Micro-Electro-Mechanical Systems (MEMS) consists of both mechanical and electrical parts. Therefore, both electrical and mechanical properties need to be quantitatively characterized to ensure reliable MEMS testing (Figure 1). This process is critical during the R&D phase and the development of MEMS manufacturing process.
.jpg)
For this article, a FT-MPS02 MEMS Probestation was used to mechanically test microfabricated flexure-arrays on wafer level. The flexure includes a square-shaped pad that was suspended using four springs. The design of the springs allowed the pad to be deflected in both vertical (perpendicular to the wafer plane) and horizontal (inside the wafer plane) planes.
A FT-S1000 Microforce Sensing Probe mounted on the FT-MPS02 was used to measure the vertical stiffness. The horizontal stiffness was measured using a FT-S1000-LAT Lateral Microforce Sensing Probe. Using the force-deflection data obtained from the graph (Figure 2), the linearity could be calculated, in addition to the stiffness value.
.jpg)
Figure 2. Mechanical MEMS Testing
The mechanical properties of the MEMS structures are influenced by several process parameters during development of the micro-manufacturing process. The working flexures (green), and the flexures that are out of the desired specification range (red), can be identified through a chip map. The chip was formed by defining an upper and a lower limit for the target stiffness. By taking the ratio of green and red marks, the yield rate could be easily detected (Figure 3).
.jpg)
Figure 3. Yield Testing of MEMS
Piezoresistive Cantilever Testing
MEMS chips with an array of six cantilevers (Figure 4) are designed to enhance the efficiency of Dip-Pen nanolithography systems. The cantilevers are provided with piezoresistive sensors, which correct the tilt angle between the cantilever array and the sample substrate, and measure the contact force of each cantilever. A Wheatstone bridge is integrated to stabilize the signal.
.jpg)
Figure 4. Electro-mechanical piezoelectric cantilever testing
Stiffness of each cantilever in the array was the first critical parameter to be tested. The compression tests were carried out using the FT-MPS02 MEMS Probestation. The graph shown in Figure 5 illustrates the force-deflection curve for the two cantilevers.
.jpg)
Figure 5. Mechanical testing of two piezoelectric MEMS cantilevers
Four electrical probes were made to contact with the Wheatstone bridge to test the output signals of the cantilevers with respect to the applied force. It was possible to quantify the statistical distribution of the stiffness/sensitivity by repeating the measurements on all cantilever arrays within the wafer. In addition, defective devices can be detected by defining the upper and lower limits for these properties. Figure 6 shows the graph, with good devices marked in green, and devices that do not meet the specifications in red. Eventually, the total yield rate of the manufacturing process could also be calculated.
.jpg)
Figure 6. Wafer map
Piezoelectric Ultrasonic Transducer Testing
The FT-MPS02 MEMS Probestation was used to perform quantitative, in-depth mechanical testing of an ultrasonic transducer array (Figure 7). Using this, both static mechanical and electro-mechanical properties were tested.
.jpg)
Figure 7. Schematic of the Ultrasonic Membrane Actuator
For mechanical testing, the center point of the piezoelectric membrane can be chosen on the camera image. A compression test was carried out when the force sensing probe is automatically triggered to the desired position. The linearity and hysteresis of the resulting force-deflection curve was evaluated. In addition, the topographical height, adhesion force and stiffness of the MEMS chip was determined.
The short- and long-term drift / repeatability and fatigue behavior of the MEMS chip could be calculated through repeated measurements at the same location. The compression test was automatically repeated in a 600 x 600 µm array to form a “compliance map” and a “topography map”, from which geometry of the undeflected membrane, as well as the spatial propagation of the membrane stiffness, can be measured.
The FT-MPS02 MEMS Probestation was mounted with two electrical probes so as to measure the deflection and actuation force of the piezoelectric membranes corresponding to the driving signal. The shape of the deflected membranes was quantified based on the driving signals through topography maps formed at different actuation voltages. Figure 8 and 9 show graphs illustrating the topography of the membrane at an actuation voltage of 0 and 150 V, respectively.
.jpg)
Figure 8. Topographic map of ultrasonic membrane actuator at 0V
.jpg)
Figure 9. Topographic map of ultrasonic membrane actuator at 150V
Electro-Thermal Actuator Testing
MEMS thermal actuators produce motion through thermal expansion amplification. In order to test an electro-thermal actuator design, the temperature was increased by an electrical resistive heating of a series of 6 V-shaped parallel expanding beams in the actuator.
The quantitative characterization of the actuator performance is achieved through combined electro-mechanical testing (Figure 10). This is highly critical as the actuator properties are difficult to simulate as a result of unknown thermal effects (e.g. thermal expansion, thermal boundary conditions) and the large variability in the doping concentration of the silicon wafers.
.png)
Figure 10. Electro-mechanical testing and calibration of a linear thermal MEMS actuator
Two electrical probes were made to contact with the pads over the actuator chips to carry out combined electrical and mechanical testing. The FT-S1000-LAT Lateral Microforce Sensing Probe was used to measure the generated horizontal force and deflection. A non-linear relationship between the input current and actuation movement is achieved. The FT-MPS02 included multimeter was used to measure the non-linear relationship of the actuation current corresponding to the applied voltage. The non-linearity is a result of heating the boron doped silicon beams, which affects the material's resistivity. The response of the actuation force can be characterized by the application of sinusoidal and square-wave input currents (Figure 11) to the electro-thermal actuator.
.jpg)
Figure 11. Square wave testing of a thermal MEMS actuator
Electrostatic Micromirror Testing
A MEMS based micromirror has been designed for large mirror deflections. The micromirror design consists of a mirror plate suspended from one end of the mirror edge through low-stiffness SU8 polymer flexures. The interdigitated, vertical comb drives was used to electrostatically actuate the mirror (Figure 12). The mechanical properties of the MEMS-based micromirror were explored through mechanical testing. With the combination of electrical and mechanical measurements, quantitative characterization of the actuation force corresponding to the actuation angle could be performed. The actuation angle was directly measured on the wafer without time-intensive procedures like wafer dicing and wire-bonding.
.jpg)
Figure 12. Electrostatic micromirror testing
The FT-MPS02 MEMS Probestation was used to perform the compression tests at various locations along the beam axis. The mirror plate came in contact with the underlying chip substrate at the maximum deflection of the mirror plate of 145 µm, which was denoted by an abrupt increase in the forces, as shown in Figure 13. The figure shows steeper force-deflection curves generated at positions near the fixed end of the beam, as a large amount of force is needed for mirror deflection. Based on the transformation of the acquired x-y-z position data to rotation angle, and the force data into torsional moment, the rotational stiffness could be evaluated.
.jpg)
Figure 13. Mechanical testing of an electrostatic micromirror
The corresponding driving forces and angles of the interdigitated vertical comb drive were measured using two electrical probes mounted on the FT-MPS02 for the application of actuation voltages. The FT-MPS02 integrated signal generator was used to generate the actuation voltages. Finally, the step response of the micromirror (Figure 14) was determined using a force response upon applying a square-wave actuation voltage.
.jpg)
Figure 14. Response time of an electrostatic micromirror
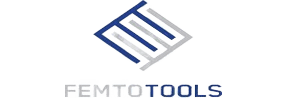
This information has been sourced, reviewed and adapted from materials provided by FemtoTools AG.
For more information on this source, please visit FemtoTools AG.