Particle size is the most important parameter in the production of ceramic products. The particle size must be optimized to ensure that the desired physical / mechanical properties are achieved. The majority of ceramic products are manufactured by the process of slip casting in a mould. Maintenance of the desired particle size distribution requires control of the dispersion stability of the ceramic slip.
Ceramic Slips
Slips are suspensions of one or more ceramic in a liquid, usually water, with a particle size of around 1µm and may be considered as a colloidal system. It is vital that there is control over the ability of the particles to remain in suspension so that deposition occurs evenly onto the mould walls.
Colloidal Dispersions and Zeta Potential
In colloidal dispersions, the stability is controlled by the interaction forces between particles. Without repulsion between particles, aggregates will form. Zeta potential is a measure of this interaction.
Conclusion
The production of strong defect free ceramics is obtained by producing a well-dispersed slip of known particle size distribution.
Zeta potential measurements using the Malvern Panalytical Zetasizer assist in developing a good dispersion and indicate the likelihood of aggregation.
- Enables optimization of process variables such as particle size and pH to improve slip dispersion and control product quality.
- Determine quantities of additives controlling dispersion.
- Measure the size of ceramic particles down to 2nm.
- Zeta potential measurement of virtually any ceramic slip.
- Measurements are fast and reproducible.
Case History – Monodisperse vs. Conventionally Milled Powders in Ceramic Slips
Since the early 1980’s increasing attention has been paid to the preparation of monodisperse sub-micron oxide powders, with a view to obtaining denser packing and a lower sintering temperature than can be achieved with a milled material.
Table 1 gives a comparison between the lower sintering temperature required using a monodisperse product, compared with a conventionally milled product.
Table 1. Sintering temperature comparison for a monodisperse powder and a conventionally milled product.
Sintering Temp (K) |
Oxide |
Initial Particle size (µm) |
Final Grain Size (µm) |
Monodisperse Product |
Conventionally Milled Product |
TiO2 |
0.3 |
0.5 |
1273 |
1873 |
ZrO2 |
0.2 |
0.3 |
1273 |
1973 |
Al2O3 |
0.25 |
0.5 |
1523 |
2023 |
Recent work by Zhang and Min Fang has shown that successful production of ceramic composite slip castings from sub-micron alumina and zirconia powder is highly dependent on the zeta potential of the powder in suspension. The suspending media was water with and without additions of a dispersing additive - PAA (polyacrylic acid). Zeta potential vs pH plots of the ZrO2and Al2O3were obtained on a Malvern Panalytical Zetasizer. Although the two materials codisperse well at pH 4-5, where the zeta potential was greater than 50mV, they were not suitable for slip casting because the acid medium seriously etched the plaster mould. In the basic pH region, the plaster mould was etched less by the medium. However, the powders could not be suspended in the basic medium because of the much smaller Al2O3zeta-potential compared to that of ZrO2. However, adding PAA had a dramatic effect on the zeta-potential of the powders.
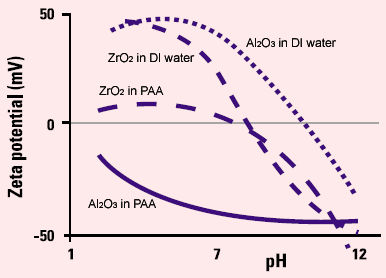 |
Figure 1. Zeta potential vs pH plot for alumina and zirconia casting slips.
|
At pH 10, the zeta-potentials of both powders were about -50mV, consequently, the powders could easily be co-dispersed.
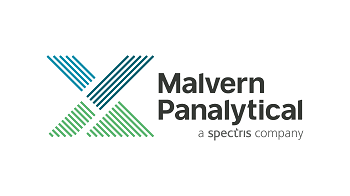
This information has been sourced, reviewed and adapted from materials provided by Malvern Panalytical.
For more information please visit Malvern Panalytical.