When encountering complex alignment applications, designers of precision motion systems typically have to endure an unsatisfactory compromise between force, dynamics, and accuracy.

A new hybrid approach can help resolve many of these concerns. Hybrid actuators bring together the optimal features of two distinct drive concepts into one high-performance, precision positioning system. There are a range of existing types, customized for different applications, including optical inspection, semiconductor manufacturing, aerospace, astronomy, and laser technology.
Hybrid Concept with Linear Voice Coil and Motor/Screw Drive
Over longer travel ranges, ball or roller screw drives offer high feed and holding forces. Friction in the drive screw and the linear guides limit linearity, resolution, and repeatability. Thus, by adding a voice coil motor in-line with the drive screw can ensure these limitations are circumvented. Operating without friction, voice coils can offer smooth motion, sub-nanometer resolution, and fast response. Travel ranges are ordinarily restricted to one inch and they require powering to hold a load.
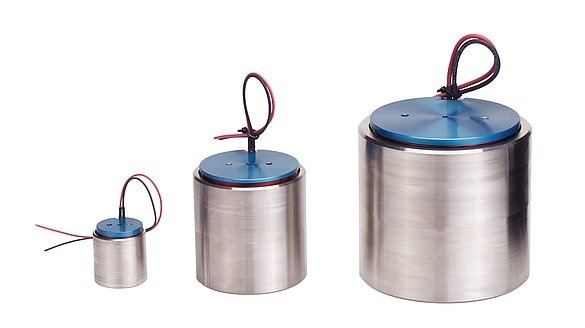
Custom voice coil motors
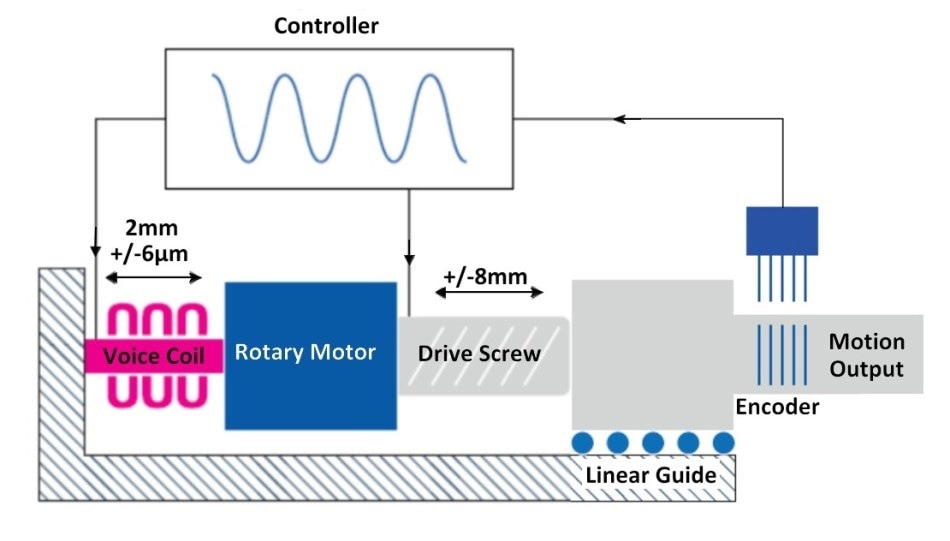
Hybrid concept with screw drive / rotary motor and voice coil linear actuator in line. Inherently soft the voice coil can supply a range of advantages with print-through of external disturbances. (Image PI) Functionality in both drives throughout series on a common position feedback signal, the voice coil can correct for all higher frequency error components such as those caused by cyclical errors, friction, and stick-slip effects.
Hybrid Linear Actuator Concept with PiezoWalk Linear Motor and Piezo Stack Actuator
Based on a combination of a PiezoWalk linear motor and an “analog” piezo actuator, an additional hybrid precision mechanism was developed and established for high-end semiconductor inspection applications.
A range of different piezo motor concepts is offered to stand up to the various requirements in terms of force, size, speed, and cost. The PiezoWalk® motor principle is significantly robust, as it gives precise linear motion to a runner by a succession of small steps (see animation).
Otherwise unlimited, travel ranges are only dependant on the length of the runner, and the motor is very stable, stiff and self-clamping, even when powered down. Incorporating a PICMA® piezo stack actuator in-line with the runner can enable high dynamics over different travel ranges. The stiff, monolithic piezo stack with efficient responsiveness in the millisecond range, or beyond, offers the requisite dynamics for high-speed focusing and scanning applications.
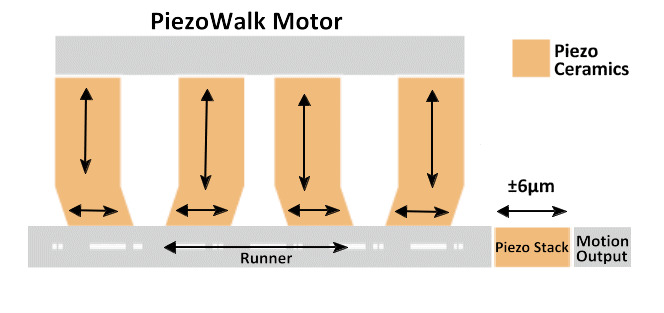
Hybrid concept with piezo walking drive and piezo actuator (Image: PI)
Operating Modes of High-Force Piezo-Walk Motor / Drive System, Nanometer Precision
Animation: PiezoWalk motor operating principle
Hybrid Concept with Piezo Stack and Motor/Screw Drive, Designed for the ELT Telescope
Based on a motor/screw drive and integrated piezo stack actuator, a closed-loop hybrid linear actuator was designed for the ELT telescope. PI engineers, meeting the expectations and requirements set by scientists and astronomers from the European Southern Observatory (ESO), developed a distinctive ultra-high precision, high-load actuator to align the mirror segments of what will be the largest terrestrial optical telescope on the planet.
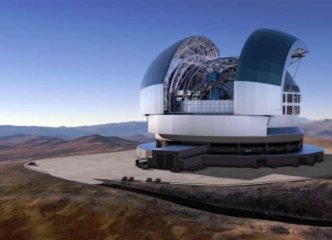
Artist rendering of the European Extremely Large Telescope (ELT), built on the 3,000-meter-high Cerro Amazones in the Atacama Desert in Chile. The ELT will be the largest terrestrial optical telescope for scientific evaluation of electromagnetic radiation in the visible and near-infrared wavelength range. (Image: ESO)
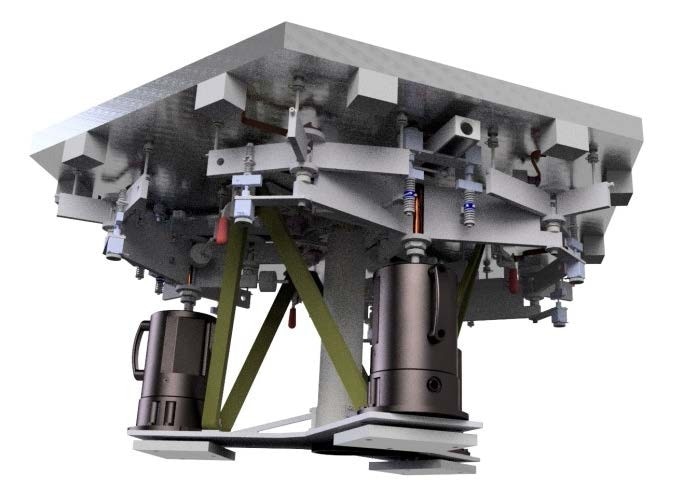
Concept of one Mirror Segment Subunit of the ELT primary mirror illustrating the 3 hybrid drives. (Image: ESO)
The telescope's breakthrough state-of-the-art design comprises of a 39m diameter primary mirror (M1) split into 798 independent mirror segments (segmenting is necessary due to it not being technically feasible to produce one mirror of that size). Each segment of the mirror weighs about 550 lbs and is put in place by three independent hybrid actuators in a tripod configuration, providing a max travel range of 10 mm and push force of 1050 N.
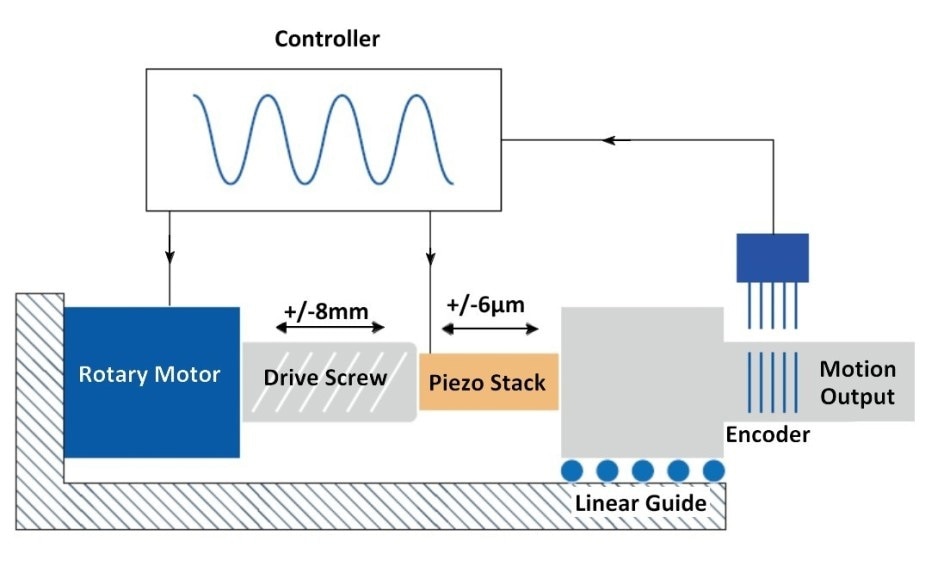
Schematic diagram of a hybrid linear actuator based on a motor/drive screw and piezo actuator. The common control with one single high-resolution linear encoder enables extremely smooth motion control with constant velocity and high precision positioning. The limited range of the piezo actuator is sufficient to counter for any of the inaccuracies of the drive screw over the full travel range (Image: PI)
Hybrid Linear Positioning Technology Used in ELT Telescope Actuator | PI
Animation: Hybrid Linear Slide with screw drive and piezo stack actuator positioned between the drive nut and the moving platform. A high resolution (sub-nanometer) linear scale offers position feedback to both two parallel control loop structures. (Image: PI)
For achieving the highest optical resolution expected from the new telescope design, it is necessary that all mirror segments need to remain aligned to <2 nanometers at all times. Aside from the superb accuracy and force, low energy consumption was another key requirement in the actuator design to reduce the negative effects of heat dissipation on the performance of the telescope.

Hybrid actuator prototype
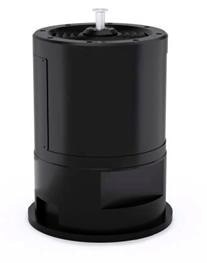
Final design of the hybrid position actuator (PACT) for the ELT. The dimensions are approx. 200mm diameter and 285 mm length. (Image: PI)
Controller and Position-Feedback Sensor for the Hybrid Drive System
Whereas in conventional coarse/fine systems, two independent mechanisms operate with independent-position sensors and controllers, the benefits of the unorthodox hybrid drive can only be acquired when a common controller and position feedback sensor are used. In this instance, a high-resolution optical linear encoder with 0.1 nm resolution per increment was chosen.
Operated by a brushless, high-torque motor, the drive screw works in tandem with a high-ratio, zero-play, reduction gearhead with a constant transmission ratio. The high transmission ratio enables the load to be held in place throughout, even when the motor is not powered (another step to ensure reduced power consumption).
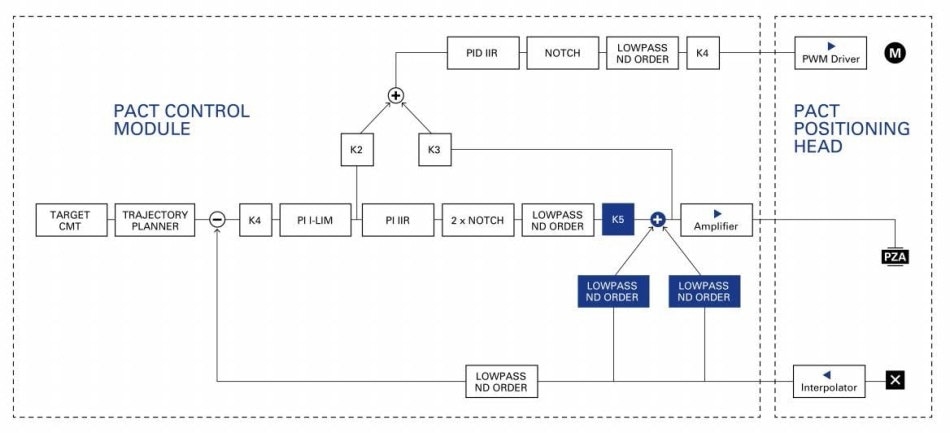
Hybrid controller structure. The motor voltage derives from the control voltage of the piezo actuator. The larger this voltage, the more-likely the motor will run at high-speed. When the piezo expands, the motor drives the screw in the same direction, supplementing the fine motion range of the piezo, automatically centering it in its positioning range as well. This offers the best error correction performance for both directions. (Image: PI)
Driving and simultaneously receiving feedback from the common position measuring system is achieved using a dedicated control module. The servo-algorithm is designed to view the brushless motor/screw and the piezo actuator as a single unit.
Beyond the realm of astronomy, application areas for hybrid precision actuators include microscopy, measuring technology, semiconductor manufacturing, surface inspection, and laser technology.
Traditional Piezo Actuators - Short Range Positioning with Sub-nanometer Accuracy, High Force, and Fast Response
Piezo actuators act by converting electrical charges into mechanical displacement and vice versa. Resolution is virtually unlimited due to the solid stage nature of this effect. Linear motion can be produced without conversion from rotation, with no friction involved. The piezo effect is both maintenance and wear-free. Standard piezo actuators provide travel ranges of 10 to a few 100 µm, but they are sufficient in transporting loads up to several tons with great accuracy.
Electrically, piezo actuators function as capacitive loads and require very little power in steady-state operation – but they can respond with high-speeds to a drive voltage change with increased times in the microsecond to millisecond range.
Furthermore, the lifetime of piezo actuators is encouraging. In a study, 100 billion cycles without failures were conducted by NASA/JPL using PICMA® multilayer actuators, before sending them to Mars on the Curiosity rover’s science lab.
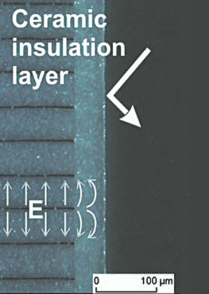
The ceramic insulation layer protects the active layers inside the piezo actuator from moisture.
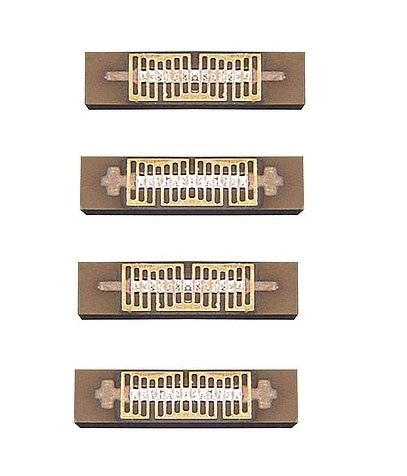
PICMA® monolithic multilayer piezo actuators are durable even under difficult operating conditions. (Image: PI)
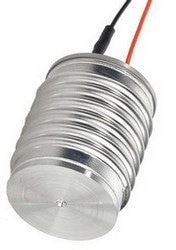
For additional protection, encapsulated PICMA® piezo actuator, embedded in a metal container with nitrogen filling. These types of actuators are used in the hybrid drive concept for the ELT. (Image: PI)
The active layers of PICMA® multilayer actuators consist of fine ceramic films encapsulated by an all-ceramic insulating layer that gives electrodes protection against humidity, thus greatly reducing the risk of failure caused by leakage currents. The monolithic piezoceramic block of an actuator like this can be depended on under the most extreme of ambient conditions and high temperature differences. Its success spans a range of applications, including life science, machining, aerospace, medical technology, and microscopy.
The piezo actuators used in the telescope hybrid actuator offer additional protection as they are embedded in sealed metal containers supplied with nitrogen in order to span 30 years of lifetime in the hostile ambient conditions in the Atacama Desert.
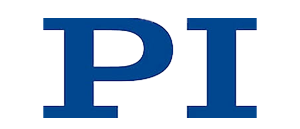
This information has been sourced, reviewed and adapted from materials provided by Physik Instrumente (PI) GmbH & Co KG.
For more information on this source, please visit Physik Instrumente (PI) GmbH & Co KG.