In modern electronic devices such as digital cameras, mobile phones, portable gaming consoles, laptops or netbooks, sensors and micro-optical systems are decisive interfaces between the real world and the microelectronics inside.
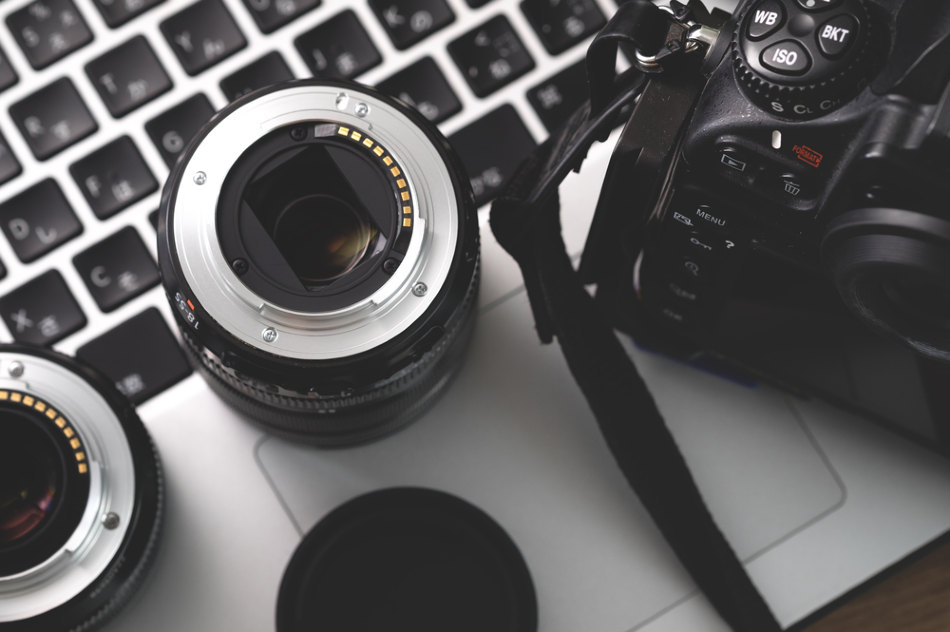
Image Credit: Shutterstock/structuresxx
The transition from discrete assembly to wafer-level integration of these components, using well-established and emerging semiconductor technologies, results in increased performance and functionality, reduced energy consumption, smaller form factors and lower costs. In addition to wafer-level cameras, which started to replace conventional modules several years ago, wafer-level optics (WLO) manufacturing solutions from EVG enable a host of new optical sensing devices for mobile consumer electronics products. Biometric authentication, 3D sensing, microlens and camera arrays, infrared sensing, and environmental sensing are major examples of optical sensing solutions and devices. Other applications include medical imaging, automotive front-lights, optical diffusers, and light carpets.
EVG’s NILPhotonics Competence Center supports the company’s WLO solutions.
Wafer Level Cameras (WLCs)
Wafer level cameras (WLCs) are devices in which all the individual parts are fabricated at wafer level and are then bonded to form one single part consisting of a CMOS image sensor (CIS) and a micro-optics stack enhancing the light capture efficiency of the camera.
UV imprint lithography, originally developed for cost-efficient replication of structures in the nanometer range, is now considered a powerful tool for the fabrication of wafer-level optics in highly parallel mass fabrication processes.
EV Group offers manufacturers a complete range of solutions, including master stamp fabrication, replication and integration of optical elements at wafer level based on its well-established mask alignment and nanoimprint lithography systems. Its product portfolio is highly versatile, enabling customers to implement highly customized hardware and software processes. Coupled with process development and optimization in EV Group's cleanroom facilities, EV Group provides a total solution from system configuration and fabrication to process integration and material know-how.
.jpg)
Elements of a typical wafer-level camera module include a CMOS image sensor, polymeric lenses molded onto glass carriers by UV imprint lithography, spacers and aperture layers, as shown in this exploded view. Source: EVG
Master Stamp Fabrication
Master stamps are wafer-size templates fully populated with microlens molds, each replicated from a single lens or lens array template in a step-and-repeat (S&R) approach. Starting from a single lens master made out of metal, silicon, or glass, EV Group offers all essential process steps for the fabrication of master stamps featuring unmatched lens position accuracies of <100 nm and high lens shape repeatabilities.
Individual S&R process steps featured by EV Group:
- High precision positioning of single lens template across the wafer
- Droplet dispense of master stamp material
- Wedge compensated force or distance controlled high-precision first imprint
- UV exposure
- Demolding
Please see our related product EVG®770 Gen II NILStepper for detailed information.
UV Microlens Molding
Soft UV Imprint Lithography is a highly parallel technique for the fabrication of polymeric microlenses, the key elements of wafer level optical systems. Through this soft UV Imprint Lithography process, lens patterns can be converted into optical polymer materials using working stamps simulated from wafer-size master stamps. Therefore, starting out from soft working stamps replicated from wafer-size master stamps, EV Group offers hybrid and monolithic microlens molding processes which can be easily adapted to various material combinations for working stamp and microlens materials. In addition, EV Group offers a qualified microlens molding process including all relevant material know-how. When it comes to high-volume wafer-level lens replication, EVG systems are customers’ first choice.
.jpg)
Soft UV Imprint Lithography Setup for single and double side lens molding. Source: EVG
Individual UV Molding process steps featured by EV Group:
- Puddle dispense of optical pre-polymer
- Wedge compensated force or distance controlled aligned imprint
- UV exposure
- Demolding
Please see our related product IQ Aligner® for detailed information.
.jpg)
Single side 300 mm lens wafer fabricated by Soft UV Imprint Lithography.
Source: EVG
SmartNIL®
EVG offers industry-leading UV-nanoimprinting equipment with its sturdy and field-proven SmartNIL technology. Advances in photonic manufacturing technologies and processes as well as applications are closely associated with developments in equipment capabilities. Among these, new developments in SmartNIL® provide additional degrees of freedom to fabricate novel photonic structures with the smallest form factors and highest functionality at high volumes. This proprietary technology enables diffractive optical elements (DOEs), optical waveguides and other micro- and nanophotonic elements used for 3D sensing, biometric authentication or augmented reality.
With SmartNIL technology, the manufacturing of extremely small features down to less than 40 nm, a wide range of structure sizes and shapes and nanopatterning of high-topography or rough surfaces is supported. Since SmartNIL incorporates multiple-use soft stamp processing, it enables unmatched throughput with considerable cost-of-ownership advantages while preserving scalability and maintenance-friendly operation. In addition, the lifetime of the master template is extended to periods comparable to masks used for optical lithography. EVG's SmartNIL redeems the long-term promise of nanoimprinting being a low-cost and high-volume alternative lithography technology for mass manufacturing of micro- and nanoscale structures.
Gen 2 panel polarizer imprinted on the EVG®7200 LA
.jpg)
EVG® SmartNIL® full-area imprinted 150 mm Si substrate
Sub-100 nm resolution lines replicated using SmartNIL®
Aligned UV Bonding
The final micro optics stack is fabricated by UV bonding of all elements, including individual double-side microlens wafers as well as spacer wafers, to achieve the final stack height. Crucial parameters are lens-to-spacer alignment accuracy, lens-to-lens alignment accuracy, total thickness variation of the resulting bond interface, tilt of the resulting bond interface, and wafer throughput.
Individual process steps featured by EV Group:
- Wedge compensated aligned UV bond
- UV exposure
Please see our related product IQ Aligner® and our Gemini® for detailed information.
.jpg)
Wafer-level micro lens arrays created utilizing UV-NIL.
.jpg)
Lens pattern fidelity measurement
.jpg)
SmartNIL® patterned optical nanostructures. Source: EVG, Master provided by IMS Chips
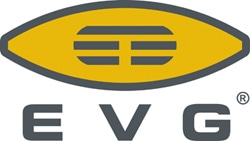
This information has been sourced, reviewed and adapted from materials provided by EV Group.
For more information on this source, please visit EV Group.