By JanakyReviewed by Lexie CornerUpdated on Sep 17 2024
Advanced materials play a vital role in the performance, safety, durability, and efficiency of aircraft and spacecraft. As aerospace technology advances, there is a growing need for materials that are lighter, stronger, and more resistant to extreme conditions.1
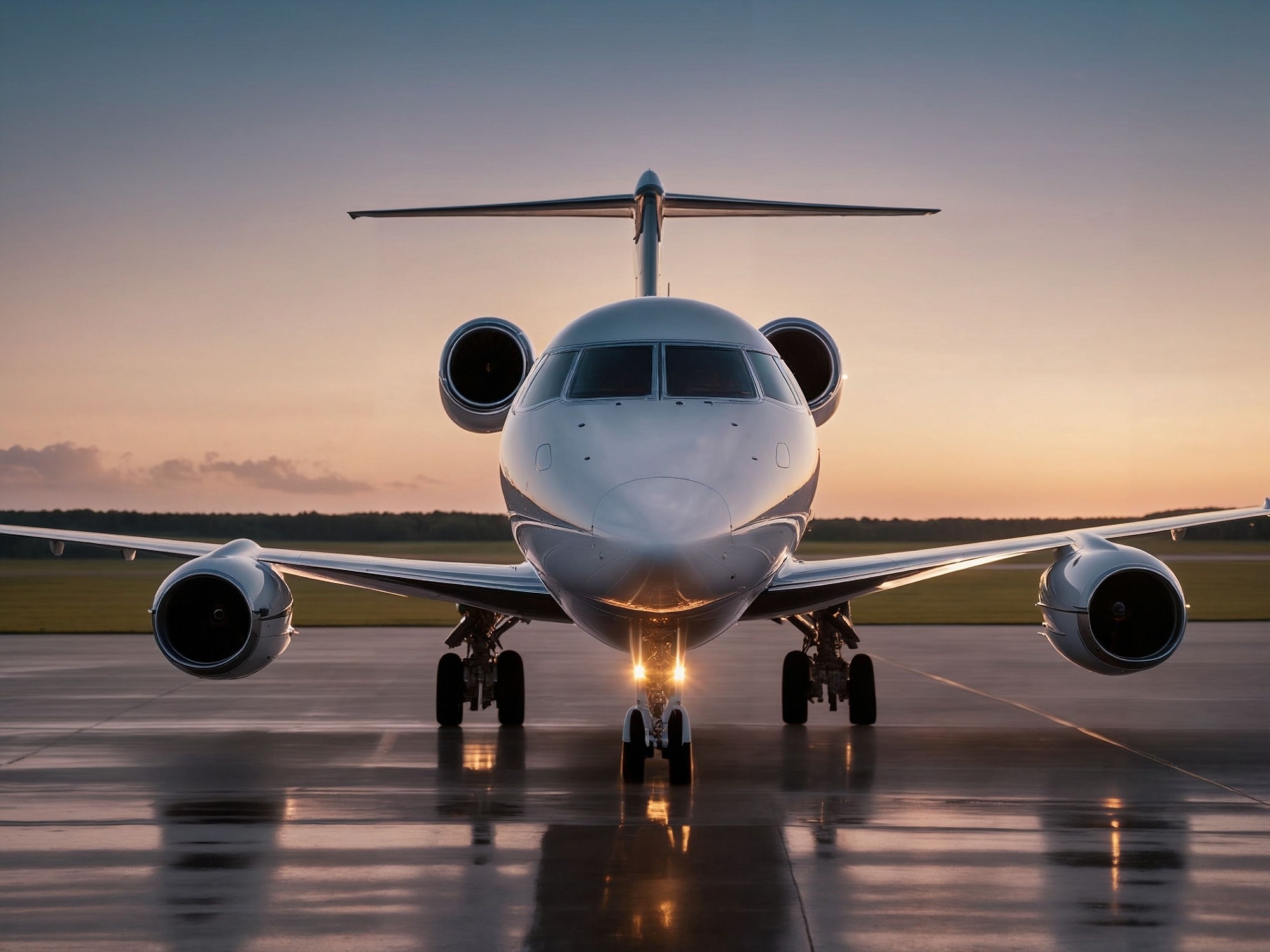
Image Credit: Lanzelot/Shutterstock.com
Nanotechnology offers innovative solutions by modifying material properties at the atomic or molecular level, enabling groundbreaking advancements in aerospace materials.2
Enhancing Material Properties Through Nanotechnology
Nanotechnology alters material properties by manipulating structures at the nanoscale (typically less than 100 nanometers), resulting in a high surface-to-volume ratio and quantum size effects.3 These nanoscale changes can make them well-suited for aerospace applications.
Lightweight materials are critical in aerospace, as reducing an aircraft's weight improves fuel efficiency, lowers carbon emissions, and reduces costs.1 The challenge for engineers is to decrease weight without compromising safety or structural integrity. Nanomaterials (NMs) address this issue by enabling the creation of lighter, stronger composites for aircraft construction.2
This reduces the overall material needed to meet performance standards, further decreasing weight.2 Additionally, NMs enhance stiffness, strength, and durability while enhancing thermal management, contributing to efficiency and safety in demanding environments.
NMs have promising applications beyond traditional composites, especially with advancements in additive manufacturing like 3D printing.4 Incorporating NMs into 3D-printed thermoplastics allows for the rapid production of both critical and non-critical aircraft components with enhanced mechanical strength and durability.
NMs Used in Aerospace Engineering
Several NMs, such as nanotubes (NTs), graphene, and nanoparticles (NPs), are used in the aerospace industry. Each offers unique properties that significantly enhance flight vehicle performance.2
NTs are cylindrical nanostructures with remarkable strength and electrical conductivity. Carbon NTs, for example, are often used to reinforce composite materials in aircraft frames and engine components. Their incorporation can reduce weight while maintaining structural integrity, which in turn can improve fuel efficiency and the overall performance of the aircraft.
Boron nitride NTs, known for their high thermal stability and electrical insulation properties, are ideal for thermal protection systems, rocket nozzles, and engine components in spacecraft.5 These NTs shield spacecraft from aerothermal flux during re-entry, maintaining structural integrity.5 Recent studies also suggest that advanced materials such as aluminum reinforced with boron nitride are used to fabricate complicated wing models for aircraft.6
Graphene, a carbon allotrope with high electrical conductivity, protects airplanes from lightning strikes and is widely used in protective coatings to prevent oxidative damage and environmental degradation, thus extending the lifespan of aircraft components.7 Graphene-based sensors also provide advanced capabilities for monitoring the structural health of aerospace materials, allowing for early detection of damage or stress.
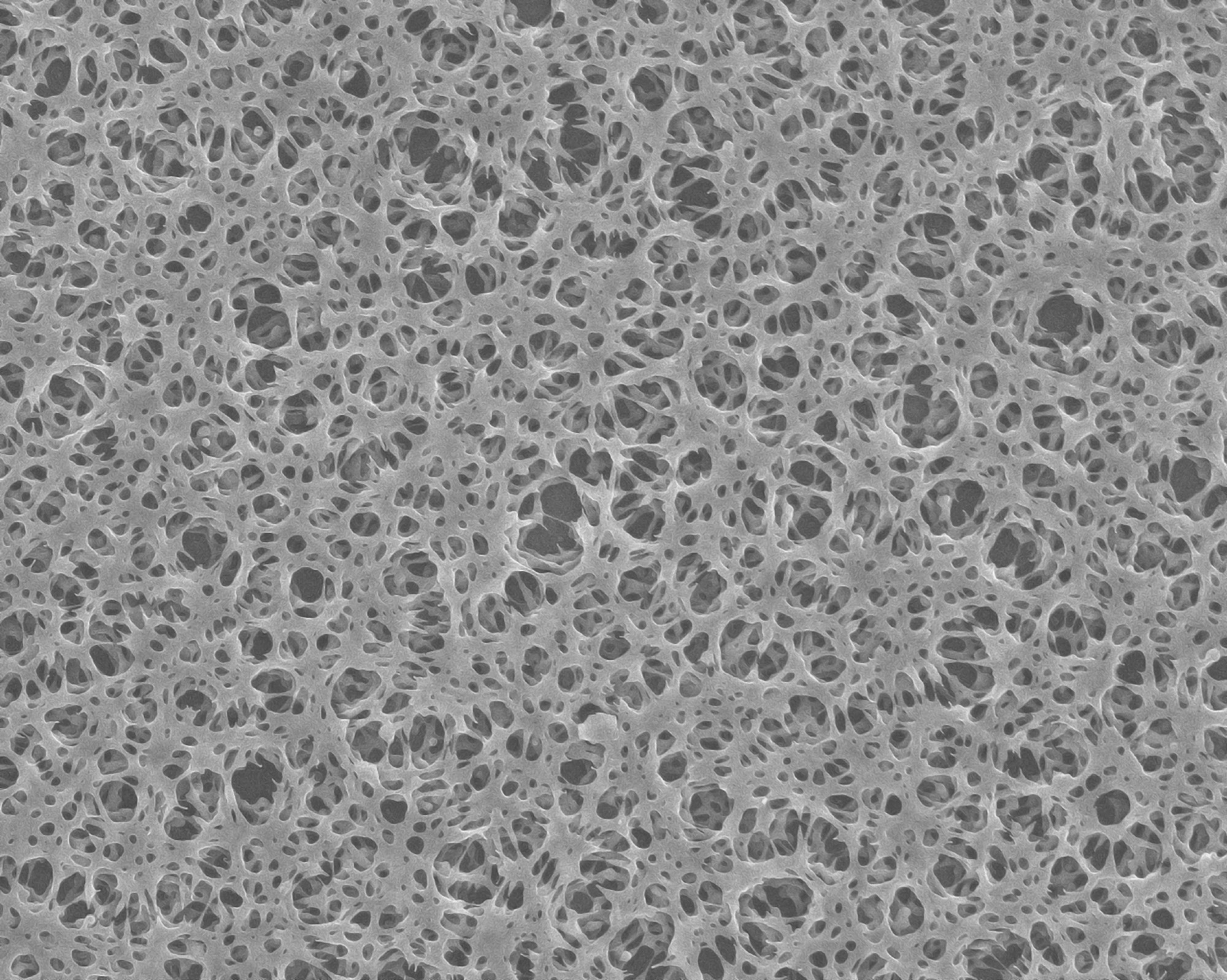
Image Credit: DooDee Studio/Shutterstock.com
Silver NPs are incorporated into antimicrobial coatings and filters to maintain sterile environments within aircraft and spacecraft. Their strong antimicrobial properties are crucial for preventing microbial growth and safeguarding crew health and mission integrity.2
Silicon carbide NPs are employed in high-temperature components, such as jet engines.8 They are also used in many aircraft parts, including turbine bearings, brake disks, turbine blades, nose caps, and nozzles. 9
Titanium dioxide NPs are used in aircraft and engine parts, often incorporated into photocatalytic and self-cleaning coatings.2 These coatings break down organic pollutants and protect against UV radiation, significantly reducing maintenance requirements, especially for vehicles operating at high altitudes or in space.2
Applications in Aircraft Performance and Durability
NMs provide considerable benefits in aircraft performance by offering protection against environmental hazards like lightning strikes and ice buildup. By incorporating conductive NMs like graphene into aircraft structures, engineers are developing lightweight alternatives that can effectively dissipate electrical energy from lightning, minimizing the risk of structural damage.10
Additionally, incorporating NMs into aircraft components helps prevent ice accumulation, ensuring aerodynamic efficiency.10 These enhancements not only improve flight safety but also reduce the risk of hazardous in-flight conditions.
Thermal and fire resistance are crucial for aircraft and spacecraft, especially those designed for high-performance and multifunctional applications.1 NMs, such as nanopolymers and graphene, exhibit high heat resistance, making them well-suited for advanced thermal protection systems.2
Nanostructured ceramics and aerogels provide excellent insulation, protecting sensitive electronics and structural components from the intense heat experienced during high-speed travel and atmospheric re-entry.2 These are vital for preserving the functionality and integrity of critical components under extreme conditions.
The superior mechanical properties of NMs, such as increased tensile strength and wear resistance, also enhance the durability of aircraft parts, reducing the need for frequent replacements and maintenance.2 In addition to improving safety, this enhanced durability results in long-term cost savings and more consistent aircraft performance.2
NMs also improve passenger comfort by reducing vibrations throughout the aircraft, which helps lower cabin noise levels.
Recent Advancements and Research
While nanotechnology offers many advantages for aerospace engineering, several challenges must be addressed to harness its complete potential. Such concerns include safety, cost, and long-term impact of extensive use.11
If not properly managed, NMs can be toxic, posing health risks to workers handling them. Current research is focused on understanding the long-term environmental effects of NMs, which remain relatively unexplored due to their recent development.
Despite these challenges, nanotechnology continues to find new applications in aerospace. Research is focused on developing multifunctional NMs that are not only strong and lightweight but also capable of self-healing and adapting to environmental changes.4
Current studies are also exploring the integration of nanosensors into aerospace structures to monitor real-time stress, corrosion, or damage, supporting proactive maintenance and flight safety management.12 Additionally, researchers are investigating ways to enhance the efficiency of aerospace electronics and displays by leveraging nanotechnology, ultimately reducing energy consumption and improving system performance.
Highlights and Future Trends
Nanotechnology has become crucial in advancing aerospace materials, providing significant benefits in strength, weight reduction, thermal resistance, and durability. Nanoscale manipulation has enabled the development of advanced composites, coatings, and sensors that enhance the overall performance and efficiency of aircraft and spacecraft.2
An article in Nanotechnology Reviews explores the potential for continued innovation in nanocomposites, highlighting ongoing improvements in aerospace technology and future advancements in air and space exploration.13
The integration of advanced NMs and NM-based additive manufacturing could revolutionize aerospace design, making air and space travel safer, more efficient, and environmentally sustainable.4 The future of nanotechnology in aerospace materials promises far-reaching, innovative breakthroughs.
Discover More: The Versatility of Non-Contacting Seals in Aerospace
References and Further Reading
- Boyer, RR., Cotton, JD., Mohaghegh, M., Schafrik, RE. (2015). Materials considerations for aerospace applications. MRS Bulletin. DOI: 10.1557/mrs.2015.278, https://www.cambridge.org/core/journals/mrs-bulletin/article
- Abbasi, S., Peerzada, MH., Nizamuddin, S., Mubarak, NM. (2020). Functionalized nanomaterials for the aerospace, vehicle, and sports industries, Handbook of functionalized nanomaterials for industrial applications. DOI: 10.1016/B978-0-12-816787-8.00025-9, https://www.sciencedirect.com/science/article/abs/pii/B9780128167878000259
- Onyia, AI., Ikeri, HI., Chima, AI. (2020). Surface and quantum effects in nanosized semiconductor. American Journal of Nano Research and Applications. DOI: 10.11648/j.nano.20200803.11, https://d1wqtxts1xzle7.cloudfront.net/90495335/10.11648.j.nano.20200803.11-libre.
- Rahman, M., et al. (2024). A review on nanomaterial-based additive manufacturing: Dynamics in properties, prospects, and challenges. Progress in Additive Manufacturing. DOI: 10.1007/s40964-023-00514-8, https://link.springer.com/article/10.1007/s40964-023-00514-8
- Jakubinek, MB., Kim, KS., Kim, MJ., Martí, AA., Pasquali, M. (2022). Recent advances and perspective on boron nitride nanotubes: From synthesis to applications. Journal of Materials Research. DOI: 10.1557/s43578-022-00841-6, https://link.springer.com/article/10.1557/S43578-022-00841-6
- Ninh, DG., et al. (2023). A new study for aeroplane wing shapes made of boron nitride nanotubes-reinforced aluminium, Part I: review, dynamical analyses and simulation. Composite Structures. DOI:10.1016/j.compstruct.2022.116239. https://www.sciencedirect.com/science/article/pii/S0263822322009710
- Kulyk, B., et al. (2022). A critical review on the production and application of graphene and graphene-based materials in anti-corrosion coatings. Critical Reviews in Solid State and Materials Sciences. DOI: 10.1080/10408436.2021.1886046, https://www.tandfonline.com/doi/full/10.1080/10408436.2021.1886046
- Ponraj, JS., Dhanabalan, SC., Attolini, G., Salviati, G. (2016). SiC nanostructures toward biomedical applications and its future challenges. Critical Reviews in Solid State and Materials Sciences. DOI: 10.1080/10408436.2016.1150806, https://www.tandfonline.com/doi/abs/10.1080/10408436.2016.1150806
- Wang, X., et al. (2021). Advances in modifications and high-temperature applications of silicon carbide ceramic matrix composites in aerospace: A focused review. Journal of the European Ceramic Society. DOI: 10.1016/j.jeurceramsoc.2021.03.051. https://www.sciencedirect.com/science/article/pii/S0955221921002120
- Alemour, B., Badran, O., Hassan, MR. (2019). A review of using conductive composite materials in solving lightning strike and ice accumulation problems in aviation. Journal of Aerospace Technology and Management. DOI: 10.5028/jatm.v11.1022, https://www.scielo.br/j/jatm/a
- Haynes, H., Asmatulu, R. (2013). Nanotechnology safety in the aerospace industry. In Nanotechnology Safety. DOI: 10.1016/B978-0-444-59438-9.00007-2, https://www.sciencedirect.com/science/article/abs/pii/B9780444594389000072
- Javaid, M., Haleem, A., Singh, RP., Rab, S., Suman, R. (2021). Exploring the potential of nanosensors: A brief overview. Sensors International. DOI: 10.1016/j.sintl.2021.100130, https://www.sciencedirect.com/science/article/pii/S2666351121000516
- Bhat, A., Budholiya, S., Aravind Raj, S., Sultan, MTH., Hui, D., Md Shah, A. U., Safri, SNA. (2021). Review on nanocomposites based on aerospace applications. Nanotechnology Reviews. DOI: 10.1515/ntrev-2021-0018, https://www.degruyter.com/document/doi/10.1515/ntrev-2021-0018/html
Disclaimer: The views expressed here are those of the author expressed in their private capacity and do not necessarily represent the views of AZoM.com Limited T/A AZoNetwork the owner and operator of this website. This disclaimer forms part of the Terms and conditions of use of this website.