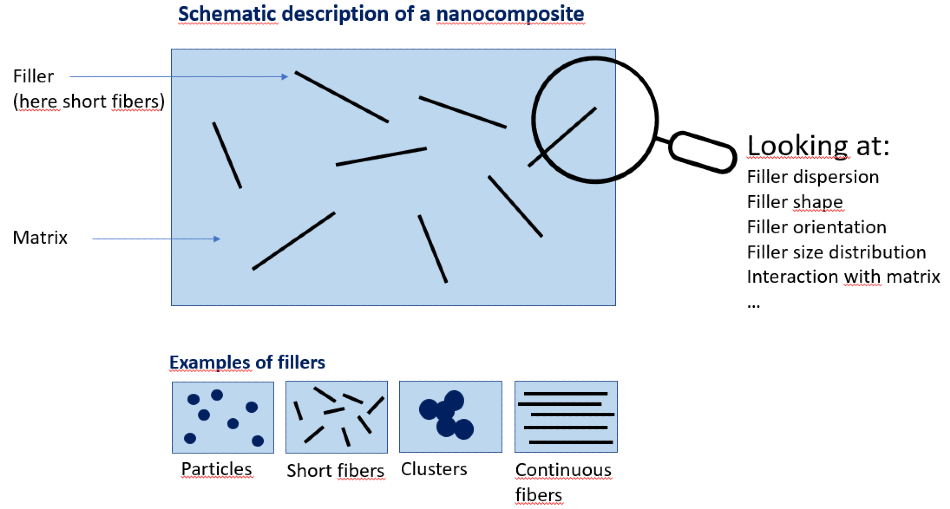
Nanocomposites are igniting exciting discussions across various industries right now, including the automotive industry, due to them being a supreme class of high-performance materials.
They incorporate a series of desirable attributes including low-cost yet high-performance materials with the potential to exhibit thermal, mechanical, and processing properties that are valuable for automotive manufacturing.
Their bulk properties are determined by their structure on the nanoscale, therefore, the accurate analysis of small-scale structure is necessary to the characterization and development of nanocomposites. X-ray scattering technology provides unprecedented insight into the many parameters that affect nanocomposite properties.
Nanocomposites are a class of materials known as composites in which nanoscale particles or fibers (the filler) containing one or more materials are dispersed across a bulk (matrix) material. While the filler(s) and the matrix maintain elements of their own bulk material properties, the nanoscale parameters of the fillers supply a unique set of features to the nanocomposite.
Some of these variables include shape, orientation, dispersion, and size distribution of the filler particles, as well as their interaction with the bulk matrix.1-4
Therefore, nanocomposites can be adapted during production by altering the physical and chemical properties of the constituent materials, making them a broad class of materials with novel properties.
Using microscopy for acute analysis of such materials produces vital information about the individual geometries of nanoparticles in composite materials; however, this technique falls short when it comes to delivering statistical information about nanoparticle size distribution and volume fraction. Therefore, microscopy techniques cannot provide a relevant characterization of variations across a sample of substantial volume. Furthermore, the effectiveness of microscope analysis is limited as many nanocomposite materials involve overelaborate sample preparation, or they are opaque to visible light.
Small-Angle X-Ray Scattering for Nanocomposites Characterization
Small-Angle X-ray Scattering (SAXS) can solve these issues when it comes to the statistical analysis of nanoparticles in nanocomposite materials. SAXS can establish precise nanoscale parameters, such as the size distribution of nanoparticles in nanocomposites within a key statistic volume (usually around 1 mm3).8
Figure 1 displays an example of measurements with SAXS in the case of nanocomposites with highly ordered layered structures generated with a new manufacturing strategy.6
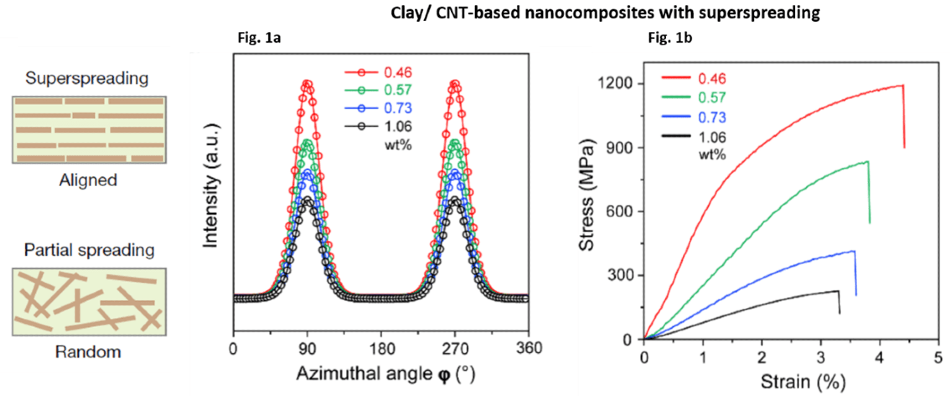
Figure 1. X-ray scattering measurements and mechanical properties of Clay/CNT-based nanocomposite films produced by a new method of shear-flow-induced alignment of nanosheets (superspreading). Fig 1a: 1D plots of X-ray scattering intensity depending on azimuth angle for different concentrations of nanofillers (in wt%, see key)-orientation ordered parameter and nanosheets interlayer distance can be calculated (not shown). Fig 1b: corresponding stress-strain curves for the different nanocomposites. Adapted from Zhao, C., Zhang, P., Zhou, J. et al. Layered nanocomposites by a shear-flow-induced alignment of nanosheets (Supplementary Data). Nature 580, 210–215 (2020).
Application in the Automotive Industry
Requirements for low emissions and fuel economy in the automotive industry means that there is an increasing demand for lightweight structural materials in vehicles: nanocomposites offer such solutions.5 Nanocomposites provide comparable or improved reliability to metals, so a switch to nanocomposite materials could offer considerable weight reductions without placing structural integrity in jeopardy.
Additionally, the novel properties of nanocomposites can also enhance the properties of non-structural components; including increased durability, corrosion resistance, and noise dampening qualities.5 UV-shielding can also be achieved through the material integration of nanocomposites.7
Car tires already exhibit how the extensive application of nanocomposites can be beneficial to the automotive industry. The durability required of tires can be intensely demanding, however, it can also be realized through the use of nanocomposite fillers. Enhancing tires with silica nanoparticles or carbon black has previously demonstrated deformation resistance and higher strength than unfilled rubber polymers. Analysis of silica clusters in rubber has facilitated the discovery of new materials for the development in the manufacture of tires.
X-Ray Scattering for Multiscale Filler Structure Characterization
Committing to structural analysis at a range of length scales offers a meaningful and in-depth understanding of the properties of a nanocomposite material: from the overall geometry to the surface structure, as well as the characterization of nanoparticle clusters and agglomerates of various scales.
A typical SAXS setup allows measurement of the radius of gyration (an indicator of size) of the individual particles and aggregates of particles.
Using a Bonse-Hart Ultra-Small- Angle X-ray Scattering (USAXS) setup it is possible to access larger length scales and acquire information about agglomerates, as shown in the curve below. Throughout this case, simulation of the curve provided key information about individual particle size as well as cluster and agglomerate sizes alongside fractal dimensions at 3 length scales.
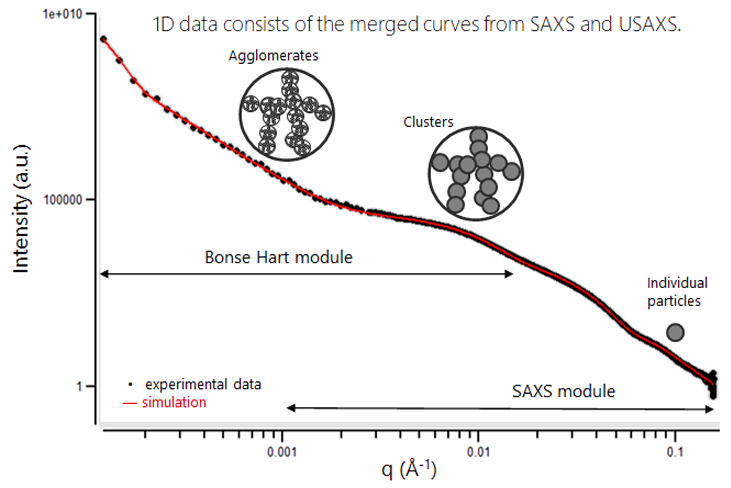
Figure 2. Combined SAXS and USAXS experimental curve of silica clusters in rubber (sequential automatic measurement performed on a Xeuss) and multiscale fit model. Graphic inserts show a different type of particles analyzed.
Therefore, utilizing SAXS technology to gather information concerning a size distribution of filler particles in nanocomposites, alongside microscopy techniques to characterize single particles, achieves a comprehensive and information-rich description of nanocomposite structure.
Rapid analysis of results using standard models can be especially useful when comparing different formulation parameters of samples. Furthermore, there has been significant development where quantitative models of the complex filler structure of industrial nanocomposites are concerned. For example, the use of high-performance microscopy methods such as Tunneling Electron Microscopy (TEM) together with SAXS can generate a complete characterization of inter-aggregate interactions, aggregate polydispersity, and compacity in addition to a full hierarchical structure.9
The Xenocs Xeuss 3.0 is a high-performance SAXS beamline for laboratory use, designed to aid Small-, Ultra-Small-, and Wide-Angle X-ray Scattering (SAXS, USAXS, and WAXS) for soft matter and nanomaterial analysis. Quick characterization of filler networks in nanocomposites such as bio-rubber,10 carbon black filler for rubber,11 or graphene oxide with Poly(ethylene methyl acrylate) is possible using the Xeuss.12
Configurable for a wide range of length scales, the Xeuss can effectively provide particle size distributions from a few nanometers to 350 nm, and an additional Bonse-Hart USAXS add-on permits the definition of large structures over 4 μm. Despite its state-of-the-art capabilities and unrivaled analysis, the Xeuss is designed with ease-of-use in mind: configurable for fully remote operation, its adaptable, large vacuum chamber with the stationary sample during measurement offers maximum versatility. 13
References and Further Reading
- Genix, A.-C., Bocharova, V., Carroll, B., Lehmann, M., Saito, T., Krueger, S., He, L., Dieudonné George, P., Sokolov, A.P., Oberdisse, J.. Understanding the Static Interfacial Polymer Layer by Exploring the Dispersion States of Nanocomposites. ACS Appl. Mater. Interfaces 11, 17863–17872 (2019).
- Zhang, P. & Kraus, T. Anisotropic nanoparticles as templates for the crystalline structure of an injection-molded isotactic polypropylene/TiO 2 nanocomposite. Polymer. 130, 161–169 (2017).
- Pletsch, H., Tebbe, M., Dulle, M., Förster, B., Fery, A., Förster, S., Greiner, A. & Agarwal, S., Reversible gold nanorod alignment in mechano-responsive elastomers. Polymer. 66, 167–172 (2015).
- Heinrich, G., Klüppel, M. & Vilgis, T. A. Reinforcement of elastomers. Opin. Solid State Mater. Sci. 6, 195–203 (2002).
- Garcés, M., Moll, D. J., Bicerano, J., Fibiger, R. & Mcleod, D. G. Polymeric Nanocomposites for Automotive Applications. Adv. Mat., 12, 1835-1839 (2000).
- Zhao, C., Zhang, P., Zhou, J., Qi, S., Yamauchi, Y., Shi, R., Fang, R., Ishida, Y., Wang, S., Tomsia, A.P., Jiang, L., Liu, M., Layered nanocomposites by shear-flow-induced alignment of nanosheets. Nature, 580, 210–215 (2020).
- Olson, E., Li, Y., Lin, F.-Y., Miller, A., Liu, F., Tsyrenova, A., Palm, D., Curtzwiler, G.W., Vorst, K.L., Cochran, E. & Jiang, S., Thin Biobased Transparent UV-Blocking Coating Enabled by Nanoparticle Self-Assembly. ACS Mater. Interfaces 11, 24552–24559 (2019).
- Size distribution of nanoparticles: powders, dispersions and composites. Available at: https://www.xenocs.com/size-distribution-of-nanoparticles-powders-dispersions-and-composites/
- Oberdisse, J., Pyckhout-Hintzen, W., Straube, E., Structure Determination of Polymer Nanocomposites by Small Angle Scattering, Recent Advances in Polymer Nanocomposites, Chapter 12 (2019).
- Manoharan, P. & Naskar, K. Biologically sustainable rubber resin and rubber-filler promoter: a precursor study. Adv. Technol. 28, 1642–1653 (2017).
- Mondal, T., Bhowmick, A.K., Ghosal, R., Mukhopadhyay, R., Expanded Graphite as an Agent Towards Controlling the Dispersion of Carbon Black in Poly (Styrene –co-Butadiene) Matrix: An Effective Strategy Towards the Development of High Performance Multifunctional Composite, Polymer, 146, 31-41 (2018).
- Ganguly, S., Mondal, S., Das, P., Bhawal, P., Das, T.K., Ghash, S., Remanan, S. & Das, N.C., An Insight Into the Physico-Mechanical Signatures of Silylated Graphene Oxide in Poly(ethylene methyl acrylate) Copolymeric Thermoplastic Matrix. Macromol. Res. 27, 268–281 (2019).
- USAXS SAXS WAXS Nanostructure – Lab Beamline Characterization. Available at: https://xenocs.com/products/xeuss-3-0/.
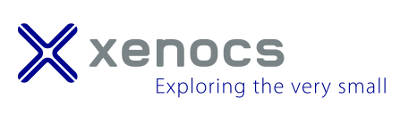
This information has been sourced, reviewed and adapted from materials provided by Xenocs.
For more information on this source, please visit Xenocs.