• We have developed a new polymer-blending technique with only a high-shear flow field without any additives.
• We have enabled nano-scale dispersion of immiscible polymers by blending with high-shear processing; the domain sizes of the dispersed polymer phase are over one order smaller than those using conventional methods.
• High-performance ferroelectric-polymer blends prepared using high-shear processing have enabled the development of flexible, wide-area piezoelectric devices (aqua sonar and sound insulation materials).
Synopsis
In the National Institute of Advanced Industrial Science and Technology (AIST; Yoshikawa Hiroyuki, President), Shimizu Hiroshi (Nanostructured Materials Group, Group Leader) et al. of the Nanotechnology Research Institute (Yokoyama Hiroshi, Director) have developed a new polymer-blending technique using high-shear flow field, and succeeded in making miscible-polymer blends with nano-dispersion structures. Using this technique, we have succeeded in blending polyvinylidene fluoride (PVDF) and polyamide 11 (PA11) without any additives, which have been very hard to mix with each other at the nano-level until now, and have prepared blends in which PA11 with a domain size of ten to several tens of nanometers (1 nm = 10-9 m) is homogeneously dispersed densely in the PVDF phase (Figure 1).
Until now, for immiscible polymer blends, additives have been used for nano-dispersion, but they work as impurities and cause defects, resulting in problems for practical use. On the other hand, it has been considered that there is a lower limit to the domain size of the dispersed polymer phase when using purely mechanical blending.
In this work, we have, for the first time in the world, realized nano-dispersion structures in polymer blends with a high-shear processing technique but without any additives; the dispersed domain sizes obtained are over one order smaller than the previous limit value. Furthermore, we have found that the nano-structures can remarkably enhance the mechanical properties of the blends. Our method is also considered to be useful for inorganic dispersants such as carbon nanotubes, and thus can be applied to medicines and cosmetics. Moreover, as not only blending but also cross-linking reactions can be done at the same time under a high-shear flow field, the creation of new elastomers can be expected.
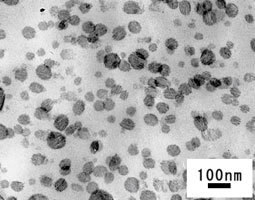
Figure 1. A transmission electron microscope image of a PVDF/PA11 blend prepared using high-shear processing. PA11 of ten to several tens of nanometers in diameter (round black parts) is homogeneously dispersed densely in the PVDF matrix (white background region).
Background For Research Work
Polymers have been used as functional, high-performance, and basic materials in a wide range of industrial fields. However, single polymers alone cannot respond to a variety of industrial needs, and thus multi-component polymer systems such as blends, alloys, and composites are currently used to create high-performance materials. However, most of the useful polymers are almost immiscible at a molecular level. Even if they are mechanically blended after being melted, they soon exhibit phase separation. In addition, the domain sizes of the separated dispersed polymer phase are several to several tens of µm.
For this reason, the hoped-for physical properties of the polymer blends have not been obtained. Thus, methods for making immiscible polymers compatible by using compatibilizing agents or by reacting polymer ends at interfaces (reactive processing) have been developed, but they have had technical limits; for electronic materials using the former method, the additives may be considered impurities, and also cause defects, resulting in a big obstacle to the enhancement of material performance, and for the latter method, a reduction in physical property performance due to sub-reactions has been pointed out.
History Of Research Work
AIST has advanced basic research into a simple, clean technique to create nano-dispersive immiscible-polymer blends. For the nano-technology program, "Project on Nanostructured Polymeric Materials" (in the fiscal years 2001-2004) of the New Energy and Industrial Technology Development Organization (NEDO), we have carried out in-situ phase behavior analyses of polymer blend systems under external fields, and thereby we felt that the nano-dispersion blend of immiscible polymers must be realized by applying a high-shear flow field.
Conventional extruders cannot generate high enough shear rates, and thus we have jointly developed with Imoto Seisakusho Co., Ltd., an extruder enabling the generation of high-shear rates of over 1000 sec-1.
Details Of Research Work
The high-shear extruder developed can generate a shear rate of 4400 sec-1 at a screw rotation speed of 3000 rpm. Also, using a feedback-type screw, the mixing time can be set arbitrarily, rotating the screw at high-speed. In other words, this extruder can remain for a long time in the state of high-shear flow.
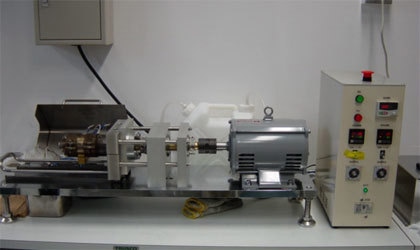
Figure 2. The high-shear extruder we have developed
Using this extruder, we have succeeded in preparing miscible blends of immiscible polymers, PVDF and PA11; PA11 with a domain size of ten to several tens of nanometers in diameter is homogeneously dispersed in the PVDF matrix. The nano-structures prepared can dramatically enhance the physical properties of the blends. For example, Figure 3 shows stress-strain curves for PVDF/PA11 = 80/20 blends.
As shown in curve a, a blend sample formed by a conventional technique shows only a little elongation, while a sample prepared by the high-shear extruder developed exhibits a large elongation at breakup, as shown in curve b, corresponding to five times larger than that of the sample in curve a, because the PA11 phase with a domain size of several tens of nanometers in diameter is dispersed in the PVDF region.
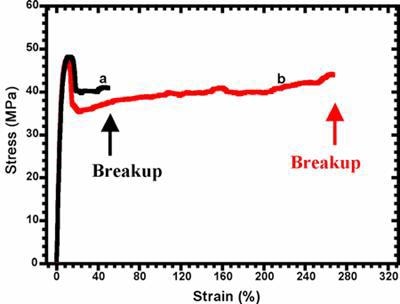
Figure 3. Stress-strain curves of PVDF/PA11 = 80/20 blend systems
a. for a PVDF/PA11 = 80/20 blend formed by a conventional blending method
b. for a PVDF/PA11 = 80/20 blend formed by a high-shear extruder
PVDF and PA11 are ferroelectric polymers, and blends of them with nano-dispersion structures are expected to have excellent ferroelectricity. Table 1 shows remnant polarization values (Pr: values of electric displacement D at an electric field E = 0) in ferroelectric hysteresis (D-E curve) for PVDF/PA11 = 80/20 blends prepared using a conventional machine and our high-shear extruder. The Pr value of PA11 is approximately half that of PVDF (Pr = 76), and thus, the Pr value of the blends is expected to reduce by blending. However, we have found that the Pr values of the nano-dispersion blend systems formed by our high-shear extruder are comparable to or exceed that of PVDF.
Table 1. Comparison of remnant polarization values in ferroelectric hysteresis of PVDF/PA11 = 90/10 blends prepared by a conventional blending method and our high-shear extruder
Moreover, as clearly shown in Table 1, the blend samples obtained by our high-shear extruder show Pr values 3-4 times those of blend samples prepared by a conventional method. This may be due to the formation of nano-dispersion structures in the samples in the high-shear blending process. As shown above, a high-shear processing technique enables not only the formation of nano-structures for PVDF/PA11 blends, but also a great enhancement of their adhesion performance and mechanical properties, such as elongation, which are disadvantages for PVDF, leading to the creation of new high-value added materials. The evaluation of ferroelectricity of the polymer blends used was jointly carried out with Tokyo University of Science (Prof. Takeo Furukawa, Faculty of Science Division I, Chemistry).
Future Prospects
We plan to apply our high-shear processing technique to a variety of polymer blend systems to create new materials utilizing enhanced polymer-miscibility and nano-dispersion structures. Furthermore, we plan to use our technique for the creation of new nano-composite materials, because high-shear flow field can also be useful to disperse fillers well, e.g., clays (layered silicate), carbon black, carbon nano-tubes, etc. in matrix materials.
In particular, our technique can be used as a clean method for the production of medicines and cosmetics, because it enables nano-scale dispersion without any additives such as compatibilizing agents. Furthermore, as our method can provide not only a high-shear flow field but also a reaction field, e.g., for dynamic cross-linking reactions, at the same time, it must also be useful for the creation of elastomers, etc. Thus, we aim at the creation and practical use of new materials by joint research with companies.
|