By Owais AliReviewed by Frances BriggsJul 23 2025
Plastic waste could fuel the future, as new catalytic and thermochemical processes convert discarded plastics into valuable carbon nanotubes and clean hydrogen, boosting recycling and cutting emissions.
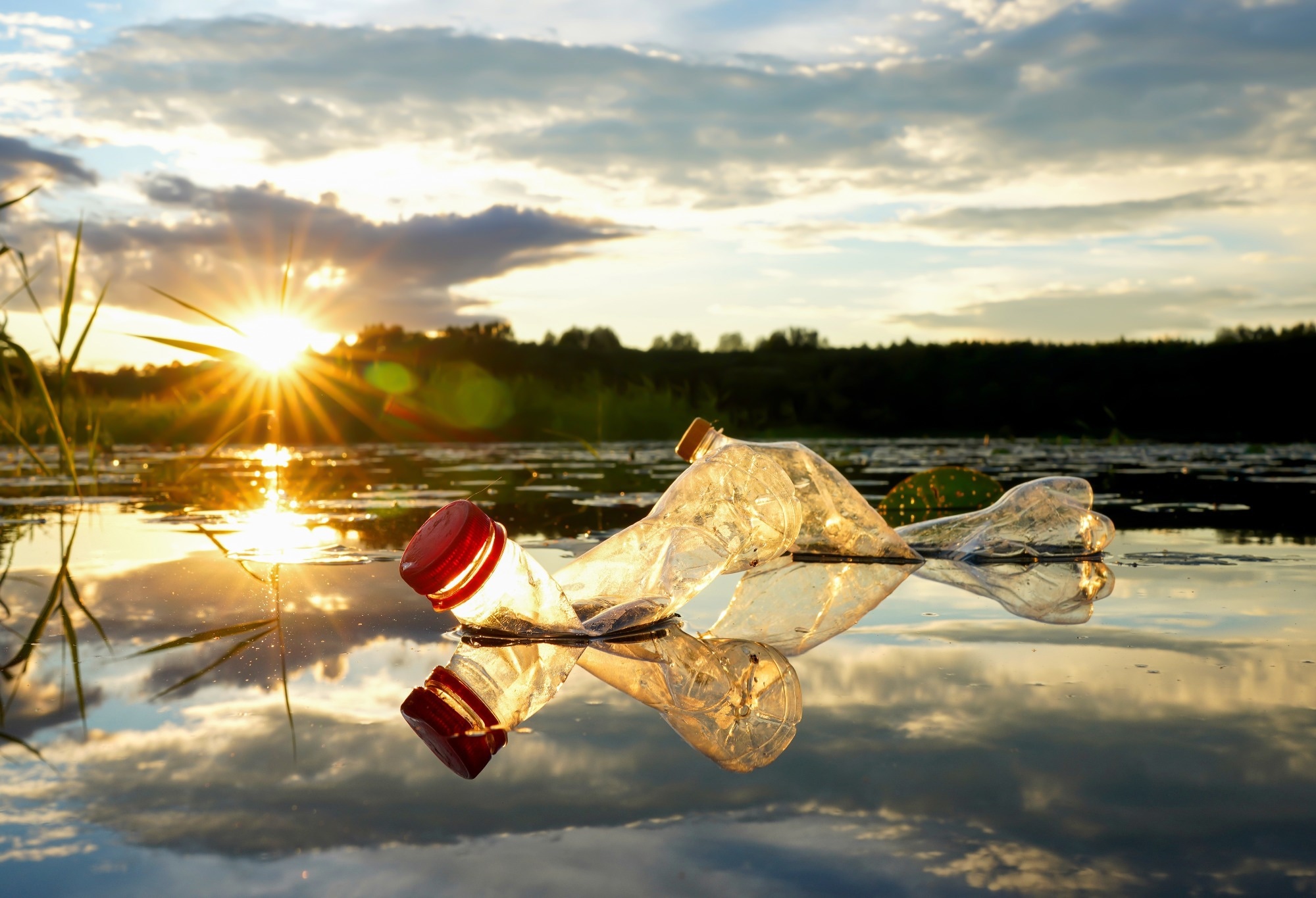
Image Credit: Maksim Safaniuk/Shutterstock.com
The global plastic waste crisis remains one of the most pressing environmental challenges in science. Now, researchers are developing innovative ways to turn non-recyclable plastic into high-value products, such as carbon nanotubes, that could help clean up pollution while powering a low-carbon economy.
Plastic Waste Upcycling
The widespread use of plastics across various industries stems from their exceptional properties. They're strong, light, and incredibly durable.
However, mass production, combined with limited disposal options, has led to the accumulation of approximately 8.3 billion tonnes of non-biodegradable plastic waste, with more than three-quarters simply thrown away. Incineration and landfilling are the predominant disposal routes, yet both have major environmental drawbacks and fall short of EU Directive 94/62/EC targets to recycle 50-55 % of plastic waste by 2030.1
Converting plastic waste into valuable products offers a sustainable alternative. Hydrogen serves as a clean energy carrier with growing relevance in decarbonization strategies, while carbon nanotubes offer exceptional mechanical, electrical, and thermal properties for applications in electronics, energy storage, and composite materials.
Turning plastic waste into these high-value products lightens the environmental load and makes recycling a more economically attractive option.2
Recent Advances and Pilot-Scale Technologies in Plastic Upcycling
CNT via Pyrolysis
Pyrolysis is one of the most commercially viable chemical recycling methods. It's a simple thermochemical process that involves heating plastics in the absence of oxygen to break them down into gases, liquids, and solids. Pyrolysis is particularly useful because it can process a wide range of plastics.
Recent studies have shown that carbon nanotubes (CNTs) can be synthesized from the gases produced during pyrolysis, boosting economic value while generating hydrogen as a co-product. A research team at Ulsan National Institute of Science and Technology has recently found a way to use waste mask materials in pyrolysis as feedstocks for carbon nanotubes and hydrogen.
By adding a high-temperature catalytic step, they converted the gases into high-purity CNTs and hydrogen, with no need to separate plastic types beforehand. Their results suggest that the process could be scaled up cost-effectively, especially if powered by renewable electricity, offering lower emissions than conventional CNT production.3
Microwave-Initiated Catalytic Plastic Upcycling
Microwave-assisted catalysis is another emerging approach. Instead of heating plastic waste uniformly, it localizes energy at specific points, triggering efficient chemical reactions.
This process uses microwave-absorbing catalysts such as FeAlOx to convert electromagnetic radiation into heat at the catalyst-plastic interface, triggering C–H bond cleavage via dehydrogenation.
The localized thermal environment promotes hydrogen desorption, yielding up to 55.6 mmol/g from HDPE, while carbon species form Fe3C, which facilitates the growth of carbon nanotubes.
A study published in the Chemical Engineering Journal showed the synthesis of low-cost, self-dispersing mono- and bimetallic iron–cobalt–nickel oxide catalysts via a simple, solvent-free one-step method.
These catalysts demonstrated high activity for microwave-assisted dehydrogenation of low-density polyethylene, producing hydrogen yields of 63.5, 63.2, and 60.2 mmol/g for Ni3Co3Ox, NiCo3Ox, and NiFe3Ox, respectively. With a selectivity of up to 83.7 vol %, this method achieved hydrogen yields two to three times higher than conventional thermal catalysis.
The improved performance is a result of the synergistic bimetallic interactions and acetate-derived carbon structures formed during calcination, which improve metal dispersion and inhibit alloy formation. 4
Tackling Hard-To-Recyle Plastics
Researchers at Nanyang Technological University have developed a two-stage process to convert particularly troublesome waste streams, such as contaminated food packaging and plastic bags, into high-value materials.
First, the plastic waste undergoes pyrolysis at approximately 900-1,000 °C, producing syngas with low hydrogen concentrations and various gaseous byproducts.
In the second stage, those gases are fed into reactors which catalytically convert them into carbon nanotubes via chemical vapor deposition mechanisms.
The resulting nanotubes are purified and functionalized using dry, water-free techniques that facilitate metal recovery without creating wastewater—a key goal of Singapore's Zero Waste Masterplan.5
Photocatalyzing Plastics
Photocatalysis offers another sustainable option. It uses sunlight and semiconductors to drive reactions, a lower-energy approach to plastic waste processing.
Plastic polymers act as sacrificial agents, donating electrons as they break down into useful molecules and release hydrogen gas. Co-products produced include glycolate, acetate, and ethanol.
A recent study published in the Journal of Colloid and Interface Science fabricated MXene/ZnxCd1-xS photocatalysts using a solvothermal method, optimized by varying the Zn/Cd ratio and MXene content.
The composites achieved a hydrogen evolution rate of 14.17 mmol g-1 h-1 in an alkaline polyethylene terephthalate (PET) solution while simultaneously degrading PET into useful organics. Their high efficiency was achieved by fine-tuning the catalyst's electronic properties to maximize light absorption and charge separation.6
Download your PDF copy now!
Future Outlooks
These technologies could help transform plastic into a truly circular material, providing both clean energy and advanced materials.
However, their widespread implementation depends on developing cost-effective catalysts, optimizing processes, and integrating renewable energy sources to ensure environmental benefits and economic viability.
Policy support and infrastructure investment will also be vital, creating demand for upcycled products and rewarding cleaner waste management.
If successful, plastic waste could shift from being a growing burden to a valuable resource waiting to be harnessed.
References and Further Reading
- Chen, Z., Wei, W., Chen, X., Liu, Y., Shen, Y., & Ni, B. (2024). Upcycling of plastic wastes for hydrogen production: Advances and perspectives. Renewable and Sustainable Energy Reviews, 195, 114333. https://doi.org/10.1016/j.rser.2024.114333
- Hosny, M., & Fawzy, M. (2024). From Waste to Worth: Upcycling Plastic into High-Value Carbon-Based Nanomaterials. Polymers, 17(1), 63. https://doi.org/10.3390/polym17010063
- Kim, H., Nam, E., An, K., & Lim, H. (2024). Laboratory-scale plastic upcycling and green growth: Evaluating the upcycling of plastic waste into carbon nanotubes from economic and environmental aspects. Chemical Engineering Journal, 495, 153300. https://doi.org/10.1016/j.cej.2024.153300
- Zhao, J. et al. (2024). Microwave-intensified catalytic upcycling of plastic waste into hydrogen and carbon nanotubes over self-dispersing bimetallic catalysts. Chemical Engineering Journal, 483, 149270. https://doi.org/10.1016/j.cej.2024.149270
- Nanyang Technological University. (2022). Turning plastic trash into clean hydrogen fuel. [Online]. Available at: https://www.ntu.edu.sg/news/detail/turning-plastic-trash-into-clean-hydrogen-fuel
- Cao, B. et al. (2021). Highly-efficient visible-light-driven photocatalytic H2 evolution integrated with microplastic degradation over MXene/ZnxCd1-xS photocatalyst. Journal of Colloid and Interface Science, 605, 311-319. https://doi.org/10.1016/j.jcis.2021.07.113
Disclaimer: The views expressed here are those of the author expressed in their private capacity and do not necessarily represent the views of AZoM.com Limited T/A AZoNetwork the owner and operator of this website. This disclaimer forms part of the Terms and conditions of use of this website.