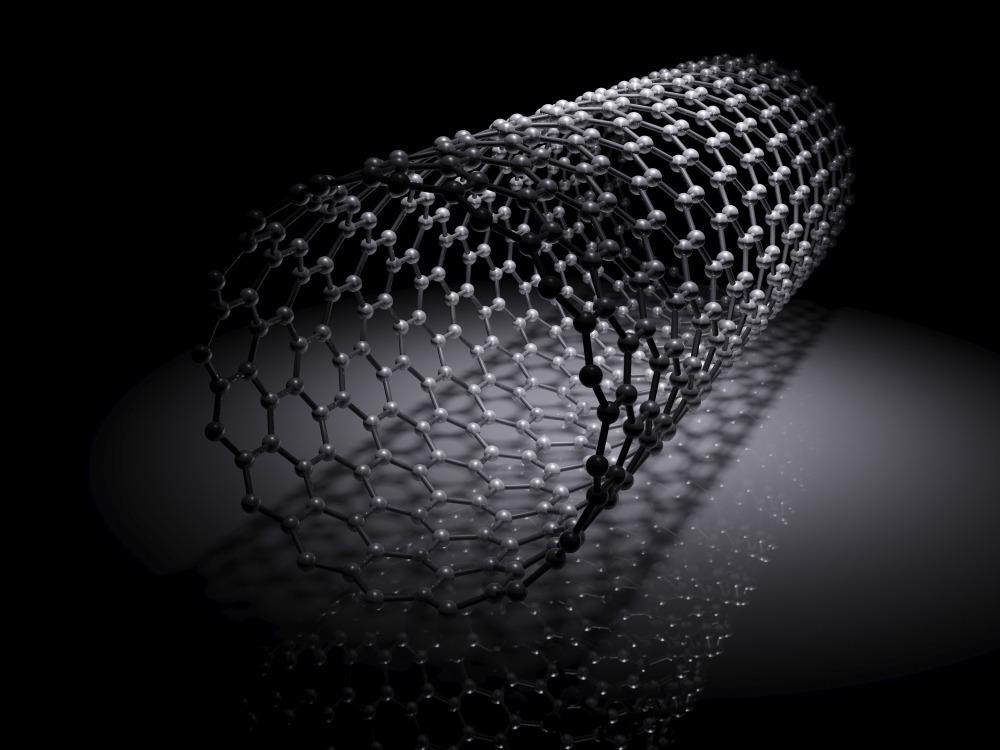
Image Credit: Evannovostro/Shutterstock.com
New materials with improved mechanical properties are constantly needed to keep up with the rapid advancements in the mechanical industry. Graphene and carbon nanotube-reinforced metal matrix composites (MMCs) are promising types of materials that can be used as an alternative to improve the properties of common metals such as aluminum.
Advantages and Limitations of Aluminum
Throughout the years, aluminum has found many applications, ranging from household items to making automobile components and missile bodies.
In recent years, its use in the manufacturing and mechanical industries has increased significantly. This has resulted in the constantly growing demand for the material.
Being the third most abundant element on earth, aluminum and its alloys are some of the most commonly used materials in the mechanics industry, after steel and iron. Aluminum alloys have the advantage of being simultaneously light and strong, as well as having good corrosion resistance and thermal properties.
Alongside its numerous applications and advantages, aluminum has several limitations, such as its high thermal expansion coefficient and inferior tribological properties. These limitations can be overcome when using different fillers and creating MMCs.
Metal Matrix Composites
MMCs are a group of materials, such as metals and alloys, incorporated with reinforcing fillers. They are made out of matrix and reinforcement – the matrix is a monocrystalline continuous material, such as aluminum or magnesium, in which the reinforcement is embedded. Having at least two constituent parts, MMCs are heterogeneous at the microscale but homogeneous at the macroscale.
Compared to monolithic material, MMCs are much stronger and have higher stiffness while being lighter and showing greater corrosion resistance. Another advantage is that they do not change or lose their properties under extreme conditions.
Although MMCs are very promising for many industries, they still have some disadvantages compared to monolithic materials. For example, they are much more expensive to produce and have been shown to be inferior in terms of toughness.
A way to overcome these limitations is by using macro reinforcements such as silicon carbide and titanium dioxide. The materials produced after adding the macro reinforcements have improved mechanical properties at a reduced cost.
Overcoming Limitations Using Nanomaterials
Another way to overcome these limitations is by using carbon-based nanomaterials such as nanodiamonds, graphene oxide, and carbon nanotubes. They have better mechanical properties compared to macro reinforcements and their use improves the tensile strength and toughness of MMCs.
Using graphene oxide as a nanofiller improves the hardness of the composite as well as its yield strength, and the use of carbon nanotubes enhance the ductility of the MMC. Nanoscale reinforcement also improves the functional properties of materials.
Graphene-based nanofillers can be used to overcome the limiting tribological properties of aluminum and its alloys. Traditionally, different methods have been used to reduce friction and wear of materials, such as adding solid lubricant coating. However, this approach is not suitable when working under severe conditions such as very high or low temperatures, or high vacuum environments.
Carbon allotropes, such as carbon nanotubes and graphene oxide, show self-lubricating behavior, which can be used to improve the tribological performance of aluminum. They can be embedded in an MMC with an aluminum matrix to create a self-lubricating surface.
Many advancements have been achieved in the mechanical properties of aluminum using carbon-based nanofillers. Embedding graphene oxide and carbon nanotubes in aluminum MMCs has shown improvement in Young’s modulus, hardness, and tensile strength.
Due to their exceptional reinforcement properties, graphene oxide and carbon nanotubes are some of the most promising materials to be used for aluminum MMCs.
Future Developments
Although using carbon-based nanofillers for MMCs is a very promising advancement, the field is still relatively new, and more research into their use in the fabrication of MMCs is needed. For example, further developments are needed to increase their lifetime and reliability as well as improving some of their properties such as oxidation and corrosion behavior.
Another big challenge is the uniform dispersion of the graphene or carbon nanotubes into the material when working with large volumes.
Aluminum-based MMCs find applications in many fields such as aerospace, automobile parts, and electronics industries. When engineers overcome the posed challenges, these materials could replace traditionally used metals in many of the engineering sectors, offering better quality and more sustainable production.
References and Further Reading
[1] Khanna, V., Kumar, V., and Bansal, S. A. (2021). Mechanical properties of aluminum-graphene/carbon nanotubes (CNTs) metal matrix composites: Advancement, opportunities and perspective. Materials Research Bulletin. https://doi.org/10.1016/j.materresbull.2021.111224.
[2] Santos Jr, M. C., et al. (2016) Machining of aluminum alloys: a review. The International Journal of Advanced Manufacturing Technology. https://doi.org/10.1007/s00170-016-8431-9 .
[3] Chawla, K. (2012) Metal Matrix Composites. Composite Materials. pp 197-248. https://doi.org/10.1007/978-0-387-74365-3_6.
[4] Bains, P. S., Sidhu, S. S., and Payal, H. S. (2016). Fabrication and machining of metal matrix composites: a review. Materials and Manufacturing Processes. https://doi.org/10.1080/10426914.2015.1025976.
[5] Jawalkar, C. S., et al. (2017). Fabrication of aluminum metal matrix composites with particulate reinforcement: a review. Materials Today: Proceedings. https://doi.org/10.1016/j.matpr.2017.02.174.
[6] Tabandeh-Khorshid, M. et al., (2016). Tribological performance of self-lubricating aluminum matrix nanocomposites: role of graphene nanoplatelets. Engineering science and technology, an international journal. https://doi.org/10.1016/j.jestch.2015.09.005.
Disclaimer: The views expressed here are those of the author expressed in their private capacity and do not necessarily represent the views of AZoM.com Limited T/A AZoNetwork the owner and operator of this website. This disclaimer forms part of the Terms and conditions of use of this website.