The production of nanofibers from polymer materials plays a vital role in nanotechnology, which is the most important area of technological and scientific activities in the last decade. An increasing number of scientific publications have been demonstrated, thanks to advancements in nanofiber production methods such as air blowing from melt or solution, centrifugal-spinning, electrospinning, and optimization of process parameters of those methods.
There has been a rapid increase in the development of nanotechnology as well as in the production of nanofibers through electrospinning, which can be achieved with needless and needle methods. Both needless and needle electrospinning processes rely on implying electrostatic forces and producing an electric field between polymer feeding and nanofiber collecting areas using high voltage.
Benefits of using the needle electrospining method is that electrospinning jet occurs when high voltage, applied to polymer solution, is generated with less voltage compared to needless electrospinning, because the polymer’s surface tension, which must be gained by electrostatic forces, is low and controllable.
Needle electrospinning allows mass and continuous nanofiber production, in addition to being compatible with small quantity nanofiber production. Additionally, advanced nanofiber analysis such as hollow nanofibers, coaxial electrospinning, and nanofiber yarn production can be practicable with a wide range of needle and process designs.
Electrospinning has been accepted as the most versatile and effective technology for developing nanofibers from a variety of polymeric materials. However, most of the electrospun fibers are produced in the form of randomly oriented nonwoven mats, which restrict the utilization area.
The first step of this study focuses on producing 3D nanofiber yarns for utilization areas and multipurpose research, and the second step deals with the coating of monofilament yarns with nanofibers.
Experiment
Materials
Polyacrylonitrile (PAN) was the polymer used in the research, and the solvent used was N,N-dimethylformamide (DMF). The required amounts of polymers were dissolved in the solvents at the required temperature in order to prepare the electrospinning solutions. 18%, 15%, 12% and 10% PAN solutions were obtained.
Scanning Electron Microscope (Zeiss Evo10) Inovenso™ nanofiber yarn apparatus.
.jpg)
Figure 1. Schematic view of nanofiber yarn production system
Image Credit: Inovenso
Electrospinning of Nanofiber Yarns
A nanofiber yarn electrospinning system is made up of a purpose-made cylinder collector, three needle nozzles, a high-voltage power supply, and a yarn winding system. Three spinnerets encircle the collector, and a winding system was positioned below it.
All three spinnerets were connected to 20 kV positive high power supply. Electrospun nanofibers were deposited onto the rotating cylinder collector and a nanofiber web was formed to cover the collector’s end. A standard guide yarn attached to the collector was used to draw the nanofiber yarn.
.jpg)
Figure 2. Nanofiber yarn that was obtained by 10% PAN solution and SEM images
Image Credit: Inovenso
Characterization
A scanning electron microscope (SEM) was used to observe the fiber and yarns. Images obtained by SEM helped to calculate twist level, average fiber diameter, and average yarn diameter.
Results and Discussions
Nanofiber yarn was continuously electrospun from 10% PAN solution. The optimized solution was achieved using a 15 rpm rotation speed of winding system, 350 rpm rotation speed of collector, 20 kV voltage, and 1,5 ml/h feeding rate.
Nanofibers were electrospun from positively charged three spinnerets and deposited onto the grounded rotating cylinder collector. These nanofibers were mainly deposited onto the mouth end of the collector because of it's structure. A standard yarn was used as a guide to draw the nanofiber yarn from the collector to the winding system. The rotating speed of the collector caused the nanofiber to twist.
Some part of the deposited nanofibers were coupled to the cone-shaped web formation, and some of these fibers were stuck at the inner edges of the collector. The reason for this could be electrostatic interaction between positively charged nanofibers. They are likely to repel each other and be deposited on the grounded collector. It was observed from open literature that mainly negative and positive high power supplies were used simultenously.
When the solvent was not adequately evaporated, wet fibers were obtained. Observation from SEM images proved that diameters of such nanofiber yarns were unbalanced. Varied feeding rates (2,5, 3, 4 ml/h) were experienced to avoid wet nanofibers; however, an extremely weak fibrous cone was obtained.
Most of the nanofibers were observed to be stuck at the edges of the collector, so yarn formation was not observed. A high voltage amount was also tried between 25 and 40 kV, but it was also not possible to obtain yarn and even fibrous cone as most of the nanofibers were deposited onto the inner walls of collector.
.jpg)
Figure 3. Nanofiber yarn
Image Credit: Inovenso
General Results
The use of oppositely charged high power supplies (+ and -) will enable the formation of all the deposited nanofibers joining fibrous cone and yarns due to electrostatic interaction.
In some experiments, it was observed that nanofibers were deposited onto the nanofiber yarn while removing the yarn from the collector to the winding system. Both the process and product are negatively effected by withdrawing the yarn in between the spinnerets. Better solutions can be obtained by changing the place of the winding system. This will require a new apparatus design which is under process.
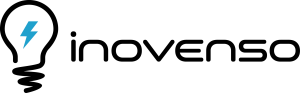
This information has been sourced, reviewed and adapted from materials provided by Inovenso.
For more information on this source, please visit Inovenso.