As nanotechnology continues to advance in almost every scientific field, its application in industry has been particularly valuable through the growing use of nanocomposites. A nanocomposite can be a one, two or three-dimensional matrix in which particles (<100 nm in size) have been added to improve a particular property of the material. The presence of these composite materials are able to reinforce properties of interest such as hardness, thermal and electrical conductivity, tensile strength, density, ductility, and wear resistance.
Nanocomposites can be derived from a metal, polymer or ceramic. Metal Matrix Nanocomposites (MMNCs) are still in their early developmental stages, yet numerous MMNCs have already been synthesized.
MMNCs can be prepared through powder metallurgy, deformation processing, vapor phase processing, and solidification processing. Powder metallurgy involves the blending of powdered metals and reinforcements, which is then followed by the sintering of mixtures to powders that form the composite. This mechanism has already synthesized numerous MMNCs such Mg-SiC, Al-CNT (carbon nanotube), Cu-CNT and Ti-SiC.
Solidification processing, which is the least expensive method for production, can involve three different mechanisms including rapid solidification, mixing of nanosize reinforcements in liquid, and infiltration of liquid into a preform of reinforcement followed by solidifcation. This mechanism has synthesized several MMNCs as well, including Al-SiC, Mg-SiC, Al-CNT, Al-Diamond, and Zn-SiC.
The ability of each metallic nanocomposite to accurately enhance properties of interest is dependent on many factors including the properties of the reinforcement and distribution, as well as the strength between the reinforcement and the matrix. One example of this challenge is in Al-CNT composites, in which aluminum carbide could form during processing. The formation of this brittle material can then affect the mechanical properties and electrical conductivity of the nanocomposite. In order to prevent these types of processing disruptions, methods are being developed in order to ensure uniform dispersions of nanomaterials with little deleterious reactions during the production of MMNCs.
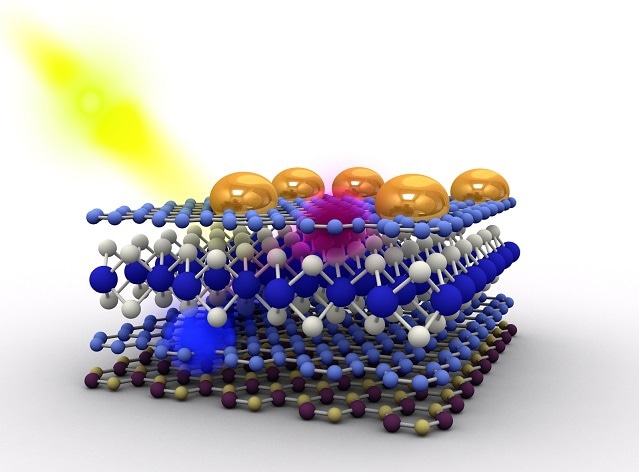
Image Caption: These 2D crystals can be assembled in 3D heterostructures that do not exist in nature and present unique physical properties due to low dimensionality and a special crystal structure. Image Credit: The University of Manchester
Industry Applications
MMNCs have been successfully applied in the automotive and aerospace industries, in which these products are able to exhibit greater strength and safety for consumers. For example, nanocomposites have enhanced the high wear resistance and thermal conductivity in automotive brake system components and the ventral fins of aircrafts, allowing for a much greater strength capability of these products. While nanocomposites are predicted to bring significant savings in materials and energy, further research is needed towards generating processing mechanisms that will produce bulk materials at a lower cost, with little to no voids or defects.
The aerospace industry has also had great success in its application of nanocomposites through carbon nanotubes and nanoclays, carbon fibre, glass fibre, carbon-carbon composites, and other multilayered structures. Each of these composites focuses primarily on reinforcement structures within each matrix. For example, a carbon fibre is a macro reinforcement that is incredibly stiff and strong, and when added to a matrix such as a polymer, the composite, as a whole, can exhibit these advantageous properties.
Similarly, ceramic nanocoatings, such as ZrO2, have been utilized for their thermal protection of aerospace turbo engines. These mono and multilayer protections offer temperature resistance and prevention of corrosive and erosive wear to a wide range of aerospace technologies.
Graphene Composites
Often used to enhance polymer composites, graphene is utilized for its flexible, transparent, strong, and electrically and thermally conductive properties. Previously, labs were unable to incorporate graphene-like materials into composites because of weak links that existed between graphene flakes, often causing them to clump together and create irregularities within the composites. In order to avoid this problem, scientists at Oak Ridge National Laboratory, managed by the University of Tennessee, have created composites using large flat or rolled up graphene sheets that measure five centimeters by five centimeters. Through chemical vapor deposition, these scientists have been able to grow graphene sheets directly from hydrocarbon vapor on metal catalysts such as copper.
With a thickness of only one atom, graphene has been described by the University of Manchester as “a hundred times stronger than steel.” As one of the first and best known two-dimensional materials, graphene holds a tremendous amount of promise for industrial purposes, in which its addition is estimated to yield a doubling or tripling of physical properties. With applications in the automotive and aerospace industries, graphene composites give added value to products by improving mechanical, thermal and electrical properties.
Graphene: Composite Materials
Video Courtesy of The University of Manchester YouTube channel
Developing Nanocomposites
As industrial business demands continue to rise, organizations, such as the iGCAuto research collaborative by the University of Sunderland, who are pioneering methods to produce functional graphene nancomposites, must play a leading roll. Funded by the European Union’s 10-year billion-euro Graphene Flagship program, iGCAuto plans to make high-performance graphene composites that have the potential to reduce 30%-50% of the weight of cars. Research is also being done to understand how graphene-based materials can improve the strength, dimensional stability, thermal behavior, flame retardance and even lessen smoke emissions for the benefit of consumer safety. This large-scale production of graphene was inspired by the research done at facilities like the Trinity College in Dublin, Ireland, where graphene was synthesized in a liquid process. Through a liquid exfoliation technique, researchers first mix graphite with a solvent (usually water) and soap, in which the problematic graphene flakes are sheared off.
The International Institute for Nanocomposites Manufacturing (IINM) also encompasses fundamental and applied research in order to ensure the production of safe and advanced nanocomposite materials. This organization aims to not only understand the dispersion and distribution patterns of nanoparticles in polymer melts, but also hopes to characterize the role of the interface relationship between the matrix and nanoparticle. The research performed by this organization has already found success in several industries including telecommunications, electronics, aerospace, automotive, security, pharmaceuticals and medicine.
Haydale are a leading nanomaterials company who are heavily involved in the development and supply of graphene composites for the Aerospace industry. In a recent interview with AZoNano, CEO Ray Gibbs explained how Haydale Composite Solutions is working closely with aerospace organization to develop a range of graphene based composite materials for this market.
Electrically conductive epoxy resins is one such composite the company is developing, which can increase the electrical conductivity of carbon composites used in the fuselages of aircraft. This could negate the need for copper mesh currently used to prevent damage caused from lightning strikes.
Conclusion
The progressive development of nanocomposite materials has offered a new and extensive range of improvement options for countless industries. This broad range of nanocomposite applications has the potential to save millions in spending costs, while also improving the welfare of the consumer. While researchers have already made significant advances in the scientific field through these applications, further analyses and experiments are necessary to ensure the absolute safety and reliability of this advancing technology.
References
- "Nanocomposites, Their Uses and Applications." Nanocomposites. Web. <http://www.understandingnano.com/nanocomposites-applications.html>.
- Rohatgi, Prof. P. K., and B. Schultz. "Lightweight Metal Matrix Nanocomposites - Stretching the Boundaries of Metals." Sigma-Aldrich. Material Matters, 2007. Web.
- "Carbon Fibre Composites | Aircraft Composite Materials | Haydale." Haydale. N.p., 11 Nov. 2014. Web.
- Dinca, Ion, Victor Manoliu, Adriana Stefan, and Sorina Ilina. "Nanocomposites and Nanotechnologies in Aerospace Research." National Institute for Aerospace Research & Development. Web.
- Choi, Charles Q. "Graphene Composites Go Big." IEEE Spectrum., 18 May 2015. Web.
- Ashley, Steven. "Graphene Composites for Cars." SAE International., 3 Oct. 2014. Web.
- "International Institute for Nanocomposites Manufacturing." WMG. Web.
Disclaimer: The views expressed here are those of the author expressed in their private capacity and do not necessarily represent the views of AZoM.com Limited T/A AZoNetwork the owner and operator of this website. This disclaimer forms part of the Terms and conditions of use of this website.