Sponsored by Park SystemsReviewed by Olivia FrostJun 17 2025
Polymer materials play an increasingly important role in a variety of industrial applications, thanks to their distinct physical and chemical properties. Among their key mechanical characteristics, Young’s modulus stands out as a critical measure of stiffness or rigidity.1
Temperature changes can significantly influence the mechanical behavior of polymers.2 As temperature rises, Young’s modulus typically decreases, resulting in greater flexibility and reduced stiffness. This is due to the increased thermal energy, which allows polymer chains to move more freely and reduces their resistance to stress-induced deformation.3-5
Understanding how a polymer’s mechanical properties vary with temperature is essential for designing materials that can perform reliably under different environmental conditions.
In this study, Atomic Force Microscopy (AFM) was used to examine how temperature affects the mechanical properties of polymer materials, with a focus on Young’s modulus. The PinPoint™ nanomechanical mode was used to map localized regions of the polymer surface and calculate the average Young’s modulus.
To monitor how this property changed with temperature, a temperature-controlled stage (TCS) was integrated into the AFM system, allowing measurements as the temperature increased from room temperature (RT, 25 °C) to 170 °C.
AFM and TCS
The FX40, a recently introduced AFM model by Park Systems, was used for these measurements. Designed specifically for research applications, the FX40 is a high-performance system suited for a wide range of fields including nanotechnology, materials science, life science, and semiconductor research.
This model offers advanced capabilities such as high-resolution imaging and a comprehensive selection of imaging modes. It also features a high-precision motorized stage, enabling accurate sample positioning and scanning.
To support temperature-dependent measurements, Park Systems provides temperature-controlled stages (TCS) that can be integrated with their AFM systems. Three TCS types are available, each offering different temperature ranges, stage sizes, and hardware configurations.
TCS Type 1 features rapid temperature changes enabled by active heating and cooling. While TCS Types 2 and 3 also allow for fast heating via active mechanisms, cooling is achieved passively and thus may take more time (Figure 1). Depending on the model, TCS units can operate within a temperature range of -20 °C to 600 °C. For this study, Type 1 was used, which supports temperature settings from -20 °C to 170 °C.
Source: Park Systems
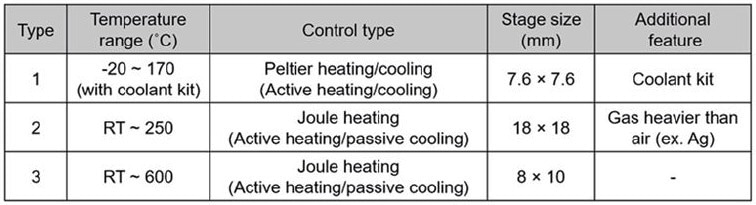
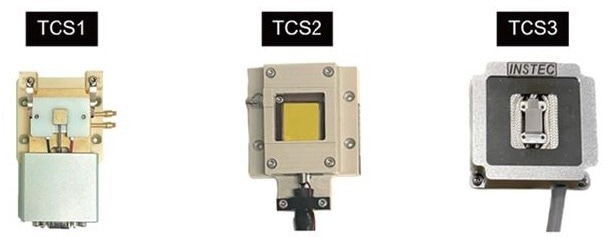
Figure 1. Three types of TCS modules of Park Systems. Image Credit: Park Systems
Results
Initially, changes in the surfaces of polyurethane and collagen films in response to temperature variations were evaluated using Non-contact mode and Tapping mode, respectively.
As shown in Figure 2a, temperature fluctuations affect the surface morphology of polyurethane. The surface appears smooth at room temperature but becomes increasingly rough as the temperature rises.
At elevated temperatures, polyurethane undergoes a transition from a crystalline to an amorphous state, or may shift between different crystalline structures. These transitions can alter the material’s crystalline morphology, leading to a reduction in crystallinity or changes in crystal size and arrangement.6
Collagen, a temperature-sensitive material, also exhibits significant structural changes with temperature variation. Figure 2b illustrates that at higher temperatures, the collagen film undergoes denaturation, resulting in changes to its structure, surface morphology, and phase behavior.
This denaturation compromises the collagen’s structural integrity, producing a rougher and more irregular surface.7
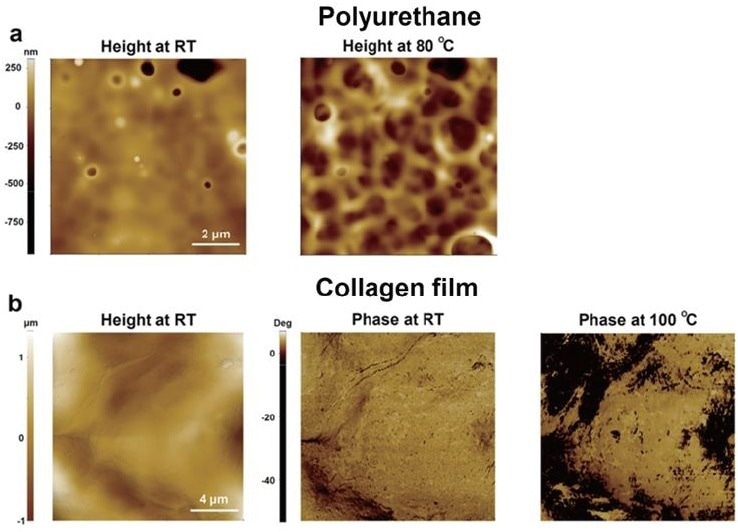
Figure 2. Topographical comparison of materials according to temperature change. Height images of polyurethane at RT and 80 °C (a), Height and phase images of collagen film at RT and 100 °C (b). Image Credit: Park Systems
Young’s modulus measurements were carried out using the PinPoint™ nanomechanical mode to evaluate how temperature variations affect the mechanical properties of five different polymers. The objective of this test was to examine changes in stiffness as influenced by temperature.
The selected materials—low-density polyethylene (LDPE), high-density polyethylene (HDPE), polystyrene (PS), polymethylpentene (PMP), and polyvinylidene fluoride (PVDF)—were chosen based on their rigidity, melting points, and thermoplastic characteristics (Table 1).
Each polymer was prepared as a square film measuring 2 × 2 × 0.5 cm and mounted onto a metal disk using a thermal compound to ensure proper heat conduction during testing.
Table 1. Properties of polymers. Source: Park Systems
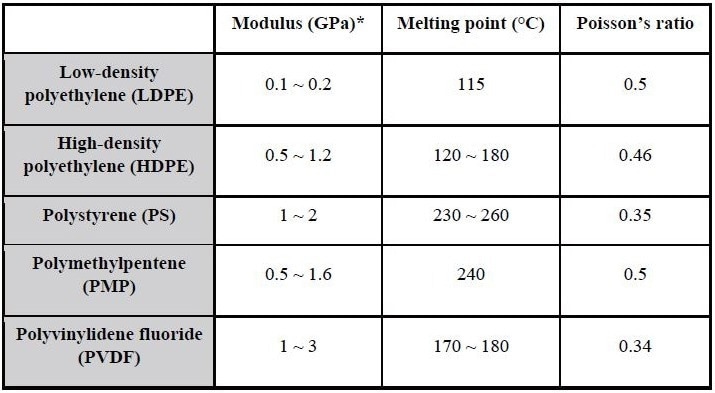
All five polymers exhibit thermoplastic behavior, with Young’s modulus values ranging from 0.1 to 3 GPa and melting points between 115 °C and 260 °C. Prior to measurement, the AFM probe was calibrated to ensure accurate and quantitative results.
Figure 3 displays Young’s modulus images for LDPE, which has a relatively low modulus and melting point, and PVDF, which is characterized by a higher modulus and melting point, across varying temperatures. The modulus maps and corresponding center line profiles clearly show a decrease in Young’s modulus with increasing temperature.
This temperature-dependent trend was consistently observed across all five polymers, as further confirmed by the data presented in Table 2 and Figure 4.
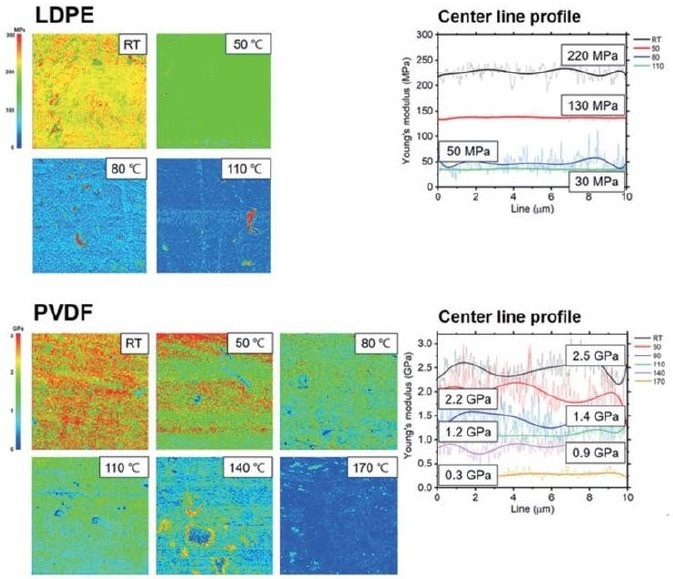
Figure 3. Young’s modulus images and center line profiles at different temperatures. Young's modulus values at center line profile indicate that the values decrease as the temperature increases. Image Credit: Park Systems
At elevated temperatures, the mobility of polymer chains is enhanced by increased thermal energy, leading to greater flexibility and reduced resistance to deformation in the polymer.
This enhanced mobility facilitates the movement and rearrangement of polymer chains under stress, resulting in a reduced Young's modulus. At elevated temperatures, the intermolecular forces that bind the polymer chains diminish, thereby contributing to the reduced Young's modulus.
Consequently, the interplay of enhanced chain mobility and diminished intermolecular forces at elevated temperatures reduces a polymer's Young's modulus.
Table 2. Young’s modulus of polymers at different temperatures. All measurements were performed by PinPoint nanomechanical mode and analyzed by SmartAnalysis (Image analysis program, Park Systems). Source: Park Systems
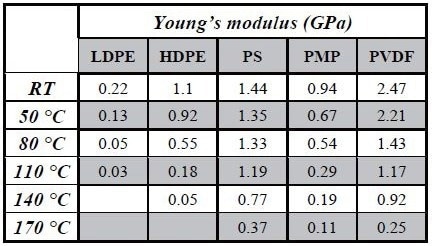
All measurements were conducted using the PinPoint nanomechanical mode and analyzed with SmartAnalysis, an image analysis program developed by Park Systems.
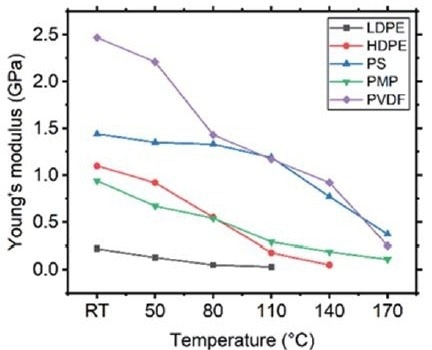
Figure 4. The graph of Young’s modulus-Tempurature of 5 polymers. The graphical information shows a similar trend for all polymers. Image Credit: Park Systems
Conclusion
This article addresses the impact of temperature variations on the mechanical properties of polymer materials, with particular emphasis on Young's modulus.
An AFM equipped with a TCS was used to measure the variations in Young's modulus as a function of temperature for several polymers, including LDPE, HDPE, PS, PMP, and PVDF.
As the temperature of a polymer material rises, its Young's modulus generally declines, resulting in increased flexibility and reduced stiffness of the material.
The characteristics of polymers can differ based on various factors, including their molecular structure, composition, and processing conditions, such as temperature.
Examining the properties of polymers in relation to temperature is crucial for numerous industries, including materials science, polymer engineering, and polymer processing.
This study aids in the development of new polymer materials with customized properties for specific applications, enhances processing conditions, and guarantees the performance and reliability of polymer-based products across various temperature settings.
Researchers and engineers can gain a deeper understanding of their behavior and performance across various conditions, allowing for the design of polymers with specific properties tailored to desired applications.
References
- Ward, I.M. and Sweeney, J. (2012). Mechanical Properties of Solid Polymers. Chichester, UK: John Wiley & Sons, Ltd. https://doi.org/10.1002/9781119967125.
- Shahabaz, S.M., et al. (2021). Influence of Temperature on Mechanical Properties and Machining of Fibre Reinforced Polymer Composites: A Review. Engineered Science, (online) Volume 16 (December 2021)(8), pp.26–46. Available at: https://www.espublisher.com/journals/articledetails/553 (Accessed 30 May 2025).
- Huang, P., Guo, Z. and Feng, J. (2019). General Model of Temperature-dependent Modulus and Yield Strength of Thermoplastic Polymers. Chinese Journal of Polymer Science, 38(4), pp.382–393. https://doi.org/10.1007/s10118-020-2360-7.
- Nasraoui, M., et al. (2012). Influence of strain rate, temperature and adiabatic heating on the mechanical behaviour of poly-methyl-methacrylate: Experimental and modelling analyses. Materials & Design, 37, pp.500–509. https://doi.org/10.1016/j.matdes.2011.11.032.
- Kendall, M.J. and Siviour, C.R. (2014). Experimentally simulating high-rate behaviour: rate and temperature effects in polycarbonate and PMMA. Philosophical Transactions of the Royal Society A: Mathematical, Physical and Engineering Sciences, 372(2015), p.20130202. https://doi.org/10.1098/rsta.2013.0202.
- Said Arévalo-Alquichire, Morales-Gonzalez, M., et al. (2020). Influence of Polyol/Crosslinker Blend Composition on Phase Separation and Thermo-Mechanical Properties of Polyurethane Thin Films. Polymers, (online) 12(3), pp.666–666. https://doi.org/10.3390/polym12030666.
- Shanmugam, G. and Polavarapu, P.L. (2008). Structural transition during thermal denaturation of collagen in the solution and film states. Chirality, 21(1), pp.152–159. https://doi.org/10.1002/chir.20598.
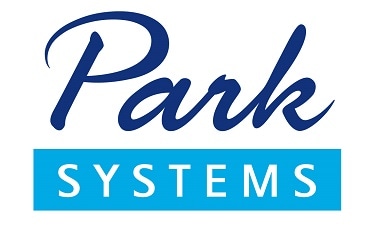
This information has been sourced, reviewed and adapted from materials provided by Park Systems.
For more information on this source, please visit Park Systems.