Batteries are widely used power sources that utilize electrochemical cells for powering various devices. Battery performance is impacted by intrinsic mechanisms of battery failure and degradation, which depend on the electrochemical and nanomechanical interactions of the constituent materials.
Tremendous efforts have been made in industry towards the next generation high energy density and high C-rate batteries, where new materials, manufacturing processes and integrations are considered in order to optimize battery performance across a wider temperature range[1]. To improve yield rates and scale manufacturing growth, it is crucial to understand batteries’ failure and its corresponding root cause. Typical battery failure modes fall into the categories of mechanical failure, thermal failure and electrical failure.
Battery Cell Manufacturing
A typical battery manufacturing process includes the electrode manufacturing, mixing, coating, calendaring, slitting, electrode making, stacking and packing, as shown in Figure 1. Throughout the process, nanoindentation techniques can be used for any of the following measurements:
- Compressive strength of cathode slurry particles (1-10μm)
- Complex modulus of binder materials
- Indentation hardness and modulus of the composite cathode coating
- Indentation hardness and modulus of the solid electrolyte
- Indentation hardness and modulus of the anode coating
- Fracture toughness and indentation cracking of stacked layers
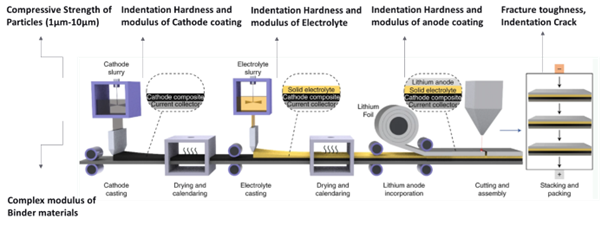
Figure 1. Schematic of large-scale manufacturing of ASSBs. Polymer and solid electrolyte composites allow for good mechanical processability as well as decreased separator thickness layers to increase cell-level energy density. Image credit: Tan et al. [2]
Nanoindentation techniques enable battery studies on micro-length scales, where nanomechanical properties are evaluated on both the electrode and particle level. For instance, these techniques accomplish the following:
- Facilitate the investigation of emerging battery materials behavior on the length scale of defects and failure mechanisms by offering indentation hardness, modulus, quantification of fracture toughness, etc.
- Boost battery reliability evaluation after cyclic charging and discharging to prevent failure.
- Enhance the battery thermal safety and thermal management by optimizing the components/materials performance at wider temperature ranges.
Measurement of Cathode Load Response
Many test methods are available for the KLA Instruments™ nanoindentation systems. To apply a mechanical load to a commercially-available composite graphite on copper foil on glass, a test method was developed that controlled actuation, sensing, data acquisition, parameter calculation and presentation of results. Figure 2 (left) shows the measured elastic modulus as a function of depth, with a SEM image of the LiNiCoMnO2 surface. Figure 2 (right) shows the measured hardness of the cathode layer as a function of depth, with a schematic of the actuator. Different testing modes are available to accommodate significant surface roughness.
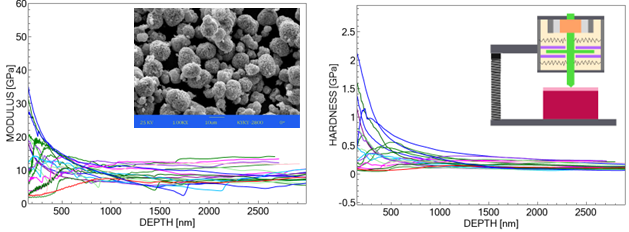
Figure 2. Cathode material modulus (left) and hardness (right) as a function of indentation penetration depth, with a SEM image of the LiNiCoMnO2 surface and the KLA actuator schematic. Image credit: KLA Instruments™
High Speed Nanomechanical Mapping of Composite Electrodes
Nanomechanical properties on a surface can be mapped using NanoBlitz 3D or Express Test, where an array of indents is specified to measure the properties at 1s per data point. Figure 3 shows the modulus and hardness maps of a lithium-ion battery electrode, composed of a mixture of active particles (LiMn2O4) and carbon black in a polymeric matrix of polyvinylidene fluoride (PVDF). The use of Express Test nanoindentation testing is extremely useful to identify the single-phase mechanical properties and their spatial distribution in lithium/polymer battery composites.
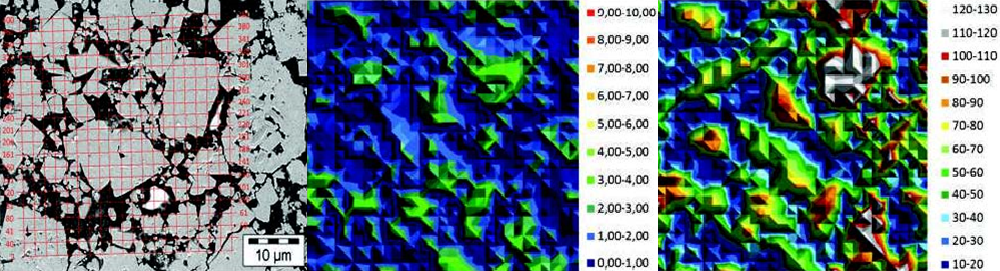
Figure 3. Nanoindentation elastic modulus and hardness mapping on a lithium/polymer battery composite. Image Credit: KLA Instruments™
In-Situ Compression Testing on Individual Particles
The often-seen cracking of particles during manufacturing leads to detrimental side reactions. KLA Instruments InSEM® in situ nanoindentation system enables the in situ observation of particle cracking and measurement of compressive strength of particles and mechanical properties of composite coatings. Figure 4 shows an InSEM video image prior to (top left) and following (top right) particle crush measurement, with the corresponding load-compression response of particles (bottom left) and rupture stress (bottom right).
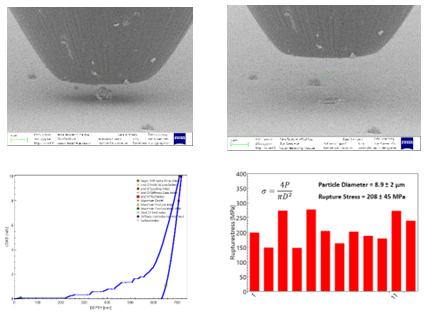
Figure 4. Synchronized particle compression test data and SEM video with calculated rupture stress. Image credit: Toyo Corporation
Measurement of Viscoelastic Properties of Binders
The KLA Instruments ProbeDMATM technique can be used to perform local dynamic mechanical analysis (DMA) testing on binder materials. ProbeDMA has the advantage of quantifying local mechanical properties by targeting specific surface locations with the nanoindenter. Figure 5 compares the measured storage modulus of binder materials under dry and wet conditions, where data was collected at a fixed frequency of 10Hz.
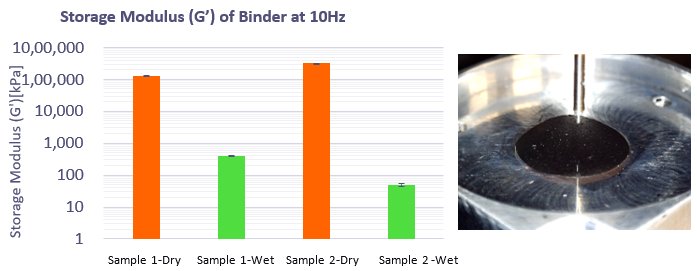
Figure 5. Storage modulus of the binder under dry and wet conditions (left). Nanoindentation measurement in electrolyte solution (right). Image credit: Toyo Corporation
Alternative Battery Materials Testing Environments
Although nanoindentation experiments are typically performed under ambient conditions, some battery materials require nanomechanical testing on liquids or at elevated temperatures that may be best carried out inside a glove box. The KLA Instruments iMicro and iNano® systems are well-suited to these environments due to their compact size. Figure 6 shows a glove box setup enclosing a Nano Indenter® G200 system for testing in an electrolyte fluid cell, where the glove box can be backfilled with argon gas to evaluate nanomechanical properties under argon and fluid environments.
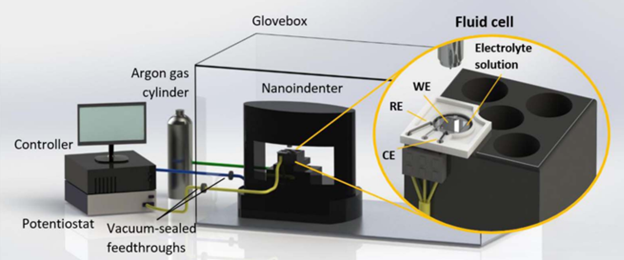
Figure 6. Example of a glove box environment for the Nano Indenter® G200 system, used to measure load response under argon and fluid environments. Image credit: Scalco de Vansconcelos et al.[3]
The Versatility and Importance of Nanoindentation to Battery Materials Manufacturing and Research
Battery cell manufacturing includes multiple process steps that affect layer uniformity and interface adhesion. Battery materials research comprises a wide array of applications and environments to test material behavior and performance, under ambient, fluid, gas, and vacuum conditions. If you are interested in learning more about how KLA Instruments nanoindentation can deliver critical nanomechanical behavior data for your battery materials research or manufacturing, please visit our website or contact us today.
[1] Fan et al., "Tailoring inorganic-polymer composites for the mass production of solid-state batteries," Nat. Rev. Mater. 6, 1003-1019 (2021).
[2] Tan et al., "From nanoscale interface characterization to sustainable energy storage using all-solid-state batteries," Nature Nanotechnology 15, 1070-180 (2020).
[3] Scalco de Vasconcelos et al., "Operando nanoindentation: a new platform to measure the mechanical properties of electrodes during electrochemical reactions," Journal of the Electrochecmical Society 164 (14), A3840-A3847 (2017).
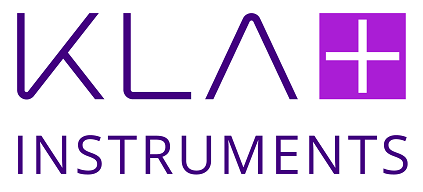
This information has been sourced, reviewed and adapted from materials provided by KLA Instruments™.
For more information on this source, please visit KLA Instruments™.