Metals with nanograins have tremendous strength, but they suffer from minimal work hardening capability and poor temperature resistance, resulting in early failure and restricting their operational usefulness.
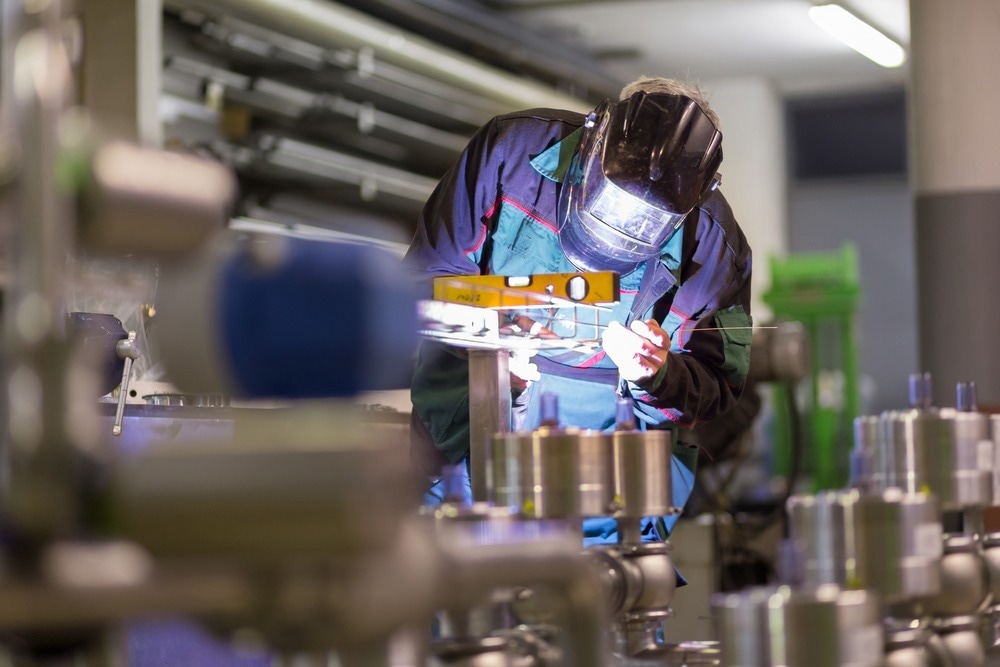
Study: A nanodispersion-in-nanograins strategy for ultra-strong, ductile and stable metal nanocomposites. Image Credit: Matej Kastelic/Shutterstock.com
A new work published in Nature Communications addresses this problem by using a nanodispersion-in-nanograins approach to concurrently reinforce and stabilize copper and nickel metal nanocomposites. This technique is based on the homogeneous dispersion of ultrafine-sized carbon nanoparticles inside nanograins.
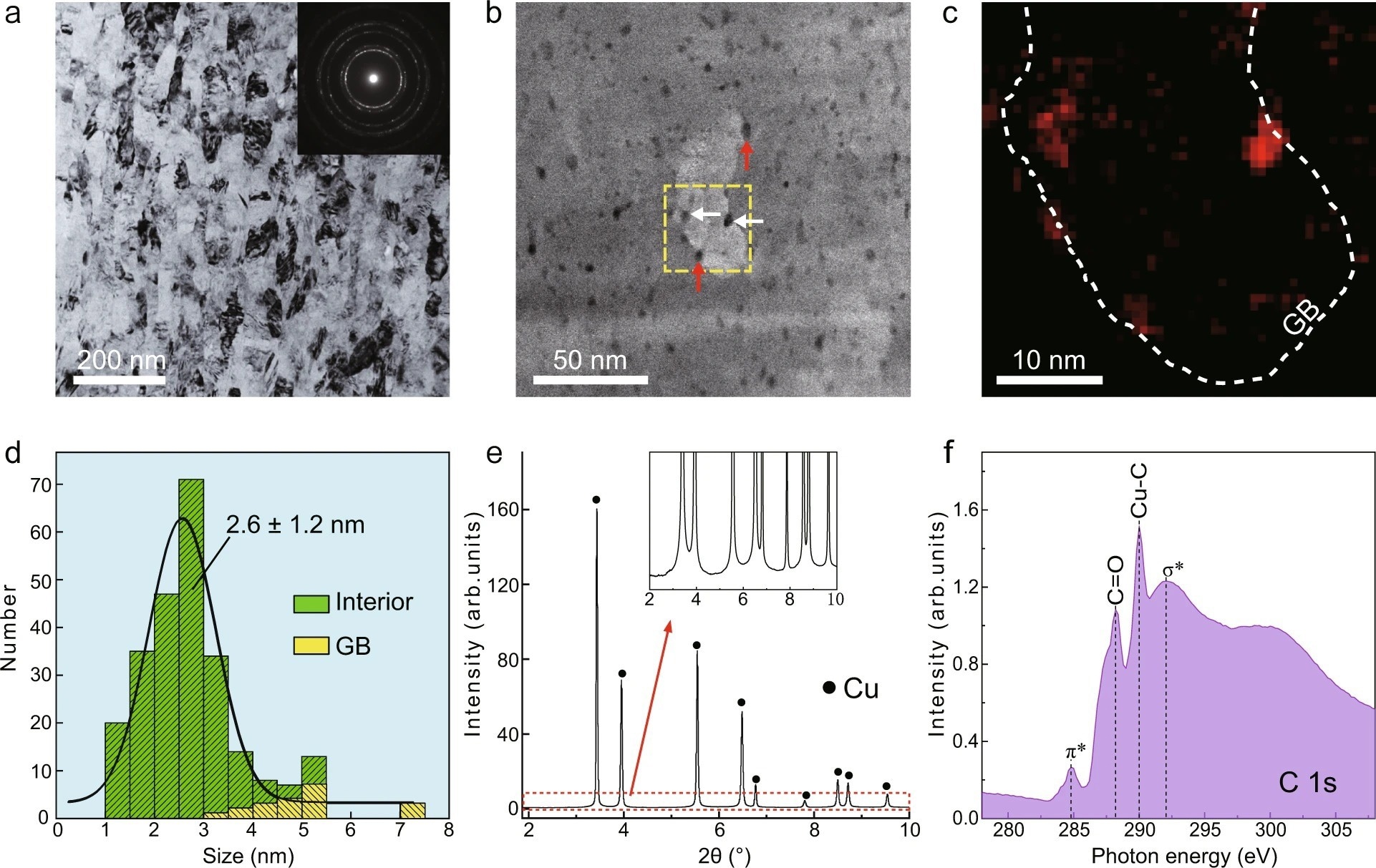
Figure 1. Microstructure of nc-Cu composites dispersed with unc particles. a A bright-field (BF) TEM image showing nanocrystalline grains in an as-synthesized composite, as confirmed by nearly uniform diffraction rings in the inset. An aperture size of 1 μm was used. b An HAADF-STEM image of nc-Cu with a C concentration of 0.8 vol.%, where a high density of unc particles is observed. Some unc particles within grains and along grain boundaries (GBs) are indicated by white and red arrows, respectively. BF- and HAADF-STEM images are used together to identify GBs. c EELS C imaging map for the boxed area in b where the GB is delineated by the white dashed line. d A histogram showing the size distribution of unc particles and their locations either in grain interiors or at GBs, as measured by STEM; 92% of 252 unc particles are found inside grains. e Synchrotron X-ray diffraction (SXRD) pattern of the composite. Inset is the magnified spectrum of the boxed region, showing the absence of additional peaks except for those of Cu. No carbide forms at Cu-C interfaces. f Near-edge x-ray absorption fine-structure (NEXAFS) spectrum at the C-K edge of nc-Cu composite (0.8 vol.% C). A distinctive peak (~290 eV) arising from Cu-C covalent bonding is observed. © Li, Z. et al. (2022)
Metal Nanocomposites: Why Are They Important?
Metal nanocomposites have become prominent in recent years due to their intriguing chemical and physical characteristics. Metal nanocomposites can be created by combining metallic nanoparticles with glass, ceramics, and polymeric materials.
Metal nanocomposites have been identified as the materials of the twenty-first century, having applications in almost every industrial sector. The wet chemical approach is the simplest way of producing these metal nanocomposites, making them both cost-effective and cytocompatible.
They can be characterized using various methods such as X-Ray diffraction, electronic microscopy, and atomic force spectroscopy, providing information on the materials' shape, particle size, and thermal stability. Metal nanocomposites are frequently used as adsorbents, photocatalysts, and antimicrobial agents because of their simple synthesis methods and wide range of tailorable properties.
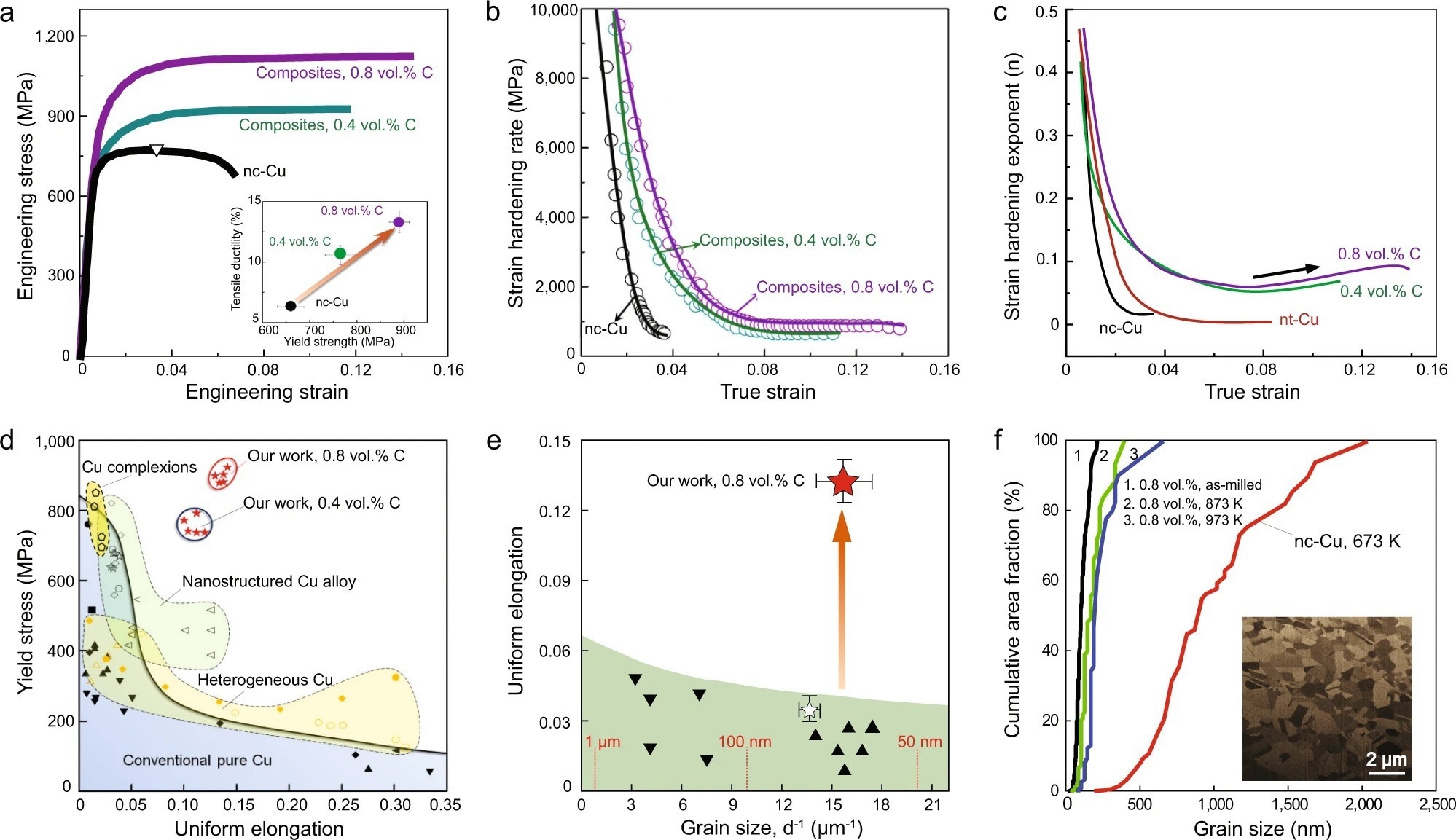
Figure 2. Tensile properties and thermal stability of nc-Cu composites. a Representative tensile engineering stress-strain curves for pure nc-Cu and nc-Cu composites (0.4 vol.% and 0.8 vol.% C, respectively). All tensile tests were performed at a strain rate of 5 × 10−4 s−1 and room temperature. The strain at which necking occurs is marked with an open triangle for pure nc-Cu. The inset shows the simultaneous improvement of yield strength and uniform elongation of nc-Cu composites over pure nc-Cu. b Experimentally measured strain hardening rate dσ/dε (with σ and ε being the true stress and true strain, respectively) for nc-Cu composites and nc-Cu. c Strain hardening exponent (n = d(lnσ)/d(lnɛ)) as a function of strain. The reference nt-Cu plot was calculated from the literature. d Yield strength versus uniform elongation of nc-Cu composites as compared with those of other Cu-based materials, including heterogeneous Cu, nanostructured Cu alloys and complexion-engineered Cu. Superior properties are observed for nc-Cu composites. Sources of the references are cited in the Methods. e Uniform elongation versus grain size of nc-Cu composites as compared with those of pure nc-Cu. f Thermal stability of nc-Cu composites: cumulative area fraction of grain size of the nc-Cu composite (0.8 vol.% C) annealed at various temperatures (873 K and 973 K) for 1 h, in comparison with that of the reference nc-Cu annealed at 673 K for 1 h. Inset shows pronounced grain growth in nc-Cu, as indicated by the ion-channelling cross-sectional image. In contrast, no grain growth was observed in nc-Cu composites after annealing at 973 K for 1 h. © Li, Z. et al. (2022)
Challenges Associated with Metal Nanocomposites
Metal nanocomposites can be severely damaged by an absence of work stiffening, leaving them prone to fracturing and mechanical failure. Nanocrystalline metals (with a mean particle size of less than 100 nm) have been intensively researched to obtain high strength.
However, they have a low work hardening capability, resulting in restricted tensile ductility and poor thermal resilience and electrical conduction.
Although alloying by one or more elements may solve some of the abovementioned constraints, it frequently comes at a high cost and an additional decrease in electrical conductance. It also encounters difficulties of longevity and, on occasion, intergranular embrittlement due to elemental separation at grain borders (GBs).
Nanosized reinforcements are an alternate method for strengthening fine-grained substances such as metal nanocomposites. Metal nanocomposites created due to this strategy have increased strength, heat resistance, and electrical conduction.
However, these additives aggregate or spread along GBs, resulting in local stress absorption, interfacial delamination, and structural failure. As a result, simultaneously improving strength, stiffness, and heat resistance in metal nanocomposites containing nanograins, a category of high-strength nanomaterials with extensive potential applications, remains difficult.
Figure 3. Microstructure, tensile properties, and thermal stability of pure nc-Ni and nc-Ni composite. a A bright-field TEM image of nc-Ni composite (0.8 vol.% C). Inset shows the Ni grain size distribution of the composite. The grain size of nc-Ni obtained with the identical fabrication process is 61 ± 10 nm. b SXRD pattern of the composite. Note that no Ni-C compounds are observed in SXRD experiments. c NEXAFS spectrum at the C-K edge of nc-Ni composites (0.8 vol.% C). Ni-C chemical bond, which corresponds to the absorption peak at 290.3 eV, is identified. d Representative tensile engineering stress-strain curves for nc-Ni and nc-Ni composites. Simultaneous enhancement of yield strength, fracture strength, and uniform elongation are observed for nc-Ni composites compared to pure nc-Ni. e Thermal stability of nc-Ni composites: cumulative area fraction of grain size of the as-fabricated nc-Ni composite (0.8 vol.% C) and after being annealed at various temperatures (973 K to 1193 K) for 1 h. No apparent grain growth was observed for nc-Ni composite after annealing at 1073 K for 1 h. The inset shows a representative bright-field TEM image for this annealing condition. f Electrical resistivity of nc-Ni and nc-Ni composite measured at the temperature range of 2 to 300 K. The electrical conductivity of nc-Ni composite (0.8 vol.% C) is ~77% higher than that of nc-Ni (3.9 S/m vs. 2.2 S/m) at room temperature (298 K). © Li, Z. et al. (2022)
Highlights of the Current Study
This study employed a "nanodispersion-in-nanograins" technique to improve mechanical characteristics, heat resistance, and electrical conduction in metal nanocomposites.
The researchers concentrated on a homogeneous intragranular distribution of high-density carbon nanomaterials instead of typically employed methodologies like multilevel microstructural designing and GB engineering.
Finely distributed intragranular nanostructures enhance the reinforcing effect of nanograins and stimulate numerous hardening frameworks via dislocation-nanoparticle connections. This results in metal nanocomposites with distinctive configurations of high tensile strength, work hardening, and elastic modulus.
Carbon is plentiful in nature, inexpensive, lightweight, and has outstanding physical and chemical qualities. The researchers showed their new nanodispersion-in-nanograins technique by incorporating carbon nanostructures into nanocrystalline copper (nc-Cu) and nickel (nc-Ni) metal nanocomposites.
Important Findings of the Research
The as-prepared nc-Cu composites had a substantial nanocarbon concentration inside copper nanograins. These intragranular nanodispersions provided a two-stage stiffening process in nano-grained metals, improving both ductility and toughness.
In addition, the strong nanodispersions gave a robust resilience to grain coarsening. Consequently, the nc-Cu composites acquired an outstanding mixture of high strength properties, consistent elongation, excellent thermal stability, and enhanced electrical conductance.
Using the same method, the researchers produced nc-Ni composites with exceptional characteristics, demonstrating the universal applicability of the nanodispersion-in-nanograins concept for building high-performance metal nanocomposites.
Based on these results, it is reasonable to assume that the homogeneous intergranular distribution of carbon nanoparticles in nanocrystalline metals is useful for achieving enhanced work hardening, improved thermal reliability, and electrical conductance.
These combined features surpass those attained by other nano-structuring techniques, such as GB engineering, hierarchical micro-structuring, and nano-twinning. Consequently, nanodispersion-in-nanograins is a promising technique that may broadly apply to the fabrication of ultra-strong, bendable, and robust metal nanocomposites for potential functional and structural applications.
Reference
Li, Z. et al. (2022). A nanodispersion-in-nanograins strategy for ultra-strong, ductile, and stable metal nanocomposites. Nature Communications. Available at: https://www.nature.com/articles/s41467-022-33261-5
Disclaimer: The views expressed here are those of the author expressed in their private capacity and do not necessarily represent the views of AZoM.com Limited T/A AZoNetwork the owner and operator of this website. This disclaimer forms part of the Terms and conditions of use of this website.