Sep 4 2007
Slim, elegant and casual it rests on its inclined legs. Its creator enjoys worldwide acclaim, its forerunners are design icons: the object of interest is the "Myto" cantilever chair – the brainchild of much celebrated designer Konstantin Grcic. This supreme example of seating furniture is made completely of the new injection moldable plastic Ultradur® High Speed from BASF and will be exhibited at the world's largest plastics show "K" in Düsseldorf in October. "The chair's delicate design combined with its high strength was only possible with this material," says Konstantin Grcic. "It gives me completely new freedom for the design".
The really special thing about Ultradur® High Speed is that it flows twice as far as standard plastic grades when heated. This makes the production of components made of Ultradur® High Speed more cost-effective and energy-efficient, which is why this innovative material has been awarded the eco-efficiency seal.
A vast array of components is manufactured by the injection molding technique – hundreds of different articles without which our daily life would scarcely be conceivable. This includes household items such as electric irons, shower heads and fryer lids or industrial components, especially for the automotive and electrical industries. Exterior car mirrors, plug connectors and electronic boxes for antilock braking control systems (ABS) or electronic stability programs (ESP) – all these parts are made of molded plastic. The starting material used to produce them consists of plastic granules which are melted by heat and then injected into a cavity known as a mold. The plastic assumes the shape of the mold, solidifies again on cooling and can then be removed for further processing.
BASF has for many years been one of the largest suppliers of injection moldable plastics. It has now upgraded its well-proven product line Ultradur® – chemical name polybutylene terephthalate (PBT) – into "Ultradur® High Speed" by adding finely distributed organic nanoparticles to the plastic. The additive allows the plastic to be processed at 230C instead of 260C and improves its flowability by 50 percent. But its mechanical properties – shrinkage and heat distort resistance – are scarcely affected.
With these properties, Ultradur® High Speed offers major advantages both in terms of cost and environmental friendliness. The plastic can be processed at lower temperatures. Only half as much pressure is needed to fill the material into the mold. This also means that much less energy is needed. "Altogether one fifth of the energy can be saved," says Dr. Andreas Eipper, BASF plastics expert and product manager for Ultradur®. "If all injection molding machines were converted from standard grade PBT to Ultradur® High Speed, an amount of energy equivalent to that consumed by 75,000 automobiles a year could be saved". The quantity of material needed also decreases because the mold is easier to fill with the easy-flow plastic. Fewer undesired air inclusions appear which means a lower rate of product rejects. Ultradur® High Speed also increases productivity. And because it is processed at lower temperatures, the injection molded parts need not be cooled for so long. The hourly output increases – by up to 30 percent.
Last but not least, Ultradur® High Speed helps improve the quality of the products. The easy-flow plastic can be reinforced with much higher glass fiber content than before. This allows thinner walled parts to be produced that are also very strong – as with the "Myto" cantilever chair. "We can now produce much more intricate and complicated components," says Martin Plank, owner and founder of the Italian furniture company Plank that made the chair. "Previously this was only possible by using expensive high-performance plastics. With this innovative material, the surface of the mold is also transferred exactly to the product." Large, complex parts also need fewer injection points. This reduces the costs of expensive injection molding tools which improves the customer's competitiveness.
Because of the numerous advantages it offers, Ultradur® High Speed has been awarded an eco-efficiency seal. "The prefix 'eco' stands for both economy and ecology," explains Konrad Hungerbühler. "The seal signifies that the material performs better than conventional PBT in both economic and ecological terms." Hungerbühler is Professor of Safety and Environmental Technology at the Swiss Federal Institute of Technology in Zurich. He has evaluated and confirmed the analysis in an expert report.
The Prospects
Ultradur® High Speed was launched at the end of 2004 and was very well accepted by customers. The demand is so intense that BASF is now offering the entire Ultradur® portfolio in the "High Speed" quality. Twenty ongoing series applications, including the housing for the steering wheel lever of the BMW Mini Cooper, mountings for rear windshield wipers, parts for sensor housings and laptop plugs are all made using this innovative plastic. The Ultradur® High Speed portfolio comprises 15 product variants designed for different applications. It includes a particularly thermally conductive Ultradur® that can be used, for example, in housing parts or sockets of light fixtures. Other products are laser printable or feature high flame retardance.
Ultradur® High Speed now allows the optimal utilization of new applications and techniques. One of them is water injection technology, a special injection molding technique for producing molded parts with a hollow cross section. This technology is suitable for producing hollow structures with long flow paths such as car roof rails or kitchen stove handles for which conventional injection molding tools are inadequate. Another example is the dolphin process for producing automotive instrument panels in a particularly cost-effective manner from several layers of rigid and foamed plastic. In this case the nanoparticles in Ultradur® High Speed provide better bonding of the soft component.
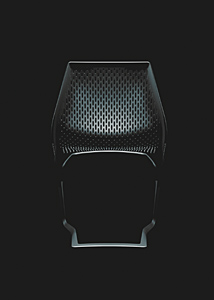
The Info Box
How nanoparticles change the flow properties Or: Everything on the move thanks to nanotechnology
The innovation of Ultradur® High Speed lies in adding to the polybutylene terephthalate (PBT) finely distributed nanoparticles with diameters of only 50 to 300 nanometers – with one nanometer (a millionth of a millimeter) being equivalent to the length of four adjacent atoms in a piece of metal. Nanoparticles can greatly influence the properties of a material: essentially, they perform the same function as the tree trunks on which the ancient Egyptians rolled the mighty stones for their pyramids across country – although with Ultradur® High Speed it is the long polymer chains of the injection molded plastic that have to be moved. In this way, these patented tiny particles developed in BASF's central polymer research lab drastically reduce the viscosity of the plastic melt, thereby reducing the required processing temperature.
BASF's development scientists had the task not only of determining the optimal particle sizes, but also of developing processes for distributing them evenly throughout the plastic matrix. Only the combination of a high-tech additive and the special admixing technique modifies the rheology of a plastic so profoundly and opens up the many new applications of Ultradur® High Speed.