The extreme conditions of nuclear reactors expose their structural alloys to high temperatures, stress, corrosion, and irradiation damage. Therefore, nuclear alloys require materials with high strength, flexibility, corrosion resistance, irradiation resistance, and microstructural stability across a wide temperature range, especially at high temperatures.
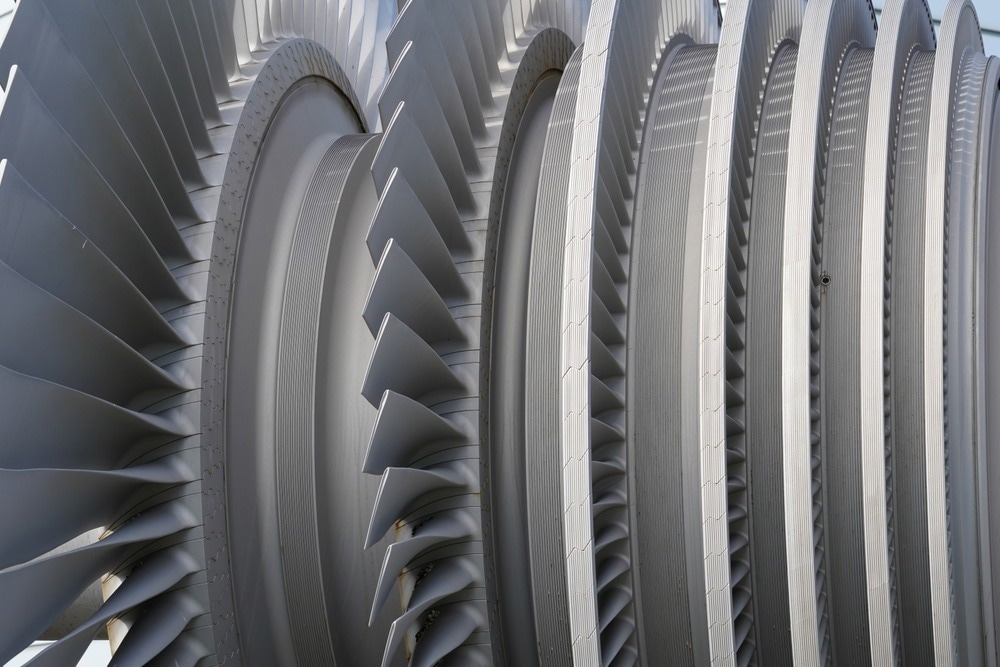
Image Credit: Luciavonu/Shutterstock.com
Nuclear reactors were designed and commercialized decades ago, using alloys and materials available at the time. As performance knowledge relevant to nuclear reactor operations grew, new materials were formulated and implemented for safer and more efficient nuclear operations.
The following are some of the most prevalent materials used to create alloys in the nuclear industry:
Zirconium-Based Alloys
Zirconium is considered the ideal fuel cladding material in commercial light water reactors due to its high strength and ductility, compatibility with transmutation materials inside cladding, low neutron absorption, and high resistance to stress corrosion cracking in extremely hot water.
Nuclear-grade zirconium alloys typically consist of more than 95% zirconium and less than 2% of additional metals, such as iron, tin, chromium, niobium, and nickel, which are added to enhance corrosion resistance and mechanical properties.
Zircaloy-4 (Zr-Sn-Fe-Cr) has been the most widely used cladding material in pressurized water reactors in recent years. However, it is now being replaced by new zirconium-niobium-based alloys that offer superior corrosion resistance.
Titanium-Based Alloys
Titanium is prized for its excellent corrosion resistance and high strength-to-density ratio, the highest among metals. In commercial applications, it is usually alloyed with small quantities of aluminum (around 6%) and vanadium (around 4%).
Titanium alloyed condenser tubes are ideal for nuclear power plant main steam condenser systems, which deaerate and condense main turbine exhaust steam and serve as a heat exchanger for the turbine bypass system.
Titanium provides significant enhancements to structural alloys in extreme environments, such as increased water velocities that promote improved heat coefficients and exceptional resistance to erosion, abrasion, and corrosion, enhancing fouling resistance. However, titanium is expensive, leading to high initial costs for titanium condenser tubes.
Nickel-Based Alloys
Nickel alloys, also known as super-alloys, are composed of a high proportion of nickel and a small proportion of copper, iron, chromium, molybdenum, titanium, and cobalt, which improves their strength and corrosion resistance.
Although these alloys are extensively employed in the nuclear industry, certain limitations restrict their broader application. For example, due to its extremely large cross-section and ability to absorb thermal neutrons, nickel reduces power production efficiency and produces radioactive components.
Iron and Carbon Alloys (Stainless Steel)
Austenitic Stainless Steels
Austenitic steels are nonmagnetic alloys due to their low carbon content and high levels of nickel and chromium.
This steel is used in nuclear reactors as it is a readily available alloy with high corrosion resistance, good fabrication properties and the researchers' significant familiarity with it in various industries, such as fossil fuel and petrochemical.
While austenitic alloys have been studied for use in fast reactors, lower helium and hydrogen production rates, the absence of water and distinct neutron spectra make them less suitable for these reactors.
Cast-Austenitic Stainless Steels
Cast-austenitic stainless steels have similar physical and chemical properties as austenitic steel. However, they are cast into the final component shape instead of machining and forging.
This alloy is widely used in safety-related components of nuclear plants, particularly in the pressurized water reactors' auxiliary piping system, coolant, valve bodies, pump casings, and other assorted fittings. In addition, it is also being incorporated into the design of new power plant construction.
This steel is chosen for economic considerations since the casting process is less expensive. Despite being inexpensive, cast-austenitic stainless steel components exhibit high corrosion, fatigue, and wear resistance throughout their lifespans.
Low-Alloy Steels
A low-alloy steel is composed of steel plus other metals, such as manganese, nickel and chromium, to achieve higher strength without losing toughness.
They have good fracture toughness, increased strength, and weldability and are reasonably inexpensive, making them ideal for nuclear applications.
Due to their ductility and cost-effectiveness, low-alloy steels are extensively used as pressure boundary materials in various water reactor components, such as pressure vessels, pressurizers, and piping material.
Low-alloy steels must be covered with corrosion-resistant materials, such as nickel-based alloys or austenitic stainless steels, on the interior wetted surface of reactor coolant system components.
Recent Research and Development in Nuclear Alloys
Anti-Corrosion Material for Fusion Reactor
In a fusion reactor, energy is produced through the fusion of two nuclei, which is then transferred to a breeding blanket surrounding the reactor core. This high-temperature blanket, with temperatures over 1173 K, generates heat that runs a turbine to generate electricity.
At these temperatures, the materials in contact with the breeding blanket are at risk of becoming corroded, compromising the stability and safety of the reactor.
To address this, the Tokyo Institute of Technology researchers have developed chemically compatible CVD-SiC and FeCrAl alloys for use in the breeding blanket of fusion reactors.
The alloys were immersed in liquid LiPb for 250 hours for corrosion testing. CVD-SiC reacted with impurities in the liquid LiPb to create a layer of complex oxides, while FeCrAl formed an oxide layer, which acted as an anti-corrosion barrier.
Nuclear Engineers Developed a Novel Resilient Oxide Dispersion Strengthened (ODS) Alloy
In a study published in the Journal of Nuclear Materials, researchers have created a new generation of high-performance oxide dispersion-strengthened alloys for fission and fusion reactors.
Oxide dispersion-strengthened alloys are recognized for their high resistance to creep at high temperatures, withstanding up to 1,000 °C.
The newly developed oxide dispersion-strengthened alloys have shown exceptional resistance to swelling, surviving up to 400 displacements per atom. As a result, they are among the most successful alloys created in the field, making them an attractive option for use in nuclear reactors where reliable and durable materials are crucial.
Future Outlook
Alloys have played an important role in developing nuclear energy as a reliable and efficient energy source. However, more research and development of new alloys are needed to meet the need for safer and more efficient nuclear reactors.
Researchers are integrating nanotechnology into alloys to create self-healing alloys that repair themselves when exposed to radiation or extreme temperature. This could extend the life of nuclear reactors and decrease their maintenance expenses.
Developing stronger, radiation-resistant, and durable alloys are essential to creating a practical and sustainable nuclear energy future to meet the growing energy demand.
References and Further Reading
Kim, H., Gigax, J. G., Ukai, S., Garner, F. A., & Shao, L. (2021). Oxide dispersoid coherency of a ferritic-martensitic 12Cr oxide-dispersion-strengthened alloy under self-ion irradiation. Journal of Nuclear Materials, 544, p. 152671. https://doi.org/10.1016/j.jnucmat.2020.152671
Kondo, M., Hatakeyama, S., Oono, N., & Nozawa, T. (2022). Corrosion-resistant materials for liquid LiPb fusion blanket in elevated temperature operation. Corrosion Science, 197, p. 110070. https://doi.org/10.1016/j.corsci.2021.110070
Nuclear Power. (2023). Titanium Alloys. [Online]. Nuclear Power. Available at: https://www.nuclear-power.com/nuclear-engineering/metals-what-are-metals/alloys-composition-properties-of-metal-alloys/titanium-alloys/
Odette, R., & Zinkle, S. (Eds.). (2019). Structural alloys for nuclear energy applications. Newnes. doi.org/10.1016/C2011-0-07772-4
Oryshchenko, A. S., Kudryavtsev, A. S., Mikhailov, V. I., & Leonov, V. P. (2012). Titanium alloys for shipbuilding and nuclear power engineering. Inorganic Materials: Applied Research, 3, pp. 497-506. https://doi.org/10.1134/S2075113312060081
Was, G. S., Petti, D., Ukai, S., & Zinkle, S. (2019). Materials for future nuclear energy systems. Journal of Nuclear Materials, 527, p. 151837. https://doi.org/10.1016/j.jnucmat.2019.151837
Disclaimer: The views expressed here are those of the author expressed in their private capacity and do not necessarily represent the views of AZoM.com Limited T/A AZoNetwork the owner and operator of this website. This disclaimer forms part of the Terms and conditions of use of this website.