When compared to their coarse-grained alternatives, ultra-fine grained and nanocrystalline materials demonstrate enhanced strain rate sensitivity (SRS). Traditionally, bulk specimens have been used to measure the SRS of these materials – either in tension or in compression.
As magnetron sputtering and electrodeposition have emerged as promising methods for the deposition of controlled microstructures of twinned and nanocrystalline materials, the adaption of bulk mechanical tests to smaller samples has become necessary.
As a result of the difficulty inherent in the preparation and testing of micro-samples, most of the nano- and micro-mechanical methods of measuring SRS involve approaches based on nanoindentation [1-3].
The goal of this present study is to expand the repertoire of nanomechanical testing methods for SRS measurements through the design of micropillar strain rate jump tests on nanocrystalline nickel.
The results of these tests will be directly compared with more established methods, such as nanoindentation and tensile strain rate jump tests. To maximize cross-comparability, the same sample will be used for all tests.
Experimental
With the use of a proprietary electrodeposition process on a silicon wafer, nominally pure, nanocrystalline nickel tensile specimens were produced.
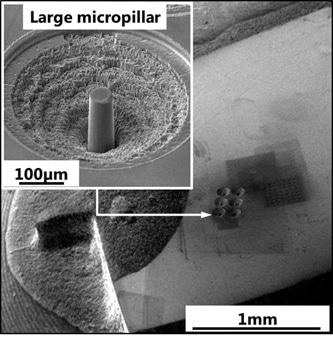
Figure 1. Nanoindentation and micropillar compression tests wereperformed on the undeformed gripping section of the tested tensile bars.
The average grain size of each of the samples was ~30 nm, which was established using TEM analysis. Using a TESCAN Lyra gallium focused ion beam (FIB) system, micropillars which had an aspect ratio of 2.5 and a nominal diameter of 3.5 m were machined on the undeformed gripping section of failed microtensile samples (Fig. 1)
An Alemnis nanoindenter (Alemnis AG) was used to perform micropillar nanoindentation and compression tests inside a Zeiss DSM962 SEM. Additionally, micropillars were fabricated on a (123)-oriented single crystal of pure nickel (Goodfellow Cambridge Ltd., UK) for control and verification, as it does not exhibit SRS.
Results and Discussion
As the nanoindenter is intrinsically displacement-controlled and utilizes an extremely responsive piezoelectric actuator, strain rates can be varied between different orders of magnitude in one experiment with a high degree of accuracy.
By varying the strain rate between 4x10-5 s-1 and 2x10-2 s-1 within each test, strain rate jump tests were performed as shown in Figure 2. Sharp jumps were observed with relatively quick stabilization of the flow stress and small transients for nanocrystalline nickel. As a result of the uniform microstructure within the material, the micropillar strain rate jump tests proved to be extremely repeatable.
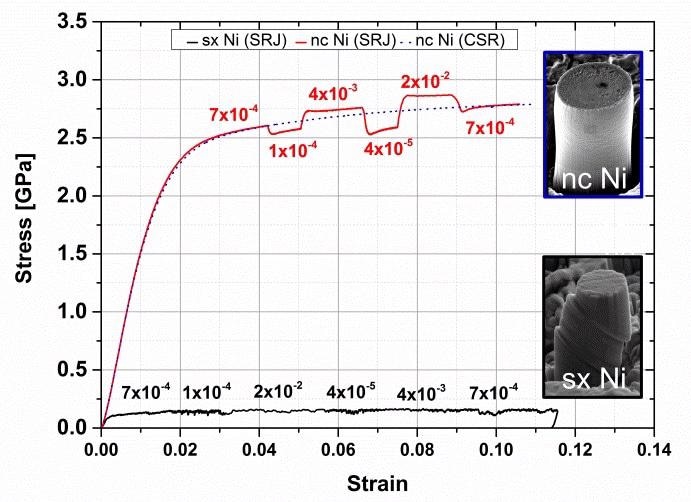

Figure 2. Micropillar stress‐strain curves for nanocrystalline and 〈123〉 oriented single crystal nickel. In‐situ SEM observation of the deformation behavior of nanocrystalline (nc) nickel (red) and single crystal (sx) nickel (black) micropillars during compression test at selected strains.
Also shown are the results for the (123)-oriented single crystal of nickel. This is to demonstrate the extraordinary strengthening effect of the nanocrystalline microstructure.
The Ni single crystal’s yield strength at 1% offset was observed as just 0.13 GPa. Its nanocrystalline counterpart delivered a value which was almost a factor of twenty greater. Furthermore, and as anticipated, it does not show any SRS.
While the majority of the plastic deformation located in the upper half is accommodated by the nanocrystalline nickel micropillar, the single crystal pillar develops numerous large slip steps over the pillar’s entire diameter (Fig. 2). This constitutes another advantage of in-situ testing in SEM, which allows the observation of the specimen deformation for the duration of the test.
The strain rate sensitivity exponent, m, is a measure of the dependence of change in flow stress, σ, as a function of change in applied strain rate, Σ, at constant temperature, T:
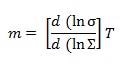
![Flow stress as a function of strain rate for tension, microcompression and nanoindentation (H/2.8) tests from the current work and the literature [2, 4]](https://d1otjdv2bf0507.cloudfront.net/images/Article_Images/ImageForArticle_5132_4454044486604177531.jpg)
Figure 3. Flow stress as a function of strain rate for tension, microcompression and nanoindentation (H/2.8) tests from the current work and the literature [2, 4]
Shown in Figure 3, the log-log plot compares resulting flow stress as a function of strain rate for the three applied test methods with literature results. Dividing the hardness values obtained from nanoindentation by a constraint factor of 2.8 converted them into representative stress values.
Even though three different nickel samples - with grain sizes of 80 nm (Maier et al. [2]), 27 nm (Mohanty et al. [4]) and 30 nm (current study) – and three different loading cases are compared in Figure 3, all of the results are reasonably consistent. This is particularly the case when the m values are compared between measurements performed in this study.
In this study, the variation in flow stresses between the larger scale (tension) and the smaller scale (microcompression and nanoindentation) measurements can be attributed to crystallographic texture.
A (111) fiber texture was revealed in the loading direction of indentation/ microcompression experiments by XRD measurements. As anticipated, in terms both of SRS exponent values and absolute flow stress, the results from the single crystal nickel sample vary substantially from the nanocrystalline results.
Conclusion
The study of the time-dependent plasticity of nanocrystalline Ni samples was the purpose for which micropillar strain rate jump tests were designed.
Two established micromechanical measurement techniques for assessing SRS were used as standards against which the results were compared. The same nanocrystalline nickel specimen was also used, so that the consistency and comparability of the test results could be studied.
The SRS exponents which were extracted from each of these three methods proved to be in exceptional agreement. These results validate the developed micropillar strain rate jump tests. This suggests that the techniques compared in this study can be used interchangeably and reliably, in order to accurately measure SRS across a range of materials.
References
- Schwaiger R, Moser B, Dao M, Chollacoop N, Suresh S. Some critical experiments on the strain‐rate sensitivity of nanocrystalline nickel. Acta materialia 2003;51:5159‐72.
- Maier V, Durst K, Mueller J, Backes B, Höppel HW, Göken M. Nanoindentation strain‐rate jump tests for determining the local strainrate sensitivity in nanocrystalline Ni and ultrafine‐grained Al. Journal of materials research 2011;26:1421‐30.
- Alkorta J, Martínez‐Esnaola JM, Sevillano JG. Critical examination of strain‐rate sensitivity measurement by nanoindentation methods: Application to severely deformed niobium. Acta Materialia 2008;56:88493.
- Mohanty G, Wheeler JM, Raghavan R, Wehrs J, Hasegawa M, Mischler S, et al. Elevated temperature, strain rate jump microcompression of nanocrystalline nickel. Philosophical Magazine 2015;95:1878‐95.
This application note is based on the paper “Comparison of insitu micromechanical strain rate sensitivity measurement techniques” published in Journal of Materials 67 (2015) p.1684 DOI: 10.1007/s11837‐015‐1447‐z Authors: Juri Wehrs, Gaurav Mohanty, Gaylord Guillonneau, Aidan A. Taylor, Xavier Maeder, Damian Frey, Laetitia Philippe, Stefano Mischler, Jeffrey M. Wheeler and Johann Michler
Guarav Mohanty [1], Juri Wehrs [1]. Gaylord Guillonneau [1]. Damian Frey [4], Jeffrey M. Wheeler [1, 3], and Johann Michler [1]
[1] Empa-Thun, [2] EPFL-Lausanne, [3] ETH-Zurich, [4] Alemnis AG
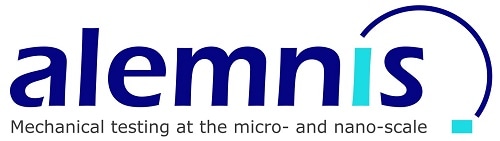
This information has been sourced, reviewed and adapted from materials provided by Alemnis AG.
For more information on this source, please visit Alemnis AG.