Engineers Jonas Reiser and Mathias Winter provide insights into PI's surface-shaping solutions for the future.
“We have created a hybrid solution with smart actuator arrays to cover demands for surface control and structuring of tomorrow.”
Technology Leadership Interview: The Future of Nanometer Precise Surface Shaping | PI
Technology Leadership Interview: The Future of Nanometer Precise Surface Shaping. Video Credit: PI (Physik Instrumente) LP
Programmable Ceramic Spacers and Shims
PIRest, a technology, best described as programmable piezo shims, can maintain position without power, and adjust thickness in increments on the nanometer scale and below. The combination of PIRest with common piezoelectric actuator technologies in smart arrays can address the precision adaptive surfaces requirements of the future.
Precision Requirements in Next-Generation Semiconductor and Optics Applications
Semiconductor and optics applications, e.g. on mirrors for astronomy, demand high precision surface quality. Engineers in the semiconductor industry are looking for smaller actuator pitches and better process parameter control.
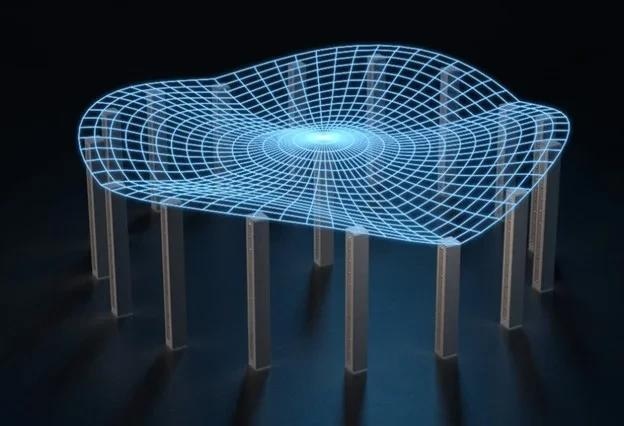
Active surface shaping with piezoelectric actuators. Image Credit: PI (Physik Instrumente) LP
Dynamic Compensation of Local Changes on Substrate Surfaces
Many applications benefit from solutions that dynamically compensate for local substrate changes caused by heat or inaccuracies. Adaptive optics corrections for dynamic and quasi-static imaging errors are also essential.
Semi-active piezo actuator elements, rooted in the patented PIRest technology, can maintain a programmed position without the need for continous power.
Combining Active and Semi-Active Actuators
Bringing together active and semi-active actuator components in a single solution assists in dynamically shaping surfaces. It also allows for the correction of static changes caused by factors like aging or drifting, without requiring a continuous power supply to the actuators.
Using piezoelectric actuators enables achieving nanometer and sub-nanometer precision, with possible travel ranges from less than one micron to tens of microns.
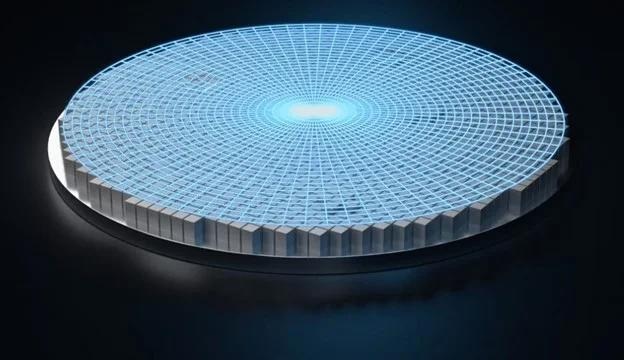
A large piezo actuator array for controlled precision surface deformation. Image Credit: PI (Physik Instrumente) LP
The challenge is to find an innovative actuator array and drive concepts capable of managing several thousand piezo actuators, while finely adjusting them with nanometer precision.
A simulation tool is in development to virtually test various connection and drive concepts, streamlining and hastening the development process.
PI's goals involve seeking novel projects and collaborating closely with its customers. It also aims to expand the achievable boundaries and advance precision in its technologies.
Active Surface-Shaping in Brief
- Flexible Actuator Design: Combining active, semi-active, or hybrid piezo actuator technologies with diverse designs accommodates specific stroke, force, or resolution requirements.
- Flexible in Operation: Employing dynamic, quasi-static, and mixed operation allows the generation of different amplitudes while minimizing position noise.
- Flexible in Shape: Arranging actuators or actuator arrays variably facilitates different deformations with superior resolution. Implementing smart wiring, drive, and sensor concepts simplifies the hardware setup.
- Flexible in Feature Size: Using structured composition in piezo ceramic material ensures maximum operational flexibility and shaping of the smallest features.
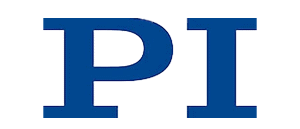
This information has been sourced, reviewed and adapted from materials provided by PI (Physik Instrumente) LP.
For more information on this source, please visit PI (Physik Instrumente) LP.