Oil spills resulting from fuel transportation and drilling operations have a great impact on the environment, as well as the huge loss of energy resources. It is essential to take appropriate actions in protecting the environment through oil spill recovery.
In general, the oil spill recovery and clean-up process is difficult and depends on various factors such as the properties of the spilled oil (including type, morphology, extension, amount and thickness of the oil slick), as well as the spillage location and weather conditions.
Techniques for Treating Oil Spills
The following are common methods for treating oil spills:
Mechanical treatment
Mechanical devices, such as skimmers and booms, can separate the oil slick from water to prevent contamination of specific regions. These devices therefore serve as a primary means of action for cleaning oil spills in water. The efficiency of this technique, however, is based on various factors such as the technical features of skimmers and booms, the oil properties and weather conditions.
In-situ burning
This physical method is a time-effective physical technique usually used for removing oil slicks on water of at least one millimeter in thickness. It is suitable for use in Arctic water, salt marshes and wetlands.
However, for regions across shorelines, windy areas and narrow vessels, this method is not recommended. The major limitations of this technique are the resulting air pollution from burning the oil as well as the inability to recover the resource.
Physical/Chemical/Biological Methods
Often used as a secondary means of action, these methods are used when oil burning and skimming are not effective or recommended. Chemicals used for cleaning up oil spills are classified into four types: emulsion breakers, inhibitors (prevents emulsion formation between water and oil retaining the original volume of oil), solidifiers (gel the oil layer to enhance oil containment and recovery), sinking agents (adsorbing the oil and then sinking to the water bed), and dispersants (breaking up the surface layer of oil into droplets).
However, toxicity and/or persistence of most of the chemical agents used can cause some serious environmental issues. In recent years, bioremediation of soil oil spills and water has become a practical approach to cleaning oil spills.
Bioremediation includes bio-augmentation (introduction of oil degrading microorganisms) and bio-stimulation (addition of supplemental nutrients to help the existing oil degrading microorganism).
Studies have shown that bioremediation has numerous advantages for many oil spills, such as low cost and the absence of toxicity. However, the method also has several disadvantages including the need of an appropriate physical and chemical oil, water or soil and surrounding environment properties, and long-time of action.
Adsorbent materials
These are considered a secondary physic-chemical means of cleaning up oil spills. They can be used as a form of containment similar to booms, or they can be used for small oil pools that cannot be easily recovered via other techniques. Oil-adsorbent materials can be classified based upon their constituent matter (inorganic mineral products, synthetic products, and organic vegetable products), selectivity (oil-only or universal sorbents) and form (bulk, pads, rolls, pillows, booms, mops and special products).
While the success of absorbents is primarily determined based on their hydrophobicity and oleophilicity, other important factors include retention of oil over time, recovery of oil from absorbents, the amount of oil absorbed per unit weight of absorbent, reusability, biodegradability, buoyancy, availability, cost, strength and durability of the absorbent material. Mineral products, such as perlite, silica, zeolites, etc., can absorb from 4-20 times their weight of oil.
These products are inexpensive and readily available in large amounts but are not used on the water's surface. Organic vegetable products, such as cotton fiber, wood fiber, corncob, straw, etc., are biodegradable and less expensive than synthetic absorbents. However, organic products have shown low hydrophobicity, relatively low oil absorption capacity and poor buoyancy characteristics. Furthermore, most of the organic absorbents are loose particles, such as sawdust, which are difficult to collect from water.
Synthetic organic products, including polyurethane, polyethylene and polypropylene, have higher absorption capacity than natural absorbents, but they degrade slowly and, since they do not occur in nature, they are highly expensive to manufacture.
Synthetic sorbents and mechanical devices are the major competitors of Grafysorber in cleaning up oil spills.
In terms of synthetic adsorption materials, polypropylene inside certain containment booms is the most used method to clean up oil spills. These devices have a fast adsorption kinetic, a maximum adsorption capacity of 20 kg/kg, and are easy to use. Their main disadvantages are they are highly flammable, they generate waste in large volumes and the sorbent material cannot be recycled.
By contrast, Grafysorber is eco-friendly, inflammable, free of toxic compounds (as it is derived from natural graphite - carbon content in form of crystalline graphite at least 98%) and has maximum adsorption capacity of 80-90 kg/kg. It facilitates recovery of sorbed oil (at least 80%), and the exhausted product can be re-used in asphalts.
The mechanical devices most commonly used for oil spills clean-up are skimmers which can be effectively used for medium viscosity oils. However, for thinness slicks or low viscosity hydrocarbons, they have a lower oil recovery rate. Grafysorber serves as an ideal replacement for skimmers, particularly in cleaning oil sheen present in low viscosity oils (diesel and unleaded petrol).
Oil spill clean-up with Basic G+
Oil-Spillage Clean Up with Basic G+
Video credit: Directa Plus / YouTube
Grafysorber for Removing Hydrocarbons from Produced Water
Produced water is usually a waste product in the petroleum industry. Water management and cost control can be performed based on the selection of a suitable water disposal options or through effective use of produced water. Waste options and uses can be chosen with respect to the water quality, and may require proper water treatment before use or disposal.
Produced water treatment should be carried out to meet the pre-disposal regulatory limits or beneficial use specifications. Upon using a low-cost disposal option, like discharge to surface waters, the produced water must satisfy or exceed limits set by regulators for key parameters.
The following are the three categories of produced water treatment services for de-oiling:
- Physical – this is the basic category service which includes sand filters, cyclones and physical adsorption
- Chemical – this includes electrochemical process, oxidation and precipitation
- Membrane – this includes polymeric and inorganic membrane market
Grafysorber is defined as a "Physical Treatment" and must be compared with this type of treatment technology. The Physical Treatment Technologies Separators are classified as follows:
- Primary – Hydrocyclone, CPI (plates), Skimmers. These methods can reduce the concentration of hydrocarbons from 2000-500 ppm to 150-50 ppm.
- Secondary – IGF (flotation) eliminates hydrocarbons from 150-50 ppm to 100-25 ppm
- Tertiary – Membrane, Walnuts filters, Fiber coalesce, Centrifuge. These methods can remove hydrocarbons down to 20-5 ppm.
Water from Tertiary Separators can be treated using filters, membranes or chemicals to reduce the concentration of pollutants down to the more restrictive limits.
Grafysorber can be a good replacement of all primary, secondary and tertiary treatments due to its high adsorption capacity and ability to reduce Total Petroleum Hydrocarbon concentrations down to 0.5 ppm or even lower in just a few minutes of contact.
Grafysorber for Site Remediation and Contaminated Ground Water
Remediation of contaminated aquifers has gained interest during the last decade. Treatment technologies are classified into the following categories:
- In-site technologies – water is treated with biological products and chemicals without being removed from the aquifer. The main advantage of this method is low operation costs, which is restricted to the cost of the decontaminant product. However, treatment of the whole aquifer is the major limitation of this method.
- On-site technologies – water is treated with different technologies after being pumped from the aquifer. Pump-and-treat is one of the most common technologies for cleaning up a contaminated aquifer. In this method, extraction wells are introduced at different locations in a contaminated aquifer, where the contaminants are removed using pumped water.
Contaminants are subsequently removed from the pumped water through various technologies. Following treatment, the groundwater is either discharged into a surface water body (such as a river or lake), in municipal sewage plants, or re-injected into the aquifer. The advantages of the pump-and-treat technology are the chances of whole aquifer remediation and high efficiency. The major disadvantage is the cost of equipment.
Thanks to its higher adsorption capacity for hydrocarbons and oils, Grafysorber can be used instead of traditional Activated Carbons in pump-and-treat equipment during treatment. The same process could be applied in other types of natural or artificial superficial basins that are contaminated with hydrocarbons.
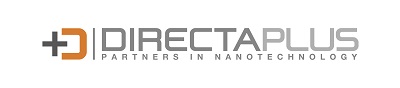
This information has been sourced, reviewed and adapted from materials provided by DIRECTA PLUS S.p.A.
For more information on this source, please visit DIRECTA PLUS S.p.A.