For many years tire manufacturers have been constrained into producing materials that fit within the ‘magic triangle’ of mechanical behavior.1 However, developments in atomic force microscopy (AFM) for nanomaterial analysis could allow manufacturers to free themselves from the magic triangle. AFM allows the relationships between nanostructure and mechanical performance to be better understood, facilitating the design of new, high-performance tread designs.1,2,3
The automotive market is already extremely competitive. In addition to this the market is under pressure from changes in customer needs, and more stringent environmental regulations, to develop vehicles that use less fuel, are cheaper to buy, require less maintenance and provide more driver/passenger safety.
How a tire performs has a significant impact on all of these factors; with a well-designed tire making the vehicle safer and more efficient (and therefore cheaper to run). In order to improve tire performance, manufacturers are now focusing efforts on developing novel, improved materials and tread designs.
.jpg)
Figure 1. Image Credit: pixabay.com/HutchRock
Understanding the Tire Magic Triangle
Improving the safety, fuel economy and tire durability of a tire at the same time is impossible using traditional tire development methods, as it places conflicting demands on the materials used to form the tread. As a result, tire manufacturers need to find a point of balance between three different key tire properties – these are the points of the triangle. These properties are:3,4,5,6
- Traction – How well a tire can grip to the road, which influences safety on ice and wet roads
- Rolling Resistance – The energy lost (inefficiency) as the tire rolls
- Wear Resistance – How durable the tire is, which determines its lifetime
Tread materials that are low energy absorbing, i.e. low hysteresis compounds, provide a better rolling resistance, however they wear quickly and have a poor rolling resistance. Whereas, high hysteresis materials absorb excess energy which protects the tire (resulting in better wear resistance) and provides better rolling resistance. As these properties work against each other it is extremely difficult to improve all three key properties at once. These are the limitations of the ‘magic triangle’.3
The Relationship Between Tire Performance and Tread Nanostructure
The treads of tires tend to be produced using a blend of rubber with a number of different nanostructured additives such as silica fillers, polymers, carbon black and nanoparticles. This complex constitution results in even more complex multiphase morphologies.7
The bulk mechanical properties of the blended rubber are the result of the morphology and phase behavior of the material on the micro- and nanoscale. Tailoring a tire for better traction, rolling resistance and/or wear resistance is possible by changing the volumes of different blend components, or by changing their distribution within the rubber blend. However, often changing these factors to improve one of the three key tire properties will have a negative impact on the other two properties.
Innovations in silica/silane technology in the 1990s produced a new generation of tires that expanded the magic triangle, improving rolling resistance and fuel efficiency without compromising on traction or wear resistance.
Tire developers now hope that by understanding the relationship between tire nanostructure and tire performance they will be able to optimize tire formulations. This could allow tire manufacturers to develop the next generation of tires, which are no longer constrained by the magic triangle. Nanocharacterization could be the key to the simultaneous improvement of traction, rolling resistance and wear resistance.8
AFM is the Best Method for Nanocharacterization
Recent research has shown that analysis of the nanostructure-performance relationships in tread design is the key to improving tire properties.
Atomic Force Microscopy (AFM) is an ideal method for the characterization and visualization of rubber blend nanostructures, the different components present in the blend, and the measurement of nanomechanical behavior.
AFM images a sample by tracing over the surface of a material with a nanosized mechanical probe, i.e. a cantilever. The nanoscale size of the cantilever allows AFM to image at greater resolutions (which can have pixel sizes of less than a nanometer) than optical methods, making it ideal for nanostructual analysis. In addition, AFM is non-destructive and requires only minimal sample preparation, meaning the technique is simple to run.
Characterization of nanostructures using AFM is usually carried out using tapping mode. In tapping mode the cantilever is oscillated close its resonance frequency. Interactions between the cantilever and the sample surface cause changes in the phase and amplitude of the oscillation, which are then used to characterize the surface.
Using a bimodal AFM method, which involves exciting another mode of resonance, allows more surface information, such as quantitative nanomechanical information and topography, to be collected.
Bimodal AFM could be one of the only AFM methods which can be used to differentiate between the different components in a tire rubber blend. Using a combination of amplitude modulation (AM) for the first resonance, and frequency operation (FM) for the second resonance gives an AM-FM mode. AM-FM can be used to rapidly create high-resolution images with data on the stiffness and mechanical moduli of the sample.9
An example of bimodal AFM images of a tire sample is shown in Figure 2. This research found that differences in the images, as a result of varying component distributions, correlated with differences in the tires hysteresis and energy dissipation. Elucidation of this performance-morphology relationship could be used to improve tread materials.
Further research has used AFM imaging to map the distribution of different phases in rubber blends, to determine the fatigue properties of the material and to characterize other forms of nanomechanical behavior. In addition, the relationship between the results of macroscale dynamic mechanical analyses (DMAs) has been directly correlated to nanoscale mechanical behaviors and morphologies.10-13
.jpg)
Figure 2. Bimodal Dual AC images of a tire sample. Low molecular weight oil and coupling agents are represented by lighter areas, while area rich in silica and carbon black appear darker. Imaged with the Cypher S AFM from Asylum. Image Credit: Asylum.
Asylum AFMs Provides Unparalleled Resolution and Nanomechanical Characterization Capabilities
Asylum Research is an industry leader in the field of AFM, with AFMs which provide images of the highest resolution and the richest nanomechanical data possible. Asylum can supply researchers with a range of AFMs of different specifications, all of which are suitable for the nanocharacterization of materials used in tire treads.
Asylum Research’s Cypher Polymer Edition AFM is the ideal tool for the analysis of tire treads. The Cypher Polymer Edition is equipped with an AM-FM viscoelastic mapping mode, which can be used to determine the nanomechanical properties of rubber blends.14
AFM’s in the Cypher range are also extremely mechanically stable, with low noise electronics and low drifts, allowing previously unreached levels of image resolution. In addition, Cypher AFMs can also can a rate, which is 10 to 100 x faster than other systems, meaning results can be accessed within minutes.
References and Further Reading
- Tire industry in boom cycle. Accessed 16/10/2018 from https://www.smithersrapra.com/resources/2017/april/tire-industry-in-boom-cycle
- Tire technology to drive future industry. K. Brown, Rubber & Plastics News. Accessed 16/10/2018 from:
http://www.rubbernews.com/article/20171009/NEWS/171009958/tire-technology-to-drive-future-industry
- Stretching Tires' Magic Triangle. A.H. Tullo, Chemical and Engineering News, 87(46), 10-14 (2009). Accessed from https://cen.acs.org/articles/87/i46/Stretching-TiresMagic-Triangle.html
- Extending the Magic Triangle. Accessed 16/10/2018 from http://www.rubber-silanes.com/product/rubber-silanes/en/effects/magic-triangle/
- Keep on Rolling! The Green Tire. Accessed 16/10/2018 from https://corporate.evonik.com/en/pages/article.aspx?articleId=1456
- Rubber composition and tire. T. Higa, K. Nakatani. US Patent Application, US20180117967A1 (2015). Accessed 16/10/2018 from
https://patents.google.com/patent/US20180117967A1/en
- The future is here. R. Evans, Tire Technology International, 26-32 (2017). Accessed from https://www.uakron.edu/
- Fast, High Resolution, and Wide Modulus Range Nanomechanical Mapping with Bimodal Tapping Mode. M. Kocun, A. Labuda, W. Meinhold, I. Revenko, R. Proksch, ACS Nano, 11(10), 10,097-10,105 (2017). https://doi.org/10.1021/acsnano.7b04530
- Bound rubber morphology and loss tangent properties of carbon-black-filled rubber compounds. D. Gabriel, A. Karbach, D. Drechsler, J. Gutmann, K. Graf, S. Kheirandish, Colloid Polymer Science, 294(3), 501-511, (2016). https://doi.org/10.1007/s00396-015-3802-6
- Enzymatic Functionalization of HMLS-Polyethylene Terephthalate Fabrics Improves the Adhesion to Rubber. S. Vecchiato, J. Ahrens, A. Pellis, D. Scaini, B. Mueller, E.H. Acero, G.M. Guebitz, ACS Sustainable Chemistry & Engineering, 5(8), 6456-6465, (2017). https://doi.org/10.1021/acssuschemeng.7b00475
- Morphological explanation of high tear resistance of EPDM/NR rubber blends. C. Gögelein, H.J.H Beelen, M. van Duinc, Soft Matter, 13(23), 4241-4251, (2017). https://doi.org/10.1039/c7sm00264e
- Morphology and nanomechanical characteristics of NR/SBR blends. D. Klat, A. Kępas-Suwara, J. Lacayo-Pineda, S. Cook, Rubber Chemistry and Technology, 10(5), 510, (2018). http://dx.doi.org/10.3390/polym10050510
- Cypher ES Polymer Edition AFM. Accessed 16/10/2018 from
https://afm.oxinst.com/products/cypher-afm-systems/cypher-es-polymer-edition-afm
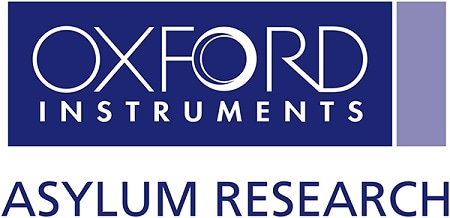
This information has been sourced, reviewed and adapted from materials provided by Asylum Research - An Oxford Instruments Company.
For more information on this source, please visit Asylum Research - An Oxford Instruments Company.