Yttria Partially Stabilized Zirconia (YPSZ) is a high toughness ceramic which has recently found increasing use in the production of dental prostheses [1].
In order to deliver a finish which is aesthetically pleasing for dental applications, YPSZ copings are veneered with porcelain. Yet, the main cause of failure for YPSZ prostheses is also caused by this – namely, near interface chipping of the porcelain veneer [2]. However, this failure’s origins have been poorly understood.
Studies conducted recently have suggested that this chipping is connected to the variation in mechanical properties and residual stress rate within a few microns of the interface [3, 4]. It is consequently vital that information is gathered concerning microscale spatial variation of fracture toughness so that this failure can be understood.
Recently, Sebastiani et al. proposed a microscale fracture toughness approach which is based upon the fracture of micropillars and nanoindentation [5, 6]. It is possible to implement this approach in a relatively short time period, and it also benefits from a microscale gauge volume which is well-defined. These qualities facilitate high resolution fracture toughness mapping and profiling.
This technique exploits the precision and speed of FIB milling for milling arrays of micropillars. Figure 1 depicts the six key steps of this technique.
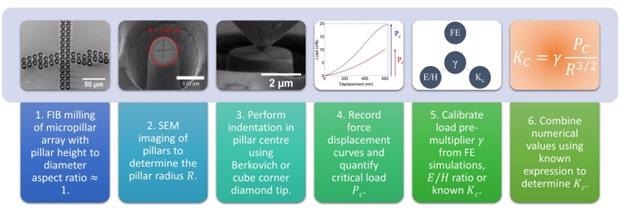
Figure 1. Flow diagram of the micropillar splitting approach.
Experimental
Using a multi-stage polishing process and a low speed diamond saw, the cross section of the YPSZ-porcelain interface was prepared (Figure 2). Subsequently, an array of micropillars with nominal height and diameter of 5 μm was generated using FIB milling.
As a means of obtaining a higher density of measurements at the location the majority of variation was anticipated, more pillars were milled near the interface. Subsequently, in order to determine the pillar radius and its distance from the interface, SEM imaging was then performed.
An Alemnis Indenter (Alemnis AG) was used to perform nanoindentation. The Alemnis AG was in displacement control mode in a scanning electron microscope, in order to record the force-displacement curves which are displayed in Figure 3.

Figure 2. Micropillars across the YPSZ Porcelain interface.
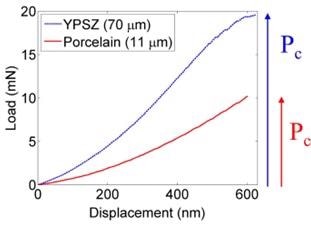
Figure 3. Typical load‐displacement curves in the porcelain and YPSZ.
On 12 pillars which were far from the interface, Berkovich indentation was performed at the location where fracture toughness was anticipated to be nominally uniform in order to measure the pre-multiplier value.
The remaining 48 indentations were performed with a cube corner tip as a means of improving indentation positioning’s precision, as this offers a larger viewing angle.
Results and Discussion
The bulk values of Young’s modulus and hardness were used to determine the Berkovich pre-multiplier values (yB) for YPSZ and porcelain, in order to provide estimates of each material’s bulk fracture toughness (KB) as Table 1 displays.
Table 1. Mechanical properties and indentation load pre‐multipliers for YPSZ and porcelain.
Material |
E
(GPa) |
H
(GPa) |
γB |
γC |
KB
(MPa.m1/2) |
YPSZ |
210
[7] |
12.75 ± 0.96
[7] |
0.31 ± 0.02 |
1.10 ± 0.05 |
4.79 ± 0.24 |
Porcelain |
60
[8] |
5.40 ± 0.20
[9] |
0.22 ± 0.01 |
0.41 ± 0.04 |
2.65 ± 0.27 |
In order to quantify estimates of the cube corner pre-multiplier (yC) for each material, these results were subsequently compared with the cube corner indentation performed at the same location. Three estimates were used to perform the remaining analysis, with an average value of YPSZ and porcelain being used for the pillars situated at the interface.
Figure 5 shows the distribution of fracture toughness as a function of distance from the interface. The results indicated that the porcelain pillars exhibited a highly brittle failure without any noticeable deviation in the loading curve prior to failure (Figure 3).
Conversely, prior to failure, a gradient decrease was observed in the loading curve of YPSZ. As Figure 4 demonstrates, SEM videos of the indentation showed that this was associated with small amounts of pre-cracking in the pillar.
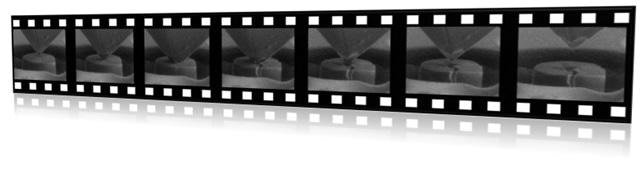
Figure 4. Stills from micrograph video of YPSZ indentation showing crack growth in the pillar before complete failure.
As Figure 5 shows, distinct differences were revealed in the pillar failure response by post-fracture SEM imaging of the pillars. The porcelain micropillars tended to fracture fully, leaving just the highly faceted pillar stub.
In pillars containing both porcelain and YPSZ, preferential half-pillar cracking was observed in a direction parallel to the interface. There were also differences observed between the Berkovich YPSZ indentation response and the cube corner, with the latter exhibiting highly faceted central cracking and the former primarily displaying edge cracking.
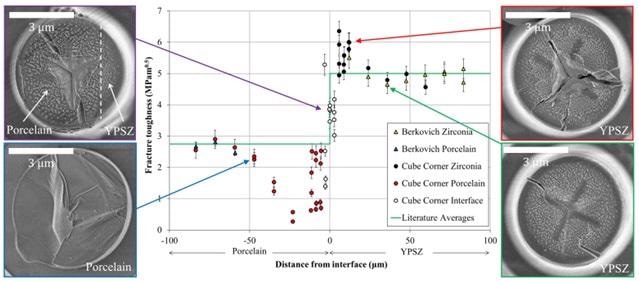
Figure 5. Fracture toughness variation across the YPSZ – porcelain interface. SEM imaging of the different types of pillar failure are shown.
Analysis of the data presented in Figure 5 shows that both porcelain and YPSZ exhibit a ‘bulk’ fracture toughness response at distances far from the interface.
An increased scatter is seen at the interface, which is probably associated with the porcelain nanovoiding which is present at this location [4].
A ~15% increase in fracture toughness is observed in YPSZ close to the interface. This effect is associated with the larger YPSZ grains located here [4], as well as the related increase in KC [7].
A clear and consistent toughness reduction of as much as 90% at the location where chipping is known to originate is exhibited by porcelain within 50 μm of the interface. This substantial toughness reduction has been revealed for the first time in these results, which have quite likely identified the origin of persistent failure.
Direct optimization of the manufacturing routine can be facilitated by this finding, with the goal of increasing the toughness at this location and consequently reducing prosthesis failure rates.
Conclusions
This study is the first to use the micropillar splitting technique to demonstrate microscale spatially resolved fracture toughness assessment. A relatively short time is required to implement this experimental technique, which can overcome many of the limitations related to fracture toughness techniques of comparable resolution.
This new method paves the way for a wide range of applications and constitutes a powerful tool for microscale spatially resolved mechanical property analysis.
References
[1] Denry I, Kelly JR. State of the art of zirconia for dental applications. Dental Materials 2008;24:299‐307.
[2] Baldassarri M, Stappert CFJ, Wolff MS, Thompson VP, Zhang Y. Residual stresses in porcelain‐veneered zirconia prostheses. Dental Materials 2012;28:873‐9.
[3] Alghazzawil TF, Janowski GM. Evaluation of zirconia‐porcelain interface using X‐ray diffraction. International Journal of Oral Science 2015;7:187‐95.
[4] Lunt AJG, Mohanty G, Ying S, Dluhos J, Sui T, Neo TK, et al. A comparative transmission electron microscopy, energy dispersive x‐ray spectroscopy and spatially resolved micropillar compression study of the yttria partially stabilised zirconia ‐ porcelain interface in dental prosthesis. Thin Solid Films 2015;596:222‐32.
[5] Sebastiani M, Johanns KE, Herbert EG, Carassiti F, Pharr GM. A novel pillar indentation splitting test for measuring fracture toughness of thin ceramic coatings. Philosophical Magazine 2015;95:1928‐44.
[6] Sebastiani M, Johanns KE, Herbert EG, Pharr GM. Measurement of fracture toughness by nanoindentation methods: Recent advances and future challenges. Current Opinion in Solid State & Materials Science 2015;19:324‐33.
[7] Zenotec Zr Bridge.
[8] Uchic MD, Dimiduk DA. A methodology to investigate size scale effects in crystalline plasticity using uniaxial compression testing. Materials Science and Engineering a‐Structural Materials Properties Microstructure and Processing 2005;400:268‐78.
[9] IPS e.max® Ceram Scientific Documentation.
This article is based on the paper “Microscale resolution fracture toughness profiling at the zirconiaporcelain interface in dental prostheses” published in Proceedings of SPIE 9668, Micro+Nano Materials, Devices & Systems (Dec 2015) DOI: 10.1117/12.2199217 Authors: Alexander J. G. Lunt, Gaurav Mohanty, Tee K. Neo, Johann Michler and Alexander M. Korsunsky http://proceedings.spiedigitallibrary.org/proceeding.aspx?articlei d=2479425
Alexander J. G. Lunt [1], Gaurav Mohanty [2], Tee K. Neo [3], Johann Michler [2] and Alexander M. Korsunsky [1]
University of Oxford, U.K. [2], Empa, Switzerland [3], Mount Elizabeth Medical Centre, Singapore
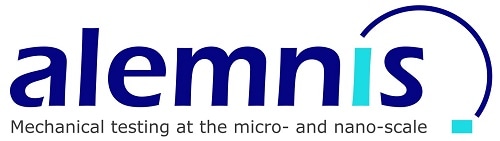
This information has been sourced, reviewed and adapted from materials provided by Alemnis AG.
For more information on this source, please visit Alemnis AG.