A recent study published in Nature Communications introduced a new method that combines the electrochemical reduction of carbon dioxide (CO2) with the production of carbon nanotubes (CNTs). These nanotubes are then used to create advanced 3D-printed carbon nanocomposites. The research highlights how this process could help reduce CO2 emissions while also producing high-performance materials with a wide range of potential applications.
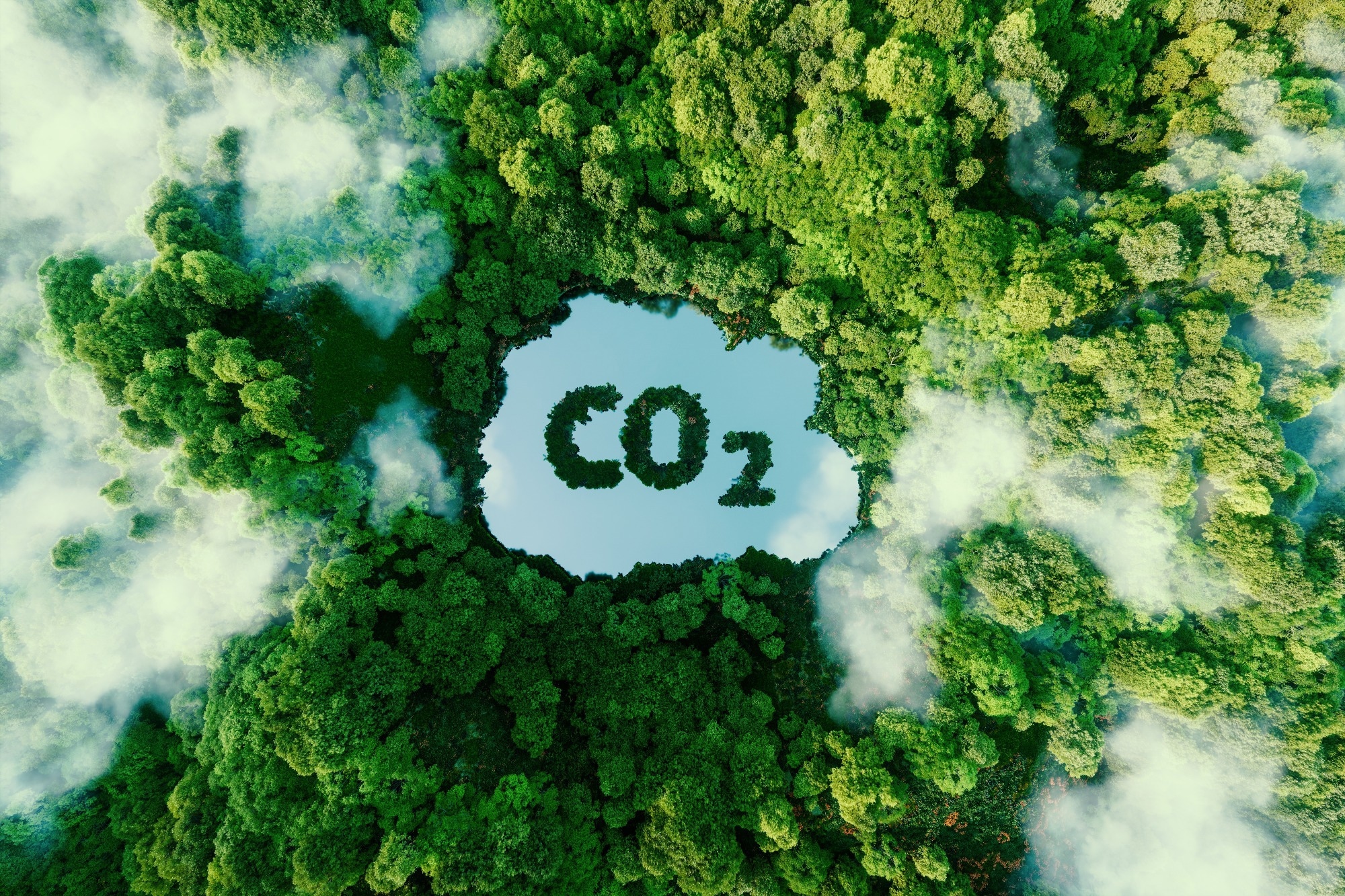
Image Credit: petrmalinak/Shutterstock.com
Background
The increasing levels of CO2 from industrial activities have raised concerns about climate change and environmental sustainability. To address this, new methods for utilizing CO2 are being explored, particularly in producing valuable materials.
CNTs are known for their strong mechanical, electrical, and thermal properties, making them useful in enhancing composite materials. Traditional CNT production methods often involve high-energy processes that are not environmentally friendly.
This study presents a method that uses CO2 as a feedstock, addressing both sustainable material production and greenhouse gas reduction. By integrating CNT production with 3D printing, it is possible to create tailored structures for specific applications. This research builds on previous work demonstrating the potential to produce CNTs at scale while maintaining process stability and efficiency.
The Current Study
The process begins with the electrochemical reduction of CO2 to carbon monoxide (CO) at ambient conditions using a specially designed electrolyzer. The electrolyzer consists of silver (Ag) cathodes and iridium (Ir) anodes, operating in a cesium bicarbonate (CsHCO3) electrolyte solution.
This setup facilitates the generation of CO, which is then directed into a thermochemical reactor. In this reactor, the CO undergoes a transformation, where it reacts with a cost-effective steel wool catalyst to produce solid carbon and additional CO2. The CO2 generated in this step can be recirculated back into the electrolyzer, creating a closed-loop system that enhances overall efficiency.
Following the production of solid carbon, the next phase involves the preparation of a carbon nanocomposite filament. A high-density CNT nanocomposite filament is created by dispersing CO2-derived CNTs into a thermoplastic polylactic acid (PLA) matrix. The CNTs are incorporated at a concentration of approximately 40 wt%, which is crucial for maximizing the utilization of CO2.
The filament is created through a multi-step process. First, PLA is dissolved in dichloromethane (DCM) and then mixed ultrasonically with the CNT solution. After the mixture is thoroughly combined, it is dried to form a film. This film is then extruded into a continuous filament, making it ready for 3D printing.
The 3D printing process uses a fused deposition modeling (FDM) technique to build a preformed CNT structure. After printing, the structure is thermally treated to remove the PLA matrix, leaving behind a stable CNT scaffold that maintains its shape and microstructure. This scaffold is then infiltrated with a thermoset resin through a vacuum-assisted resin transfer molding (VARTM) technique. The final product is cured at room temperature overnight, resulting in a durable 3D CNT/epoxy nanocomposite.
Results and Discussion
The results of this study demonstrate the successful incorporation of CO2-derived CNTs into a 3D printing process, producing high-quality carbon nanocomposites with improved mechanical properties. The CNT structures were characterized using scanning electron microscopy (SEM) and transmission electron microscopy (TEM), which provided detailed insights into their morphology and dimensions. The analysis revealed well-aligned CNTs within the printed structures, contributing to the composite's strength and performance.
Thermogravimetric analysis (TGA) confirmed the high CNT content within the nanocomposite by determining the ratio of matrix to CNTs. Mechanical testing showed significant improvements in tensile strength and thermal conductivity compared to traditional composites. The addition of CNTs enhanced the materials' structural integrity and electrical conductivity.
A techno-economic analysis also assessed the commercial feasibility of the CO2 conversion and CNT production process. By scaling up to a 100 mg production scale and achieving over 200 hours of electrolyzer stability, the research highlights advancements in the efficiency and sustainability of CNT manufacturing. The closed-loop CO2 utilization system further supports the economic viability, positioning it as a promising option for industrial applications.
Conclusion
This research offers a practical solution to the challenges of CO2 emissions and the need for advanced materials. By combining electrochemical reduction with 3D printing technology, the study successfully produces high-performance carbon nanocomposites from CO2. The process not only helps reduce greenhouse gases but also promotes sustainable manufacturing practices.
The findings highlight the potential for further development and commercialization of this technology, pointing to a more sustainable future in material science and engineering. This work underscores the value of interdisciplinary approaches in addressing environmental challenges while advancing material innovation.
Journal Reference
Crandall B.S., et al. (2024). Transforming CO2 into advanced 3D printed carbon nanocomposites. Nature Communications 15, 10568. DOI: 10.1038/s41467-024-54957-w, https://nature.com/articles/s41467-024-54957-w