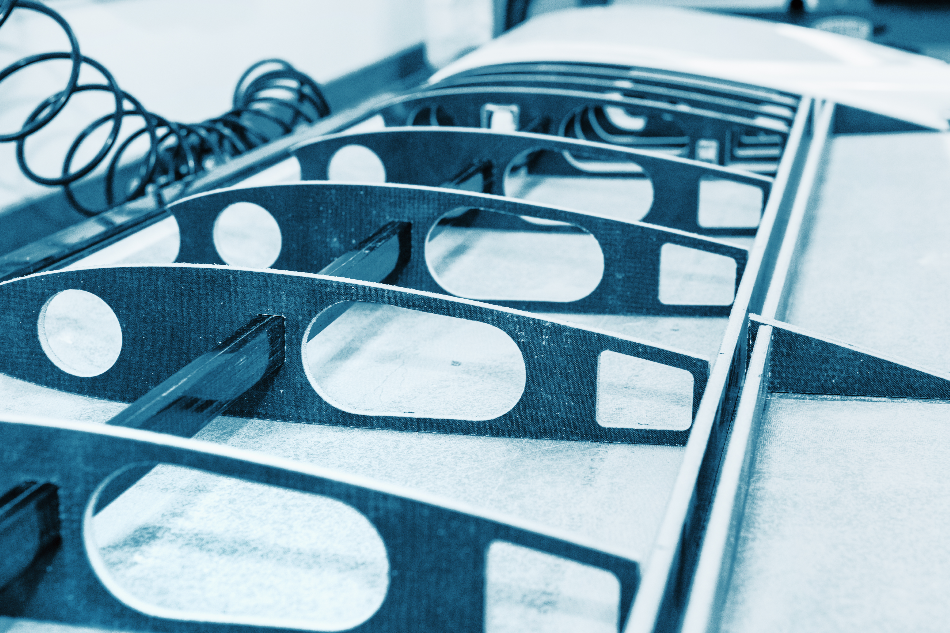
Nadezda Murmakova / Shutterstock
Aircraft are expected to function in incredibly harsh conditions; they experience extreme temperatures, shock loads, friction and vibration. This can jeopardize the integrity of the aircraft’s components, but these challenges can be addressed with the use of specialist alloys and high-performance materials.
An alloy is an amalgamation of metals or one or more metals with non-metallic elements. They can impart beneficial qualities to the metals, improving their fatigue and tensile strength properties, giving them high conductivity and strength or improving their wear and corrosion resistance, for example.
Aluminum
Aluminum has a long history in the aerospace industry; the Wright Brothers chose it for the cylinder block and other engine parts for their first manned flight in 1903. This was also the first time an aluminum alloy had been heat-strengthened.
Forty years ago, the metal dominated the industry because it exhibits high corrosion resistance, is inexpensive and is also lightweight – around 70% lighter than steel. Around 70% of an aircraft was once made of aluminum, while other composites and alloys of titanium, graphite, and fiberglass were used in small quantities.
But over time, the demands of the industry have increased; long-haul and international flights mean aircraft shells and engine parts need to be durable and resistant to fatigue, in addition to being more light-weight and resistant to high temperatures.
Today, as little as 20% of an aircraft is constructed from pure aluminum, mostly in non-critical structures materials like paneling and aesthetic interiors. Here are just two examples of aluminum alloys:
AA2014 is an alloy of aluminum, chromium, copper, iron, and magnesium amongst several other elements; its strong, tough and suitable for arc and resistance welding. However, it exhibits poor corrosion resistance so it is usually found in internal structures rather than the outer shell.
AA2024 is a widely used alloy consisting of aluminum, copper, silicon, and iron as well as other elements. This high-grade alloy exhibits excellent fatigue resistance and is often used in sheet form for the fuselage and wings due to its high tensile strength.
It is expected that the demand for aluminum will increase, reaching 80 million tons by 2025. Recycled alloys are being targeted to help satisfy demand, alongside a push for innovative new materials such as alloys of aluminum, nickel and titanium, and improved aircraft design.
New Super-Alloys
The engine is one of the most complex parts of the aircraft, home to many individual components and ultimately responsible for fuel-efficiency. Temperatures inside the engine can climb as high as 2,100 °C – current super alloys melt at 1,850 °C, so new materials capable of withstanding such extremes have been developed.
While standard aluminum alloys still have a use in aerospace, they are giving way to new materials designed to improve cost and performance. Heat-resistant super alloys (HRSAs) include amalgamations of titanium and nickel, alongside non-metal composite materials like ceramics. Nickel alloys have been chosen for their ability to resist extremely high temperatures, corrosion, and constant wear, and for their magnetic properties. They are structurally some of the toughest materials available, in addition to being good conductors of electricity.
Titanium aluminide and aluminum-lithium have been in use since the 1970s, but are now being used in new and novel ways in the aerospace industry. Aluminum lithium alloys exhibit high strength, low density, high stiffness, damage tolerance and corrosion resistance and are weld-friendly and are considered better than traditional aluminum. They are considered an advanced material because of their low density, high specific modulus, and excellent fatigue and cryogenic toughness.
Titanium aluminide retains its strength and corrosion resistance in temperatures of up to 600 °C and has the potential to improve the thrust-to-weight ratio in engines as it is half the weight of nickel alloys. Low-pressure blades and high-pressure compressor blades once made of a nickel-based superalloy are now constructed from titanium aluminide.
Ti 5553 - an alloy of titanium, aluminum, vanadium, molybdenum, and chromium – is reasonably new to the industry and boasts high strength, good corrosion resistance and is lightweight. It is being utilized for structural components as any issues with machinability have been overcome.
Composite materials are also growing in use; these are helping to reduce weight and increase fuel efficiency. Furthermore, they are easy to handle, design, shape, and repair and are being employed for wing and fuselage skins, engines and landing gear.
Conclusion
Advanced alloys impart beneficial properties such as weight reduction, fatigue resistance and corrosion resistance to metals used in today’s aircraft, thus helping to improve performance and cost in the aircraft industry.
Sources
Disclaimer: The views expressed here are those of the author expressed in their private capacity and do not necessarily represent the views of AZoM.com Limited T/A AZoNetwork the owner and operator of this website. This disclaimer forms part of the Terms and conditions of use of this website.