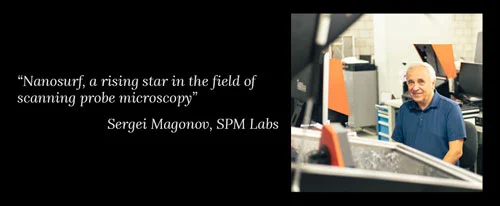
Image Credit: Nanosurf AG
These benefits are amplified in liquids as only the cantilever beam seems to be excited and the liquid environment remains highly untroubled. This leads to clean resonance peaks and not the “forest of peaks” that is seen generally with the piezo acoustic excitation of cantilevers.
Moreover, this technique of exciting the cantilever is not sensitive to variations in the surrounding and distance to the sample. This makes the complete measurement system highly stable.
The availability of small light spots in DriveAFM is consistent with the usage of small cantilevers, having numerous benefits that make them excellent in performance. As they have the same spring constant as a traditional cantilever, small cantilevers display a considerably greater operational bandwidth and resonance frequency.
Furthermore, the noise performance is improved. As a result of the small dimensions, the sensitivity has been raised, and hydrodynamic drag is decreased. All of this leads to better imaging performance.
Photothermal excitation (CleanDrive)
Photothermal excitation of the cantilever is the new best practice for high-performance AFM systems. The animation shows how the cantilever is actuated by an oscillating laser hitting the base of the cantilever beam. Video Credit: Nanosurf AG
Ultra-Low Noise
The DriveAFM consists of a very low overall noise floor, obtained via a combination of a low-noise/low-coherence superluminescent diode and a low-noise/high-bandwidth photodetector utilized in the low-noise/high-bandwidth CX Controller and the beam deflection detection module. This is considered to be the basis for the stable, sensitive and high-resolution imaging and force spectroscopy capability of the DriveAFM.
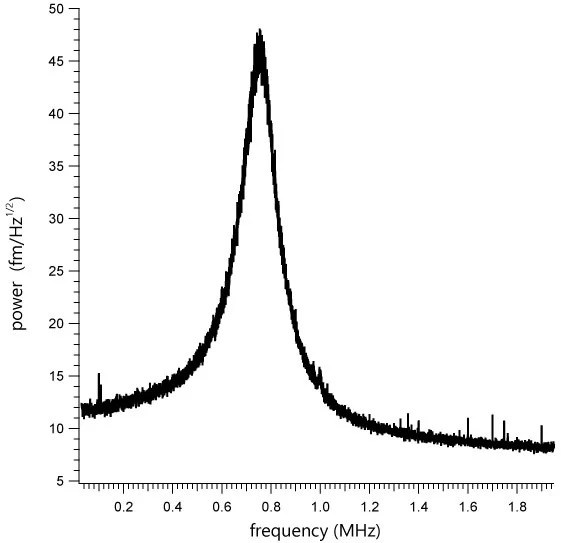
Image Credit: Nanosurf AG
Direct Drive Scanner
The DriveAFM makes good use of the power of direct drive piezo actuation. The 1:1, non-geared actuation scheme of the DriveAFM’s flexure scanner offers more force and could push stiffer scanners. The consequent higher resonance frequency of the scanner components enables a greater available actuation bandwidth compared to the geared drives of the same scan size.
Together with the low-noise 28-bit CX Controller, the direct drive scanner actuation enables both imaging at large scales and at high resolution. The DriveAFM is known to be the ideal solution for high-resolution imaging of exacting samples like proteins, nanostructures or polymeric structures (for example DNA), and also for bigger and micrometer-sized structures.
Full Motorization
The DriveAFM is known to be the first completely motorized AFM system that could be combined with an inverted optical microscope. The adjustment of the two light sources for the beam deflection detection system and the CleanDrive photothermal excitation, as well as the photodetector, are completely motorized and could be regulated from the software.
Also, the tip technique to the sample is motorized. The complete motorization not only contributes to the simple use but also enables new possibilities to completely automate the system.
DriveAFM Imaging Modes
This overview outlines which modes the instrument is capable of. Few modes might need software options or extra components. For details, users can view the brochure or contact the support team directly.
Standard Imaging Modes
- Static force mode
- Phase imaging mode
- Lateral force mode
- Dynamic force mode (tapping mode)
Magnetic Properties
- Magnetic Force Microscopy
Electrical Properties
- Electrostatic force microscopy (EFM)
- Conductive AFM (C-AFM)
- Kelvin probe force microscopy (KPFM)
- Piezoelectric force microscopy (PFM)
Mechanical Properties
- Force modulation
- Force spectroscopyUnfolding and stretching
- Adhesion
- Force mapping
- Stiffness and modulus
- Electrochemical AFM (EC-AFM)
- Lithography and nanomanipulation
System Specifications
Table 1. Scan Head. Source: Nanosurf AG
. |
. |
Scan size |
typ. typ. 100 µm x 100 µm x 20 µm
min. 95 µm x 95 µm x 18 µm |
Read-out light source |
850 nm low-coherence SLD |
CleanDrive light source |
785 nm laser |
Photodetector bandwidth |
≥8 MHz |
Standard / maximum sample size |
100 mm / 150 mm |
Z-height noise dynamic |
<30 pm (RMS) |
Z-height noise static |
<30 pm (RMS) |
DC detector noise* |
<5 pm (RMS, 0.1 Hz – 10 kHz) |
AC detector noise* |
<25 fm/√(Hz) above 100 kHz |
Approach |
10 mm motorized, parallel |
(*) measured with a USC-F1.2-k7.3 cantilever
Table 2. CX Controller. Source: Nanosurf AG
. |
. |
High resolution outputs (DAC) |
12x 28 bit, 1 MHz/sampling; thereof 4x user DAC (optional) |
Fast outputs (DAC) |
4x 16 bit, 100 MHz/sampling; thereof 1x user DAC (optional) |
High resolution inputs (ADC) |
12x 20 bit, 1 MHz/sampling; thereof 4x user ADC (optional) |
Fast inputs (ADC) |
3x 16 bit, 100 MHz/sampling; thereof 1x user ADC (optional) |
Signal analyzers |
2 signal analyzer function blocks that can be configured as dual channel lock-in |
FPGA module and
embedded processor |
System-on-chip module with low-latency FPGA signal processing at 100 MHz and dual-core ARM processor, 2 GB RAM, 1.5 GHz clock |
Scan control |
28-bit X/Y/Z-DAC |
Detector inputs |
Deflection/lateral signals each 20 bit |
Digital sync, Spike-Guard |
2-bit line/frame sync out 5 V/TTL galvanically isolated, Spike-Guard input |
Clock sync |
10 MHz/3 V clock input to synchronize data acquisition and processing |
Communication to PC |
Gigabit Ethernet, galvanically isolated |