Interview conducted by Mychealla RiceAug 12 2016
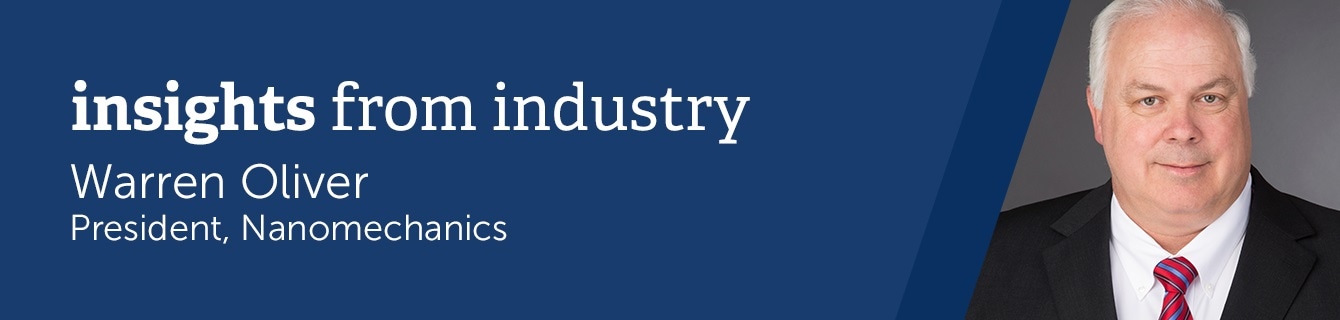
Warren Oliver, President of Nanomechanics talks to AZoNano about their range of revolutionizing Nanoindenters and Nanoindentation testing systems.
Please can you give a brief overview of Nanomechanics and the work you do?
Nanomechanics is a highly focused company, employing over 20 world-class engineers, scientists and international business experts. We design and manufacture specialized testing systems that measure the mechanical properties of materials and devices on a microscopic scale, such as MEMS, coatings, polymers and thin films.
We manufacture the instruments and develop the techniques for using them, allowing academic customers to conduct research and development at a fundamental level, and industry customers to use them for product development and process control. We are the worldwide leader in this field and we have products that nobody else in the market can offer, which is why we do well in both the academic and industrial communities.
After seven years, we continue to grow aggressively, both in terms of market share and new technical developments.
Could you explain the benefits of Nanomechanics nanoindenters and nanoindentation testing? How do they differ from previous solutions?
We spend considerable time designing our instruments to perform on extreme ends of the testing spectrum, for example, we focus on test speed to complete these tests quickly while maintaining great accuracy. Focusing on instrument precision and accuracy means people can rely on the data and consistently compare the results from instrument to instrument.
Not being able to do this is a major flaw in many other systems in the market. What sets us apart from the rest of the industry is that we fundamentally understand and design the instruments with dynamics (CSM) from the ground up which allows us to do experiments that no one else can do.
What are the major advantages of the iNano and the NanoFlip?
The iNano is a high-performance nanoindentation system, with a single purpose. This instrument includes all the things required to do very high-performance experiments without having to add a lot of unnecessary and costly features, although it can be customized for novel applications.
As our base instrument, it offers everything that you need to conduct virtually any indentation test at high speeds, and dynamically, which is a bit different then all the other systems on the market, where a base platform requires multiple options to operate at the same level.
The NanoFlip is our hybrid system, because it operates within an ambient environment, but also in vaccum.
NanoFlip integrates with any imaging system, such as optical microscopes, RAMAN systems, optical profilometers, SEM/FIB, XRD or AFMS, because of its ability to rotate the sample 90 degrees. Unlike other systems with similar designs, the NanoFlip rotates to two hard stopping points, giving it a much higher load frame stiffness which is essential for accurate data.
.jpg)
.jpg)
.jpg)
How is Nanomechanics revolutionizing nanoindentation for industrial applications?
It’s mostly in terms of the return on investment of the instrument. Typical indentation tests on other systems are very operator intensive. You sit in front of the instrument, you push a button, you take a reading and write it down then put it somewhere for future review. Then, you move over and do it again, and the operator sits there running the instrument the whole time, maybe completing one measurement every few minutes.
Although manufactures of traditional testing systems may claim automation they really don’t offer it, the systems we make are truly automated, so you can set up a long series of experiments and run them without any operator input. We routinely set up tests that run hundreds of thousands of experiments, even millions of experiments, without having to issue any additional commands.
The speed of each test is dramatically faster, providing information from a sample in less than a second per test, test after test. The revolutionary aspect of our system is its ability to achieve high speed testing and generate statistics in addition to things like topography and tomography maps without having to scan the tip across the surface of the material.
Repeatability, precision and high-speed testing are things we hang our hats on. Fundamentally, what customers are getting from us, that they will not get from other vendors, is significantly more information at a much lower cost.
.jpg)
.png)
.png)
What benefit will it have for those in Research and Development and the Quality Control sectors?
The software that runs our instruments is designed to do any experiment you can imagine. We refer to this as a universal testing system, but on a microscopic scale. You can work with compression specimens, indentation specimens, any specimen you want, plus any kind of test in terms of load versus time.
How you control the experiment and what you do with the data are all extremely flexible and adaptable with our software, such as writing complex experiments and repeating them easily. If you can dream up an experiment, our software can do it, which is important to Nanomechanics as our background is in the academic research community.
We don’t want the software to limit what the customer can do with our instrument.
In terms of process control, this software flexibility simplifies writing experiments that are also easy to repeat. The scientist or engineer writes a script, and any technician runs it regardless of their expertise, a valuable benefit, especially to the industrial customer.
Repeatability is an important factor for us as well. At Nanomechanics we ensure that all of our instruments produce precisely the same information, so a company can buy 10 of our instruments and know that all the results will be exactly the same.
.jpg)
How will Nanomechanics nanoindenters make data more reliable? Why is this important?
First, the nanoindenters from Nanomechanics are flexible enough to push the limits of indentation testing in a research and development environment and sturdy enough to handle 24 hour testing in quality control. Whether the application is scratching, thin films, elastic modulus, hardness, or stiffness measurements, our nanoindenters are a powerful analytical tool for an industrial laboratory.
Secondly, state-of-the-art instrument and software architecture allows for quick, statistical results that drive informed decisions. Finally, there is significant benefit in terms of reliability and “up time” from the instrument support that Nanomechanics offers to all customers. Our support staff includes dedicated applications scientists and engineers, as well as one-on-one training via web support.
Research and quality control divisions in industry will benefit from a product developed by a company with decades of experience in mechanical testing and instrumentation.
Within the near future do you see any areas/industries that the nanoindenters can be introduced too?
Absolutely. The industrial market place is just in the formative years. Numerous places will find nanoindentation useful over the next few years as the more traditional, old ways of testing materials are replaced, and in some cases, data becomes available where people couldn’t otherwise get that information.
For example, everywhere you look, there are thin films: car paint, razor blades, LED screens, optical lenses, semiconductors. Although the primary mission of a material in some particular product may be an electrical property, a thermal property or an optical property, everything has to stay in one piece during its use, so mechanical properties are not far down the list. Mechanical properties are as important, or more important to the development of a material or product than nearly every other property.
What sets Nanomechanics’ nanoindenters apart from the rest of the industry?
Our systems are the highest performing instruments on the market, providing fast, accurate, and repeatable mechanical property data with high spatial resolution. All of our systems provide unrivaled dynamic performance.
With a time constant of 20 µs, our systems are the only commercial nanoindenters to simultaneously meet specifications for displacement range, digital resolution, noise floor and drift rate. Other systems must sacrifice one or more of these parameters to meet this resolution. Only our systems achieve these specifications concurrently.
Furthermore, our indenters are engineered with electromagnetic actuation for linear force control. This allows force and displacement to be independent variables to maximize accuracy and precision. In contrast to other types of actuators, such as electrostatics and piezo-electrics, electromagnetic actuation does not require a feedback system to achieve specified loading conditions. Linear force control also provides an uncomplicated calibration.
As I mentioned earlier, load-frame stiffness is an indentation parameter that may significantly impact data yet the magnitude of its effect is often unrealized. Our systems have incredibly high load-frame stiffness to yield data with a high level of accuracy, something you will not find in other systems on the market.
Lastly, the speed at which our instruments operate is unmatched in the world. This allows us to do unique mapping experiments. Using a proprietary technique called NanoBlitz, all of our systems offer unprecedented and unequaled dynamic testing with high accuracy, precision and speed.
With NanoBlitz 3D, properties such as elastic modulus, hardness, and stiffness are tested at a specific load for each indent, typically at a speed of one second per indentation. NanoBlitz 3D uses a constant strain rate method to map mechanical properties with statistical significance.
Adding to this capability is the 4D version of NanoBlitz. Using a sophisticated constant strain rate method with a proprietary procedure, NanoBlitz 4D maps hardness, modulus and stiffness, along with topography as a function of depth, all at high speeds.
Please can you tell our readers about your plans for international expansion. What will it mean for the future of Nanomechanics?
We have representatives around the world who are selling, servicing and demonstrating our instruments. To date, this extensive network includes 16 distributors and several independent agents in key markets around the world, in addition to several planned R&D centers in several of these areas which provides customers with convenient local points of contact for sales, consulting and service; key elements to our success.
This international growth has taken Nanomechanics to the top of the industry and I think it is easy to say we are the number one provider of this technology in the world.
Where can out readers go to find out more?
A great place to go first is our website, www.nanomechanicsinc.com. Of course, we meet the market place in a number of different places to let them know what we are doing. If you go to any technical conference around the world where people are discussing material science and mechanical testing, you will hear reference to our instruments providing the results.
Also, we encourage customers to visit us in Oak Ridge, Tennessee, just down the road from Oak Ridge National Laboratory, not only to demo our latest developments and products , but to learn about some of the unique applications we are working on. One of the things we find all the time, whenever we are in a competitive situation, is that we blow people away with how far our technology is ahead of the competition.
We have an incredibly bright future here at Nanomechanics as we continue to grow aggressively. The opportunities we see in the market are expanding quickly and we are very excited.
About Warren Oliver
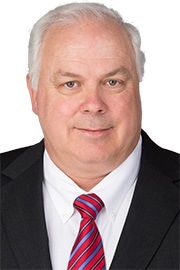
Warren Oliver obtained his BS in Materials Science from the University of Tennessee in 1976. He received a MS and PhD of Materials Science in 1981 from Stanford University studying with Professor W. D. Nix. Dr. Oliver spent one year on a postdoctoral appointment at Brown, Boveri and Co., Ltd followed by two years (1982-1984) at the United Technologies Research Center.
He then returned to Tennessee for a position at Oak Ridge National Laboratories for ten years until 1994 at which time he left to spend full time directing Nano Instruments, a company he helped to found in 1984. In 1998 Nano Instruments was acquired by MTS Corporation. In 2008 the group was acquired by Agilent Technologies.
Finally, in 2009 Dr. Oliver helped form and became president of a new company, Nanomechanics, Inc. In 2016, Dr. Oliver was also elected the National Academy of Engineers and became a member the University of Tennessee’s MSE Hall of Fame.
During the course of his research career, Dr. Oliver has made notable contributions to the area of intermetallic alloy development and the mechanical characterization of materials and structures on the micro and nano scale.
In particular, he has contributed to the development and commercialization of nanoindentation/nanoindenter equipment and techniques, published more than 250 papers in peer reviewed international journals, and been named as inventor on 14 patents.
Disclaimer: The views expressed here are those of the interviewee and do not necessarily represent the views of AZoM.com Limited (T/A) AZoNetwork, the owner and operator of this website. This disclaimer forms part of the Terms and Conditions of use of this website.