Atomic Force Microscopy (AFM) is an analytical tool applied for nanoindentation testing of materials, which assesses the resolution and depth at micro or nanoscale.
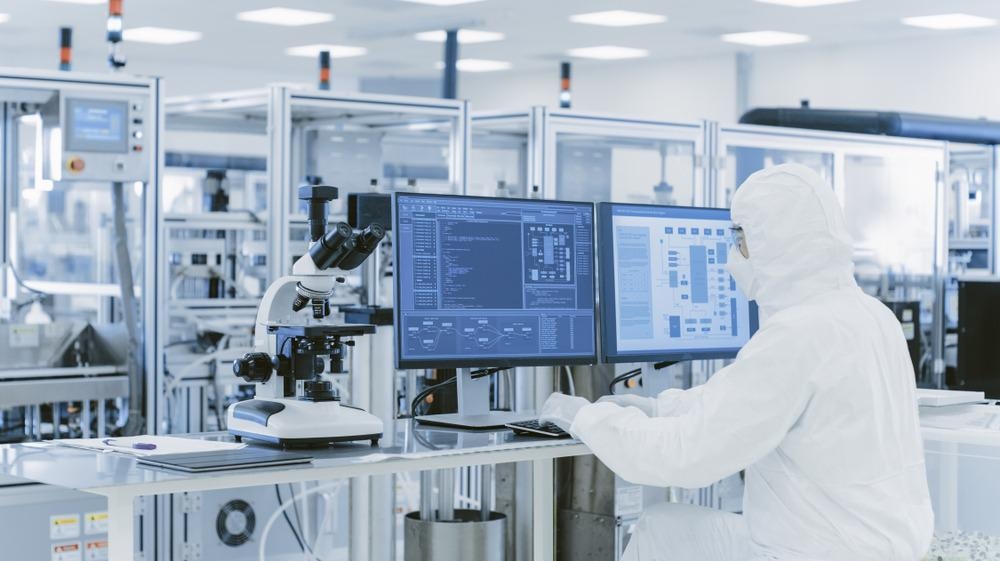
Image Credit: Gorodenkoff/Shutterstock.com
Although the tool was initially developed to image non-conducting samples, its application was later realized in surface characterization at the nano and micro scale.
AFM analyzes both the physical properties and the topography of material in parallel and without any dedicated instruments.
It operates on three modes: the tapping mode, the contact mode, and the non-contact mode. These operation modes of AFM are characterized based on the analysis and the sample requirement.
AFM’s soft tip allows the calculation of displacement-load curves, applied to the indentation imaging that enables evaluation of the mechanical properties of materials.
A commercially available AFM technology comprises a piezo-driven mode, which uses a nanoindenter tip for material topography imaging.
AFM images of a projected area obtained from the indenter tip measure values are useful for calculating the indentation hardness at a constant maximum indentation pressure.
How Nanoindentation is Performed?
Nanoindentation is a general method of characterizing the physical properties of nanoscale materials.
AFM nanoindentation can control shallow indentation depth and load, and effective contact volume. It is performed by indenting a hard tip of known size and geometry into the sample material under a short influence of pressure.
The pressure is increased with the tip’s penetration into the sample material until it approaches the user-assigned value. Once this value is reached, the pressure is either removed or held constant.
Nanoindentation gives a curve series of indentation load-displacement (P-h), from which hardness and Young’s modulus are characterized. One of the common methods to perform nanoindentation is presented by, which is applied to the geometry of cube-corner indenter.
It assumes a response of an isotropic compound and discounts impacts of sink-in and mechanisms of time-constrained deformation. Nanoindentation techniques that apply AFM are commonly used to analyze the physical properties of soft solids, such as biological samples, polymers, hydrogels, 2D nanosheets, and polymer-MOF nanocomposites.
Current Application of AFM-based Nanoindentation
AFM nanoindentation has application in surface height topology mapping and 3D high-resolution imaging, notably in facilitating in situ quantification of the residual indents’ shape.
Its applications are explored in the characterization of crystals and compounds that cannot be done by applying the traditional instrumented nanoindentation method. An AFM-related nanoindentation method, supplemented with an intender tip calibrated with a diamond cube corner, has applications in measuring materials’ adhesion energy, fractural strength, hardness, interfacial strength, and Young’s modulus.
Using Veeco Dimension 3100 equipment, the AFM-related nanoindentation can perform the analyses in the presence of a Bruker PDNISP probe and under the indentation mode.
It is also applicable in analyzing nanocrystals’ mechanical properties for a broad range of unloading strain rates. Another advantage of AFM-based nanoindentation is that easily deforms the porous MOF structures by its better load sensitivity, which is three order magnitude sensitive than that of a traditionally instrumented nanoindenter.
AFM-based nanoindentation possesses a magnificent advantage over traditionally equipped nanoindentation methods in enabling quantitative analysis of nano or microcrystals and directly measuring the physical behavior of a single nanocrystal of the metal-organic framework (MOF) based materials.
Challenges and Future
The crystal engineering community has used the instrumented nanoindentation method to quantify the hardness and Young’s modulus of crystals; the method demands large crystals (>~100 µm).
However, MOF crystals of general interest can only be synthesized in micro and nanoscale particles rather than a large single crystal.
Such samples are inadequate and tedious to characterize. Nanoindentation methods have been applied to produce polycrystalline MOF coatings and films of µm-thickness. However, the data obtained from the method are semi-quantitative since the bulk substrate interferes with the indentation measurements.
Quantification of data still faces some challenges because conditions extensively impact measurement precision.
Other notable challenges of the technique include: (i) incorrect contact area and distorted displacement-force curve due to a damaged tip, (ii) a smooth, flat surface that influences accurate determination of contact area, (iii) indentation from the use of AFM probe having big tip angle, but at the cost of poor 3D imaging resolution, and (iv) data reproducibility and quality due to viscoelasticity, indentation effects, and adhesive interactions while indenter unloading.
With these challenges addressed, the future scope of AFM nanoindentation has magnificent chances of being preferred over the traditional instrumented nanoindentation method in investigating nanocrystal and thin-film samples’ physical properties.
Continue reading: Non-Destructive Testing and Investigating Polymer Nanocomposites
References and Further Reading
Alessandrini, A. and Facci, P., (2005) AFM: a versatile tool in biophysics. Measurement Science and Technology, 16(6), pp.R65-R92.doi:10.1088/0957-0233/16/6/R01
Bundschuh, S., Kraft, O., Arslan, H., Gliemann, H., Weidler, P., & Wöll, C. (2012). Mechanical properties of metal-organic frameworks: An indentation study on epitaxial thin films. Appl. Phys. Lett. doi:10.1063/1.4751286
Cohen, S. R., & Kalfon-Cohen, E. (2013). Dynamic nanoindentation by instrumented nanoindentation and force microscopy: a comparative review. Beilstein J Nanotechnol. doi:10.3762/bjnano.4.93
Eslava, S., Zhang, L., Esconjauregui, S., Yang, J., Vanstreels, K., Baklanov, M., & Saiz, E. (2013). Metal-Organic Framework ZIF-8 Films As Low-κ Dielectrics in Microelectronics. Chem. Mater. doi:10.1021/cm302610z
Ferencz, R., Sanchez, J., Blümich, B., & Herrmann, W. (2012). AFM nanoindentation to determine Young’s modulus for different EPDM elastomers. Polymer Testing. doi:10.1016/j.polymertesting.2012.01.003
Garcia, R. (2020). Nanomechanical mapping of soft materials with the atomic force microscope: methods, theory and applications. Chem. Soc. Rev. doi:10.1039/D0CS00318B
Möslein, A., & Tan, J.-C. (2021). Vibrational Modes and Terahertz Physical Phenomena Underpinning ZIF-71 Metal-Organic Framework. https://arxiv.org/abs/2112.00813
Oliver, W., & Pharr, G. (2004). Measurement of hardness and elastic modulus by instrumented indentation: Advances in understanding and refinements to methodology. Journal of Materials Research. doi:10.1557/jmr.2004.19.1.3
Sirghi, L., & Rossi, F. (2006). Adhesion and elasticity in nanoscale indentation. Appl. Phys. Lett. doi:10.1063/1.2404981
Voorde, B., Ameloot, R., Stassen, I., Everaert, M., Vos, D., & Tan, J.-C. (2013). Mechanical properties of electrochemically synthesised metal–organic framework thin films. J. Mater. Chem. C. doi:10.1039/C3TC31039F
Zeng, Z., & Tan, J.-C. (2017). AFM Nanoindentation To Quantify Mechanical Properties of Nano- and Micron-Sized Crystals of a Metal–Organic Framework Material. ACS Appl. Mater. Interfaces. doi:10.1021/acsami.7b13402
Disclaimer: The views expressed here are those of the author expressed in their private capacity and do not necessarily represent the views of AZoM.com Limited T/A AZoNetwork the owner and operator of this website. This disclaimer forms part of the Terms and conditions of use of this website.