The A-341 Hybrid XY/XYZ Gantry positioning system from PI (Physik Instrumente) LP with air bearing is available for high-performance automation.
Features
- Hybrid design: Gantry axis comes with recirculating ball-bearing guides and a bridge axis with air bearing
- Adaptable modular platform
- Absolute encoder
- Several travel ranges. Options and customized adaptations
- High-performance ironless linear motors are available
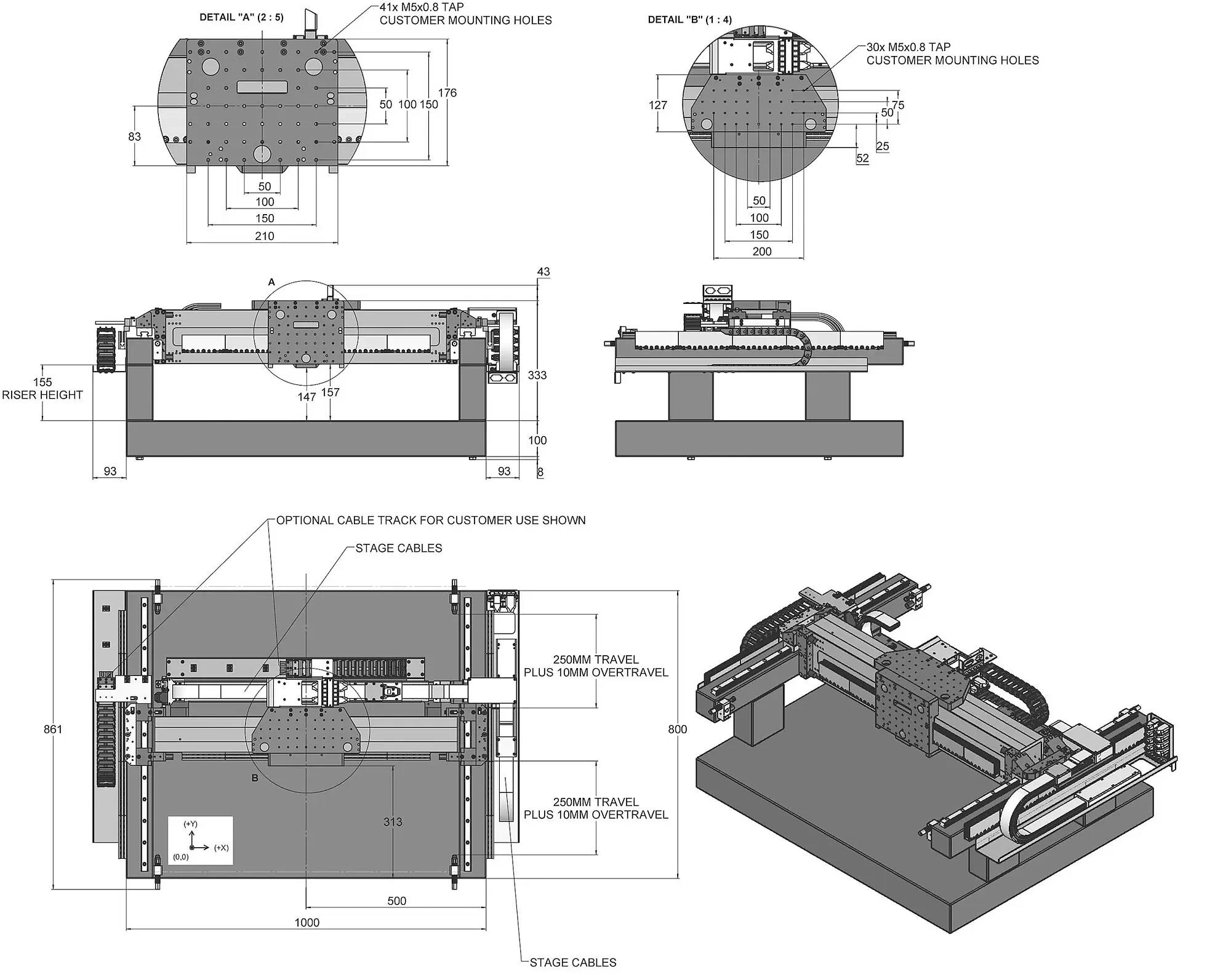
A-341 gantry system, dimensions in mm. Image Credit: PI (Physik Instrumente) LP
Overview
The A-341 PIglide HGS hybrid gantry system was made for applications requiring long travel ranges and overhead motion.
The A-341 hybrid gantry consists of a unique hybrid guide design. The bridge axis is fitted with a friction-free guide with air bearings that enable precise velocity control, excellent straightness, and repeatability.
The guide with air bearings has significantly reduced particle emission over the workspace. The gantry axis is fitted with recirculating ball bearing guides on both sides for hardiness and precision in limited installation space.
This combination of various guide technologies implies that the A-341 hybrid gantry is ideally suited to applications that depend on the step-and-scan principle and need a small design.
The A-341 has been linked with first-in-class controllers and drive modules from ACS that provide excellent servo performance, advanced control algorithms to enhance dynamic performance and error compensation, and an extensive suite of software development tools.
PIMag® Magnetic Direct Drive
The availability of a 3-phase magnetic direct drive does not utilize mechanical components in the drivetrain. They also transmit the drive force to the motion platform instantly and without friction. The drives achieve high velocities and accelerations.
Ironless motors are ideal for positioning tasks with the most significant accuracy demands since there is no unwanted interaction with the permanent magnets. This enables smooth running even at the lowest velocities, and there is no vibration at high velocities.
Nonlinearity in control behavior is avoided, and any position can be regulated easily. The drive force can be set freely.
Application Fields
- Digital printing
- Scanning
- Electronics assembly and inspection
- AOI (Automatic Optical Inspection)
- Automation.
Absolute Encoder
Absolute encoders supply clear position information that allows instant determination of the position. This means that referencing is unnecessary during switch-on, increasing efficiency and safety during operation.
Options and Customized Adaptations
- Base made of aluminum or granite
- Work height is adjustable
- Performance of the linear motors
- Systems available for decreasing vibration
- Liquid cooling of the linear motors
- Extra drag chains are available
Specifications
Source: PI (Physik Instrumente) LP
Motion |
Unit |
Bridge axis |
Gantry axis |
Travel range
|
mm
|
300
500
|
300
500
750
1000
|
Guide
|
|
Air bearing, pneumatic preloading
|
Recirculating ball bearing guide
|
Drive
|
|
1 ×
Ironless 3-phase linear motor
|
2 ×
Ironless 3-phase linear motor
|
Measuring system
|
|
Absolute linear encoder, 1 nm sensor resolution, BiSS-C, steel measuring scale
|
2 ×
Absolute linear encoder, 1 nm sensor resolution, BiSS-C, steel measuring scale
|
Load capacity (1)
|
|
10 kg
|
Positioning accuracy, calibrated (2)
|
µm
|
±0.75
|
±2
|
XY orthogonality
|
µrad
|
25
|
Max. velocity, unloaded (3)
|
m/s
|
2
|
1
|
Moved mass
|
kg
|
5
|
Depending on the travel range of the bridge axis:
300 mm: 25 kg
500 mm: 30 kg
|
(1) Assumes an air bearing operating pressure of 550 kPa. The payload center of gravity may not be more than 50 mm away from the surface of the motion platform.
(2) Accuracy values assume short time duration and do not consider the long-term effects of thermal drift on the stage.
(3) Depends on the motor selected, controller performance, duty cycle, load, and other application-specific parameters.
Drive properties |
Unit |
Option 1 |
Option 2 |
Nominal voltage
|
V DC
|
70
|
Peak voltage
|
V DC
|
300
|
Nominal force
|
N
|
58
|
87
|
Peak force
|
N
|
200
|
300
|
Nominal current, RMS
|
A
|
2.9
|
4.4
|
Peak current, RMS
|
A
|
10
|
15
|
Back EMF phase-phase
|
V·s/m
|
16
|
16
|
Resistance phase-phase
|
Ω
|
5.6
|
3.6
|
Inductance phase-phase
|
mH
|
1.8
|
1.2
|
Miscellaneous |
|
Operating pressure
|
550 ±35 kPa (80 ±5 psi)
|
Air consumption
|
< 30 l/min (1SCFM)
|
Air quality
|
Clean (filtered to 1.0 μm or better) - ISO 8573‑1 Class 1
Oil free - ISO 8573‑1 Class 1
Dry (-15 °C dew point) - ISO 8573‑1 Class 3
|
Materials
|
Hardcoat aluminum
Guide rails made of steel, cleanroom grease (guide rails made of stainless steel on request)
Mounting hardware made of stainless steel
|