Polymer-based nanofibers are produced using a process called electrospinning. In this process, the polymer material (sometimes a polymer melt) is electrically charged and then subjected to an applied electrical field where the polymeric material is removed and 'whipped' from the source in fine 'needle-like' structures to form nanofibers.
.jpg)
Figure 1. Schema of electrospinning process
Image Credit: Inovenso
Electrospinning Process
A polymer melt or solution is fed towards the opening (where droplets can develop) of a needle tip/capillary. A high voltage is applied to charge a polymeric material. When this occurs, the electrostatic repulsion of like-charges counteracts the change in surface tension and the droplet becomes elongated/stretched.
When the stretching reaches a critical point, it becomes a charged jet of liquid. The liquid jet dires in flight, which then causes the flow and rheology of liquid changes, and the charges migrate and sit at the polymer jet’s surface. This charge migration makes the jet elongate (in a similar manner to the droplet stretching) and causes the jet to 'whip' (the whipping cannot be observed with eye as the fibers are very thin).
The whipping process is governed by the instability of the electrostatic charges repelling each other, which results in the fibers bending until they are collected on the ground. The ground collector can either be stationary or moving. If the ground collector is moving, it gives aligned fibers, and the stationary collector provides randomly aligned fibers which form a 'mesh'.
This process is efficient as it allows the fibers to form in a really thin, uniform, and elongated manner within a definite size range.
Electrospinning Machine
A standard electrospinning machine is made up of a syringe filled with the polymeric solution (spinneret), connected at its tip to a high voltage direct current power supply, a syringe pump, and a collector.
These standard parts are available with some variations such as the spinneret and the collector used for producing a variety of nanofibers:
- Spinneret: Needleless or multiple needle spinners
- Continuous feed membrane coating
- Collectors: rotating drum, rotating disc, mesh, etc.
Parameters
A number of parameters impact the final nanofiber product, which requires the use of standardized equipment. The parameters are listed below:
- Concentration, surface tension, viscosity, and molecular weight of the polymeric solution
- Feeding rate of the polymeric solution
- Collection technique; for example, speed of rotation of rotary drum or rotary disc
- Voltage distance and difference between the collector and the spinneret
- Ambient parameters such as temperature should be monitored
In order to create quality nanofibers for every application, it is important to manage all of the process parameters.
NANOSPINNER
To obtain nanofibers with preferred properties, it is very important to control all of the process parameters and to intervene in the processes in necessary changes. The NANOSPINNER from Inovenso, is an electrospinning product that has been introduced into the market and attracts attention with customer satisfaction.
NANOSPINNER electrospinning machines help researchers in over 25 countries with the ability to form nanofibers with varied specifications and with high quality equipment, and safe and stable performance.
A nanofiber is a nano-object possessing a diameter of one billionth of a meter. The nanofibers can easily be manufactured through electrospinning, which is the most standard and commercially used manufacturing method. In this process, an electrified polymer solution is moved in a high voltage electric field to produce elongated nanofibers.
Several nanofibers are placed one over the other to form a nanofiber web/nanofiber mat. A nanofiber mat is a breathable fabric, but it has very small pores that do not allow the entry of bacteria.
Based on these properties, nanofibers can be used in numerous applications in various fields such as filtration, tissue repair, semiconductors, catalysts, optical waveguides, composites, fuel cells, and sensors in industries such as chemical, mechanical, energy, electronics, aerospace, automotive¸and instrumentation.
Due to its easy and economical production and its probable technical benefits, nanofibers have been a focus point in several studies especially in the last two decades (Figure 2).
.jpg)
Figure 2. Documents published between 1996-2016 with “electrospinning or nanofibers” in “Title, Abstract, Keyword” parts in Scopus Database
Image Credit: Inovenso
Sources and Further Reading
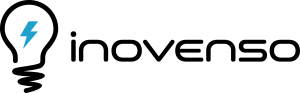
This information has been sourced, reviewed and adapted from materials provided by Inovenso.
For more information on this source, please visit Inovenso.