Nanomechanical measurements of soft materials play a critical role in their designing, development, and subsequent applications. This article presents the advancement of MEMS nanoindenterfor AFM probes for nanomechanical analysis of soft materials.
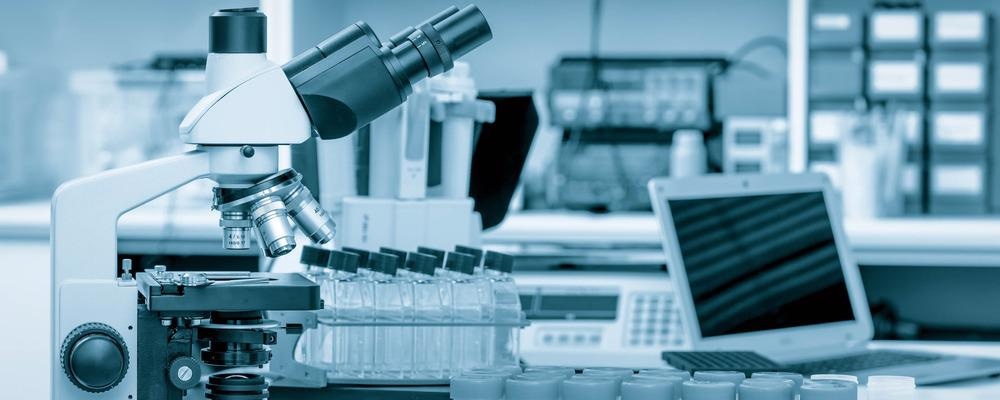
Image Credit: luchschenF/Shutterstock.com
Soft Materials: Challenges in Characterization
Soft materials, such as colloids, polymers, gels, emulsions, and liquid crystals, are extensively used in various scientific and industrial applications. Atomic force microscopy (AFM) has a high force resolution and has long been used to analyze the mechanical properties of soft materials.
Unfortunately, when a large cantilever of AFM is used for deep indentation, tip tilting and lateral scratching are unavoidable. Additionally, quantitative indentation force can be obtained after the cantilever is precisely calibrated, which is often extremely difficult when an AFM probe has a pointed and delicate tip.
As a result, a novel design for nanomechanical analytical systems based on AFM is required for soft materials.
MEMS-based Nanomechanical Measurement: Challenges and Overcome
Microelectromechanical systems (MEMS) have high force and displacement sensing resolution. While there have been several efforts to use MEMS actuators/sensors for nanomaterials characterization.
One of the critical problems in MEMS-based nanomechanical characterization methods is the fabrication of an indenter tip that can be attached directly to the end of a MEMS shaft
State of Art: MEMS Nanoindentor with AFM Probe
Researchers developed a lightweight and reliable MEMS nanoindenterthat consists of a microtransducer for nanoforce sensing and a gripper for the holding of different AFM probes
To clamp a cantilever, a gripper with one pair of L-shaped springs is customized. Indenters for material testing are typically made from Si-based AFM probes. The tip height of an AFM probe is approximately H = 9.5 µm ± 5 µm.
The AFM cantilever is fitted into the MEMS gripper using an optical microscope in such a way that the cantilever beam is perpendicular to the MEMS main shaft.
Recent Development in Characterization Using MEMS Nanoindenterwith AFM probe
Researchers used a MEMS Nanoindenterto scan a sapphire sample using a diamond-coated AFM probe held in its gripper. To prove the performance capability of the MEMS nanoindenter, a sapphire sample is shifted stepwise at a fractional amplitude of 200 pm and a frequency of 0.1 Hz. The MEMS reading has a quasi-static depth-sensing resolution of over 60 pm at frequencies greater than 0.2 Hz and a force sensing resolution of 3.7 nN in air.
The ultra-high sensitivity of the MEMS Nanoindenterenables this design to be used in nanodimensional analyses of low-dimensional sample materials. For example, using the clamped diamond AFM probe in scanning probe microscopy mode, researchers used the MEMS Nanoindenterto scan an atomic step (about 0.31 nm) in Si <111> ultraflat sample.
Nanomechanical Measurement of Soft & Ultra-soft materials
Using a silicon-coated AFM probe, scientists demonstrated the potential of the MEMS nanoindenterto conduct nanomechanical measurements on soft polymers such as polyamide, polycarbonate, and low-density polyethylene.
For example, the hardness evaluated over the indentation depth hc less than 250 nm for polycarbonate was found to be (165 ± 7) MPa, which is consistent with the quoted value obtained using commercial nanoindentation.
Using a spherical diamond-coated AFM probe, the potential of the MEMS nanoindenter for conducting nanomechanical measurements of ultra-soft materials such as polydimethylsiloxane (PDMS) was proven.
Key Features of MEMS Nanoindenterwith AFM Probe
The MEMS nanoindenter includes a passive gripper that can be used to hold commercial AFM probes as an indenter. In the MEMS nanoindenter, the electrostatic force transducer can indent up to 9.5 µm and can indent with a force of more than 600 µN. Interestingly, experimental results have shown that it can attain force and depth resolutions better than 0.3 nN/Hz1/2 and 4 pm/Hz1/2 in air for frequency greater than or equal to 1 Hz.
The MEMS nanoindenter can perform nanomechanical measurements on soft and ultrasoft materials with elastic moduli as low as a few MPa and provide accurate results. In addition, it is finally possible to quantitatively determine mechanical properties of the ultra-thin-film materials of thickness less than 10.
The MEMS transducer can clamp a variety of commercially accessible AFM probes as indenters and perform nanodimensional measurements with atomic resolution and lateral resolution of up to 10 nm.
Commercialization of MEMS Nanoindenters with AFM Probe
Bruker's ultra-low noise xProbeTM is a MEMS-based transducer that extends AFM characterization to the angstrom level. For AFM-based measurement systems, the xProbe from Bruker delivers force noise floors of less than 2 nN and displacement noise floors of less than 20 pm. The rigid probe design also allows for accurate force sensing during probe approach/retraction without contact snapping.
Another company AFMWorkshop, based in South Carolina, created AFM scanners using microelectromechanical systems (MEMS) technology. This MEMS-based nanopositioner allows users to customize the AFM for any specific applications.
Furthermore, Integrated Circuit Scanning Probe Instruments (ICSPI), a spinoff company from the University of Waterloo in Canada, has devised the world's first single-chip AFM named as nGuage AFM. Here, the sharp tip of an AFM sensor, scanners, and the sensors have all been integrated into a single 1x1mm MEMS chip.
Conclusion
The MEMS nanoindenter can be effectively integrated into various atomic force microscopy (AFMs), transmission electron microscopy (TEMs), and scanning electron microscopy (SEMs) for in-situ nanomechanical and nanodimensional measurements of soft and ultrasoft materials because of its compact design and small size.
This device can also quantitatively evaluate mechanical properties such as hardness and elastic modulus properties of soft, ultrasoft and ultra-thin film materials, which were previously a challenge.
References and Further Reading
Li, Z., Gao, S., Brand, U., Hiller, K. and Wolff, H., (2020) A MEMS nanoindenter with an integrated AFM cantilever gripper for nanomechanical characterization of compliant materials. Nanotechnology, 31(30), p.305502 https://iopscience.iop.org/article/10.1088/1361-6528/ab88ed
Bîrleanu, C., Pustan, M., Șerdean, F. and Merie, V., 2021. AFM Nanotribomechanical Characterization of Thin Films for MEMS Applications. Micromachines, 13(1), p.23. https://www.mdpi.com/2072-666X/13/1/23
Disclaimer: The views expressed here are those of the author expressed in their private capacity and do not necessarily represent the views of AZoM.com Limited T/A AZoNetwork the owner and operator of this website. This disclaimer forms part of the Terms and conditions of use of this website.