Nitinol – pronounced night-in-all – is a nickel-titanium alloy that demonstrates a unique ability, the capacity to change its shape, dependent on the surrounding environment. In this article, we discuss the benefit nanotechnology has brought to the development of nitinol.
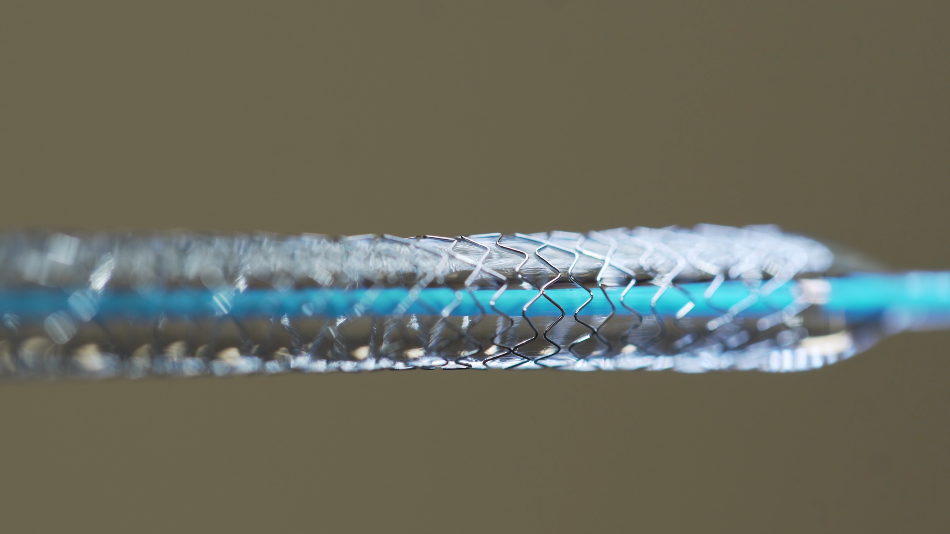
Image Credit: Alexpunker/Shutterstock.com
What is Nitinol?
Nitinol's name is derived from its alloy composition and place of discovery; Nickel Titanium and the Naval Ordinance Laboratory in America. In 1959, William J Buehler attempted to design better missile cones to resist fatigue, heat, and force of impact. His 1:1 alloy of nickel to titanium was first demonstrated in 1961 when its potential was quickly realized, although not commercialized until a decade later.
The shape memory alloy can be deformed when cold but returns to its original shape when heated. Nitinol's unique properties derive from a reversible solid to solid-state transformation and make it one of the most utilized shape memory alloys. Nitinol exhibits a shape memory effect and superelasticity – an elastic or reversible response to applied stress, caused by a phase transformation. Nitinol also displays low stiffness, biocompatibility, and corrosion resistance.
Its uses are common for many engineering applications, including sensors, actuators, smart structures, biomedical implants such as nitinol stents, and aerospace components.
What are Shape Memory Materials?
Nanotechnology employs the unique physical properties and interactions of nanoscale materials to create novel structures, devices, and systems.
Shape memory materials are a class of nanomaterials that respond to environmental changes; they can be designed to respond dramatically upon exposure to energy input, such as heat, light or electricity. Shape memory materials, like shape memory alloys, can remember their original shape and have many applications, including heart stents, actuator wires and couplings that close with heat.
Most materials undergo phase changes under heat treatment – from solid to liquid to gas – at specific transition temperatures. Because of the structure of nitinol, it experiences a solid-to-solid change. Rather than undergoing a phase change when it reaches its transition temperature, nitinol uses the energy to move atoms into a different arrangement – it changes shape but remains solid.
Like others, nitinol alloys have a crystalline structure with atoms arranged to minimize energy; this repeated pattern is a lattice of points, either atoms, ions or molecules. When thermal or mechanical input is applied, nitinol undergoes a crystal structure phase transformation. This high-temperature phase is known as austenite and has a very ordered cubic structure, known as its austenite structure.
When cooled below a set temperature, nitinol's austenite structure transforms to its martensite phase and has a plastic, deformed shape. The nitinol alloy will hold its deformed shape until it is heated back to its transition temperature, where atoms move back to their original location and the metal returns to its original, rigid shape.
Challenges of Nitinol Uses
It is difficult to make nitinol due to the exceptionally tight compositional control required and the high reactivity of titanium. Every atom of titanium that combines with oxygen or carbon is an atom taken from the nitinol lattice, thus shifting the transformation temperature lower.
There are two primary methods, both of which have their advantages:
- Vacuum arc re-melting (VAR); a casting process where a consumable electrode is melted under a vacuum at a carefully controlled rate using heat generated by an electric arc struck between the electrode and the ingot.
- Vacuum induction melting (VIM); an alternating magnetic field heats the raw material in a crucible, under a high vacuum.
Nitinol is easier to work with when hot rather than cold. Machining of the alloy is also extremely difficult, although it is easy to perform grinding, laser cutting and Electrical Discharge Machining (EDM) on this shape memory material. The material may also undergo casting and powder metallurgy processes and additive manufacturing, which is effective in producing highly complex geometries with pre-designed porosity, composition, and properties.
Laser-based additive manufacturing techniques are increasingly being used to produce nitinol parts, with selective laser melting emerging as an effective means of producing the nitinol alloy with desirable functional properties. Powder quality and material composition can influence microstructure and phase transformation. Equi-atomic nitinol has the most uniform and finest grains, which are necessary for high-density fabrication. The particle size also affects the flowability and packing density of the feedstock during fabrication.
References and Further Reading
Chekotu, J., Groarke, R., O’Toole, K. and Brabazon, D., (2019) Advances in Selective Laser Melting of Nitinol Shape Memory Alloy Part Production. Materials, 12(5), p.809. https://www.mdpi.com/1996-1944/12/5/809
National Nanotechnology Infrastructure Network. Nanotechnology Invention and Design: Phase Changes, Energy, and Crystals [online]
Disclaimer: The views expressed here are those of the author expressed in their private capacity and do not necessarily represent the views of AZoM.com Limited T/A AZoNetwork the owner and operator of this website. This disclaimer forms part of the Terms and conditions of use of this website.