Industrial separation processes make up around 10-15% of the total energy consumption throughout the United States. A total of 49% of this energy consumption is devoted to distillation.1
Distillation and its related separation technologies are highly energy-intensive due to their reliance on a phase change to separate chemical components.
Membrane-based separation is a function of mass transport through boundary layers (Fick’s law) and solution-diffusion mechanics (Graham’s law), however, representing a very different approach to distillation.
The membrane functions as a thin barrier during membrane separation, selectively restricting target molecules in nanopores (Figure 1). This results in the accumulation of two distinct populations, including the desired pure phase.
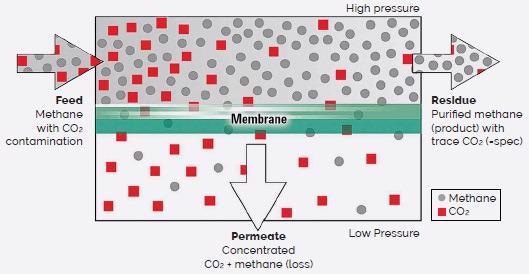
Figure 1. Schematic of a generalized gas separation membrane. (Adapted from ref. 2). Image Credit: Asylum Research - An Oxford Instruments Company
Membrane separation does not employ sorbents or require a thermal driving force, meaning that it requires 90% less energy than distillation.1
Membrane separation technology is widely used in common everyday applications for this reason, with common examples including drinking water filtration, wastewater treatment and food production.
Membrane separation has also been the subject of considerable research over the past decade, as teams throughout industry and academia work to expand its applicability to a more diverse range of separation processes.
One notable application lies in the separation and purification of gas mixtures.2 Membrane-based gas separation technology offers a number of advantages over conventional methods. These include:
- Ease of use
- Reduced energy consumption
- Mechanical simplicity
- Minimal infrastructure footprint
- A high degree of selectivity
- Good scalability potential
Organic (polymer-based) membranes currently make up the most significant segment of the membrane gas separation market.
This has been driven by an increasing focus on the separation and capture of greenhouse gases such as methane and carbon dioxide from landfill emissions, hydrogen recovery from ammonia purge, separation of natural gas components, and the separation of olefin-paraffin in crude oil refineries.
A membrane’s ability to successfully separate a gas mixture is dependent on its permeability and selectivity, both of which are closely linked to the membrane’s pore size and distribution.
It is, therefore, essential that researchers have the ability to accurately characterize pore parameters in order to support performance enhancements and future designs.
Electron microscopy (EM) is a frequently employed method in the investigation of pore parameters, but these techniques necessitate sophisticated sample preparation steps, which could disturb the sample’s native structure.
Image acquisition must take place at low vacuum, meaning that this method is not suitable for experiments with hydrated samples.
It is possible to image hydrated samples using X-Ray diffraction methods, but output data from these methods tends to be in the form of time-averaged spectra unable to truly capture dynamic membrane processes.
Atomic force microscopy (AFM) represents a viable and useful alternative to EM. Technological developments in atomic force microscopy have seen advanced AFMs able to achieve a comparable spatial resolution to even high-resolution electron microscopes.
AFM also offers a range of practical advantages over EM. Most notably, AFMs can be used under ambient conditions, meaning that no vacuum environment is required. AFM imaging can also be undertaken in liquid, a strict requirement when looking to understand membrane morphology.
AFM can be employed in the characterization of mechanical properties such as storage and loss moduli at nanoscale resolution.
Oxford Instruments Asylum Research AFMs - including the Cypher™ ES - are especially suitable for membrane research experiments as these robust instruments can offer high-speed image acquisition, atomic-level spatial resolution and the ability to precisely control the local environment.
This article explores the key features of the Cypher AFM platform and highlights its contribution to membrane gas separation research.
Modulating PCP Membrane Properties with Guest Molecule Interactions
Membranes are fabricated from a wide range of materials, resulting in an array of highly variable membrane architectures. For example, organosilicate membranes are structurally heterogenous, while porous coordinating polymers (PCPs) form crystalline membranes.
AFM can be employed in investigations into the membrane-gas/liquid interface independent of membrane structure. Researchers from Kyoto University recently reported using (Zn2(1,4-ndc)2(dabco))n to generate a porous coordinating polymer membrane.3,4
This PCP membrane is a crystalline material exhibiting a 3D structure arising from 2D square-grid layers of (Zn(1,4-ndc))n that are separated by pillars of dabco.
The researchers used an Asylum Research Cypher ES AFM to characterize the membrane-liquid interface. This instrument was equipped with a perfusion cell and operated in tapping mode (Figure 2A) with blueDrive™ photothermal cantilever excitation.
Asylum’s exclusive blueDrive technology makes use of a pulse-modulated laser to excite the cantilever on resonance, enabling the mechanical decoupling of cantilever excitation from cantilever motion.
By using the blueDrive technology, users are able to leverage superior force control compared to traditional piezoacoustic drives – particularly working with liquid environments.
Researchers can, therefore, utilize lower imaging amplitudes, generally a few nanometers or less, helping to ensure ultra-high-resolution, preserve tip sharpness and prevent sample damage.
The resulting images from this work highlight the presence of topographical features spanning several orders of magnitude. Figure 2B shows images of the {0,0,1} crystal face at a scan size of 1 µm, displaying a series of defect-free micrometer-wide terraces with ~1 nm step heights.
The tetragonal 2D lattice becomes visible at a scan size of 30 nm (Figure 2C). It is possible to assign topographical highpoints (~80 pm) to dabco and/or water molecules coordinating with free zinc ions.
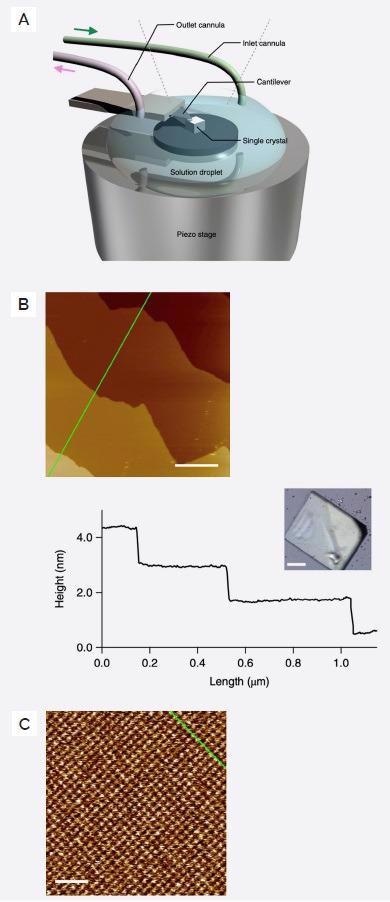
Figure 2. Cypher ES Sample environment and associated images. A) Single Crystal PCP immersed in liquid using a Cypher ES perfusion cell. B) Topographic image of {0,0,1} crystal face (inset to the right) imaged in DMF at 19.5 Hz line scan rate. Line profile to the right shows 1 nm terrace step heights. Scale bar is 250 nm. C) Atomic resolution image on a single terrace showing atomic lattice. Scale bar is 5 nm. (Adapted from ref. 4). Image Credit: Asylum Research - An Oxford Instruments Company
The application of a 2D fast Fourier transform to the topography image enabled the calculation of lattice parameters for the a-b plane. This calculation yielded a=b=11.2 Å, which is in good agreement with bulk crystal parameters measured using powder X-Ray diffraction.
Atomic level resolution is achievable thanks to the Cypher AFM’s advanced mechanical design. This design ensures maximum stiffness of the mechanical loop connecting the probe and sample, affording the instrument an industry-leading low noise floor that is half the noise floor of many other AFMs.
This experiment also required the imaging of the chemically aggressive solvent dimethylformamide (DMF). This was possible due to the environmental cell of the Cypher ES, constructed from chemically inert PEEK components, which are compatible with a wide range of solvents.
PCP membranes have been reported as having the ability to adapt their crystal structure in response to external stimuli. This is a key factor in the ability to adjust membrane selectivity by changing the porous architecture.
DMF containing biphenyl (BP) was introduced as a guest molecule into the perfusion cell at a constant flow rate of 60-70 μl/minute in order to track lattice rearrangement in situ.
This process involved the continuous acquisition of high-speed topography images - every ~13 seconds (line scan rate ~20 Hz) while simultaneously increasing BP concentration. Approximately 140 images were acquired over the course of the experiment.
Lattice dimensions and vector angle (γ) were calculated using a 2D autocorrelation function. In the absence of BP, γ=89.6° - a result which corresponded to the tetragonal lattice shown in Figure 3A (Top).
The use of high-speed in situ imaging allowed the researchers to capture a lattice transition from tetragonal to rhombic (Figure 3A, Bottom). This transition corresponds to a monotonic decrease in γ with increasing BP (Figure 3B).
The maximum concentration of BP applied was kept at 500 mM due to the solubility limits of BP in DMF. Once the guest BP had been removed, the lattice structure was reverted back to the original tetragonal orientation (Figure 3B).
![Lattice architecture of PCP membranes. A) Representative 30×30 nm topography scans (left) and associated 2D auto-correlation function (ACF) showing lattice parameters. Top is [BP] =0 mM, bottom is [BP] = 500 mM. B) ? vs. time, where ? is calculated from a 2D ACF from each topography image.](https://d1otjdv2bf0507.cloudfront.net/images/Article_Images/ImageForArticle_5993_4466231329927086469.jpg)
Figure 3. Lattice architecture of PCP membranes. A) Representative 30×30 nm topography scans (left) and associated 2D auto-correlation function (ACF) showing lattice parameters. Top is [BP] =0 mM, bottom is [BP] = 500 mM. B) γ vs. time, where γ is calculated from a 2D ACF from each topography image. (Adapted from ref. 4). Image Credit: Asylum Research - An Oxford Instruments Company
It was also noted that the rhombic lattice was not observable in powder XRD experiments, likely because these are primarily bulk measurements, and the AFM interrogates the solid-liquid interface and not the bulk.
This, therefore, suggested that the tetragonal to rhombic reorientation is confined to the interface – a finding which the researchers attributed to solvation variations between the surface and bulk.
Control of Membrane Selectivity via Photopatterning of Reactive Polymer Film
Membrane permeability and selectivity can be adjusted and optimized via the control of membrane pore characteristics such as size and distribution. The previous example highlighted efforts to modulate the membrane crystal structure to impact pore dimensionality.
Crystalline membranes can provide predictability and useful control over pore size, but they pose distinct challenges in terms of scaling, brittleness and susceptibility to damage.5
Polymer membranes represent an appealing alternative due to their durability and relative simplicity of manufacturing.
New developments in polymer manufacturing have significantly increased their scalability, with improvements and variability in mechanical properties now more feasible than ever before.
An associated lack of control remains over the size, distribution and orientation of specific structural elements within heterogenous polymer materials, however.
Researchers at the University of Colorado, Boulder, have been working to address this need to control specific structural elements in gas-separation membranes. Their goal was to develop an improved understanding of the impact of membrane heterogeneity on gas permeation properties.
The research developed an approach utilizing a single polymer containing a combination of thiols and excess acrylate groups that could be cross-linked in two stages.
During stage one, this novel two-stage reactive polymer (TSRP) employs a base catalyst to cross-link the thiols with the acrylates to produce a soft rubber. UV light exposure is used to generate nascent cross-links, further stiffening the material during stage two (Figure 4A).
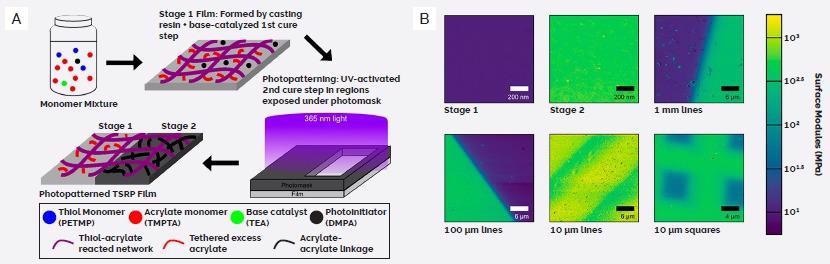
Figure 4. Two stage reactive polymers (TSRP). A) Schematic of TSRP membrane fabrication. B) Modulus maps of patterned TSRP films generated using FFM on a Cypher AFM. (Adapted from ref. 5). Image Credit: Asylum Research - An Oxford Instruments Company
Implementing photomasks during stage two enabled the patterning of various films of TSRP with 1 mm to 10 µm gratings and 10 µm squares. AFM was then used to characterize any resulting patterns and the interface between structural features.
This process saw AFM nanomechanical property characterization performed using an Asylum Research Cypher AFM working in Fast Force Mapping (FFM) mode. FFM has been specifically developed to eliminate the slow acquisition and low spatial resolution commonly associated with AFM force-mapping techniques.
FFM is capable of performing force mapping at a pixel rate of up to 2500 Hz pixel compared to a pixel rate of ~1 Hz for conventional force mapping.
Driving the tip in a continuous sinusoidal motion from pixel to pixel allows the acquisition of a 2D array of force curves in mere minutes.
These force curves provide useful mechanical information such as modulus, which can be extracted by fitting the force-distance indentation data to compatible contact mechanics models, including Johnson-Kendal-Roberts (JKR), Hertz and Oliver-Pharr.
Unlike other AFMs’ FFM modes - which are designed to calculate modulus during imaging and discard the raw force curve data - the Asylum FFM mode consistently captures this data for each individual pixel.
This more in-depth approach allows users to experiment with different models and select the one best suited to the sample.
The Asylum FFM mode ensures higher accuracy by capturing both cantilever deflection and Z sensor data. This is notably different from other implementations, which rely on an open-loop (calculated) estimate of the tip-sample separation.
FFM images of the TSRP films highlight the patterned structures that had initially been revealed in the modulus data. Unpatterned films which had only been cured to stage one were found to measure approximately 10 MPa (Figure 4B).
Regions of patterned films which had been covered by the photomask – and were therefore only exposed to stage one curing – were also found to have similar modulus (Figure 4B).
Unpatterned films exposed to UV-light as part of stage two curing were determined to possess a far higher modulus of ~600 MPa, which was found to correspond to the unmasked regions of the patterned films that were exposed to UV-light.
These observations were found to be dependent on the patterns’ scale with larger 100 µm and 1 mm patterns exhibiting both the strongest modulus gradient and presenting with regions which most closely compared to the moduli of the uniform films.
Patterned films complete with 10 µm features were notably stiffer in masked regions versus their pure stage one film values. Regions under the photomask were determined to be 170 MPa for lines and 50 MPa for squares.
These observations were believed to be related to imperfect photomasks that had allowed light to be scattered by the small features, resulting in increased free radical diffusion and acrylate cross-linking – a phenomenon found in even nominally masked regions.
TSRPs have been shown to provide a facile means of producing patterns with a range of stiffnesses.
Based on this determination, the researchers investigated whether these material modifications had a positive impact on gas permeation properties. As anticipated, the fully cured (stage two) film exhibited lower permeability than the film that had only been cured to stage one.
The designs and scales of the patterns were both found to affect the measured permeability of patterned films. It was noted, however, that the predicted permeability (calculated using an averaged composite model) had deviated from measured values as pattern size decreased.
AFM measurements that supported the identification of imperfect photomask patterning and higher-than-expected cross-link densities provided some indication as to the reason for this lower permeability.
It was also noted, however, that 10 µm squares diverged from this trend. These were less stiff than the 10 µm line pattern while still producing a membrane with 78% lower permeability.
It was necessary to develop a better model for spatial averages to resolve this discrepancy. To this end, a series of unpatterned partial stage two cured films were fabricated before being subjected to CO2 permeability tests and AFM modulus mapping.
Higher cross-linking density (longer UV exposure) was found to lead to higher modulus and decreased permeability.
This data enabled the development of a power law function relating permeation to elastic modulus, therefore allowing the researchers to convert their existing modulus maps to predicted permeability maps (Figure 5A).
Predicted permeation was found to provide excellent agreement with the measured values in every sample other than the 10 µm squares, which demonstrated a 4× lower measured value versus the prediction (Figure 5B).
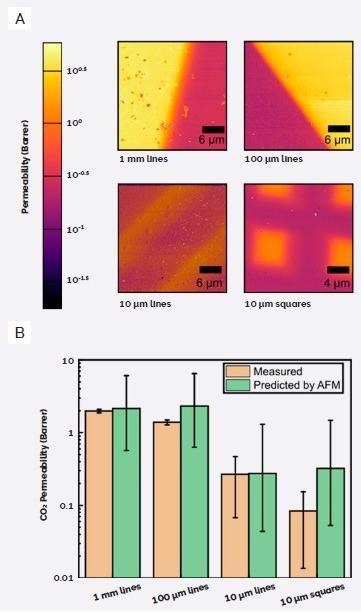
Figure 5. Using AFM for permeability prediction. A) Permeability maps generated from AFM modulus maps. B) Comparison of measured CO2 permeability vs permeability predicted from AFM modulus maps. (Adapted from ref. 5). Image Credit: Asylum Research - An Oxford Instruments Company
These findings indicated that the membrane cross-linking alone might not be entirely adequate in predicting membrane permeability.
Previous work in this area implied a significant decrease in gas diffusion through polymer materials, resulting from confinement effects that occur in line with shrinking feature dimensions.6
These findings could further support this theory since the AFM-dependent permeability maps confirm notable decreases in permeability between 1D lines and 2D squares.
Despite this unanticipated result, photopatterning of TSRP membranes has been verified to be a viable option for modulating permeability via locally-induced structural changes.
This study also highlights the power of AFM as a means of predicting variations in local permeability related to mechanical properties.
This method provides a facile and more environmentally friendly alternative to conventional membrane fabrication while highlighting the potential of TSRPs to provide a promising future for gas membrane applications.
Plasma Treatment as a Scalable Approach to Green Membrane Fabrication
The global shift towards clean energy is drawing considerable attention to the potential of hydrogen as an energy carrier. Hydrogen production processes often emit CO2 as a by-product, however, largely canceling out its related clean energy benefits.
Industry-leading CO2 capture technologies such as the Selexol process could increase the cost of hydrogen by up to 30%, meaning there is a significant unmet need for an environmentally-friendly, cost-effective means of carbon capture.
The industry is, unfortunately, struggling to produce commercial-scale membranes suitable for H2/CO2 separation.
A team led by researchers from the University at Buffalo has been working to address this issue using mixed material membranes comprised of polymer and advanced inorganic substituents.7
They have been able to develop a thin-film composite (TFC) membrane comprised of a few-nanometer thick silica film attached to a micron thick polydimethylsiloxane (PDMS) layer that has been deposited onto a stainless-steel mesh coated with porous polybenzimidazole (PBI).
They refer to this membrane as “POSi” - polymeric organosilica (Figure 6A).
Conventional silica membranes are created from organic percussors. Their production requires processing at temperatures of 400 °C and over, making this process highly energy inefficient and expensive.
POSi membranes, in contrast, are generated via oxygen plasma treatment of PDMS at ambient temperatures.
Oxygen plasma is able to degrade organic bonds, meaning it can remove carbon and hydrogen to leave behind silicon bonded to 3 and 4 carbons. This process results in the production of a dense layer of organosilica on top of the remaining PDMS layer.
PDMS is a versatile elastomer with readily tunable mechanical properties, particularly prior to curing. However, it has not thus far been possible to characterize the effect of oxygen plasma treatments on PDMS.
The group performed a comprehensive nanomechanical investigation of the organosilicate layer. This was done using FFM on an Asylum Research Cypher AFM, highlighting that PDMS exposed to 120 seconds of plasma treatment (POSi120) returned a measured modulus value of ~22 MPa.
This represented a 10× increase over pristine A PDMS (2.5 MPa) (Figure 6B and Figure 6C).
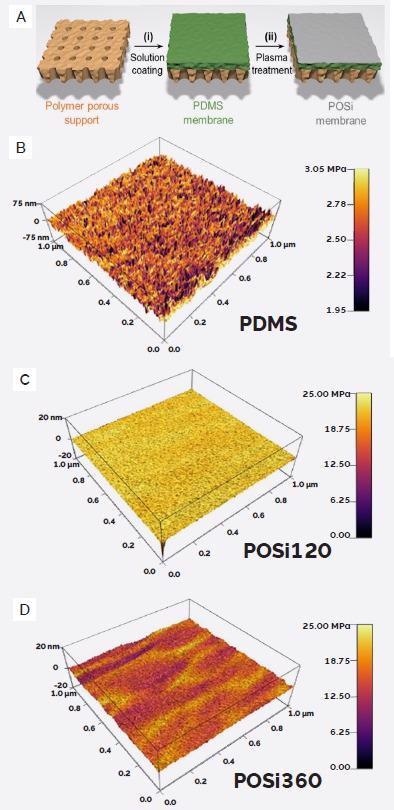
Figure 6. Polymeric organosilica membranes. A) Schematic of membrane manufacturing process. B-D) AFM topography images (Z-axis) overlayed with AFM modulus map (color scale). (Adapted from ref. 7). Image Credit: Asylum Research - An Oxford Instruments Company
It was also determined that an extended exposure time of 360 seconds (POSi360) led to samples exhibiting a range of stiffnesses from 10 to 25 MPa. This was determined to be caused by plasma-induced surface damage (Figure 6D).
It is evident that the POSi process has a significant impact on the membrane’s mechanical properties, prompting the researchers to further characterize the membrane’s functional performance.
It was determined that the POSi120 membrane exhibited H2 permeance of 144 GPU (gas permeation units) as well as H2/CO2 selectivity of 61 at 150 °C.
Pristine PDMS was found to achieve an H2/CO2 selectivity of just 0.25 under similar conditions, but this did exhibit an H2 permeability of ~5000 GPU, suggesting minimal gaseous resistance in PDMS compared to organosilica.
These results provide good indication that it is possible to tune and balance permeance and selectivity by adjusting plasma processing conditions.
Most notably, POSi120 was found to outperform other state-of-the-art polymeric membranes while offering comparable performance to inorganic membranes in terms of the separation of H2 from CO2 (Figure 7A and Figure 7B).
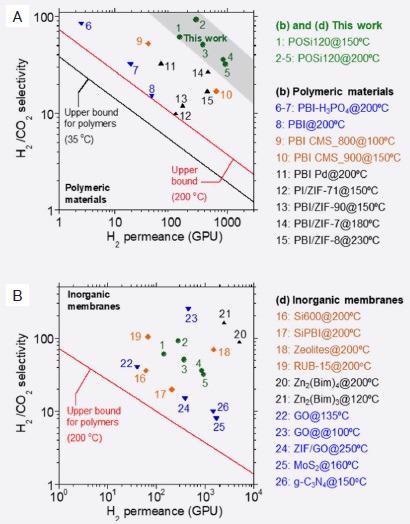
Figure 7. Comparison of H2/CO2 separation performance of POSi120 with A) other polymeric materials and B) Inorganic membranes. (Adapted from ref. 7). Image Credit: Asylum Research - An Oxford Instruments Company
POSi membranes can be produced from comparatively inexpensive polymers manufactured via a low-energy process, imparting considerable economic benefits while ensuring excellent gas selectivity.
Conclusion
The availability of improved gas separation technology is expected to be the key to more affordable, efficient and cleaner energy production.
In order to achieve this vital developmental endpoint, researchers must be provided with optimal tools to accurately characterize membrane parameters, including mechanical properties, pore size and pore distribution.
AFMs from Asylum Research are able to provide the required spatial and temporal resolution for this important task.
These instruments also offer highly sensitive quantitative nanomechanical measurements suitable for the precise measurement of even the smallest changes in membrane parameters.
References
- Oak Ridge National Laboratory. (2005). Materials for Separation Technologies: Energy and Emission Reduction Opportunities. https://doi. org/10.2172/1218755
- Valappil, R. S. K., Ghasem, N., & Al-Marzouqi, M. (2021). Current and future trends in polymer membrane-based gas separation technology: A comprehensive review. Journal of Industrial and Engineering Chemistry, 98, 103-129.
- Hosono, N. (2021). Design of Porous Coordination Materials with Dynamic Properties. Bulletin of the Chemical Society of Japan, 94(1), 60-69.
- Hosono, N., Terashima, A., Kusaka, S., Matsuda, R., & Kitagawa, S. (2019). Highly responsive nature of porous coordination polymer surfaces imaged by in situ atomic force microscopy. Nature chemistry, 11(2), 109-116.
- Blevins, A. K., Cox, L. M., Hu, L., Drisko, J. A., Lin, H., Bowman, C. N., ... & Ding, Y. (2020). Spatially Controlled Permeability and Stiffness in Photopatterned Two-Stage Reactive Polymer Films for Enhanced CO2 Barrier and Mechanical Toughness. Macromolecules, 54(1), 44-52.
- Kinning, D. J., Thomas, E. L., & Ottino, J. M. (1987). Effect of morphology on the transport of gases in block copolymers. Macromolecules, 20(5), 1129-1133.
- Zhu, L., Huang, L., Venna, S. R., Blevins, A., Ding, Y., Hopkinson, D., ... & Lin, H. Scalable Polymeric Few-Nanometer Organosilica Membranes for Pre-Combustion CO2 Capture. https://papers.ssrn.com/sol3/papers.cfm?abstract_id=3778364
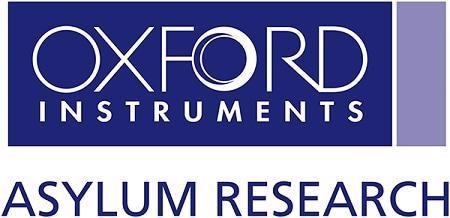
This information has been sourced, reviewed and adapted from materials provided by Asylum Research - An Oxford Instruments Company.
For more information on this source, please visit Asylum Research - An Oxford Instruments Company.