Photolithography is a fabrication process with a wide range of industrial applications, ranging from manufacturing microelectronics and micro-electro-mechanical components to thin film patterning for biosensors, and many others.
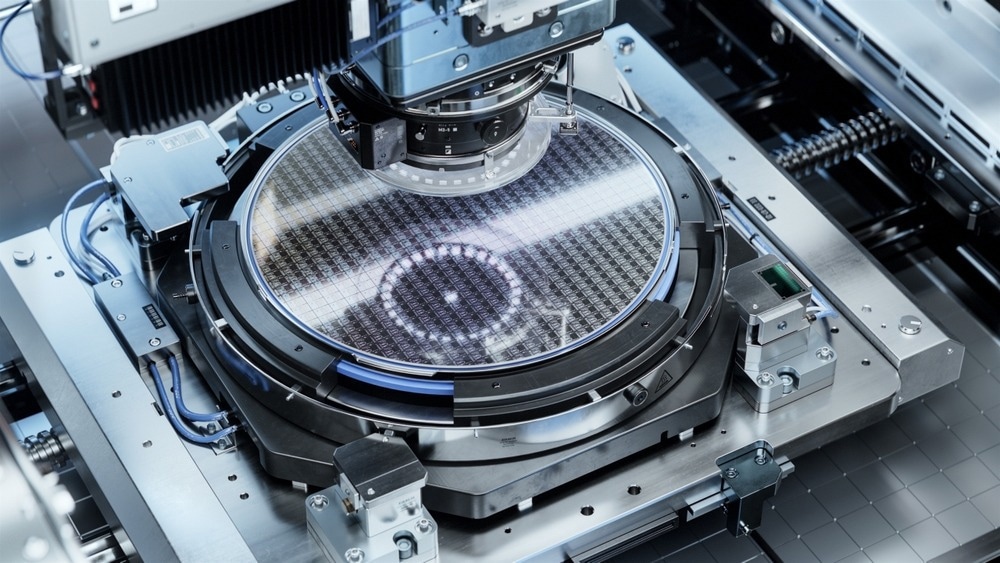
Image Credit: PastryShop/Shutterstock.com
The process utilizes ultraviolet (UV) light to expose complex geometric shapes and patterns onto a light-sensitive photoresist coating and transfer them to the undelaying substrate. This article aims to provide an overview of the photolithography process and information about each step of the process.
Photolithography is a patterning process where a photosensitive polymer is selectively exposed to light through a mask, thus creating a latent image (or pattern) in the polymer that can then be developed and selectively dissolved to expose the desired parts of the underlying substrate.
Basics of the Photolithography Process
In the photolithography process, a light source and collimating optical system are used to create an image of a patterned mask onto a substrate coated with a photosensitive polymer layer (photoresist). This illuminated pattern is then transferred into the substrate by a subsequent etching process.
Thin silicon wafers are utilized as substrates in most photolithographic applications. The entire process comprises several steps executed sequentially at specific conditions and for a certain duration, depending on the desired outcome of the patterning process.
It is worth noting that photolithography works best on flat substrates, and the process is unsuitable for patterning high-curvature surfaces and creating complex 3D structures.
Key Steps in Photolithography
The photolithographic process involves substrate preparation, photoresist application, soft baking, mask alignment, exposure and development, post-exposure baking, and pattern transfer (etching or replica molding).
Substrate Preparation
In the first step, the wafer is baked at elevated temperatures (200 - 400°C) for 30 - 60 minutes to evaporate any water present on the surface. Next, any particulate matter and any traces of organic, ionic, and metallic impurities are removed from the wafer surface. The cleaning process depends on the physical and chemical properties of the substrate materials and can involve wet cleaning (chemical bath) or dry-cleaning steps (plasma cleaning or UV irradiation).
The purpose of this step is to prepare the substrate to accept the photoresist by providing a clean, highly adhesive surface. Depending on the type of substrate and photoresist, a barrier layer (usually silicon dioxide) or adhesion promoter might be deposited on the cleaned wafer surface.
Photoresist Coating
After the wafer preparation, a uniform layer of photoresist is applied to the wafer surface. Most industrial photolithographic processes employ the spin coating technique, where the substrate rapidly rotates. The centrifugal force spreads evenly the photoresist solution, followed by solvent evaporation and formation of a uniform thin photoresist layer (0.1 – 10 μm in thickness).
Two types of photoresists can be employed to transfer the pattern onto the substrate. When using a positive-tone photoresist, the exposed region of the photoresist becomes soluble to the photoresist developer. This type of photoresist enables higher spatial resolution and better control of the sidewall roughness of the patterned structures.
In contrast, upon exposure to light, a negative-tone photoresist crosslinks and becomes insoluble during the development step. This type of photoresist is employed when high-aspect-ratio features are needed (and require thick resist layers).
Soft Baking
During the soft baking step, most of the solvent is removed from the photoresist. This step is very important as it renders the resist layer photosensitive. Positive resists might be incompletely exposed if a significant amount of residual solvent is present in the coating.
Under-baked positive resists can be attacked by the developer in both exposed and unexposed areas, degrading the etching resistance of the exposed resist. Overbaking at this stage can degrade the photosensitivity of the resist by damaging the photosensitizer molecules in the resist layer.
Photomask Alignment and Pattern Exposure
Typically, the photomask is a quartz or glass plate patterned with the desired features, usually as a metal (chromium or molybdenum) coating. The mask can have a repeating pattern that covers the entire wafer, thus creating a large number of identical patterns (or dies), or cover a small portion of the wafer and create just a few dies (such masks are known as reticules).
The mask or the reticule needs to be aligned and locked into the photolithographic equipment. When a reticule is used, it is translated stepwise parallel to the wafer surface, exposing a small portion of the wafer with each step. This type of photolithographic equipment is called a 'stepper'.
The mask pattern can be transferred through direct contact, proximity, or projection exposure. In the case of direct contact, the mask is placed directly onto the photoresist surface, resulting in high spatial resolution but also increasing the risk of mask damage and reducing the process throughput. Proximity exposure keeps the mask a short distance away from the photoresist, resulting in lower spatial resolution. In projection exposure, an optical system forms a scaled-down image of the mask onto the resist surface.
Modern photolithographic processes employ catadioptric projection optics, consisting of both refractive (lenses) and reflective (mirrors) elements, together with deep-UV (193 nm) or extreme-UV (13.5 nm) light sources to produce pattern features with characteristic dimensions of less than 10 nm.
The development is a wet process that dissolves areas of the photoresist using a developer (combination of solvents, such as tetramethylammonium hydroxide, and surfactants). The duration of the development process is critical, as underdeveloped resist could prevent access to the underlying substrate by leaving a residual resist layer on the wafer. Conversely, an overdeveloped resist can distort the pattern transferred to the wafer. To terminate the development process, the wafer is rinsed with deionized water and spin-dried.
Post-Exposure Baking and Pattern Transfer
Finally, the photoresist is subjected to a baking process to harden and strengthen the remaining resist material so that it can withstand the following pattern transfer steps without feature degradation. At this point, the photolithographic process is complete, and the wafer is ready for wet or dry etching, selective metal deposition, ion implantation, or used for replica molding.
References and Further Reading
Madou, M., Wang, C. (2012). Photolithography. In: Bhushan, B. (eds) Encyclopedia of Nanotechnology. Springer, Dordrecht. Available at: https://doi.org/10.1007/978-90-481-9751-4_342
Naulleau, P. (2019) Optical Lithography, In: Andrews, D. L., Lipson, R. H., Nann, T. (eds.) Comprehensive Nanoscience and Nanotechnology (Second Edition), Academic Press, 387-398. Available at: https://doi.org/10.1016/B978-0-12-803581-8.10433-3
Disclaimer: The views expressed here are those of the author expressed in their private capacity and do not necessarily represent the views of AZoM.com Limited T/A AZoNetwork the owner and operator of this website. This disclaimer forms part of the Terms and conditions of use of this website.