Active depth sensors, such as lidar, time-of-flight (TOF) systems, and structured light (SL) systems, can evenly sample the depth of an entire scene at a predetermined scan rate. SL-based depth-sensing technology irradiates an object with an array of dots, and diffracted light is tracked to obtain three-dimensional (3D) information.
Metasurface-based SL imaging platform scattering high-density diffracted beams into the full 180° FOV. Under the illumination of a polarization-independent coherent laser source, the proposed metasurfaces generate ~10 K points over the entire 180° space. The depths of the dot arrays illuminated on the objects are extracted using a stereo matching algorithm. Image Credit: Kim, G., et al. (2022).
Traditionally, diffractive optical elements are used to generate laser dot arrays. However, their low pixel size (micron-scale) limits their diffraction efficiency and field-of-view (FOV). An article published in Nature Communications proposed a metasurface-enhanced SL-based depth-sensing platform capable of scattering an array of dots of high density over a FOV of 180 degrees by modulating light at the subwavelength level.
Here, the team separated two face masks by 1 meter, with one placed on the beam axis and another at an axis 50 degrees away. Depth information was estimated by employing a stereo matching algorithm.
In addition, the metasurface was replicated via a 3D imaging and imprinting method using a nanoparticle-embedded resin, enabling high-throughput metasurface manufacturing on arbitrary surfaces.
3D Imaging and Applications of Metasurfaces
Laser-based 3D imaging technology has been utilized in various sensor applications, including virtual/augmented reality (VR/AR), robot vision, and autonomous driving. The depth information of a 3D object is obtained by radiating the target with a controlled laser beam via transmitters and monitoring the diffracted light through a detector.
3D imaging is classified into TOF, where the distance information is recovered through measuring the travel time for a light pulse, and SL, where the distance information is recovered through triangulation.
Although TOF-based 3D imaging has several limitations in terms of limited FOV, SL-based 3D imaging can overcome such drawbacks. Thus, the latter type of 3D imaging system uses unique 2D light patterns to illuminate the target, effectively widening the FOV.
Projecting an SL pattern onto a 3D object with a nonplanar surface distorts the light and helps to calculate the surface profile from the distorted light pattern by utilizing different algorithms. This type of 2D operation increases the frame rate of the acquired object. Furthermore, concurrent imaging of several objects reduces the computational load of this 2D operation. To date, spatial light modulators (SLMs) and diffractive optical elements (DOEs) have been used to produce 2D light patterns.
Metasurfaces are 2D arrangements of engineered nanostructures referred to as meta-atoms, which primarily derive their qualities from the constituent parts, namely wave-guiding and resonant effects. Metasurfaces have been used to achieve unusual light tuning at the nanoscale level.
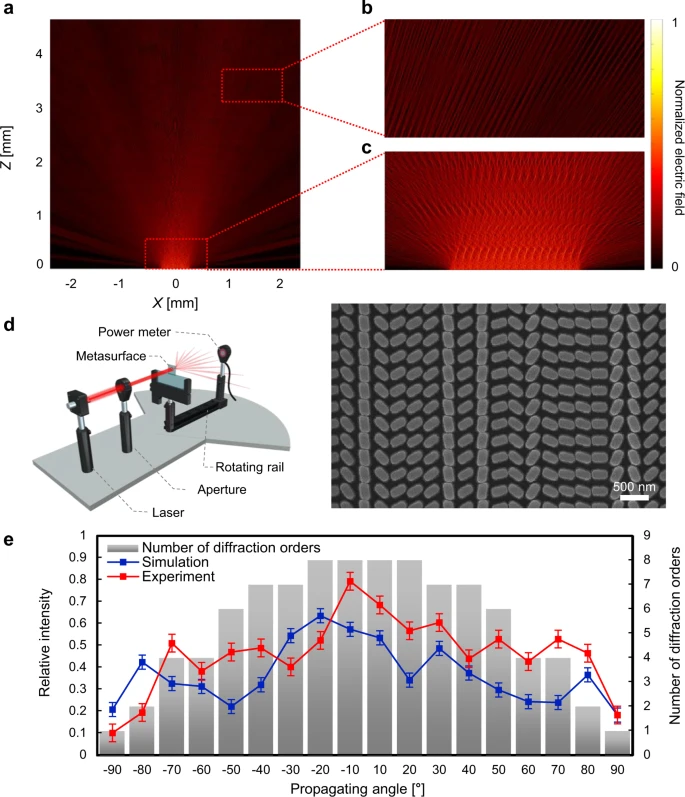
Comparison between simulated and measured diffraction patterns of 1D diffractive metasurfaces. a–c Simulated distribution of amplitude of electric field at the plane normal of the metasurface (a) together with magnifications of the far (b), and near fields (c). d Schematic of the optical setup to measure power of each point by rotating power meter at the operation wavelength of 633 nm where the incident laser light is chirped to fit into the size of metasurfaces. SEM image of the corresponding metasurfaces. e Plot of number of diffraction orders, and relative intensities of simulated and measured diffracted beam with respect to propagating angle. The intensities are plotted with averaged value with error bars, as propagating angle is grouped at intervals of 10°. Kim, G., et al. (2022).
Metasurface-Based 3D Imaging
In this study, a metasurface-based SL device capable of projecting approximately 10,000 dot arrays of light into full space was realized over a 180-degree FOV. The metasurface was periodically arranged with supercells that facilitated the diffraction of the projected laser light to several diffraction orders with high density and uniform intensity.
Supercells were arranged along the x- and y-coordinates with different periodicities, considering the interference effects of the periodic assemblage of supercells. The phase-only distribution of a single supercell serves as the convolution kernel function used in the convolution theorem analysis of the final diffraction patterns.
Multiple types of metasurface-based SL projectors, such as 1D dot arrays, 2D dot arrays, and 2D parallel line arrays of light, have been demonstrated analytically and empirically over a 180 degrees FOV by comprehending the total optical response concerning diffraction and interference effects.
Furthermore, face masks were set up with wide viewing angles of up to 60 degrees with respect to the optical axis as a proof-of-concept to irradiate high-density dot arrays produced by the suggested metasurfaces. The stereo-matching technique employed two cameras to retrieve the depth information of 3D face masks.
Additionally, a scalable imprinting manufacturing approach based on the nanoparticle-embedded resin was used to directly print a metasurface on a curved glass surface, enabling high-throughput manufacturing of metasurfaces on arbitrary substrates.
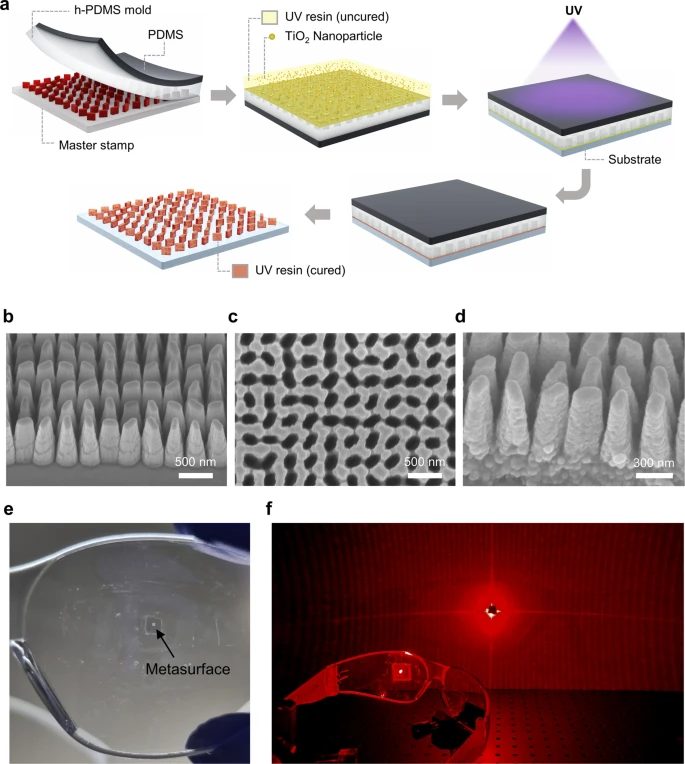
Demonstration of prototype device by direct printing of nano-PER on curved surface of glasses. a The flow chart of nano-PER based imprinting fabrication process. b–d SEM image of the master stamp fabricated by EBL (tilted view) (b), soft mold composed of h-PDMS and PDMS (c), and replicated nano-PER-based metasurface (tilted view) (d). e Replicated metasurface on the curved surface of safety glasses. The size of printed metasurface is 510 μm by 510 μm. f Experimental demonstration of full-space covering SL of 2D line array. Laser light illuminate the nano-PER-based metasurface printed on surface of glasses exhibiting application for ultra-compact depth sensor for AR glasses. Kim, G., et al. (2022).
Conclusion
In summary, the present study simulated and analyzed a metasurface’s optical response to reconstruct its 3D depth, and experimentally validated the features of the proposed metasurface through the diffracted light in 3D space.
Additionally, nanoparticle-embedded-resin imprinting technology was used to print an SL projecting metasurface on a curved glass surface to project a prototype of AR glasses. With high-density dot arrays, metasurface-based SL imaging devices may enable 3D imaging of objects over a complete FOV, using high-density dot arrays, which is both technically and economically feasible.
The present study demonstrated that an ultra-compact depth perception platform for face identification and automotive robot vision applications could be made possible using such a full-space diffractive metasurface.
Reference
Kim, G., et al. (2022). Metasurface-driven full-space structured light for three-dimensional imaging. Nature Communications. https://doi.org/10.1038/s41467-022-32117-2
Disclaimer: The views expressed here are those of the author expressed in their private capacity and do not necessarily represent the views of AZoM.com Limited T/A AZoNetwork the owner and operator of this website. This disclaimer forms part of the Terms and conditions of use of this website.