Jul 29 2015
A future where power plants feed their carbon dioxide directly into an adjacent production facility instead of spewing it up a chimney and into the atmosphere is definitely possible, because CO2 isn’t just an undesirable greenhouse gas; it is also a good source of carbon for processes like polymer production.
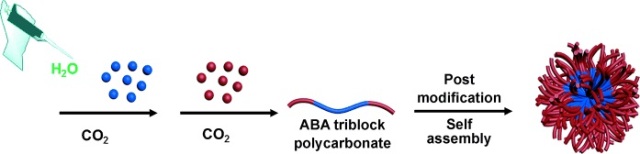
In the journal Angewandte Chemie, American scientists have now introduced a two-step, one-pot conversion of CO2 and epoxides to polycarbonate block copolymers that contain both water-soluble and hydrophobic regions and can aggregate into nanoparticles or micelles.
CO2 and epoxides (highly reactive compounds with a three-membered ring made of two carbon atoms and one oxygen atom) can be polymerized to form polycarbonates in reactions that use special catalysts. These processes are a more environmentally friendly alternative to conventional production processes and have already been introduced by several companies. However, because current CO2-based polycarbonates are hydrophobic and have no functional groups, their applications are limited. In particular, biomedical applications, an area where the use of biocompatible polycarbonates is well established, have been left out.
A team led by Donald J. Darensbourg along with graduate student Yanyan Wang at Texas A&M University (USA) has provided a solution. For the first time, the researchers have been able to produce amphiphilic polycarbonate block copolymers in which both the hydrophilic and hydrophobic regions are based on CO2. They were also able to incorporate a variety of functional and charged groups into the polymers. Because it is very difficult to find building blocks to make hydrophilic polycarbonates, the researchers used a trick: they polymerized first and attached the water-soluble groups afterwards.
The entire process is even a “one-pot reaction”: The researchers first produce the hydrophobic regions by polymerizing CO2 and propylene oxide (as the epoxide component). In the same vessel, they then change to a different building block, allyl glycidyl ether (AGE), an epoxide with a double bond in its side chain, and continue the polymerization. The AGE-containing polymer grows on both ends of the existing polycarbonate, leading to a triblock copolymer. The length of the blocks can be controlled precisely. Subsequently a “thiol–ene click reaction” can be used to simply “click” a water-soluble group into place at the double bond. This makes it possible to attach acidic and/or basic groups that carry a positive or negative charge in certain pH ranges. Some of the amphiphilic polycarbonates made by this method are able to aggregate into particles or micelles in a self-organization process. This, and the ability to attach bioactive substances, for example, could provide many more possibilities for biomedical applications.