A key property in the majority of engineering applications is a material’s fracture toughness. In order to measure the fracture toughness of low volume materials fracture tests should be carried out a small scale with a micro-cantilever bending test. Micro-cantilever bending tests can also be used to determine how individual microstructural features contribute to a bulk material’s crack resistance.
Carrying out these tests with the assistance of SEM imaging allows crack path observations to be correlated with stress-strain data, allowing fracture mechanisms to be elucidated.
.jpg)
A typical micro-cantilever bending test involves the compression loading of free-standing notched cantilever beams that have been produced using a FIB or via lithography.
For brittle fractures, the fracture toughness (KIC) is equal to the stress intensity factor (K) at the highest load. For the measurement to be correct the instrument used must have true displacement control, as this prevents the specimen from catastrophically failing when the crack becomes unstable – a common problem with force-controlled instruments.
.jpg)
A different approach is required for the measurement of elastic-plastic fractures. These fracture mechanisms use a J-Integral to determine the elastic-plastic fracture toughness (JIC) and the crack growth resistance curve (J-R curve). In general, a steeper J-R curve or higher JIC or KIC value indicates that a material has a higher fracture resistance.
Continuous stiffness measurement (CSM) during micro-cantilever bending testing can be used to monitor how the length of a crack develops and to continuously determine the J-integral through periodic unloading phases.
The FT-NMT04, from Femtotools, combines high displacement and load resolutions with true displacement control, rapid data collection and a wide harmonic frequency range; allowing the fracture process to be carefully controlled and measured, with the determination of the individual effect of different microstructural features on a material’s bulk fracture toughness.
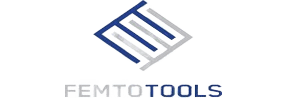
This information has been sourced, reviewed and adapted from materials provided by FemtoTools AG.
For more information on this source, please visit FemtoTools AG.