Mar 16 2010
Seiko Instruments Inc. (SII) has succeeded in developing a high precision siliconbased MEMS resonator. In addition, SII, in collaboration with the Institute of Microelectronics (IME), a research institute of the Agency for Science, Technology and Research (A*STAR), has also succeeded in the development of a new wafer level packaging technology for vacuum sealing MEMS devices.
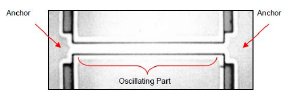
High Precision Silicon-based MEMS Resonator
The resonator is a device that is indispensable in modern electronics products such as computers, digital appliances and telecommunications devices. Currently, resonators using quartz crystals are the mainstream due to its light weight, highly precise and stable frequency properties. Research for new silicon based resonators shows that further miniaturization and reduction in cost may be possible through the use of MEMS processes to fabricate with silicon material.
High temperature dependency of the resonant frequency of silicon-based resonator poses a major challenge. More specifically, due to factors like thermal expansion and Young's modulus temperature dependence, its resonant frequency fluctuates when there is a change in temperature and generally has a temperature coefficient of - 40ppm/°C. This means that for its operating temperature limit (-40°C~80°C), the resonant frequency will fluctuate in the 5000ppm range, making it very difficult to ensure precise output frequency in the resonator.
In order to ensure precise output frequency, electrical circuit has to be used to compensate for the change in resonant frequency as a result of temperature fluctuations. This creates a problem in the design for low power consumption and miniaturization. Furthermore, the use of electrical circuit to substantially compensate for temperature fluctuations will also lead to the occurrence of noise in the output. Now, SII has successfully developed manufacturing technology that can greatly improve the problem of temperature dependence of the resonant frequency in silicon-based MEMS resonator by adding a layer of silicon dioxide film to the MEMS resonator fabricated on the SOI (Silicon On Insulator) substrate, and employing a structure that would produce residual stress within the resonator.
The temperature coefficient of resonant frequency fluctuation has improved from - 40ppm/°C to ±2ppm/°C. The frequency accuracy could also be controlled to a range with a maximum of 500ppm at operating temperature range (-40°C~80°C) This will reduce the need for temperature compensation to the minimal and allow for application in low power consuming, miniaturized and high precision resonator.
Development of new wafer level packaging technology for vacuum sealing MEMS devices
In MEMS devices such as a resonator, a vacuum has to be present when in operation and low cost vacuum packaging technology for devices are desired. SII, in collaboration with IME, has developed a new vacuum sealing wafer level packaging technology by bonding the silicon substrate which acts as a cover, to the MEMS resonator device.
Usually, anodic bonding is used for sealing processes for MEMS devices with silicon substrate. However, this application is limited to the high temperature (400~500°C) and high voltage (600~1000V) needed for the bonding process, which might cause warping of the device. In addition, gases such as oxygen are produced during anodic bonding, making it necessary to include getters in the sealing process to remove the gases produced during the vacuum packaging process.
SII and IME have jointly developed vacuum packaging technology using gold-tin eutectic bonding processes. With gold-tin eutectic bonding, the process can take place at low temperatures making it possible to inhibit the release of gases during bonding. This indicates that a higher level of vacuum sealing below 26Pa can be achieved without the use of a getter and external electrode can be drawn out laterally without passing through the substrate. This method not only improves the mechanical strength but also lowers fabrication cost. SII and IME have successfully tested the performance of the aforementioned siliconbased MEMS resonator vacuum-sealed with the new wafer level packaging technology. With the newly developed silicon-based MEMS resonator and the new wafer level packaging technology, it would be possible to achieve miniaturization and low power consumption.
SII will conduct further performance evaluation to verify the possibility of a miniaturized and low power consuming resonator for future application in resonator devices. Silicon MEMS resonator devices are very compatible with ICs, making application in high frequency resonator, which would otherwise be difficult to achieve with quartz crystals. Its practical application will make low cost, high-mix low-volume production and miniaturized single chip high frequency resonator possible. Application for the packaging technology in MEMS devices with various functions is also currently under review, with the aim to continue development for more compact and low power consuming devices. SII has set up a representative office in Singapore and has been collaborating with IME since 2007.