This article features newly announced Park FX40, a groundbreaking autonomous atomic force microscope, infused with innovative robotics, intelligent learning features, safety features, software and specialized add-ons. Park FX40 Atomic Force Microscope is the first AFM to automate all up-front set up and scanning processes, putting the intelligent Park FX40 in a groundbreaking new class of atomic force microscope. The article includes sample analysis using new automated features of Park FX40.
Expanding upon the cross-talk elimination design of the XE- and NX-series of AFMs, FX40 further improves the performance and productivity that is accessible to everyone. Through the use of the FX40, meaningful and high-definition data can be acquired with just a few clicks.
From start to finish, this article explains the imaging process, along with examples demonstrating real-world applications.
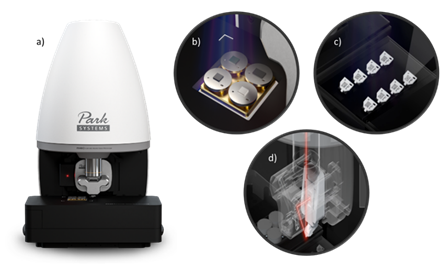
Figure 1. Park FX40 Atomic Force Microscope. (a) FX40 main-body, (b) multi-sample chuck showing kinematic mounting plates, (c) tip cassette for automated tip exchange (ATX), and (d) new beam-bounce scheme to measure cantilever deflection. Image Credit: Park Systems
With an atomic force microscope (AFM), the user can reliably take repeated measurements of surface topography in three dimensions, with sub-nanometer resolution. Additional information such as magnetic, electrical, chemical, or nano-mechanical information can be recorded simultaneously, producing a large volume of information from just a single instrument. Sample preparation, if required, is minimal and the cost of ownership is low when compared to similar techniques.
Images can be attained in a controlled atmosphere, liquids, and air, making AFMs indispensable tools in research and industrial applications. Before acquiring any AFM data, the user must select an appropriate cantilever/tip (or probe), load it into the tool using tweezers, before aligning the optical detection system and viewing optics. Only then can a sample be loaded, and the areas to image be selected.
The user then has to select a basic imaging mode, such as Tapping or Non-contact, tune the system, and manually guide the AFM tip to within detection range of the surface. To acquire valid surface information, the operator must instruct the AFM how to track the surface – often based just on “visual” feedback.
Such complex procedures have stopped AFM from becoming mainstream, as it generally requires experienced technicians to acquire reproducible data of a high standard.
Park Systems AFMs, like the NX- or XE-series, have already resolved some of the existing hurdles; a user-friendly interface that aids the operator select imaging parameters based on objective boundary conditions, and the addition of pre-mounted tips. However, the FX40 goes one step further by automating the entire imaging process; this removes barriers, allowing for the quick and easy generation of consistent data. This essential step forward affords access to a wider audience, and subsequently, the valuable nano-metrology information AFM can produce.
Further to the automated imaging process, FX40's new optomechanical design elevates measurement precision and data quality. The low-level noise allows the FX40 to perform, with ease, accurate nano-metrology on the most challenging of samples. Although counterintuitive, a frequent challenge for AFM is the acquisition of accurate data on large, flat samples.
Here, FX40 expands upon the experience gained by using cross-talk elimination on the previous generation of Park AFMs. The raw out-of-plane-motion (OPM) before image correction is <2 nm over 80 mm scan range, allowing precise measurements but without the effect of common leveling artifacts.
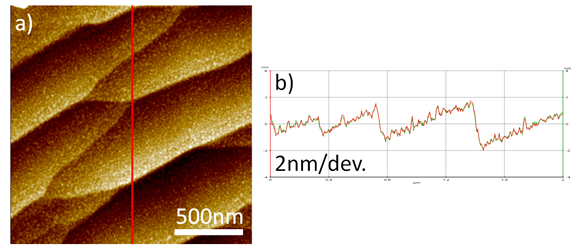
Figure 2. Low noise levels for accurate nano-metrology. a) Atomic terraces on sapphire, b) Linescan profile of sapphire. Steps with sub-nm features signals are perfectly matched in forward (red) and reverse scan (green). Image Credit: Park Systems
The following describes the procurement process for topographic images using four different samples, whilst demonstrating the automation capability of Park FX40, including the easy sample-to-sample navigation:
- The first sample, a semi-fluorinated alkane (F14H20), is assembled on a silicon substrate (Figure 8).
- The second sample, graphene on boron nitride, is a common 2D material system, currently studied for its electronic properties (Figure 9).
- The third sample is a co-polymer of styrene-butadiene-styrene (Figure 10).
- The fourth sample is polytetrafluoroethylene (Teflon), a polymer with a broad variety of industrial applications (Figure 11).
As well as topographic data, FX40 can obtain further physical information about the sample, and correlate this with the topography. Four examples are given in Figure 3: nano-mechanical information including adhesion information or modulus (Figure 3a), magnetic information such as studying samples under controllable external magnetic fields (Figure 3b), nanolithography (3c), and measuring electrical properties with high spatial frequency (3d).
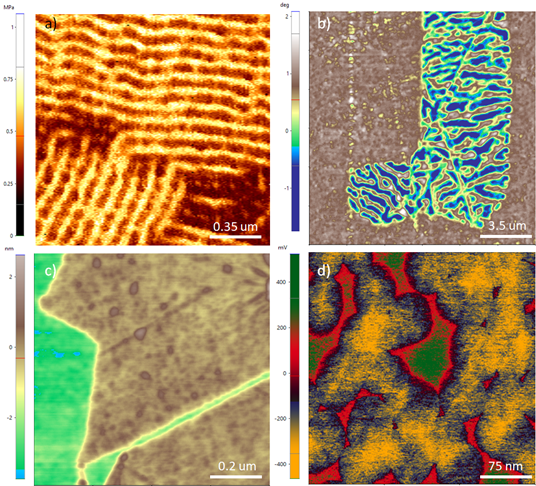
Figure 3. A small sample of FX40 Data acquisition modes. a) Young’s Modulus of block copolymers obtained by PinPointTM. b) Magnetic Vortex Cores in Cr/Ni/Mo alloy obtained by Magnetic Force Microscopy. c) Topography of divided graphene flakes. d) Surface Potential of Semifluorinated alkanes obtained by Sideband KPFM: Negative potential (yellow/blue section) identifies the alkanes relative to the substrate. Image Credit: Park Systems
Experimental
From tip mounting to final imaging, the real-time operational process is executed in three simple steps, and described below in the following outline:
- “ATX” (Automatic Tip Exchanger) – the user selects the cantilever for the chosen imaging mode. With no extra input from the operator, FX40 mounts the probe-tip automatically and then, by using machine learning, aligns the beam-bounce system for optimal cantilever detection.
- “Sample'' – the operator selects the sample and required initial imaging area using the two built-in, high-performance optical viewing systems. After selecting, the AFM moves to the chosen area, performs the required tuning operations, and automatically moves towards the sample. The built-in optical autofocus system allows for a tip-sample approach within seconds.
- The automatic AFM scan and data acquisition starts.
This article splits the methodology into discrete steps, whilst explaining the mechanism behind each one.
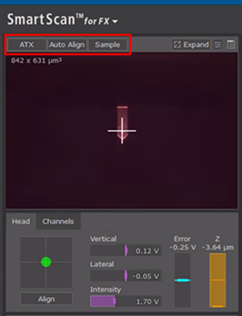
Figure 4. Part of the SmartScanTM Interface for FX40. “ATX” button in the top left corner enables the automatic-tip exchange. Auto align button focuses the cantilever, aligns the SLD and the photo detector. Sample button enables the sample navigation camera, allowing the user to select the desired sample. Image Credit: Park Systems
Step 1: Auto Tip Mounting and Beam Alignment
By reading the QR-codes on the chip carriers in the probe cassette, the software can identify the probe type. After identification, the user may select their chosen probe, and FX40 automatically picks the corresponding probe from the cassette. Subsequently, the FX40 finds the super-luminescent diode (SLD) and cantilever and automatically performs the photodetector alignment.
The Park FX40 positions the SLD within the optical microscope; this inventive design guarantees that the SLD beam is focused at the center of the lens at all times. As a result of the fixed position of the SLD, centering the cantilever in the middle of the optics immediately aligns with the SLD.
To conclude beam-bounce alignment, embedded motors in the AFM head fine-tune the angle of the steering mirror, which automatizes the photodetector alignment process – all with one simple click. The automatization of this process eliminates human error and ensures faultless and consistent operation with every use.
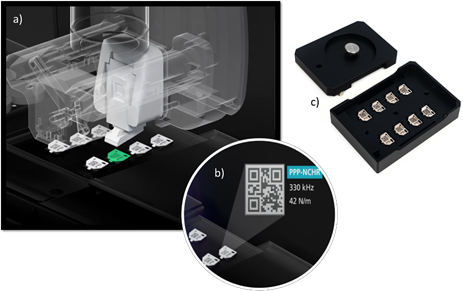
Figure 5. Automatic tip exchanger (ATX). a) View of automatic tip exchange slots image with cantilevers. b) Magnified rendering of QR codes that allows the system to recognize the selected probe and automatically upload the cantilevers profile. c) Probe cassettes can easily be removed and exchanged. Image Credit: Park Systems
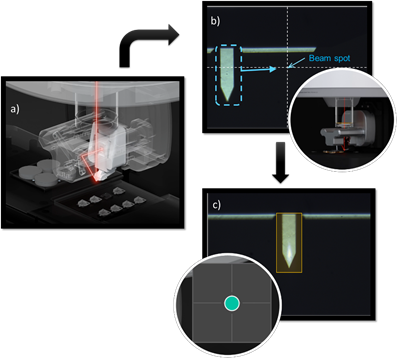
Figure 6. Optical cantilever alignment and laser beam detection. a) Park FX40 superluminescent diode beam path. b) Machine learning is used to center the cantilever. c) Centering the cantilever automatically aligns the beam-bounce system. Image Credit: Park Systems
Step 2: Auto Sample Positioning
FX40 uses a dedicated sample view camera to move the probe to the desired location. Depressing the “Sample” button (Figure 4) will open the positioning panel and activate the sample view camera. The sample view camera is situated above the sample chuck and can store a maximum of four samples.
After the desired initial imaging location has been selected, the system immediately navigates toward the area selected (Figure 7). After choosing the preferred imaging spot, FX40 performs a fully automated, fast tip-sample approach [3].
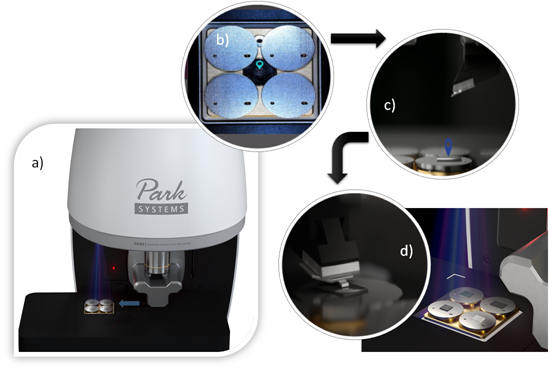
Figure 7. Sample navigation. a) Park FX40 main body with the multi-sample chuck kinematically locating the samples. b-d) Sample panel activates and allows the user to select the desired spot on the sample. The cantilever then moves to the user selected location and automatically approaches at the selected sample location. After completing data acquisition, the software secures the system by lifting the Z stage and turning the SLD off. The used probe returns to the ATX cassette if the operator does not plan to use it right away. Image Credit: Park Systems
Step 3: Auto Imaging
SmartScan Auto Image Mode is selected to obtain the topographical data. This feature performs all the required imaging operations and cleverly selects the optimum scan speed and image quality. By selecting this mode, consistent data quality is guaranteed, independent of users’ ability and experience.
Processes such as the operations setpoint, cantilever frequency sweep, gain adjustment, or scan speed are part of the automatized procedures. As a result, this level of automatization greatly reduces the amount of manual operator input and manipulation required and therefore saving time.
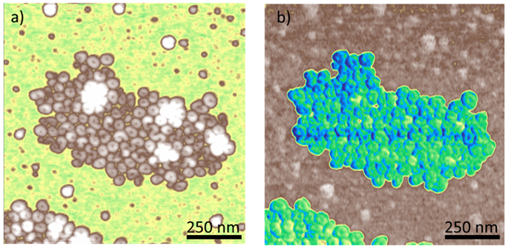
Figure 8. Semifluorinated alkanes on Si. (a) Topography image depicting the spiral morphology of the sample (vertical scale range 0 to 12 nm) and (b) Phase image of F14H20 alkanes (vertical scale range 0 to 6 degrees). The phase highlights additional sample details. Image Credit: Park Systems
Testament to the automation capabilities of FX40, the data in Figure 8 was obtained within a couple of minutes, from beginning to end. Figure 8 illustrates the high-quality topography data acquired using an NCHR cantilever in non-contact mode, which unmistakably depicts the spiral superstructure of the F14H20 aggregates.
After imaging the first sample, the “Sample” button was activated, instructing the FX40 to proceed to the next sample: Graphene on h-BN. The same cantilever was used to generate the topography data, capturing the Moiré patterns information from the sample (Figure 9).
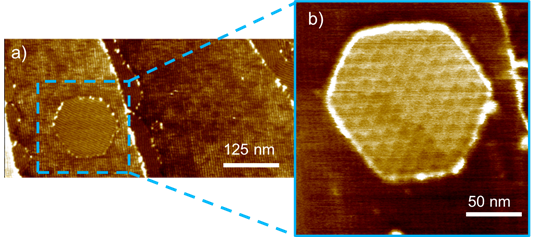
Figure 9. Moiré pattern observed on graphene on h-BN. a) Topography scan of graphene on h-BN, vertical scale 0 to 6 nm. b) Zoom in: Moiré pattern clearly visible, vertical scale 0 to 6 nm. Image Credit: Park Systems
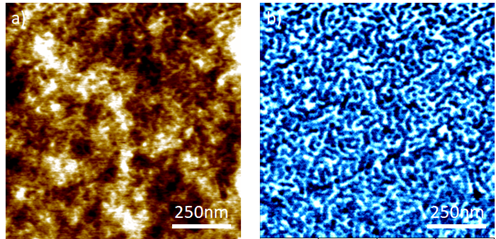
Figure 10. Styrene-butadiene-styrene (SBS) copolymer. a) Topography, vertical scale range 0 to 5 nm. b) Corresponding phase showing the organizational structure, vertical scale range 0 to 5 degrees. Image Credit: Park Systems
Again, the same tip was used to image the third sample. The phase image in Figure 10 emphasizes the composition of the sample. For the fourth-and-final sample, the tip was changed for a high-frequency tip and positioned into the scan location on the multi-sample chuck. Figure 11 depicts the molecular arrangement of the sample in-phase and topography data.
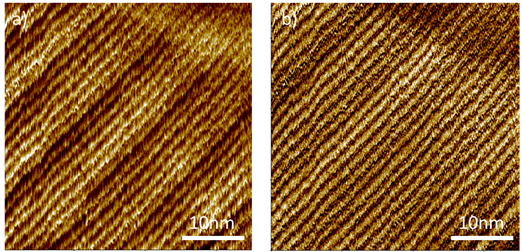
Figure 11. High resolution Image of PTFE (Teflon). a) High resolution topography. Vertical scale range 0 to 3 nm b) Corresponding phase image. Vertical scale range 0 to 10 degrees. Image Credit: Park Systems
Conclusion
This article demonstrates the advanced imaging capabilities, innovative design and ease of operation of the new Park FX40. This automatic AFM system can quickly generate high-quality images using novel techniques such as pattern recognition and machine learning, including fully automatic tip exchange and alignment and QR-code-based tip selection.
Lastly, FX40 can generate precise data with its low signal-to-noise ratio, and intuitive user interface. Park FX40 is a major development in metrology and nano-technology that will facilitate innovation and discoveries across engineering and nanoscience fields.
Acknowledgments
Produced materials originally authored by Armando Melgarejo, Cathy Lee, Charles Kim, Ben Schoenek, Jiali Zhang, Byong Kim, and Stefan Kaemmer from Park Systems Corporation.
References
- Park SmartScanTM: Park AFM Operating Software https://parksystems.com/products/operating-software/park-smartscan
- Park Systems (2020). Probe Store. California, USA: https://parksystems.com/service/probe-store
- Park Systems Inc (2015). Revolutionary Park Systems SmartScan Automatizes the Atomic Force Microscope Imaging Process – High-Quality Images at Click of a Button. California, USA. https://www.parksystems.com/en/news-events/news
- Park Systems Inc (2021). NCHR Cantilever. Probe Store. California, USA: https://parksystems.com/service/probe-store
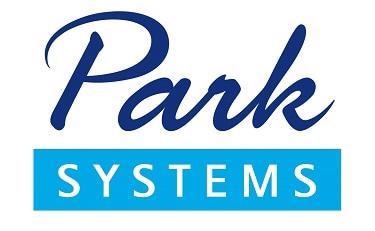
This information has been sourced, reviewed and adapted from materials provided by Park Systems.
For more information on this source, please visit Park Systems.